Electroerosión y mecanizado de alta velocidad: tecnologías actualizadas para los retos de la industria médica
Desde GF AgieCharmilles hemos visto que para mantenerse en la línea de continua evolución y poder responder a las elevadas exigencias del sector médico, es imprescindible invertir en tecnología, desarrollo y seleccionar minuciosamente los procesos de fabricación más adecuados. Existe una clara tendencia a la miniaturización de los componentes para la consecución de operaciones cada vez más complejas o la realización de intervenciones menos invasivas. Por otro lado la diversificación de los materiales de aplicación médica también tiene sus efectos en la evolución de las tecnologías empleadas para la fabricación.
Así es como desde métodos ya conocidos tales como la electroerosión (donde AgieCharmilles es pionera y actualmente está celebrando el 60 aniversario de esta tecnología) y el mecanizado de alta velocidad o más conocido como HSM, son tecnologías que han ido evolucionando y mejorando para poder mantenerse a la vanguardia de los procesos de mecanizado.
Pero ¿cuál es el ámbito de aplicación de estas dos tecnologías y qué avances aportan al sector médico?
La electroerosión, cada vez más sofisticada
Para los neófitos, la electroerosión se basa en la conductividad eléctrica de la pieza a mecanizar. La aplicación de una diferencia de potencial eléctrico entre un electrodo situado a una corta distancia de la pieza crea un canal de ionización en el dieléctrico donde está sumergida. Una chispa se genera y la implosión de plasma en el canal conlleva el arranque de material por erosión de la pieza.
Con un electrodo de forma, se pueden obtener cavidades de geometría compleja mediante la llamada electroerosión de penetración. En cambio, si se emplea un hilo como electrodo, con su desplazamiento se obtiene el corte de superficies regladas con la electroerosión por hilo.
Esta tecnología permite la obtención de formas complejas y mantener grados de tolerancia muy estrechos así como acabados de gran calidad. El ámbito de su aplicación se limita a los materiales conductores. Con la EDM, no existe contacto físico entre herramienta y pieza, por tanto los esfuerzos de corte desaparecen. Esto permite sobrepasar los límites de lo viable con procesos comunes como fresado y rectificado, sobre todo cuando se buscan las fronteras en la miniaturización de los componentes. En este campo, el proceso es muy fiable y económico, incluso en las aplicaciones más complejas o los materiales de difícil mecanizado para otros métodos.
La evolución de las máquinas de electroerosión ha permitido importantes y atractivos avances para la industria del sector médico. Generadores de altas prestaciones que no alteran las propiedades de los materiales (conocidos como CC o Clean Cut), nuevos softwares con tecnologías de erosión específicas para los distintos materiales, máquinas de corte por hilo con doble cabezal para trabajar con diferentes diámetros de hilo, el empleo de ejes adicionales de rotación de pieza, sistemas de robotización y automatización, son algunos de los avances que se han producido para mejorar la productividad de la electroerosión y ampliar el abanico de su aplicación.
Numerosos desafíos planteados por los elementos a fabricar para el sector médico encuentran su solución con estos avances. Así el trabajo de piezas de pequeñas dimensiones (inferior a 10 mm2) se vuelve más accesible y abre nuevos horizontes con la reducción máxima de radios internos con cortes de hilo hasta 0,02 mm de diámetro, la ausencia de rebabas en pieza y la máxima calidad superficial.
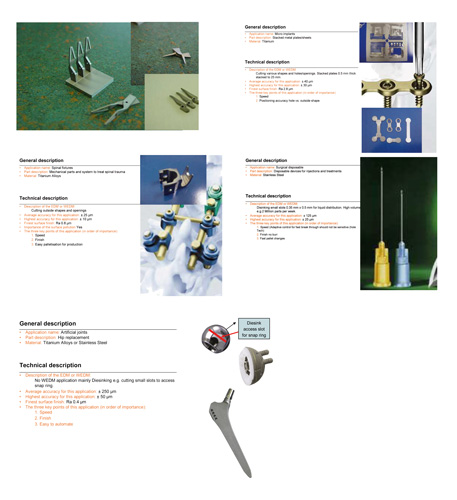
Para la implantología y la fabricación de material quirúrgico, el progreso de la electroerosión, con los generadores CC “Clean Cut” y las tecnologías de corte adaptadas, ha aportado mejoras no solo reduciendo los tiempos de producción, sino también en la obtención de superficies “limpias” reduciendo de forma considerable la contaminación superficial de pieza derivada del proceso de corte y degradación del hilo. Así, aparte de una mayor calidad de acabado superficial, se obtiene también una menor contaminación de la pieza y alteración de su composición química en la zona superficial. Como ejemplo, en el corte por hilo de piezas en aleaciones de titanio, los generadores CC Clean Cut evitan la oxidación del titanio y dejan la superficie exenta de latón y zinc provenientes de la degradación del hilo.
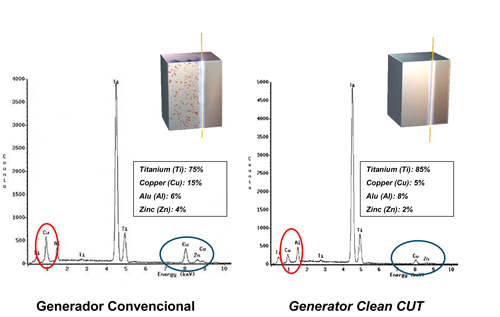
Avances en fresado
La tecnología del fresado también ha sabido evolucionar para mantenerse a la vanguardia de los métodos productivos para el sector médico. El mecanizado de alta velocidad se ha hecho hueco y es uno de los procesos de mayor crecimiento actualmente en el campo de la implantología. Las nuevas técnicas de mecanizado, la evolución de las máquinas y las herramientas de corte especializadas permiten sacar mayor rendimiento al fresado. Bien sea para las ya conocidas aleaciones de titanio, cromo cobalto y otros aceros inoxidables, también se ha ido adaptando a la aparición de nuevos materiales plásticos, composites o incluso cerámicos que se extienden en el ámbito de aplicación de la industria médica.
Con el mecanizado de alta velocidad HSM, como su nombre indica, se aumenta la velocidad de corte entre herramienta y material. Esto tiene un efecto de aumento de temperatura local en la zona de corte y evacuación del calor con la viruta o material desprendido. Los esfuerzos de corte se reducen considerablemente, la capacidad de arranque de material aumenta y se consiguen mejores calidades superficiales y precisión dimensional de pieza.
Avances tecnológicos como el empleo de electromandrinos de alta frecuencia, que pueden hacer girar la herramienta hasta más de 50.000 revoluciones por minuto, el afianzamiento de la tecnología de motores lineales, la transmisión directa en los ejes giratorios de las máquinas de 5 ejes y la evolución de los controles numéricos han ido madurando esta tecnología dotándola de una mayor versatilidad y ampliando su espectro de aplicación.
La tendencia actual viene marcada por el empleo de centros de mecanizado de 5 ejes con prestaciones de elevada dinámica y aceleración. Estas características aportan considerables ventajas para dar solución a los desafíos del mecanizado para el sector. El empleo de 5 ejes (3 de desplazamiento lineal y 2 de rotación) permite dar a la herramienta la orientación idónea respecto a la pieza en todo momento. Así se puede acceder a niveles de complejidad geométrica elevados de manera productiva. La gran dinámica de desplazamiento en el mecanizado, no solo en velocidad sino también en aceleración, aporta en primer lugar una reducción de tiempos de producción. Para el proceso de corte también provoca una estabilización y mejora de las condiciones de corte para la herramienta. Esto se traduce en una reducción del desgaste y por tanto aumento de la vida útil de herramienta, se mejora así la calidad superficial obtenida incluso en materiales de difícil mecanizado. El resultado son piezas de alta complejidad en menor tiempo, con máxima calidad y precisión y una optimización de costes de herramientas.
Un punto clave para sacar el máximo provecho de esta tecnología es el desarrollo de la automatización y gestión del proceso. En efecto se está viendo como en el sector crece la demanda de sistemas de automatización. Por una parte con la robotización de los centros de mecanizado y por otra en sistemas de programación CAM cada vez más automáticos y especializados para aplicaciones concretas. La gestión automática de la información es también un punto clave para mantener la trazabilidad y minimizar los errores durante toda la cadena de proceso.
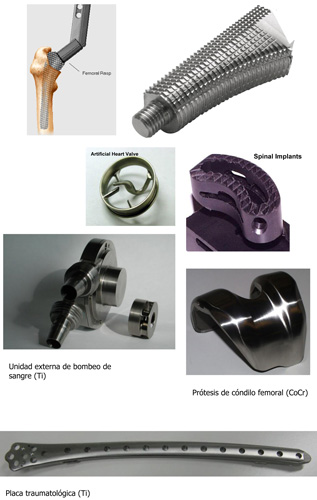
Tecnología en el ámbito dental
Un ejemplo claro donde el mecanizado de alta velocidad a aportado grandes cambios es el sector de la prótesis dental. Desde hace unos años está experimentando una auténtica revolución industrial. Se está pasado de procesos manuales que revelan auténtica artesanía a sistemas completamente numerizados.
Una nueva cadena de proceso con digitalización, diseño CAD, programación CAM y fabricación por fresado de alta velocidad es ya una realidad en este sector. En base a esta solución tecnológica se han desarrollado los llamados centros de fresado. El abanico de soluciones es muy amplio pudiendo abastecer desde pequeños centros para uno o varios laboratorios protésicos hasta centros industrializados con capacidad de cobertura internacional.
Para dar respuesta a la demanda, tanto fabricantes de máquina, como desarrolladores de software de diseño y programación, así como los proveedores de herramienta han sabido adaptarse para ofrecer soluciones integrales basadas en esta tecnología. El resultado es la obtención de células de fabricación especializadas dedicadas a productos concretos pero con la flexibilidad suficiente para adaptarse a los requisitos específicos de cada usuario, material, método de fabricación o tipología de pieza.
Actualmente, existe una gran variedad de materiales tanto en composición como en formatos para trabajar en la aplicación médica y las proporciones de su utilización están en constante cambio. Esto supone un reto para el desarrollo tecnológico de máquinas. En efecto, es necesario que los medios productivos estén especializados para atender a las necesidades de un producto o material específico, pero deben ser a la vez flexibles para poder evolucionar y absorber los cambios con nuevos diseños o nuevos materiales.
No son las mismas prestaciones que se piden a una máquina que deba fabricar prótesis de Ti o CoCr que a la que se emplea para fresar zirconio, resinas, ni tampoco disilicato de litio u otras cerámicas. Si algunos materiales requieren el uso de refrigerante para mecanizado, otros excluyen esta opción, el arranque puede generar viruta en unos casos o polvo abrasivo en otros. Las magnitudes de fuerzas de corte generadas son totalmente distintas. Por todo ello, el diseño de una máquina de altas prestaciones debe darle la flexibilidad suficiente para adaptarse a las diferentes situaciones y requisitos sin tener que sufrir pérdidas de rendimiento o tener que ser sometida a importantes modificaciones. Un equipamiento a la carta debe permitirle enfrentarse al máximo de situaciones y problemáticas.
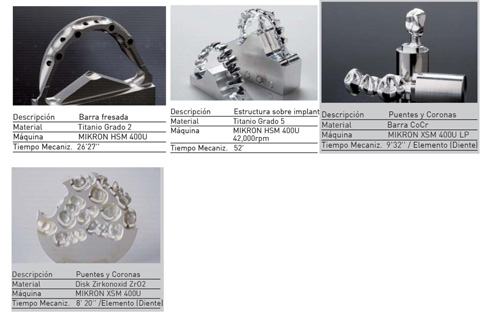
La demanda actual y la evolución de la fabricación para el sector médico exigen una combinación de tecnología puntera y saber hacer para afrontar las exigencias del presente. En un mercado en constante cambio donde la competitividad se ha vuelto un imperativo, ya no basta con tener los mejores equipamientos o máquinas más vanguardistas para crear los productos más novedosos. La rentabilidad exige sacar el máximo rendimiento de los medios productivos.
Procesos como la electroerosión o el mecanizado de alta velocidad han sabido modernizarse y hacer frente a los cambios y tendencias que marca el sector. Así aparecen cada vez más soluciones técnicas especializadas para responder a problemáticas concretas.
Sin embargo existen unas tendencias claras en la demanda tecnológica de este sector. Los fabricantes de esta industria piden soluciones integradas y el soporte de colaboradores tecnológicos, más que simples proveedores de equipamientos y maquinaria. La productividad pasa por la automatización de las cadenas de proceso y la robotización de las máquinas para maximizar su potencial. Finalmente, las soluciones especializadas no pueden ir reñidas con la flexibilidad si se deben afrontar los retos del futuro con la tecnología del presente.