Fabricación aditiva mediante láser selectivo en el sector aeronáutico
La fabricación aditiva (AM) es un proceso que permite unir materiales con el objetivo de fabricar objetos a partir de un archivo tridimensional generado por ordenador, también llamado CAD 3D. A diferencia de otras tecnologías de fabricación, en donde se arranca material, en la fabricación aditiva se suele fabricar capa a capa permitiendo, entre otras ventajas, libertad de forma en el diseño de las geometrías a producir. Esta relativamente nueva tecnología, también llamada comúnmente impresión 3D, continúa su evolución y se prevé que generará en el futuro un profundo impacto en las industrias manufactureras. Estos métodos avanzados de fabricación pueden aportar a la industria nuevos diseños, una mayor flexibilidad, una reducción de la energía y de los esfuerzos utilizados, y un ahorro de los tiempos de comercialización de los nuevos productos. Por otra parte, la industria aeronáutica requiere continuamente piezas que sean más ligeras y más resistentes y en ocasiones conductivas eléctricamente con el objetivo de mejorar la eficiencia de los aviones, pero además buscan una reducción de los niveles de ruido y contaminación generados durante el vuelo. Además, las complejidades en el diseño en el sector van en aumento, y en muchas ocasiones, requieren de pocas unidades e incluso de piezas unitarias, lo cual incurre en unos altos costes de producción.
Debido a estas características especiales, la industria aeroespacial [1] está particularmente interesada en la fabricación aditiva1 Por ejemplo, Boeing y Airbus están implementando estas tecnologías para reducir sus tiempos de fabricación, a través de la generación de piezas aligeradas y reducir los costes operacionales. Gracias a los avances en diferentes campos, la fabricación aditiva ya está contribuyendo a eliminar utillajes, procesos de soldadura, reducir inventarios y stocks, y a la mejora de los tiempos de producción de líneas completas de ensamblaje.
Sin embargo, aunque los beneficios son evidentes, aún quedan numerosos aspectos por mejorar para superar las limitaciones de la tecnología, especialmente en un sector con unos requerimientos tan estrictos como es el aeronáutico. Aunque se han realizado numerosos avances y mejoras en la fabricación aditiva queda aún un largo camino por recorrer hasta llegar a conseguir piezas totalmente funcionales y certificables para el sector aeronáutico.
Bajo esta marco se abren diversas líneas de trabajo relacionadas con el desarrollo de materiales avanzados de altas prestaciones, integración de procesos de diseño optimizado para de fabricación aditiva y trabajos de cualificación y certificación del proceso productivo.
1. Comportamiento de aleaciones de titanio en procesos DMLS
Los materiales juegan un importante rol en los procesos de fabricación aditiva para el sector aeronáutico. A día de hoy, un material suele resultar determinante por su peso a la hora de la realización del diseño. Por esta razón, surge la necesidad inherente de obtener, cada vez más, nuevos materiales que satisfagan las necesidades de los ingenieros y que permitan la obtención de piezas más ligeras cumpliendo con la funcionalidad requerida.
El DMLS ofrece diversas variantes de materiales [2] en función a las capacidades de la maquinaria existente. Si caracterizamos las tecnologías existentes en función de los materiales que pueden procesar, podemos establecer que existen máquinas con procesos para la fabricación de piezas de forma directa en materiales poliméricos, metálicos y cerámicos. En esta línea cabe destacar que uno de los materiales, procesables por fabricación aditiva, que por propiedades físico-químicas y mecánicas, presentan un mayor interés desde el punto de vista de la industria aeronáutica es el Ti6AL4V. Del modo que ha sido mencionado en apartados anteriores el proceso de fabricación avanzada no está certificado [3] para el sector, abriéndose en este campo una línea de trabajo intensa al objeto de establecer, de cara al futuro, la fabricación aditiva como un proceso más involucrado en la producción aeronáutica.
Una forma de evaluar el comportamiento de los materiales procesados por tecnologías de fabricación aditiva es la realización de estudios empíricos en los cuales se lleven a cabo análisis comparativos entre las propiedades de elementos generados por tecnologías convencionales y las mismas geometrías generadas por fabricación aditiva. En esta línea, desde Prodintec se han realizado diversos trabajos de investigación y evaluación del comportamiento de uno de los materiales de interés para el sector aeronáutico como es el Ti6AL4V cuando es sometido a un proceso de sinterizado láser tipo DMLS (Direct Metal Laser Sintering).
El procedimiento de trabajo utilizado fue el análisis comparativo de diferentes propiedades mecánicas frente a unos valores de referencia establecidos. En este caso se toman como patrón un elemento Ti6AL4V generado por métodos convencionales de fundición. Las propiedades estudiadas fueron la resistencia mecánica, elongación, dureza, rugosidad y porosidad. Así pues las propiedades del elemento de fundición, que se toman como patrón, son:
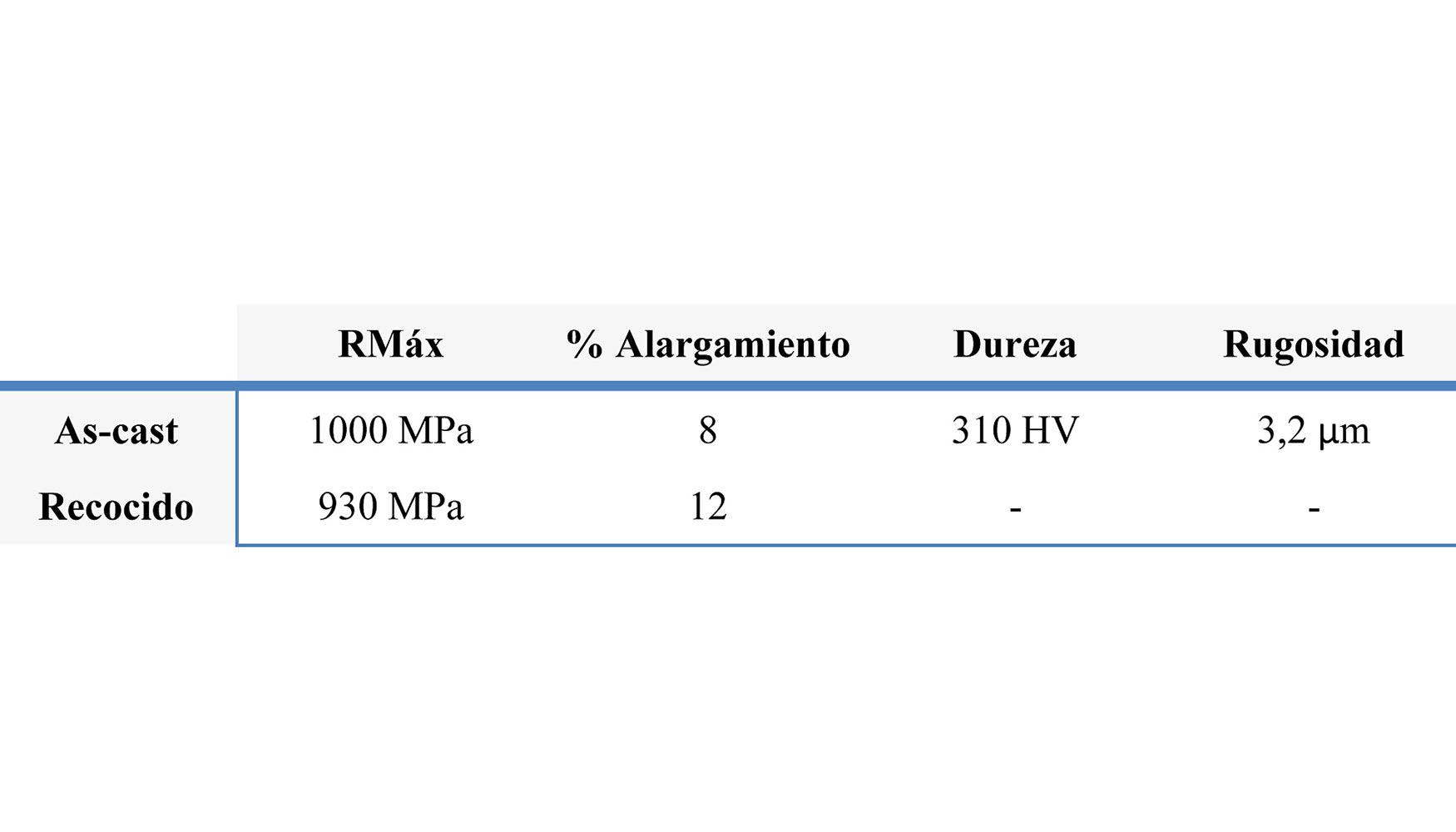
Como se refleja en la tabla anterior se incluyen datos sin y con post-tratamiento térmico (recocido). Con respecto a los materiales a procesar por DMLS se trabajó con una aleación comercial de cuyos valores característicos según ficha técnica son:
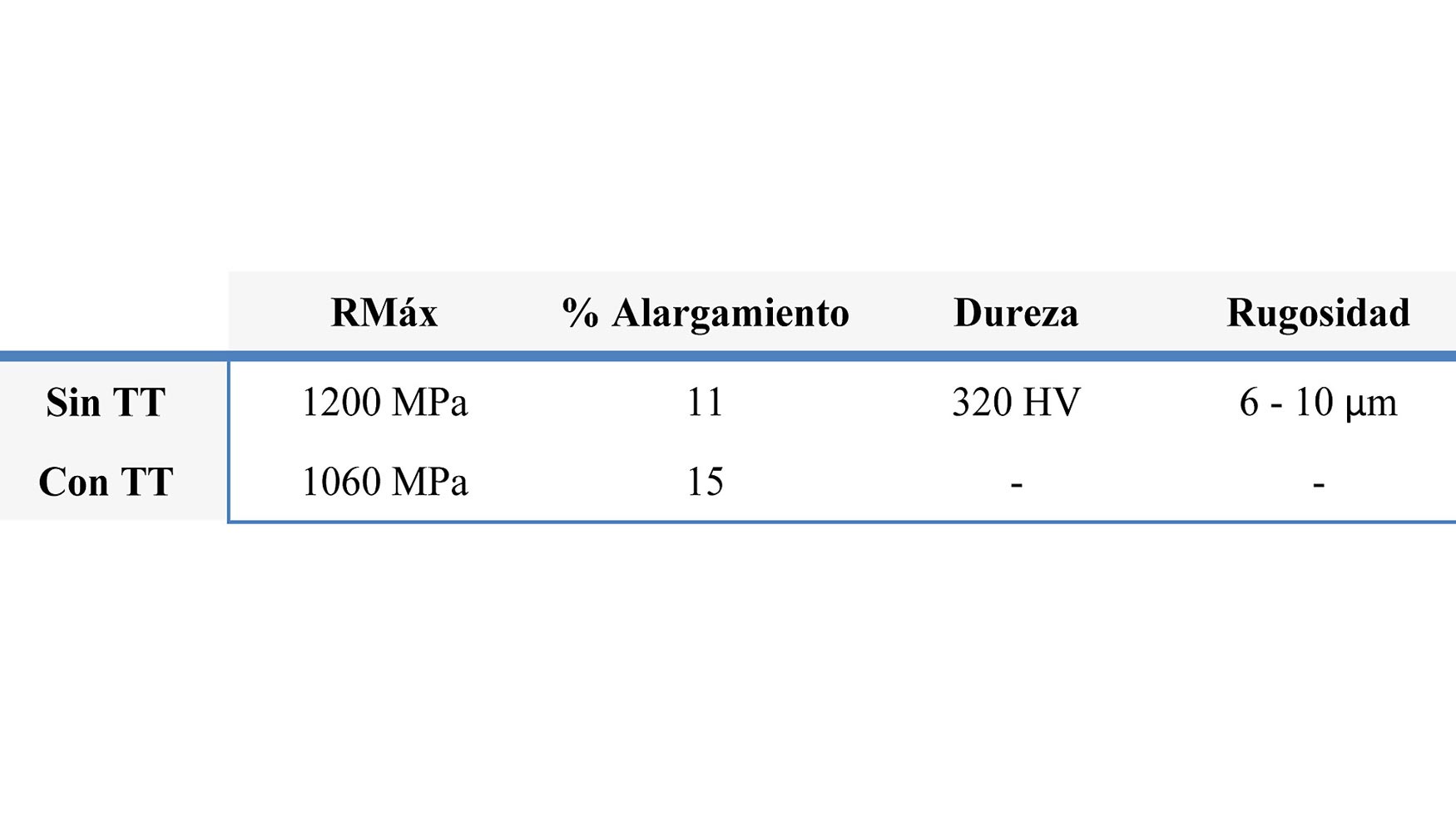
Como se refleja en la tabla anterior se incluyen datos del material sin y con posttratamiento térmico. A partir de los datos indicados sobre estas líneas se procedió a la generación de probetas, mediante fabricación aditiva (tecnología DMLS), al objeto de estudiar el comportamiento de la aleación de titanio cuando es procesada mediante un sinterizado láser. Así mismo en el estudio se incluyó el post-mecanizado de las probetas como otro factor a estudiar de modo que se pudiese establecer la influencia de este post-proceso sobre las propiedades físico-mecánicas. A continuación se muestra el detalle de varias probetas para ensayos de resistencia mecánica y pruebas de dureza:
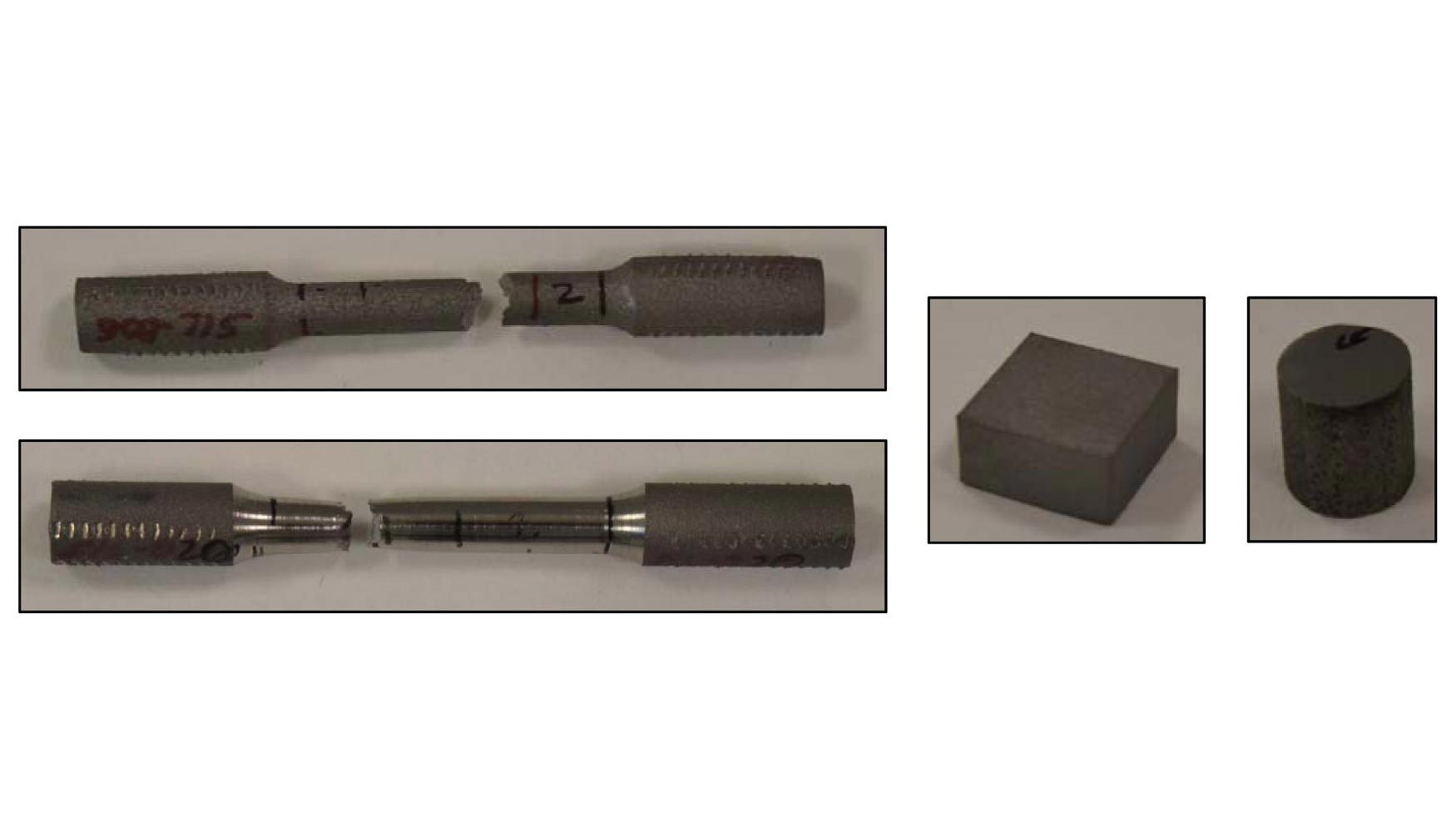
En los siguientes gráficos se recoge un análisis comparativo entre las propiedades físico-mecánicas de los elementos de aleación de titanio generados por fundición convencional, los valores de las fichas técnicas del mismo material para fabricación aditiva y el resultado experimental de los estudios realizados sobre probetas generadas por DMLS:
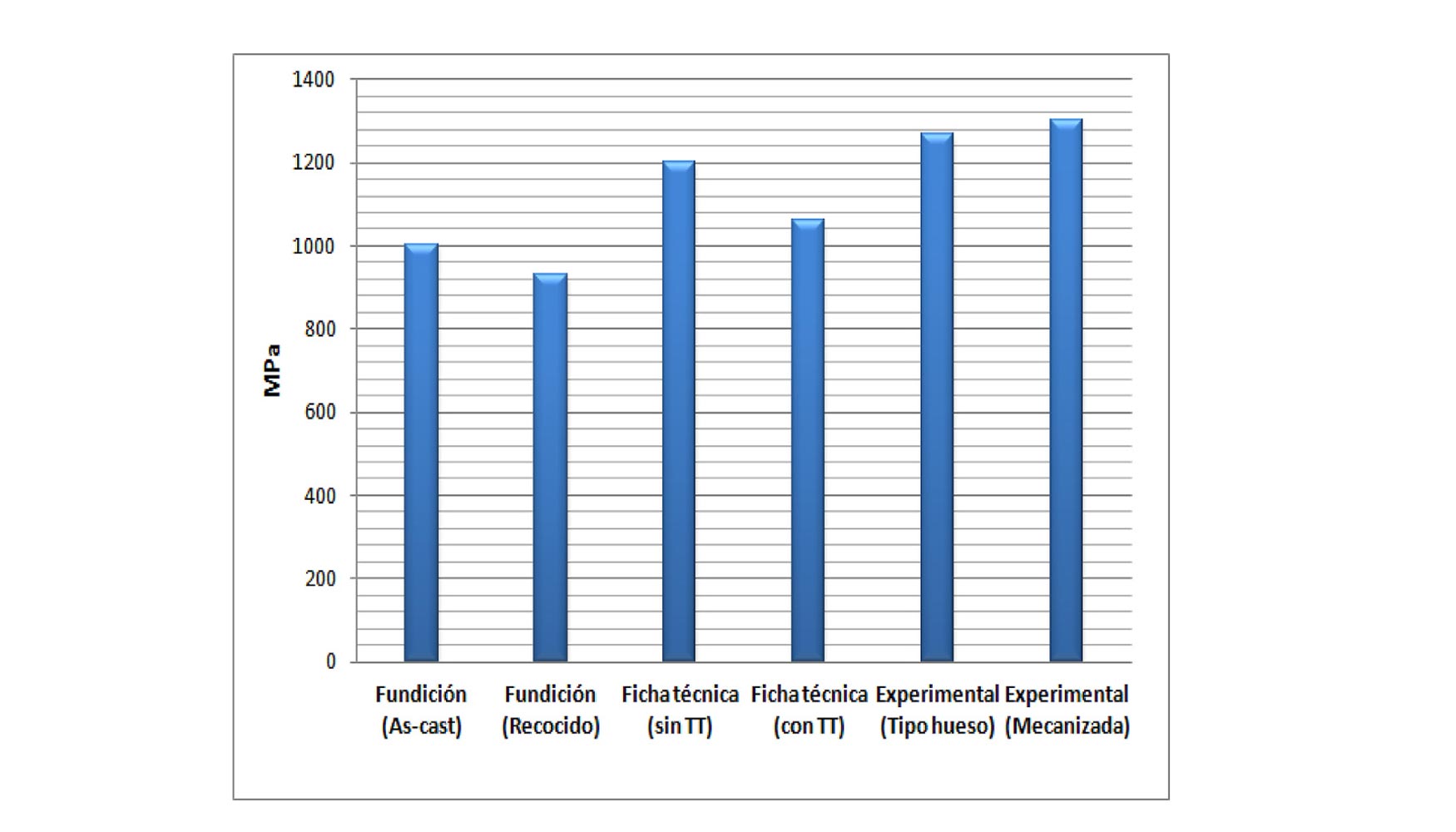
Tal y como queda reflejado en el esquema anterior el proceso de fabricación aditiva arroja unos buenos valores de resistencia mecánica, superando a los definidos en ficha técnica y los establecidos en las piezas de fundición. Junto con los ensayos de resistencia mecánica indicados se llevó un estudio de la deformación de los diferentes elementos bajo la acción de esfuerzos. Los resultados se muestran en el siguiente gráfico:
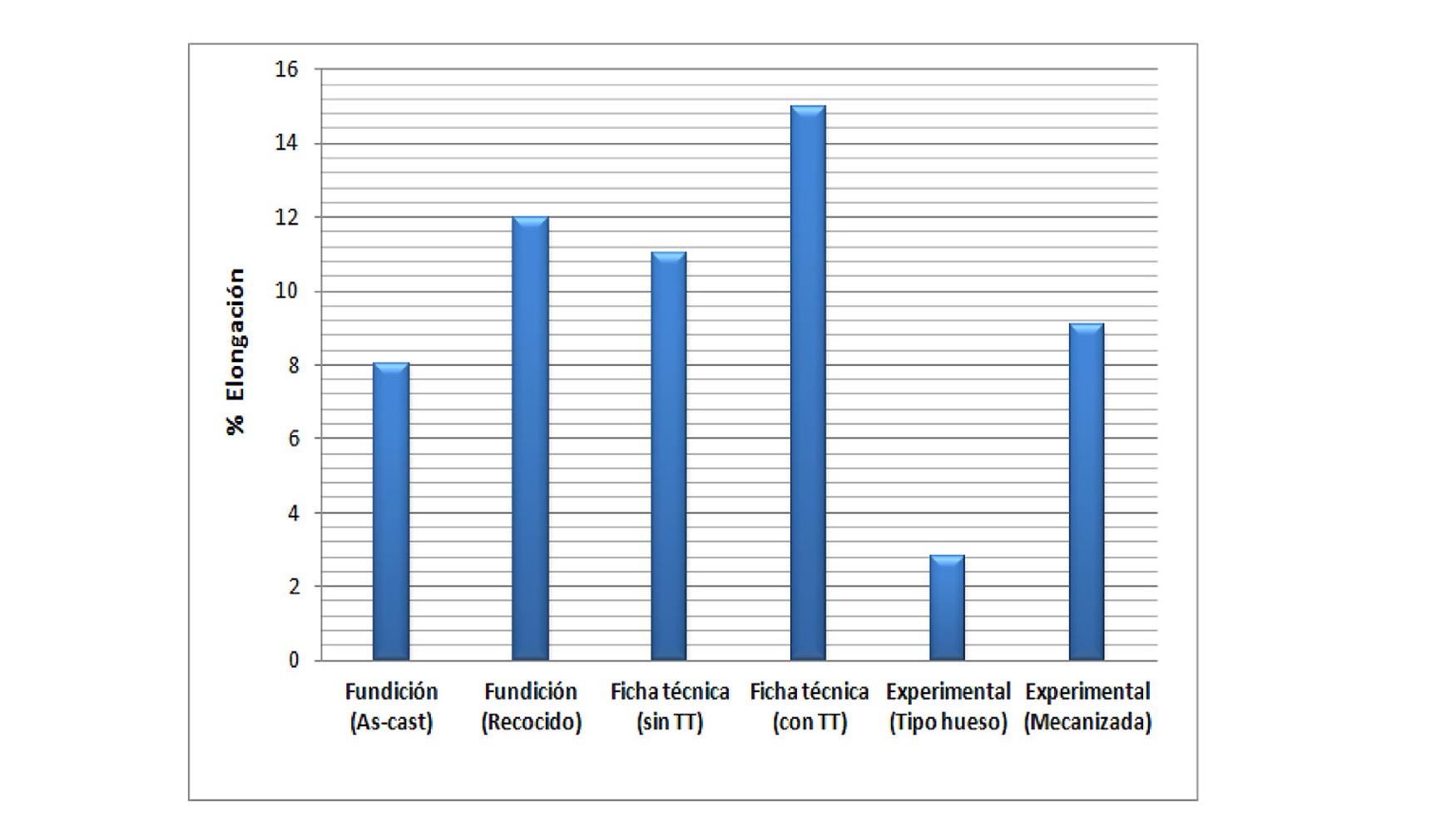
Del modo que ha quedado expuesto sobre estas líneas los materiales procesados por sinterizado láser tienen un comportamiento más rígido que los convencionales con valores de deformación inferiores. Los resultados anteriores se completaron con estudios de dureza y rugosidad los cuales arrojaron los siguientes resultados:
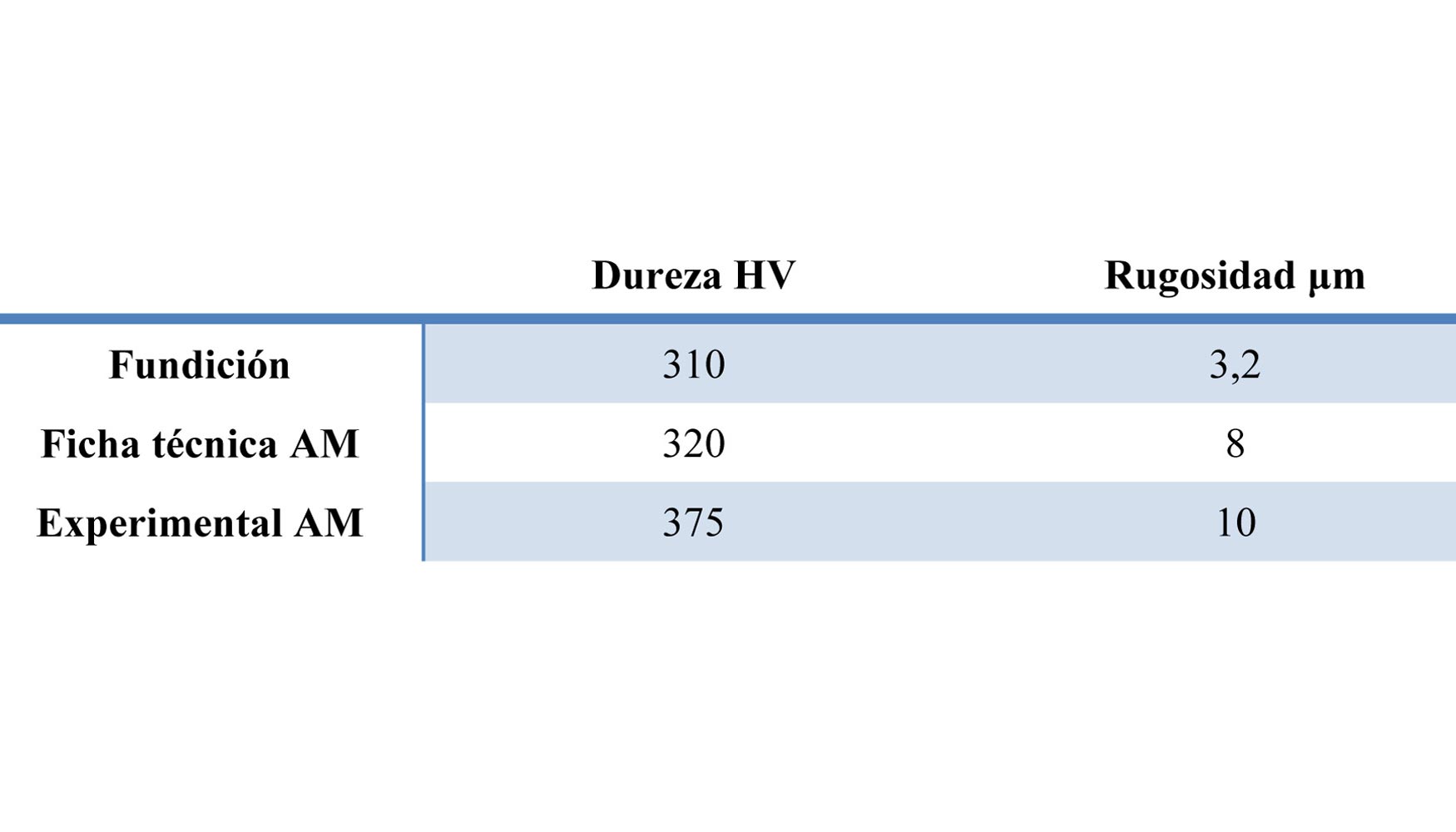
El proceso de fabricación aditiva penaliza en cierto modo el acabado superficial con rugosidades superiores a las del proceso convencional de fundición.
2. Diseño optimizado para fabricación aditiva
Una de las ventajas clave de las tecnologías avanzadas de fabricación aditiva es su alta capacidad para generar estructuras complejas que por otros métodos resultan, en muchos casos, inviables técnica o económicamente. En esta línea se abre todo un abanico de posibilidades a la hora de trabajar en el diseño de la configuración geométrica óptima de un cuerpo que minimice o maximice una cierta función, optimizar el coste, al tiempo que satisface las restricciones o condiciones de contorno del problema mediante metodologías de optimización topológica. De cara a la realización de un proceso de optimización topológica es importante conocer tanto las características del material, Ti6AL4V (véase el apartado 2), como las ventajas y restricciones del proceso productivo, en este caso fabricación aditiva mediante DMLS (véase tabla 4).
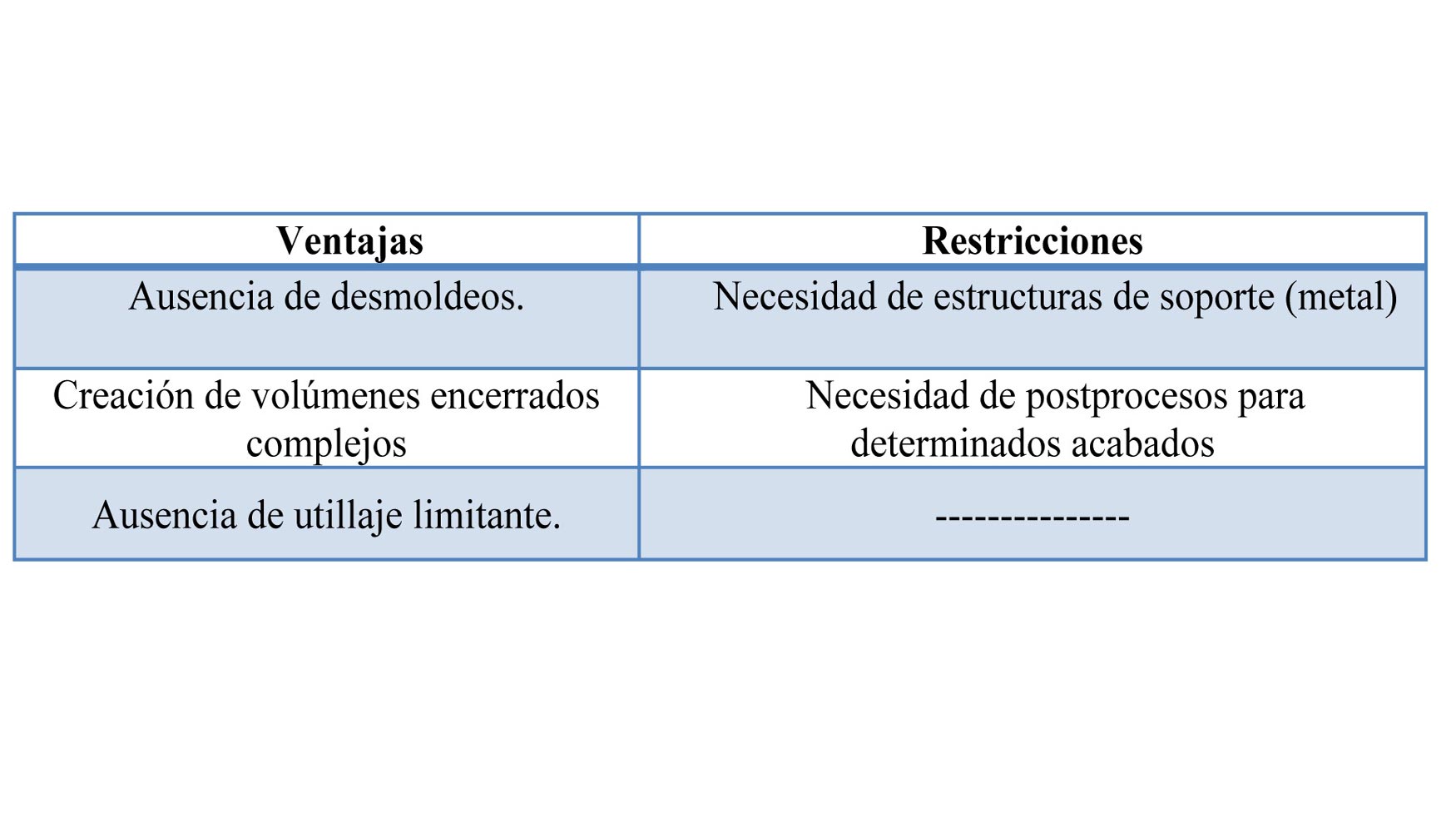
2.1. Caso práctico
A continuación se expone un caso práctico del desarrollo de optimización de un herraje metálico de Ti6Al4V de la bisagra de un capot de motor de un avión comercial, de la compañía Airbus. El herraje original se realiza mediante procesos de arranque de viruta y se está evaluando la realización del mismo mediante técnicas de fundición de precisión de modelo perdido, con el fin de eliminar la pérdida de material de partida que se produce con el actual proceso sustractivo.
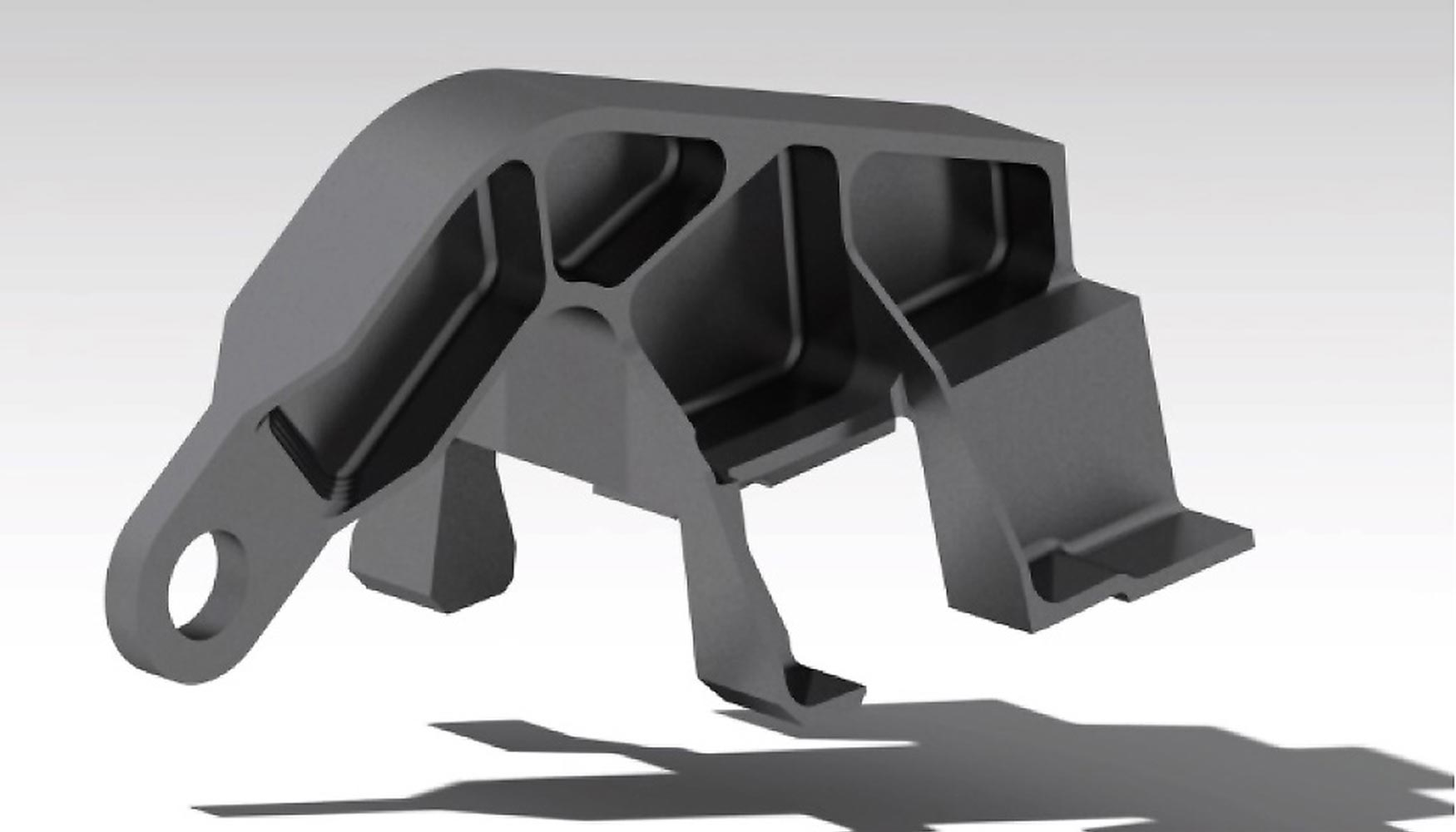
El presente desarrollo se llevó a cabo al objeto de evaluar de forma cualitativa y cuantitativa la realización de estas piezas mediante técnicas de AM, cuando el proceso y los materiales fueran elegibles para su realización.
En primer lugar, tomando como datos de partida las propiedades del material y las características del proceso de fabricación (DMLS), se establecieron una serie de restricciones de diseño tales como las que se indican a continuación, a partir de las cuales trabajar en el diseño optimizado:
→ Aplicación de restricciones de dirección predominante para la eliminación de soportes.
→ Tamaño mínimo de elemento de 0,5mm en plástico y de 0,1 mm en metal de manera general.
→ Restricción de formas asociadas a bóvedas.
Combinando las ventajas de la fabricación aditiva junto con la utilización de técnicas de optimización topológica se realizó un diseño, tal y como aprecia en las siguientes figuras:
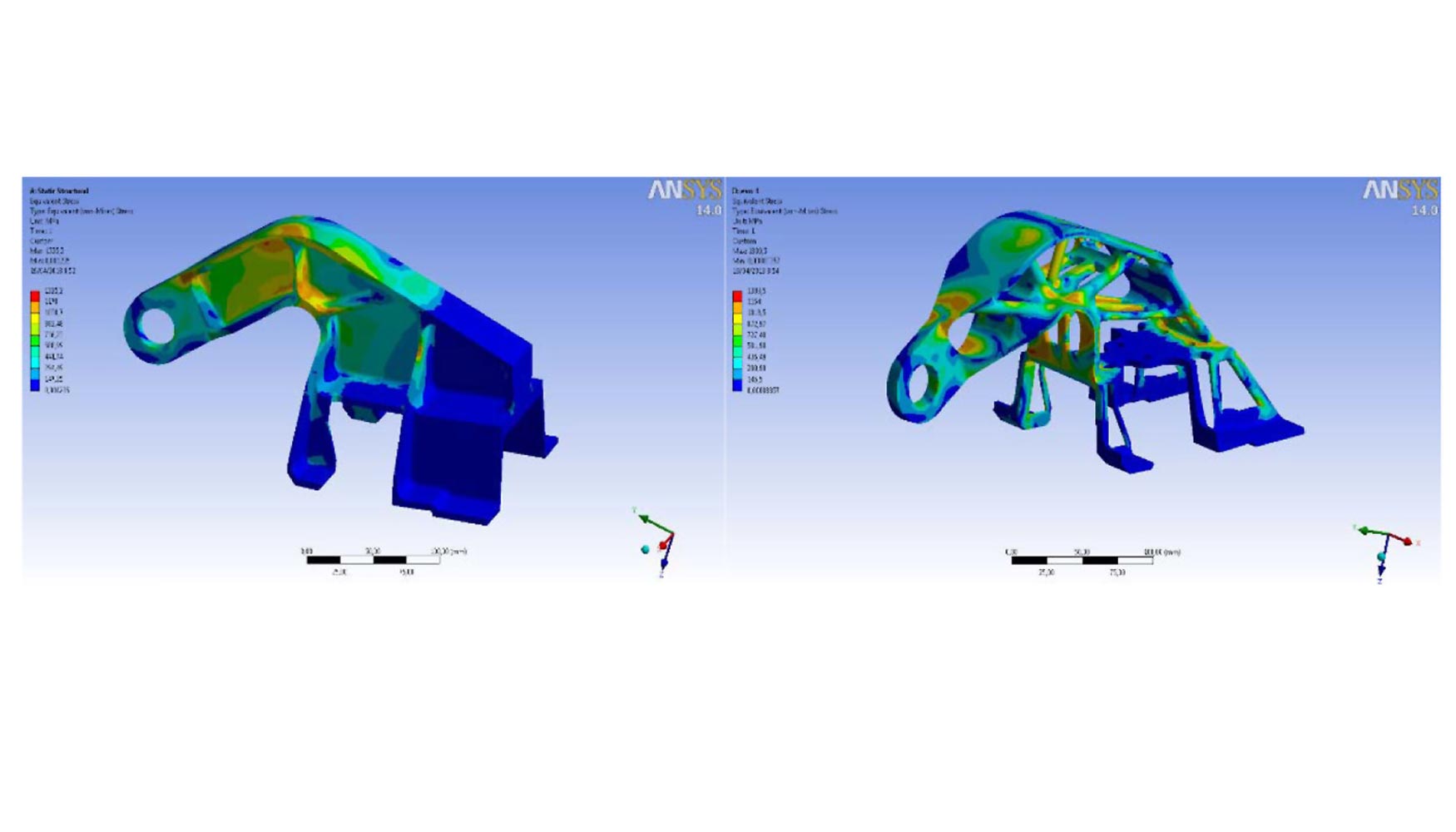
Tal y como se refleja en los gráficos, el nuevo diseño optimizado es una estructura aligerada que ha permitido:
→ Reducción de peso del 24%
→ Reducción del coste total de fabricación, un 15%, con respecto a medios sustractivos.
→ Ahorro en tiempo de fabricación del 20%
→ Todo ello manteniendo rigideces y con un mejor reparto de tensiones localizadas.
A continuación se muestran algunas imágenes de detalle del elemento fabricado mediante tecnología DMLS en aleación de Ti6Al4V:
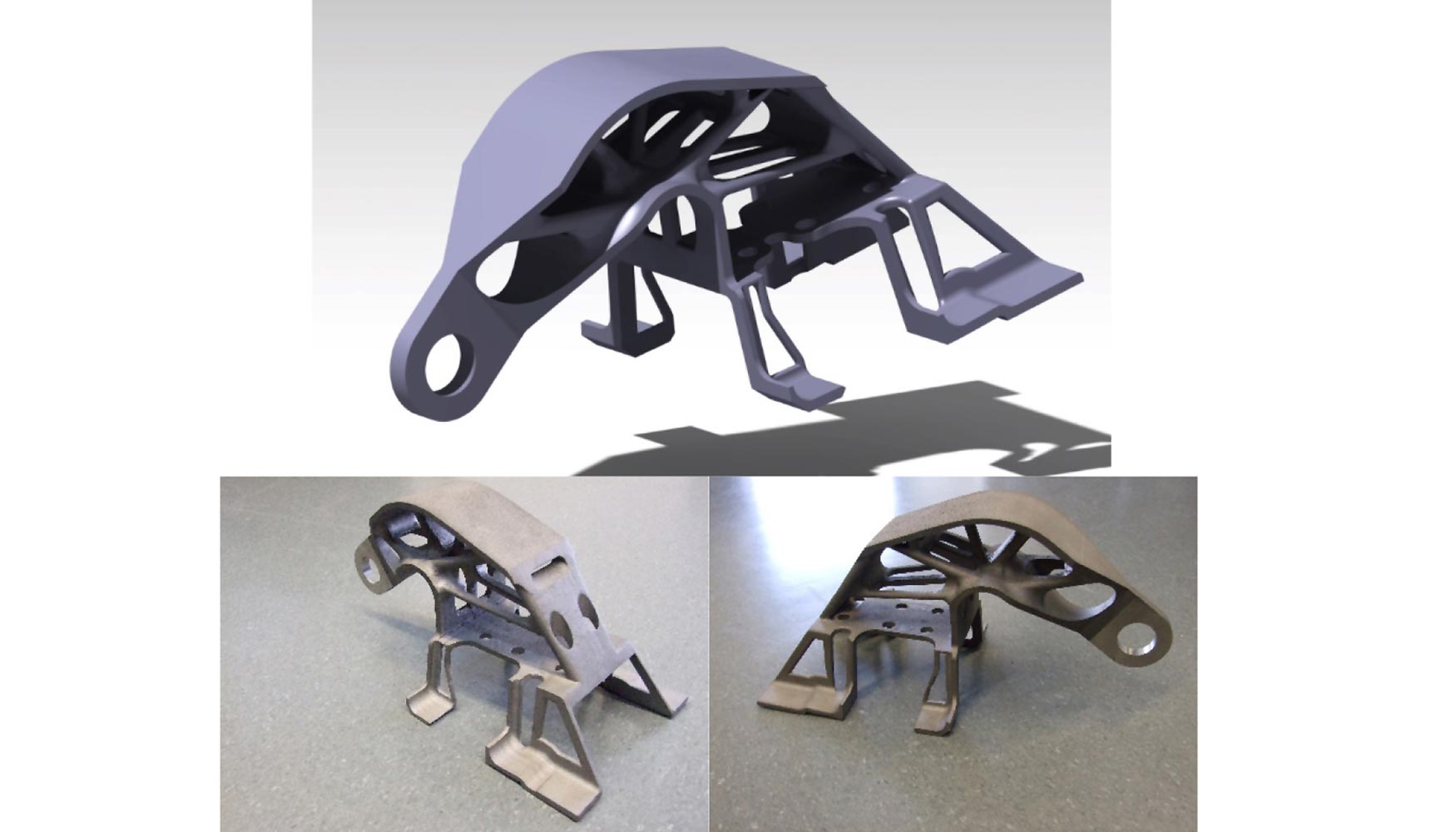
La combinación de un proceso de diseño mediante optimización topológica combinado con la tecnología de fabricación avanzada por sinterizado láser (DMLS) permite crear soluciones y nuevos conceptos no realizables hasta el momento.
3. Conclusiones
Tal y como ha quedado reflejado las tecnologías avanzadas de fabricación aditiva conforman una herramienta muy potente de cara al desarrollo de elementos de alto valor añadido en sectores tan exigentes como el aeronáutico.
La combinación del estudio y conocimiento de materiales, el proceso de fabricación y el diseño optimizado permite generar estructuras aligeradas, reducir los costes y tiempos de fabricación, manteniendo en todo caso las propiedades estructurales de las piezas. Pese a las ventajas de la tecnología y los trabajos realizados existen, a día de hoy, algunos aspectos que frenan la implementación de la tecnología en aeronáutica tales como: la ausencia de certificación del proceso y materiales para su uso directo en este sector, así como la imposibilidad de hacer frente a una situación de producción real, debido a la ausencia de disponibilidad de recursos (máquinas de DMLS) disponibles en el mercado. De cara al futuro, y a la vista de los buenos resultados que ofrece la tecnología, se abren importantes campos de trabajo tales como la certificación4 de procesos y materiales, y el escalado de la tecnología para la generación de elementos de mayor tamaño.
Referencias
[1] Additive Manufacturing Technology Assessment, February 2015.
[2] Roadmap for Additive Manufacturing in Aerospace, EOS e-Manufacturing Solutions, March 2015.
[3] Summary of NDE of Additive Manufacturing Efforts in NASA, July 2014.
[4] Measurement Science Roadmap for Metal-Based Additive Manufacturing, national Institute of Standards and Technology, May 2013.