Hexagon exhibe sus competencias en digitalización para el sector automotriz
A primeros de marzo Hexagon abrió las puertas de su Automation Centre Barcelona, para celebrar el evento HxGN LIVE ‘Soluciones para la Digitalización y Eficiencia en el sector de la Automoción’. Una jornada pensada especialmente para mostrar en directo y con demostraciones reales las soluciones de fabricación inteligente desarrolladas por Hexagon dirigidas a mejorar los procesos de ingeniería e inspección en el sector del automóvil.
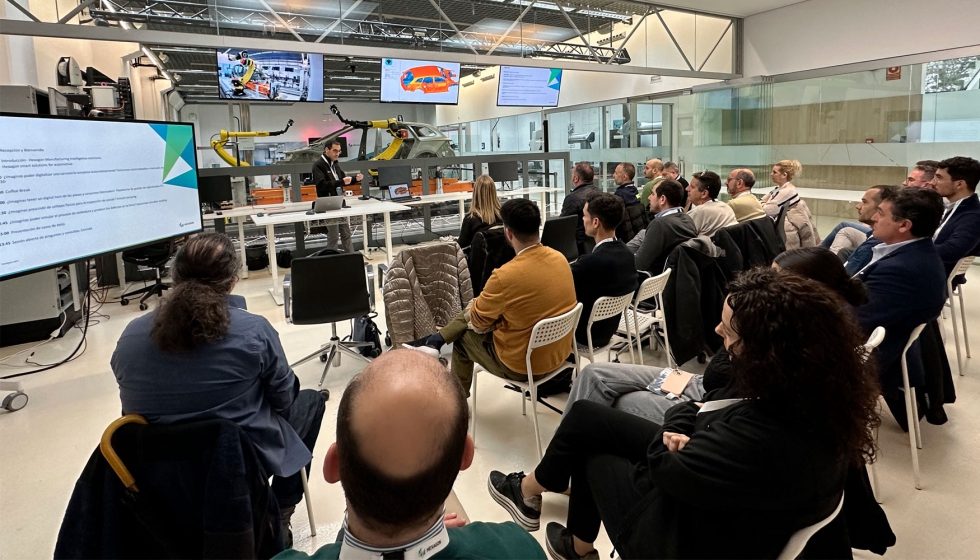
Abrió la jornada Jordi Planell, director comercial de Hexagon Manufacturing Intelligence Iberia, quien expuso la necesidad de apostar por la virtualización a fin de poder prescindir en la mayor medida posible de los utillajes físicos y apoyarse en la simulación de procesos para poderse anticipar a la fabricación antes de la producción real. El objetivo es obvio: “reducir errores y tender al máximo a la pieza cero defectos a la primera”.
En este sentido, Planell apuntó que “hoy la calidad no es solo la validación de pieza, sino que incide directamente en la producción. La propuesta de Hexagon es que la información entre procesos —ingeniería, producción, inspección, digitalización…— sea continua y en tiempo real para decidir, durante la propia etapa de producción, si deben hacerse o no cambios”. Para ello es necesario tener un control absoluto de la información “pero también saber cómo aprovecharla al máximo”.
Aquí es donde entran en juego las soluciones para la gestión de esta información, como Simufact, un software de simulación de procesos con el objetivo de alcanzar los cero defectos en producción gracias a los gemelos digitales. Hexagon cuenta en su portafolio también con soluciones como las plataformas Q-DAS y eMMA, que ofrecen potentes herramientas para su aplicación en producción industrial. Del mismo modo, VGStudio MAX ofrece análisis geométricos y de materiales completos para piezas escaneadas mediante TC, y todo en un único software.
En resumen, la transformación digital total permite el digitalizado automatizado para captar la realidad, la gestión del digitalizado como información de base y, finalmente, mediante la simulación y los procesos virtuales, se obtiene una modelización del proceso, sus parámetros y resultados. En este sentido, Planell expuso que “cualquier proceso físico susceptible de ser virtualizado supone un salto en la digitalización que aportará mucha más eficiencia, una mayor productividad y mejor calidad final”.
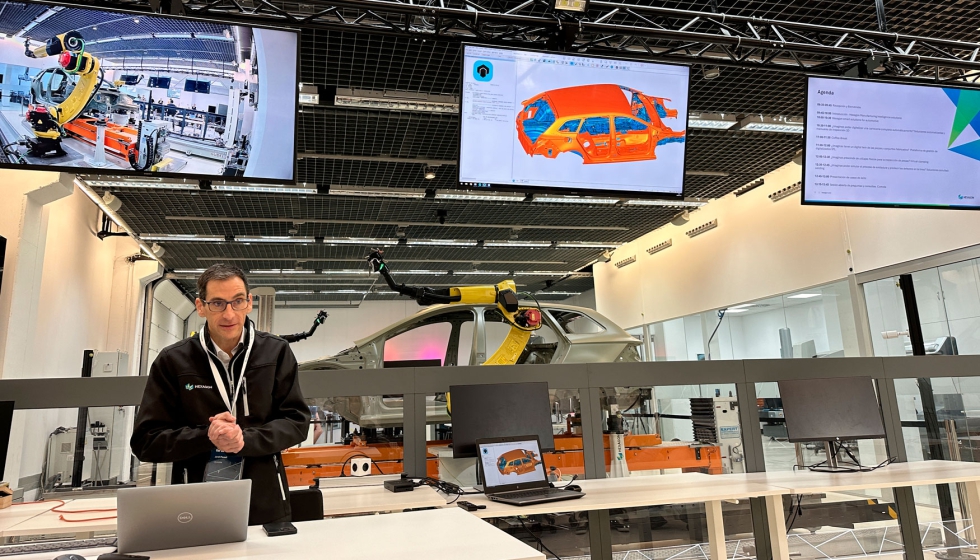
El proceso planteado por Hexagon comienza escaneando la pieza al completo y a partir de los datos obtenidos, analizar solo los parámetros que se necesite, siguiendo las fases de modelar, simular y analizar. Así, la simulación previa a la producción real permite realizar todos los cambios necesarios y anticiparse a la fase de fabricación. Aquí es donde entra en juego Nexus, una plataforma de realidad digital para fabricantes que conecta operarios, tecnologías y datos a modo de catalizador. Nexus facilita la colaboración fluida y en tiempo real entre disciplinas al permitir el intercambio seguro de datos que, de otro modo, quedarían encerrados en los departamentos. Así, mediante Nexus y con la información en tiempo real, el operario puede recibir indicaciones como si debe cambiar un utillaje, esperar que termine un proceso, etc.
Hexagon permite digitalizar una carrocería completa de manera automatizada
Christopher Juvé, especialista en programación de PLC en Hexagon Manufacturing Intelligence, fue el encargado de mostrar cómo digitalizar por completo, y de manera automática la carrocería de un vehículo mediante dos robots y dos Laser Tracker. Un sistema de escaneado que no se ve afectado ni por el color de la carrocería, ni la luz o los brillos que puedan haber (“por ejemplo pueden escanear pernos”) y no exige conocimientos previos de metrología o programación robótica. Es un sistema especialmente con velocidad y precisión de medición, adecuado para piezas de chapa y plástico de midas considerablemente grandes.
La demostración en directo permitió ver cómo programar el escaneado simulándolo previamente, confirmando así el movimiento de los robots y los Laser Tracker y asegurar que no se producirán colisiones durante la ejecución real. Durante la jornada se mostró también cómo realizar el escaneado de partes de una carrocería mediante un láser de brazo y un sistema manual.
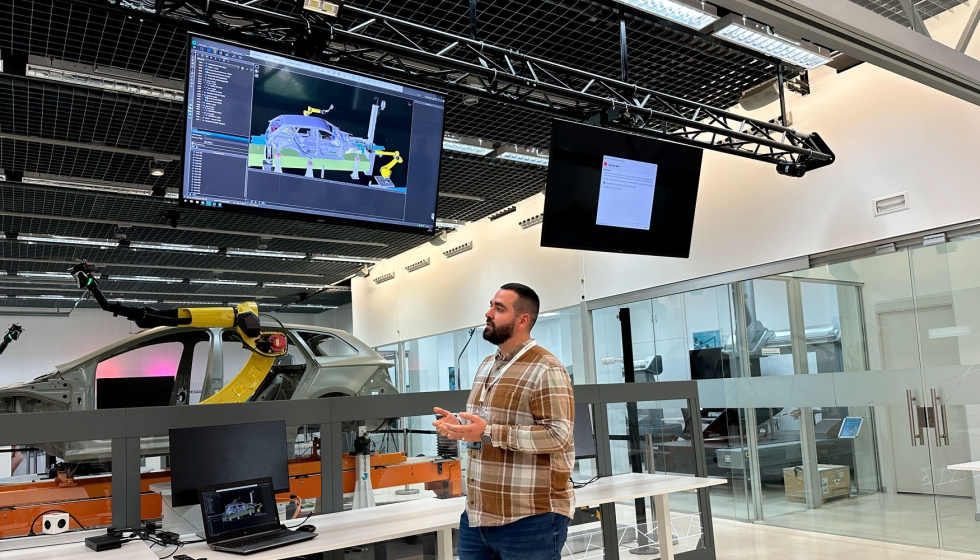
Christopher Juvé mostró un caso real de digitalización completa de la carrocería de un vehículo.
Una base de datos… de datos
Tras la pausa café, Jordi Planell retomó la palabra para explicar eMMA, un software para la gestión de datos dimensionales, planificación de calidad y análisis. Mediante sus módulos principales, eMMA MDM, eMMA Analyst y eMMA Reporter, Hexagon ofrece un conjunto de herramientas que permiten a los OEM y a sus proveedores planificar, obtener y analizar información dimensional en diferentes etapas del ciclo de vida del producto. eMMA obtiene datos del taller a partir de los diversos sistemas de metrología instalados y los incorpora en rutinas de control de calidad gestionadas para análisis automatizados y en tiempo real. Para simplificarlo, Planell lo definía como “una base de datos que agrupa todos los datos y la información obtenida mediante la digitalización”.
El software eMMA ofrece funcionalidad de origen 3D e integración a la gestión de datos del producto (PDM) y gestión del ciclo de vida del producto (PLM) así como otros sistemas personalizados, lo cual lo convierte en una herramienta indispensable para los departamentos de metrología para los fabricantes de diversos sectores industriales, como el estampado, carrocería, ensamblado, interiores de la industria de la automoción, construcción naval y otras.
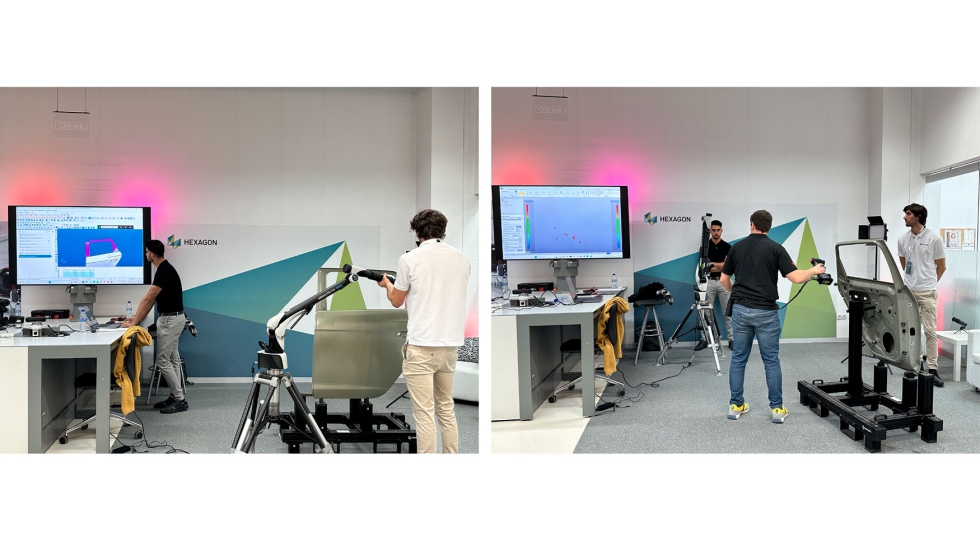
Durante la jornada se mostró también cómo realizar el escaneado de partes de una carrocería mediante un láser de brazo y un sistema manual.
Virtualizar la realidad
La digitalización permite simular múltiples situaciones a partir de usar la realidad virtual para sustituir la realidad física. Así, por ejemplo, Virtual Clamping permite prescindir de utillajes físicos para la inspección de piezas. Se trata de un proceso de virtualización que permite medir una pieza con el utillaje de posición, pero sin este utillaje: Virtual Clamping simula la sujeción de piezas en el software de escaneado y permite que el usuario calcule el estado de sujeción utilizando los datos de la pieza real en estado libre.
Las soluciones en realidad virtual de Hexagon incluyen Simufact Welding, que se utiliza para modelar y optimizar una variedad de procesos de unión térmica, teniendo en cuenta la secuencia de soldadura y el dispositivo de sujeción. Y es que, tras un proceso de soldadura, si no está optimizada, hay riesgo de que se produzcan deformaciones térmicas o tensiones residuales del conjunto que dificulten, incluso impidan, el montaje posterior porque la geometría del subconjunto está fuera de tolerancia. Con Simufact Welding, el proceso y los parámetros de soldadura pueden optimizarse para lograr la calidad de producto deseada.
Con el módulo de soldadura por arco se simulan los procesos comunes de soldadura por arco, prediciendo las tensiones residuales, la deformación y la distorsión causadas por el proceso de soldadura. Simufact Welding evalúa el impacto de varios parámetros, como la secuencia de soldadura, parámetros del proceso de soldadura por arco y estrategia de fijación.
En soldadura por láser y por haz de electrones, Simufact Welding permite simular el proceso para predecir distribución local de la tensión residual, la deformación y la distorsión. Simufact Welding tiene en cuenta las características específicas de una fuente de calor láser o de haz de electrones.
Asimismo, en procesos de soldadura por puntos por resistencia, con Simufact Welding se predice el impacto de parámetros como la secuencia de puntos, los parámetros del proceso de soldadura (fuerza, corriente, tiempo) y la estrategia de fijación/sujeción en la estructura de la soldadura. Y, con la ayuda de la sujeción virtual, es posible predecir la geometría exacta de las piezas y las estructuras ensambladas: Simufact Welding simula el comportamiento de las piezas a medida que se sujetan y sueldan en sus coordenadas designadas (por ejemplo, vehículo), lo que reduce la necesidad de prototipos o pruebas.
En resumen, la simulación permite realizar pruebas virtuales para lograr el mejor proceso de tratamiento térmico posible.
Caso real: escaneado de un espejo retrovisor
Xavier Mira, director nacional de la división de Software de producción en Hexagon Manufacturing Intelligence, expuso la experiencia de un caso real de cómo funciona el flujo de trabajo integral de Hexagon aplicado a la producción de un espejo retrovisor.
A partir del escaneado de la pieza real, se obtuvo su virtualización mediante ingeniería inversa. Aplicando posteriormente una solución de modelado, se realizaron los cambios necesarios a nivel de CAD. Mira lo explicaba así: “con VISI simulamos la producción del molde del retrovisor y, todo lo que podamos anticipar en el diseño es tiempo que ganamos en la producción posterior”. El paso siguiente fue simular las diferentes estrategias de mecanizado —“teniendo en cuenta todas las tecnologías”— o incluso la adición de material en caso de querer apostar por la impresión 3D.
En el proceso de simulación, Hexagon incluye también el control de calidad y el escaneado de la pieza en la propia máquina-herramienta, liberando así la CMM —“sin substituirla”— como fase de control previa en cas de que deba hacerse una última comprobación antes de sacar la pieza de la máquina. “Hexagon tiene soluciones para todos estos procesos de modo que, de manera integrada, permiten que la información fluya en todo momento”, concluyó Xavier Mira.
