Tecnologías para el taladrado de materiales aeronáuticos avanzados
Por otro lado, la mejora en el rendimiento productivo de las empresas en el siglo XXI no debe acomodarse en exclusiva a enfoques lineales que sólo contemplen beneficios económicos, olvidando no sólo el contexto socioeconómico en el que se encuentran inmersas, sino, a su vez, la responsabilidad ante una sociedad global que exige cada vez más un máximo respeto al medio ambiente y un uso racional de los recursos energéticos que se refleje en un acercamiento a niveles óptimos de eficiencia energética en los sistemas de fabricación.
En el sentido de lo anteriormente expuesto, el desarrollo de tecnologías y materiales que abran nuevas vías en el transporte aéreo ha sido una preocupación continua en la industria aeroespacial. En la actualidad, la mayoría de las compañías constructoras aeronáuticas contemplan el uso de aleaciones de aluminio bien conocidas o algunas de sus variantes suficientemente estudiadas. Así, se emplean, básicamente, aleaciones de la serie 2XXX (Al-Cu), como la UNS A92024, y de la serie 7XXX (Al-Zn), como la UNS A97075 o la UNS A97050 o sus más recientes variantes como la UNS A97150. Estas aleaciones se han venido utilizando debido a su excelente relación peso/propiedades físico-químicas/coste. La continua búsqueda de mejoras en el rendimiento productivo y en servicio de los elementos aeronáuticos lleva consigo el desarrollo de materiales que optimicen la relación anteriormente expuesta.
Así, se abren tres vías de investigación que tiendan a mejorarla [6]:
- Disminución de peso. La reducción de peso de la estructura del avión permite la posibilidad de incorporar una mayor carga sin necesidad de aumentar el consumo energético para su desplazamiento. Esta reducción de peso contempla el empleo de materiales más ligeros que, como mínimo, aseguren las mismas propiedades que los utilizados tradicionalmente, lo que garantiza un mantenimiento de las excelentes condiciones de seguridad demostradas hasta el momento. Estos ambiciosos objetivos requieren un cambio revolucionario en la tecnología aplicable a este sector industrial. En esta línea se encuentran las investigaciones tendentes a la modificación de las aleaciones ya existentes, al desarrollo de nuevas aleaciones y a la aplicación de otros materiales más ligeros. En lo relacionado con los aspectos más específicos de este proyecto cabría destacar el desarrollo y aplicación de aleaciones de Al-Li, (UNS A92098 y su variante actualmente en fase de estudio UNS A92198), en su día abandonadas por problemas de corrosión y retomadas en la actualidad (cabe citar como ejemplo el hecho de que es una de las líneas prioritarias de investigación marcadas por Airbus —Airbus R&D Strategic Program— en el año 2005). Por otro lado, la aplicación de materiales no metálicos que provoquen una marcada reducción de peso, como es el caso de los materiales compuestos de matriz orgánica (NMMC, Non-Metal Matrix Composites), especialmente la Fibra de Carbono (FC) está cada vez más extendido y su porcentaje de presencia en las aeronaves es cada vez más elevado. De hecho, aunque el uso de materiales compuestos para la fabricación de componentes de estructuras aeronáuticas en aviones comerciales puede retrotraerse al programa ACEE (Aircraft Energy Efficiency) de la Nasa en los años setenta, actualmente, el empleo de materiales compuestos en estructuras aeronáuticas es muy alto tanto en aviones comerciales de última generación como el Boeing 787 o el Airbus A350, en los que los materiales compuestos pueden constituir más del 50% de la estructura, como en aviones militares (A 400M) o helicópteros, en los que, en algunos casos, llega, incluso, a superarse con amplitud.
- Mejora en las propiedades físico-químicas. La mejora de las propiedades se busca desde la incorporación de materiales como las aleaciones de titanio (fundamentalmente la aleación Ti6Al4V), ligeras, con buenas propiedades mecánicas y altamente resistentes a la corrosión, o como los ya mencionados NMMC que permiten, solos o en combinación con otros materiales metálicos formando FML (Fiber Metal Laminates), disponer de excelentes valores de muchas propiedades fisico-químicas con una notable reducción del peso efectivo. Precisamente el uso de las combinaciones FC/Ti6Al4V, FC/Aleación de Aluminio y FC/Aleación de Aluminio/Ti6Al4V son los FML más frecuentes en la industria aeroespacial. En particular, los primeros tienen una especial relevancia debido a que no forman un par galvánico tan acusado como en el caso de la combinación FC/Aleación de Aluminio. Adicionalmente, en relación con este tipo de mejoras, las investigaciones también se dirigen hacia la aplicación de posibles modificaciones en los procesos de fabricación que permitan mejorar el rendimiento en servicio en materiales más comúnmente empleados, aplicando nuevos tratamientos de acabado que mejoren propiedades en superficie como la corrosión o su combinación con otras propiedades mecánicas como es el caso de la corrosión bajo tensión (CBT). Finalmente, otra de las posibilidades abordadas en esta línea contempla la mejora de las propiedades en superficie sin necesidad de empleo de tratamientos superficiales sino, directamente, a partir de una situación de compromiso entre la calidad de acabado obtenida (desde los puntos de vista macro y microgeométrico) y dichas propiedades fisico-químicas.
- Disminución del coste. Actualmente, a la hora de hacer referencia al coste, no deben tenerse únicamente en cuenta los aspectos económicos en términos absolutos, sino que, adicionalmente, también deben contemplarse los aspectos relacionados con el impacto medioambiental de los materiales y su procesado. Una situación de compromiso entre ambos aspectos se tiene cuando se eliminan etapas intermedias en el proceso de fabricación de los distintos elementos, lo que, de manera directa, afecta al tiempo de manufactura y al consumo energético asociado. Otros factores, como la adecuación de los parámetros, el alargamiento de la vida del utillaje o el empleo de tecnologías más limpias influyen positivamente sobre los dos aspectos anteriormente mencionados.
Utilización de materiales compuestos en la fabricación de aeronaves
Las propiedades asociadas a los materiales compuestos cubren ampliamente el rango de mejoras anteriormente expuesto debido, esencialmente, a su elevada eficiencia estructural, posibilitando fabricar aeronaves y otros sistemas de transporte colectivo e individual en los que se puede alcanzar un considerable ahorro en costes operativos directos, por una parte por el ahorro de combustible debido a disponer de estructuras más ligeras, y por otra por la disminución considerable de problemas de corrosión y deterioro de estructuras. Por otro lado, el empleo de estos materiales hace factible la realización de ingenios que resultaban imposibles o muy difíciles de realizar con el empleo de materiales clásicos de ingeniería.
Estos materiales tienen además indudables ventajas ligadas a las exigencias de una mayor seguridad, menor consumo de energía y de costes de mantenimiento o prevención de riesgos que caracterizan hoy en día al transporte aéreo [6], frente a otros materiales en estos usos, como excelente relación entre resistencia mecánica y peso, rigidez, aumento de la vida útil gracias a su buena resistencia a la fatiga, resistencia a la corrosión, resistencia a la abrasión, aislamiento acústico y su ductilidad que permite darles la forma exigida por el diseño, lo que permite aumentar los elementos monolíticos, reduciendo de esa forma los componentes para ensamblaje y, en consecuencia, los puntos de unión, que son, con frecuencia, los más críticos en la estructura de una aeronave.
Además, los materiales compuestos puedan considerarse actualmente como un nuevo tipo de material con la madurez suficiente como para poder emplearse de forma masiva con un elevado grado de fiabilidad. Sin embargo, existen muchos aspectos, tanto de los propios materiales como de las tecnologías a ellos asociadas, que no están totalmente maduros y existe una considerable capacidad de mejora, tanto en las prestaciones y características de los materiales en sí, como en los procesos y tecnologías asociados al empleo y puesta en servicio de los elementos estructurales realizados con este tipo de material [7-9].
En la actualidad, el mercado mundial de los materiales compuestos crece desde mediados de los años 90 al 5,7% anual. El crecimiento es más favorable para compuestos termoplásticos que para compuestos termoestables: el 9% y el 3% anual, respectivamente; sin embargo, los materiales termoestables, representan aún más de las dos terceras partes del mercado [10].
En la figura 1, se puede observar el porcentaje de los principales materiales de refuerzo y matriz más utilizados, por otro lado, en la figura 2, se puede apreciar la forma de estos refuerzos [11].
![Figura 1. Principales materiales utilizados en la matriz y en el refuerzo. Adaptada de [11] Figura 1. Principales materiales utilizados en la matriz y en el refuerzo. Adaptada de [11]](https://img.interempresas.net/fotos/769540.jpeg)
![Figura 2. Principales formas de los refuerzos utilizados en los materiales compuestos. Adaptada de [11] Figura 2. Principales formas de los refuerzos utilizados en los materiales compuestos. Adaptada de [11]](https://img.interempresas.net/fotos/769541.jpeg)
En esta línea se encuentran las investigaciones tendentes a la aplicación de materiales no metálicos que provoquen una marcada reducción de peso, como es el caso de los materiales compuestos de matriz orgánica, especialmente los reforzados con fibra de carbono (Carbon Fiber Reinforced Plastics-CFRP), cuyo empleo está cada vez más extendido y su porcentaje de presencia en las aeronaves es cada vez más elevado.
En cuanto a necesidades de material, la aviación civil es, con diferencia, el segmento aeronáutico que mayor consumo demanda, pero los materiales compuestos también están entrando con fuerza en el resto de segmentos. Una tendencia de este hito se aprecia en el aumento del porcentaje de utilización de materiales compuestos en un avión, desde un 5% en la década de los años 80, al 50% utilizado actualmente.
De forma genérica, la utilización de material compuesto (básicamente de fibra de carbono con matriz polimérica) en la industria aeronáutica puede estimarse en [2-5]:
- Aeronaves comerciales: 21.000 toneladas en 2007-2011 (33.000 toneladas en 2012-2016).
- Aviación ejecutiva y general: 1.200 toneladas en 2007-2011.
- Aeronaves de ala rotatoria: 3.000 toneladas MC en 2007-2012.
- Aeronaves militares: 2.300 toneladas en 2007-2011.
- Vehículos lanzadores: 1.500 toneladas en 2007-2011.
La capacidad mundial actual de producción de fibra de carbono de grado aeroespacial se estima en unas 60.000 toneladas/año.
Como se ha comentado anteriormente, la introducción de los materiales compuestos en aviación civil tuvo sus inicios en los años 80 y aunque con una repercusión muy pequeña en el total de las aeronaves, poco a poco el porcentaje de materiales compuestos ha ido aumentando de manera significativa. En el caso del Airbus A380, el uso de materiales compuestos alcanza casi el 25% del total de la estructura y en el Boeing B787 (figura 3) llega a un 50% del peso estructural, del mismo orden que en el Airbus A350XWB (figura 4), que alcanzará un 52%. Estos valores son quizás más indicativos cuando se expresan en términos volumétricos (un B787 tiene aproximadamente un 80% de estructura de materiales compuestos en volumen).
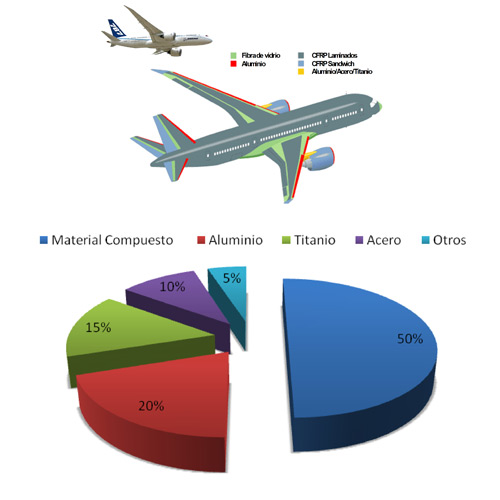
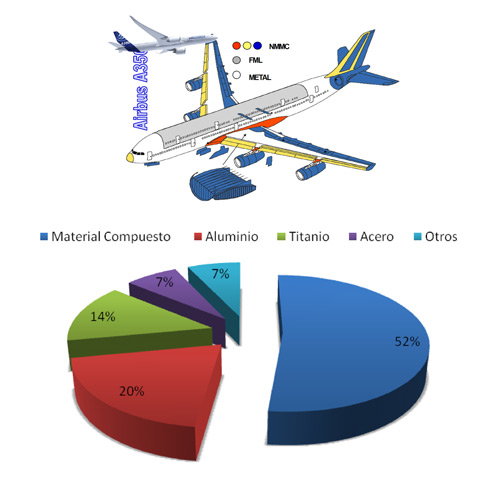
A pesar de sus indudables ventajas, estos materiales presentan en la actualidad una serie de inconvenientes. En efecto, los costes de fabricación son elevados (costosas inversiones en instalaciones y equipos), costosos programas de evaluación, calificación y certificación de estructuras. Puede haber variaciones en la rigidez y la resistencia mecánica de los compuestos (en determinadas circunstancias), baja resistencia al impacto, baja conductividad eléctrica, costes de materiales elevados, entrada de agua en estructuras sándwich y difícil reciclado, etc. [12, 18-21]. Además, los controles de las piezas fabricadas (inspección visual, rayos X, ultrasonidos y ensayos de resistencia) para detectar los principales defectos que pueden presentarse en las mismas pueden resultar especialmente costosos. Estos defectos, entre los que pueden citarse las discontinuidades entre láminas producidas por la existencia de aire atrapado, la falta de resina, delaminaciones que aparecen durante el curado, curado incompleto de la resina, exceso de resina entre láminas, porosidad, orientación incorrecta de las láminas para formar el laminado, daño en las fibras, inclusiones, variaciones en el espesor y uniones inaceptables pueden resultar especialmente críticos para la seguridad [24-28].
Adicionalmente, los componentes y piezas realizados con este tipo de materiales son normalmente fabricados para una aplicación concreta. Además, debido a exigencias técnicas de calidad y de ensamblaje, estos deben ser sometidos a diferentes operaciones de conformado. Uno de los procesos más ampliamente empleados son los procesos de mecanizado.
Mecanizado de materiales compuestos empleados en la industria aeronáutica
Los procesos de mecanizado de materiales compuestos difieren significativamente en muchos aspectos del mecanizado de materiales metálicos [26,31], ya que se comportan como materiales no homogéneos y anisótropos, dependiendo de las características y el contenido de sus constituyentes (matriz y refuerzos). Debido a ello, durante el proceso de corte, las herramientas entran en contacto alternativamente con la fibra de carbono y la matriz, donde la respuesta de cada uno es totalmente diferente. Además, hay que tener en cuenta que dos materiales compuestos nunca se comportan igual a la hora de ser mecanizados, aun habiendo sido fabricados con el mismo proceso [24].
Tecnologías en el taladrado de materiales compuestos en la industria aeronáutica
Uno de los procesos más críticos en el mecanizado de materiales compuestos es el taladrado. Esto se debe al gran número de orificios que son necesarios realizar durante las operaciones de montaje en elementos estructurales. Debido a ello, es necesario estudiar los problemas actuales que rodean el mecanizado de fibra de carbono con matriz epoxídica en la industria aeronáutica [33-36].
Como consecuencia de lo expuesto anteriormente y debido a las características descritas de estos materiales, surge la necesidad de modificar o adaptar en la industria las herramientas y técnicas de mecanizado tradicionales incorporando nuevas mejoras al mínimo coste. En definitiva, el mecanizado de materiales compuestos persigue la mejora del proceso. Este objetivo debe conseguirse en condiciones que favorezcan un mínimo gasto de energía y la menor repercusión en el medio ambiente, sin sacrificar la funcionalidad de las piezas obtenidas.
En este contexto, se contempla la posibilidad de hacer uso de tecnologías no convencionales de mecanizado, como son el corte por láser o el corte por chorro de agua y sustituir los medios manuales o semiautomáticos, que eran y son en muchos casos los utilizados en la industria aeronáutica.
El uso de estas tecnologías en el mecanizado de estos materiales ha crecido considerablemente en los últimos años, si bien las investigaciones siguen siendo más intensas en lo que se refiere a las tecnologías convencionales, figura 5.
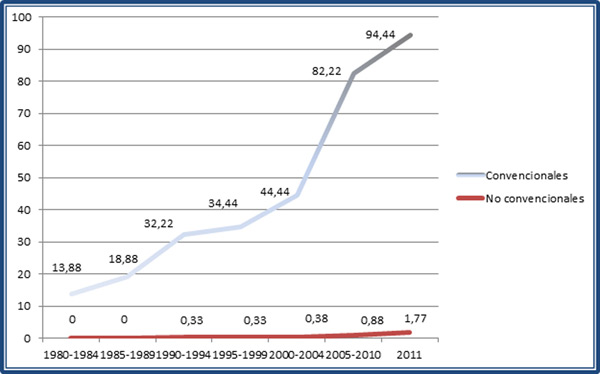
En cualquier caso, es necesario disponer de elementos de juicio para poder efectuar un análisis comparativo que permita seleccionar las tecnologías más adecuadas para el taladrado de este tipo de materiales sobre la base de criterios de cercanos a las variables habitualmente empleadas, como son material a mecanizar, herramienta: geometría y material, parámetros de corte, fuerzas de corte y potencia de corte, proceso de mecanizado, tipología de la viruta, acabado superficial, fricción y temperatura de corte, lubricación, desgaste y vida de herramienta y vibraciones.
En el caso de los CFRP, la calidad de los agujeros está determinada principalmente por defectos geométricos, la delaminación, y el daño térmico [1, 7, 11]. En la tabla 1 se reproduce, una tabla comparativa en la que se resume la defectología de los agujeros desarrollados por distintas técnicas.
Tabla 1. Defectología de los taladros por diferentes tecnologías
Tipo de Defecto |
Tecnología convencional |
Tecnología Láser |
Tecnología AWJM |
Delaminación |
X |
|
X |
Conicidad |
|
X |
X |
HAZ (Zona afectada térmicamente) |
X |
X |
|
Circularidad |
X |
X |
X |
Cilindricidad |
X |
X |
X |
La delaminación está caracterizada por la separación de capas adyacentes del laminado causado por una acción externa y depende no sólo de la naturaleza de la fibra o de la resina sino también de las propiedades de la unión. La conicidad no es más que una diferencia uniforme de diámetro que resulta en una cuña o una figura cónica. El defecto circular está relacionado con la orientación de las fibras de la capa afectada y depende de la posición angular de los ejes de corte [10], el comportamiento unilateral de las fibras de carbono conduce a la forma elíptica del agujero. La zona afectada térmicamente (HAZ, de Heat Affected Zone) se acota a la región en la cual la temperatura excede a la temperatura de vaporización de la matriz [11].
De acuerdo con [12-20] los principales estudios para el taladrado convencional de CFRP se han orientado al análisis del empleo de las brocas con diferente composición, recubrimientos, geometría y parámetros de corte, basados, fundamentalmente en la caracterización de la delaminación y el establecimiento de correlaciones con la fuerza de empuje ejercida. Adicionalmente, se han realizado estudios de rugosidad, daño térmico [9, 10, 21-23], echándose en falta la existencia de estudios sistemáticos en los que se contemplen las distintas variables.
En el caso del taladrado con haz láser (LBM, de Laser Beam Machining) las propias características de la técnica [24] han motivado que la evaluación de la calidad de los agujeros se haya centrado, especialmente, en el daño térmico y las desviaciones macrogeométricas de conicidad [11, 15, 25-27], además del mismo tipo de estudios realizados para taladrados convencionales.
En cuanto a los parámetros de estudio para la calidad de los agujeros por taladrado láser, han servido como base también para el estudio de la calidad de los orificios mediante mecanizado con chorro de agua (WJM, de Waterjet Machining, o AWJM, de Abrasive Waterjet Machining) [44, 48].
A partir de los datos recogidos en la bibliografía, en la tabla 2, se ha establecido un resumen comparativo para las distintas tecnologías empleadas.
Tabla 2. Comparativa entre tecnologías
|
Tecnología convencional |
Tecnología Láser |
Tecnología AWJM |
Fuente de Energía |
Mecánica |
Luz |
Hidromecánica |
Inversión inicial |
Media |
Alta |
Alta |
Coste de operación |
Media |
Bajo |
Bajo-Medio |
Coste del equipo |
Medio |
Alto |
Alto |
Mantenimiento |
Medio |
Bajo |
Medio |
Flexibilidad |
Media |
Alta |
Alta |
Tiempo de operación |
Alto |
Bajo |
Medio |
Contaminación |
Media |
Baja |
Media |
Producción de polvo |
Si |
No |
No |
Producción de gases |
No |
Si |
No |
Necesidad de taladro inicial |
No |
No |
No |
Precisión |
Buena |
Alta |
Media |
Tamaño del agujero |
Medio |
Todos |
Medio y Grande |
Agujero ciego |
Si |
No |
No |
Espesor limitado |
Si |
Si |
No |
Efecto taper |
No |
Si |
Si |
Riesgo de delaminación |
Si |
No |
Si |
Fuerzas de corte |
Alta |
Inexistente |
Baja |
HAZ |
Media |
Alta |
Inexistente |
Conclusiones
La mejora del rendimiento en un proceso y sistema de fabricación debe contemplar aspectos económicos, energéticos y medioambientales. En la industria aeronáutica, una aproximación a la maximización del rendimiento se puede llevar a cabo a partir del empleo de materiales más ligeros y con mejores propiedades fisicoquímicas. Entre estos materiales se encuentran los materiales compuestos reforzados con fibra de carbono, cuyo empleo se está extendiendo hasta alcanzar porcentajes superiores al 50% en los elementos estructurales de las aeronaves. Estos materiales deben soportar diferentes procesos de conformado antes de adoptar su forma final. Entre dichos procesos se encuentran los procesos de mecanizado y, muy especialmente, los procesos de taladrado. La naturaleza de estos materiales hace que su maquinabilidad presente especiales dificultades, lo que se refleja en una defectología específica muy característica en el caso de los procesos de taladrado. En estos procesos, en los últimos años se ha tratado de aplicar un conjunto de tecnologías no convencionales que puedan mejorar el rendimiento.
De todo lo anteriormente apuntado, cabe destacar que cada una de las tecnologías señaladas produce un tipo de defectología a la pieza mecanizada que afecta a la calidad del orificio realizado. Por tanto, se deben estudiar los parámetros que gobiernan el proceso de corte para lograr minimizar dichos daños. Por otro lado, el procesamiento de este material mediante las técnicas no convencionales es bastante viable, pero se debe remarcar que no existe un proceso de mecanizado idóneo en sí, sino que dependiendo de diversos parámetros existirá un proceso más adecuado para el taladrado [45-50].
Referencias
- P. Mayuet. ‘Propuesta Metodológica y Primeros Resultados para el Estudio de la Calidad del Taladrado de Materiales Compuestos de Fibra de Carbono con Matriz Epoxídica’. Universidad de Cádiz, Escuela Superior de Ingeniería, Máster Universitario en Ingeniería de Fabricación. Cádiz (2011).
- ‘Resumen del plan ejecutivo de la plataforma aeroespacial española’. [En línea: 20/06/2.012]. URL: http://www.plataforma-aeroespacial.org/
- ‘Agenda estratégica de investigación aeroespacial. Resumen ejecutivo’. [En línea: 20/06/2.012]. URL: http://www.plataforma-aeroespacial.org/
- ‘¿Qué son las JTI?’ [En línea: 22/11/2.011]. URL:http://www.oemicinn.es/programas-e-iniciativas/iniciativas-tecnologicas-conjuntas-jtis/ultimas-noticias/reportaje-que-son-las-jti
- ‘Armonización de las actividades en materiales compuestos para aeronáutica y el espacio en España’. [En línea: 22/11/2.011]. URL: http://www.plataforma-aeroespacial.org/
- J. Salguero. ‘Estudio del proceso de fresado periférico de alta velocidad de la aleación de uso aeroespacial UNS A92024-T3’. Universidad de Cádiz, Escuela Superior de Ingeniería, Programa Interuniversitario de Doctorado en Ingeniería de Fabricación. Cádiz (2008).
- M. Álvarez. ‘Estudio preliminar del taladrado de materiales compuestos de uso aeronáutico’. Universidad de Cádiz, Escuela Superior de Ingeniería, Programa Interuniversitario de Doctorado en Ingeniería de Fabricación. Cádiz (2008).
- ‘Materiales Compuestos en la Industria Aeronáutica’. [En línea: 24/06/2.012]. URL:http://es.scribd.com/doc/6114467/MATERIALES-COMPUESTOS-AERONAUTICA-AIRBUS
- ‘Materiales Compuestos en la Industria Aeronáutica. Nuevos desarrollos de materiales compuestos de matriz orgánica’. [En línea: 24/06/2.012]. URL: http://www.urjc.es/fundacion/cursos_verano/ponencias/josesanchez.pdf
- ‘Jornada materiales compuestos para aeronáutica y el espacio en España’. FIDAMC. España (2010).
- A.M. Abrao, P.E. Faria, J.C. Campos Rubio, P. Reis, J. Paulo Davim. ‘Drilling of fiber reinforced plastics: A review. Journal of Material Processing Technology’, Volume 186 (2007). 1-7.
- M. S. Carrilero, M. Marcos. ‘Relaciones Paramétricas en el Mecanizado’, Servicio de Publicaciones de la Universidad de Cádiz. Cádiz (España). 1994.
- ‘El Mecanizado Moderno (Manual Práctico)’, Sandvik Coromant, Dtpo. de Ediciones Técnicas, Primera edición (España).1994.
- H. El-Hofy. ‘Machining Processes. Conventional and Non-Conventional Processes’. Taylor and Francis Group. UK. 2007
- G. Boothroyd, W. A. Knight. ‘Fundamental of machining and machine tools Marcel Dekker’, Inc. Segunda Edición. 1989.
- N. Marín, ‘Análisis termomecánico de la influencia del desgaste geométrico de las herramientas en procesos de corte ortogonal de aceros inoxidables austeníticos’, Universidad Carlos III, Leganés, Madrid (España).
- M. Batista. ‘Caracterización de elementos de desgaste de herramienta de corte por adhesión secundaria en el torneado en seco de aleaciones de aluminio’, Universidad de Cádiz, Escuela Superior de Ingeniería, Máster Oficial en Ingeniería de Fabricación. Cádiz (2008).
- S. Rawat, H. Attia. ‘Wear mechanisms and tool life management of Wc-Co drills dry high speed drilling of woven carbon fibre composites’. Wear, Volume 267 (2009). 1022-1030.
- S.C. Lin, I.K. Chen. Drilling carbon fiber-reinforced composite material at high speed. Wear, Volume 194 (1996). 156-162.
- S. Abrate, D.A. Walton. ‘Machining of composite material. Part I: traditional methods. Composites manufacturing’, Volume 3, Nº2 (1992). 75-82.
- L.N. López de Lacalle, J.A. Sánchez-Galíndez, A. Lamikiz. ‘Mecanizado de alto rendimiento’. Ediciones técnicas Izaro. Bilbao (España). 2004.
- R. Piquet, B. Ferret, F. Lachaud, P. Swider. ‘Experimental analysis of drilling damage in thin carbón/epoxy plate using special drills’. Composites: part A. Applied sciencie and manufacturing, Volume 131 (2000). 1107-1115.
- M. Álvarez, M. Sánchez-Carrilero, B. Grille, J. M. Sánchez, F. Torres, M. Barro, J. M. González, M. Marcos. ‘Estudio del taladrado de fibra de carbono’. Anales de Ingeniería Mecánica, Volumen 14 (2003). 1635-1638.
- F. Girot. ‘Mecanizado de materiales compuestos. Seminario de Ingeniería de Mecanizado de Materiales Compuestos’. Universidad de Cádiz, 2012.
- R. Teti. ‘Machining of composite materials’. CIRP Annals - Manufacturing Technology, 51(2002) 611-634
- H.K. Tönshoff, W. Spintig, W. König. ‘Machining of holes developments in drilling technology’. CIRP Annals - Manufacturing Technology, 43 (1994). 551-561.
- ‘Tecnología de fabricación’ [En línea: 20/11/2.011]. URL: http://www.izaro.com/contenidos/ver.php?id=es&se=3&su=32&co=1297422668
- ‘Eficiencia en despegue’. Metalworking world. Sandvik Coromant. Volumen 1 del año 2010.
- Precorp. ‘Aerospace solutions’. Catálogo de herramientas aeronáuticas, 2012.
- W. König, C. Wulf, P. Graβ, H, Willerscheid. ‘Machining of fibre reinforced plastics’. Annals of the CIRP, 34 (1985). 537-548.
- R. Piquet, B. Ferret, F. Lachaud, P. Swider. ‘Experimental analysis of drilling damage in thin carbón/epoxy plate using special drills. Composites: part A. Applied sciencie and manufacturing’, Volume 131 (2000). 1107-1115.
- H. Hocheng, C.C. Tsao. ‘The path towards delamination-free drilling of composite materials’. Journal of Material Processing Technology, Volume 167 (2005). 251-264.
- C.C. Tsao. ‘Investigation into the effects of drilling parameters on delamination by various step-core drills’. Journal of Material Processing Technology, Volume 206 (2008). 405-411.
- C.C. Tsao, Y.C. Chiu. ‘Evaluation of drilling parameters on thrust force in drilling carbon fiver reinforced plastic (CFRP) composite laminates using compound core-special drills’. International Journal of Machine Tools & Manufacture, Volume 51 (2011). 740-744.
- H. Hocheng, C.C. Tsao. ‘Comprehensive analysis of delamination in drilling of composite materials with various drills bits’. Journal of Material Processing Technology, Volume 140 (2004). 335-339.
- L.N. López de Lacalle, J.A. Sánchez-Galíndez, A. Lamikiz. ‘Mecanizado de alto rendimiento’. Ediciones técnicas Izaro. Bilbao (España). 2004.
- S.C. Lin, I.K. Chen. ‘Drilling carbon fiber-reinforced composite material at high speed’. Wear, Volume 194 (1996). 156-162.
- W. König, P. Graβ. ‘Quality definition and assessment in drilling of fibre reinforced thermosets’. Annals of the CIRP, Volume 38 (1989). 119-124.
- L.S. Shyha, D.K. Aspinwall, S.L. Loo, S. Bradley. ‘Drill geometry and operating effects when cutting small diameter holes in CFRP’. International Journal of Machine Tools & Manufacture, Volume 49 (2009). 1008-1014.
- A. Langella, L. Nele, A. Maio. ‘A torque and thrust prediction model for drilling of composite materials’. Composites: part A. Applied sciencie and manufacturing, Volume 36 (2005). 83-93.
- M. Álvarez, M. Sánchez-Carrilero, J.E. Ares, J. M. González, M. Marcos. ‘Influencia de la relación velocidad de corte-avance en la calidad superficial de muestras taladradas de fibra de carbono’. Revista de Metalurgia, Volumen Ext. (2005). 361-364.
- A. Faraz, D. Biermann, K. Weinert. Cutting edge rounding: an innovate tool wear criterion in drilling CFRP composite laminates. International Journal of Machine Tools & Manufacture, Volume 49 (2005). 1185-1196.
- K. Ogawa, E. Aoyama, H. Inoue, T. Hirogaki, H. Nobe, Y. Kitahara, T. Katayama, M. Gunjima. ‘Investigation on cutting mechanism in small diameter drilling for CFRP (thrust forcé and surface roughness at drilled hole wall)’. Composite Structures, Volume 38 (1997), 343-350.
- K. D. Avanish, Y. Vinod, Laser beam machining—‘A review, International Journal of Machine Tools & Manufacture 48’, (2008), 609-628.
- Z. L. Li, P. L. Chu, H. Y. Zheng, and G. C. Lim, ‘Process development of laser machining of carbon fibre reinforced plastic composites’, SIMTech technical reports (STR_V10_N1_03_MTG).
- C.Y. Yeo, S.C. Tam, S. Jana, M. W.S. Lau, ’ A technical review of the laser drilling of aerospace materials’, Journal of Materials Processing Technology, 42, (1994),15-49.
- C. F. Cheng, Y. C. Tsui, T. W. Clyne, ‘Application of a three-dimensional heat flow model to treat laser drilling of carbon fibre composites’, Acta Metallurgica, Vol. 46, No. 12, (1998) pp. 4273-4285.
- D.K. Shanmugam, T. Nguyen, J. Wang, ‘A study of delamination on graphite epoxy composites in abrasive waterjet machining, Composites: Part A’, 39, (2008), 923-929.
- C. A. Friend, R.W. Clyne, G.G. Valentine, ‘Machining graphite composite materials’, Proc. 6th Symp. on Composite Materials in Engineering Design, ed. Noton, B.R., ASM, (1973), 242-250.
- R.B. Adams, ‘Waterjet machining of composites’, Society of Manufacturing Engineers, Conference on Composites in Manufacturing, 5th, Los Angeles (EE UU), 1986.