Eurecat está comprometido con la transformación verde de la industria del acero y el desarrollo de nuevos aceros más resistentes
Nuevas metodologías de fabricación y optimización de aceros para avanzar hacia la descarbonización de la automoción
En la actualidad, la producción de acero genera entre el 7 y el 9% de las emisiones globales de dióxido de carbono. Tal y como destaca Eurofer, la Asociación Europea del Acero, abordar este desafío requiere cambios destacados en los métodos de producción, ya que los procesos actuales están cerca de sus límites técnicos y termodinámicos.
A nivel europeo, se han fijado ambiciosos objetivos para reducir su impacto ambiental. La Unión Europea se ha comprometido a lograr una reducción del 30% en las emisiones de gases de efecto invernadero para 2030, con el objetivo último de alcanzar la neutralidad de carbono para 2050.
Las reducciones a largo plazo requerirán la adopción de nuevas metodologías y tecnologías. Esto incluye el desarrollo de rutas de fabricación más sostenibles, el uso de nuevos materiales o bien la captura y el almacenamiento o uso del carbono. El objetivo final es reducir la huella ambiental de la producción lo más cerca posible de cero.
Sin embargo, a corto plazo, la producción de acero basada en materiales reciclados y metales más ligeros ofrece un enorme potencial de reducción de emisiones con una disponibilidad casi inmediata. Esta dirección estratégica implica una mayor optimización de los componentes metálicos y el desarrollo de tecnologías para la fabricación de aceros avanzados con bajas emisiones de CO2, cruciales para la descarbonización del sector.
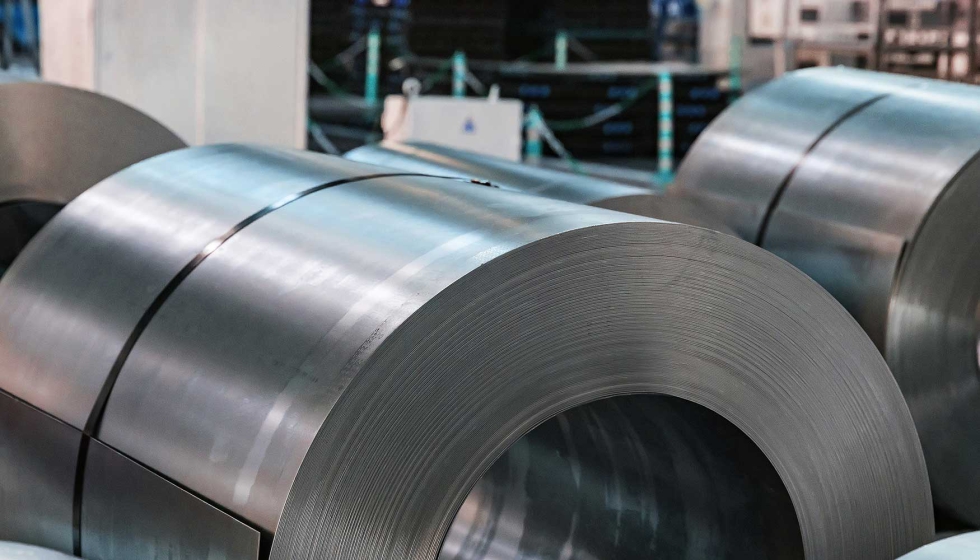
Bobina de acero para la producción de componentes en el sector de la automoción.
La transformación de la industria del acero hacia la sostenibilidad va de la mano con los esfuerzos de la industria automotriz, donde la reducción de emisiones y la preocupación por el medio ambiente es también una prioridad. La electrificación de los automóviles con el impulso de vehículos eléctricos e híbridos ha sido el enfoque hasta la fecha para reducir las emisiones durante la fase de uso. Sin embargo, la industria automotriz también debe abordar las emisiones incorporadas en los materiales del vehículo, que representan aproximadamente entre el 18 y 20% de las emisiones durante el ciclo de vida de los vehículos de combustión.
En respuesta a los desafíos de una industria tan importante para el sector del acero, representando el 16% del total de productos basados en este material en Europa según datos del 2021 de la Asociación Mundial del Acero (World Steel Association), para la industria del acero esto implica no solo desarrollar nuevas aleaciones o aceros con bajas emisiones, sino también nuevos métodos de fabricación y rediseñar los procesos existentes. Además, es importante mejorar la eficiencia en la fabricación de componentes destinados a la industria automotriz, reduciendo al máximo el uso de recursos y rechazos de producción.
El centro tecnológico Eurecat, desde su unidad tecnológica de materiales metálicos y cerámicos, está comprometido con la transformación verde de la industria del acero y el desarrollo de nuevos aceros más resistentes, a la vez que ligeros, con propiedades mejoradas para mitigar el cambio climático y garantizar un futuro sostenible.
La optimización de componentes de acero para el sector de la automoción se ha convertido en una de sus principales áreas de investigación por su gran impacto, ya que contribuye a la mitigación del cambio climático y la promoción de una movilidad más limpia y segura. Parte de las líneas de investigación se lideran en cuatro proyectos europeos financiados por el fondo de investigación para el carbón y el acero (RFCS, por sus siglas en inglés) que impulsan la optimización de diferentes calidades de acero para mejorar sus propiedades y usos en el sector de la automoción, a la vez que buscan conseguir una reducción de defectos, costes de manufactura y emisiones de dióxido de carbono en su fabricación.
Optimización de aceros de tercera generación y alta resistencia
Los aceros de temple y particionado y aceros de medio manganeso, pertenecientes a la tercera generación de aceros avanzados de alta resistencia (AHSS, por sus siglas en inglés) se caracterizan por mostrar una alta resistencia mecánica y muy buena ductilidad, ofreciendo la posibilidad de fabricar componentes para automoción de alto rendimiento más delgados y geometrías más complejas, lo que los hace especialmente adecuados para componentes estructurales de seguridad.
Estos aceros permiten optimizar el diseño de la carrocería del automóvil reduciendo el peso y mejorando la resistencia al impacto del vehículo. Se ha demostrado que el uso de AHSS en lugar de aceros convencionales o materiales de baja densidad (como el aluminio, magnesio y composites) puede proporcionar una solución más sostenible para reducir las emisiones de gases de efecto invernadero a lo largo del ciclo de vida completo del vehículo.
En este sentido, el proyecto europeo Sup3rForm se centra en la optimización de aceros de tercera generación de temple y particionado y aceros de medio manganeso con el objetivo de mejorar sus propiedades y favorecer su uso en aplicaciones estructurales ligeras que den respuesta a la necesidad de vehículos más ligeros, eficientes, seguros y económicos en la movilidad del futuro.
Para abordar los retos asociados al uso de AHSS en la industria del transporte europea y fomentar su aplicación, Sup3rForm implementará técnicas de modelización y caracterización multiescalar para identificar los principales mecanismos de daño y deformación de estos aceros avanzados de nueva generación, así como para comprender la relación entre sus microestructuras y propiedades críticas para su implementación como la conformabilidad, tenacidad de fractura, fatiga y resistencia al choque.
Así pues, en el proyecto Sup3rForm se demostrará la viabilidad industrial de los aceros de tercera generación de temple y particionado y aceros de medio manganeso para la fabricación de piezas de automóvil de alto valor añadido a bajo coste y con una menor huella de carbono a lo largo del ciclo de vida del vehículo.
El impulso del uso de estos aceros contribuye indirectamente a reducir el consumo de combustible en la industria automovilística. Esto tiene dos impactos finales en la sociedad y el medio ambiente: por un lado, la reducción de los costes de combustible contribuye a un transporte más barato y accesible y, por otro lado, el ahorro de combustible significa menos contaminantes emitidos a la atmósfera, lo que se traduce en una mayor sostenibilidad. En lo que refiere a la movilidad eléctrica, un menor peso también se traduce en una mayor eficiencia y autonomía de conducción, lo que permite reducir el consumo energético a lo largo de la vida del vehículo y alargar la vida útil de las baterías.
Además, Sup3rForm desarrollará métodos experimentales y numéricos avanzados que permitirán predecir con precisión las propiedades y el rendimiento de las piezas desde las primeras etapas de diseño, de forma que se reduzca el tiempo de comercialización de nuevos productos de acero de alto rendimiento. También se desarrollarán modelos digitales predictivos que permitirán reducir de forma drástica el número de ensayos experimentales necesarios para el diseño y optimización de nuevas microestructuras avanzadas. Esto implicará un ahorro significativo de material en la fase de desarrollo en comparación con métodos basados en prueba y error.
Se espera que con los resultados obtenidos se abra el camino para la implementación industrial de nuevas calidades de acero avanzado en el sector de la automoción y contribuyan a consolidar el papel del acero como solución ligera rentable en la movilidad futura.
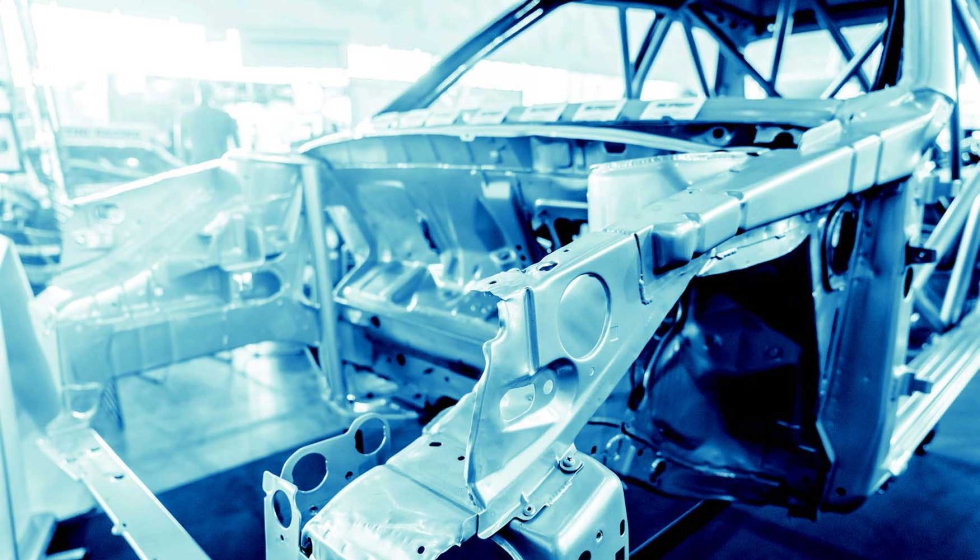
Vista de componentes de acero de un chasis de un vehículo.
Investigación europea para la producción de acero de baja huella de CO2
La aplicación de aceros de alta resistencia es una opción para la industria automotriz para cumplir con las estrictas directivas de seguridad requeridas en la construcción de carrocerías de automóviles menos pesadas y con propiedades mecánicas superiores. Sin embargo, estas ventajas conllevan desafíos técnicos significativos. La elevada resistencia de estos aceros puede traducirse en una menor conformabilidad, un aumento del comportamiento de recuperación elástica y un desgaste excesivo de las herramientas en aplicaciones de conformado en frío.
En ese contexto los aceros de estampación en caliente (Press Hardened Steels - PHS) emergen como una alternativa prevalente para la fabricación de carrocerías de automóviles. Estos aceros son materiales estructurales ligeros y resistentes, esenciales en los componentes de seguridad de los automóviles actuales; componentes con un rol crítico en la protección del pasajero durante el impacto y que llegan a suponer más del 20% de estructura de algunos vehículos modernos.
El proyecto europeo COOPHS ha sido uno de los pioneros en abordar el uso de PHS en la industria automovilística desarrollando metodologías de producción ambientalmente más respetuosas con el medio ambiente para este tipo de aceros a partir de la sustitución del alto horno como ruta de producción principal por la utilización del horno de arco eléctrico (EAF, por sus siglas en inglés).
La fabricación de aceros de estampación en caliente en hornos de arco eléctrico resulta en emisiones de dióxido de carbono más bajas, alrededor de 600 kg de CO2 por tonelada de acero producida, lo cual es significativamente menor que la ruta de producción convencional a través de altos hornos - horno de oxígeno básico (BOF), estimado en más de 2.000 kg de CO2 por tonelada. Además, se fomenta la inclusión de una alta proporción de material reciclado, lo que fortalece un modelo de economía circular dentro del industria automovilística y del acero en Europa.
Se estima que esta tecnología permitirá reducir en más de un 75% la huella de CO2 de la producción de estos aceros, además de afianzar un modelo de economía circular para la industria automovilística y el mercado europeo del acero, en línea con los objetivos del programa RFCS y el Pacto Verde Europeo.
COOPHS profundiza en los complejos efectos introducidos por los elementos residuales habituales del material reciclado en las rutas de producción en EAF sobre la microestructura y las propiedades del material. Además del rendimiento estructural del material, estos elementos de traza tienen un gran impacto en los tratamientos superficiales y recubrimientos necesarios para lograr una larga vida en servicio del componente. En este sentido, uno de los objetivos principales del proyecto es determinar las cantidades aceptables de estos elementos residuales en un despliegue industrial de estas soluciones.
Finalmente, los resultados se compilarán en una base de datos que, mediante una herramienta de agregación, permitirá garantizar un compromiso entre emisiones y rendimiento de producto final. Esta información facilitará el desarrollo e implantación de aceros bajos en CO2 en el mercado de la automoción. La investigación de COOPHS también comparará diversas soluciones existentes y propondrá rutas optimizadas de procesamiento de acero con bajas emisiones.
El proyecto COOPHS contribuirá así al avance del estado del arte en la optimización de los aceros de estampación en caliente (PHS), y de los aceros de alta resistencia en general.
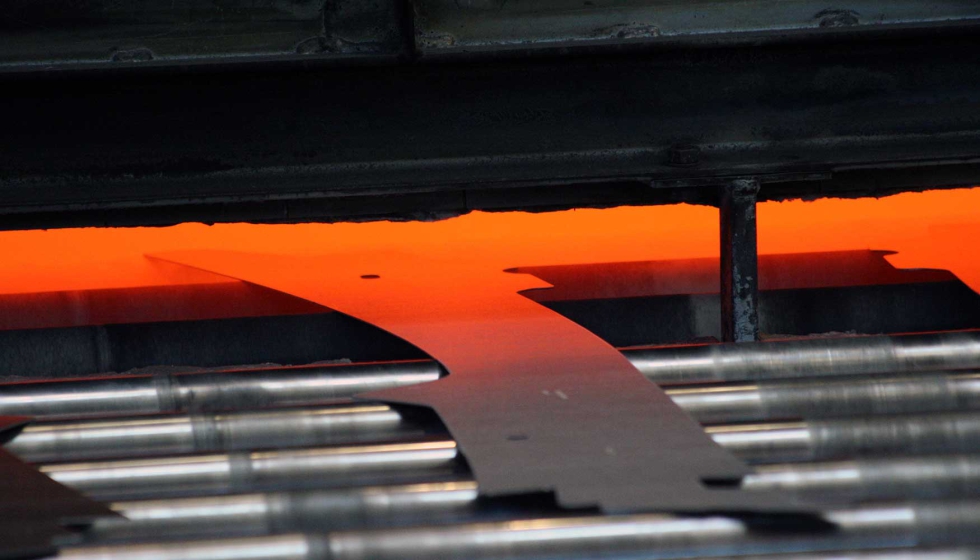
Proceso de producción de aceros de estampación en caliente.
Fabricación aditiva para aceros de alto rendimiento y piezas libres de defectos
Este enfoque tecnológico no solo está transformando la manera en que se fabrican los productos, sino que también está abriendo nuevas vías para el desarrollo de nuevos aceros vanguardistas y diseños altamente personalizados.
En el proyecto SuPreAM se están desarrollando nuevos modelos predictivos y de optimización de operaciones de acabado superficial con el objetivo de impulsar la fabricación aditiva en el sector industrial del acero y reducir defectos y costes de fabricación, que contribuirán a minimizar componentes defectuosos.
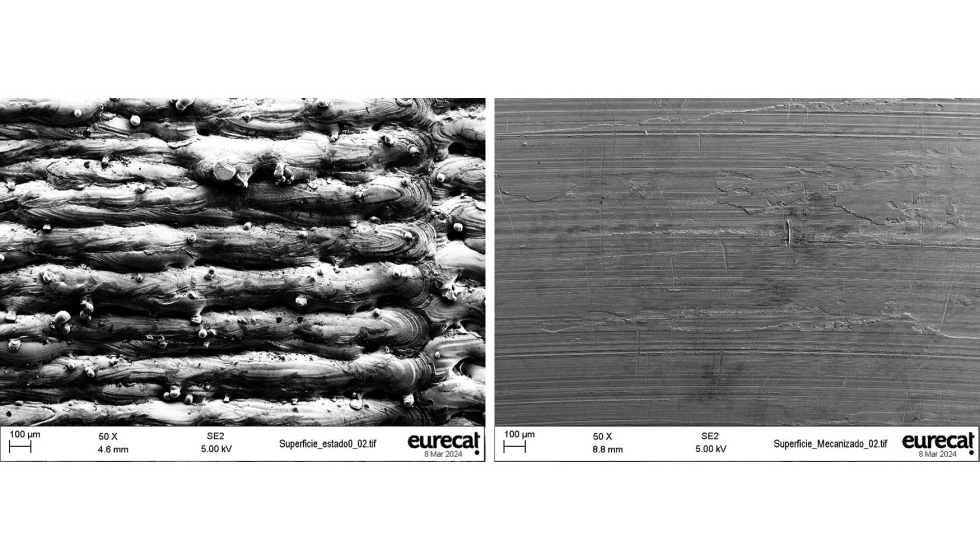
Proyecto SuPreAM - Imágenes de microscopía electrónica de una superficie de acero obtenida por fabricación aditiva (SEM AM) y después de un post proceso de mecanizado (SEM Mecanizado).
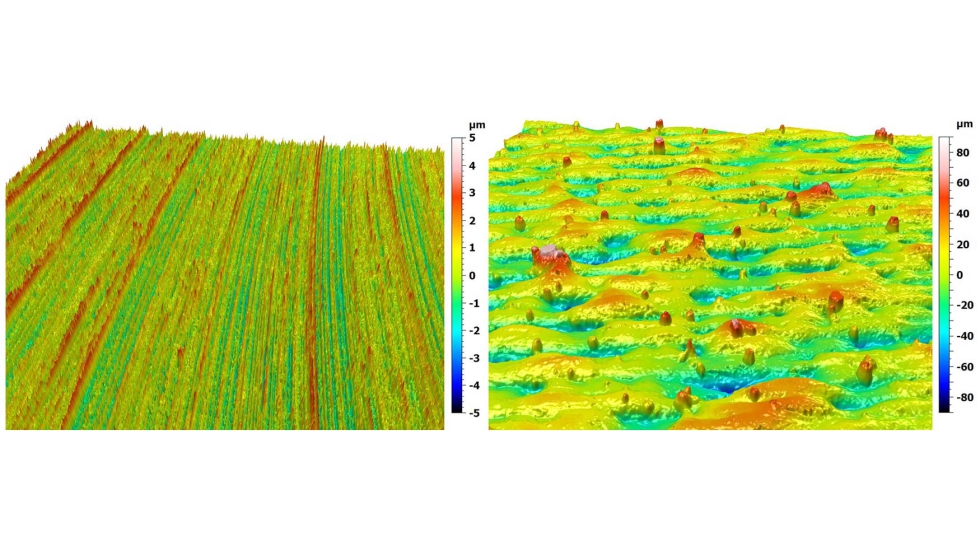
Proyecto SuPreAM - Imágenes topográficas de una superficie de acero obtenida por fabricación aditiva (Topografía AM) y después de un post proceso de mecanizado (Topografía mecanizado).
Para el desarrollo de los modelos predictivos de operaciones de acabado, se considerará la influencia de la tecnología de fabricación aditiva y la calidad del acero, así como las estrategias y parámetros de postproceso de mecanizado y las propiedades superficiales de los componentes obtenidos por fabricación aditiva, que permitirán identificar las principales variables que afectan a la integridad de la superficie.
El proyecto SuPreAM se basa en la integración de todos los factores que afectan a la integridad de la superficie de piezas fabricadas aditivamente, a fin de proporcionar soluciones y estrategias de mecanizado para el acabado de la pieza en la etapa previa de diseño, y evitar la generación de chatarra, con el objetivo de producir componentes libres de defectos.
Con este fin, se han seleccionado dos casos prácticos en los que los componentes son piezas reales en uso. Se trata de un molde de inyección de plástico, donde el acabado superficial es determinante para garantizar el comportamiento del molde y la calidad de las piezas inyectadas, así como de un componente estructural para aplicación aeroespacial, que requiere resistencia a la fatiga. Además, en el proyecto se producirán demostradores de ambos casos prácticos y se utilizarán para la validación de los modelos y la comparación con el comportamiento de piezas obtenidas con aceros convencionales.
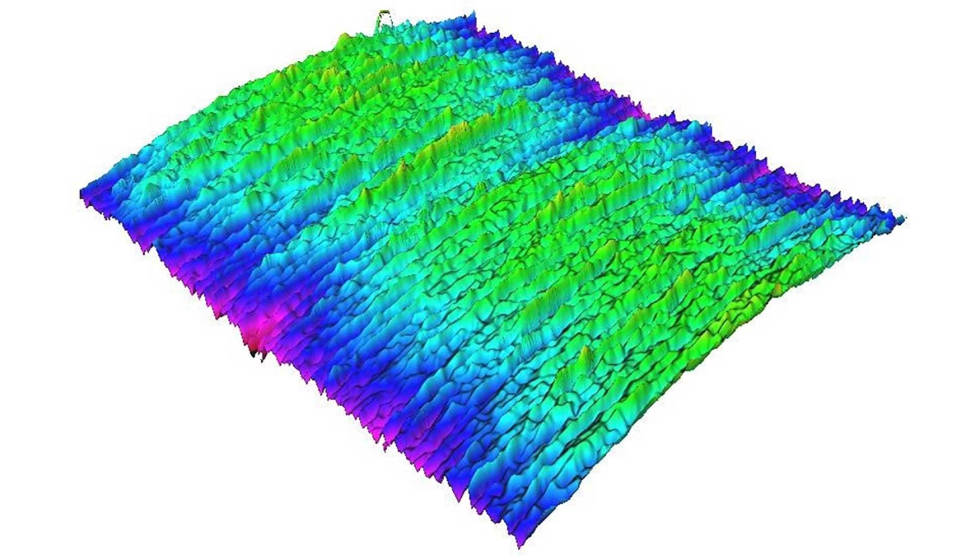
Proyecto SuPreAM - Imagen topográfica de una superficie de acero.
Por otro lado, el proyecto NewAIMS propone el uso de la fabricación aditiva de nuevos aceros de alto rendimiento, tecnología que puede permitir una reducción de costes en su producción y un desarrollo mucho más personalizado a cada cliente.
NewAIMS propone combinar una composición química de acero bien adaptada y un proceso no convencional de tiempo-temperatura para la impresión 3D. De esta forma, se pretende obtener microestructuras avanzadas con mejores prestaciones que las que se consiguen actualmente con la fabricación aditiva convencional y optimizar el rendimiento del material y las piezas finales impresas, superando limitaciones actuales. Asimismo, propone dos cualidades de acero de alto rendimiento y una demostración de soluciones de impresión basadas en tecnologías de Powder Bed Fusion (PBF) que se utilizan para el rápido prototipado, al tiempo que vincula los procesos y las microestructuras a su rendimiento final.
El proyecto implementará estas soluciones en un caso de uso basado en aceros para herramientas, una familia esencial de aceros utilizados en prácticamente todos los procesos de fabricación, y donde las características de la fabricación aditiva ofrecen un potencial muy atractivo para su implementación transversal.
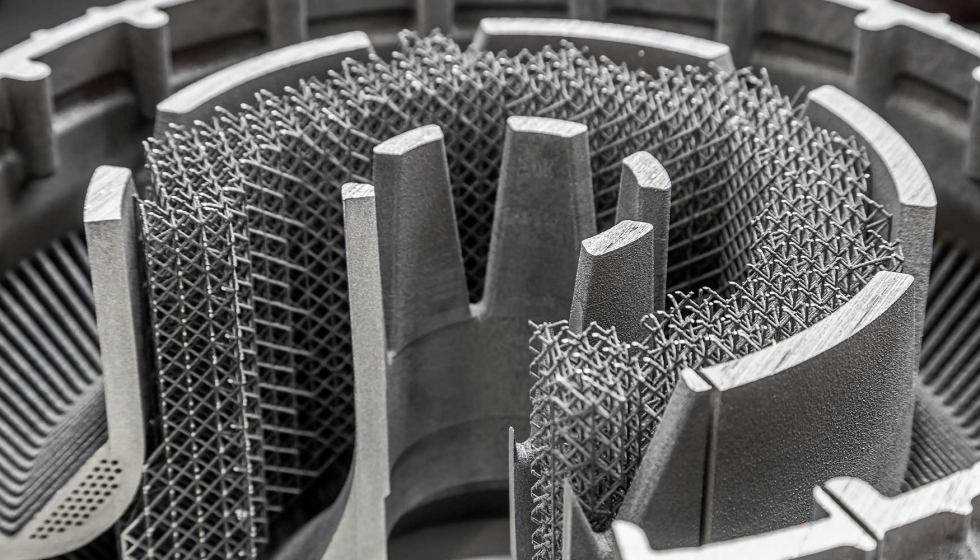
Detalle de una pieza impresa mediante fabricación aditiva.