La nueva fábrica digital, protagonista en la jornada FabConnect
El pasado 7 de marzo se celebró en el IMH (Elgoibar, Gipuzkoa), la jornada FabConnect, en la que se presentaron casos de éxito y retos sectoriales en las industrias de máquina-herramienta, aeroespacial, equipamiento, madera y diseño. Con la fábrica digital como telón de fondo, la jornada estuvo organizada por los clúster AFM, Hegan, Gaia y Habic.
Patricia Tamés, directora de Tecnología de AFM Cluster, fue la encargada de presentar la sesión, que comenzó con una breve explicación de la actividad de cada uno de los clústeres organizadores. A lo largo de las mismas se puso de manifiesto el reto que supone la transformación digital en la industria en general y, más en concreto, en la máquina-herramienta, la aeroespacial, las TICs y el equipamiento, madera y diseño. Tal y como explicó Patricia Tamés, la colaboración de estos cuatro sectores diferentes a través de sus clústeres demuestra lo mucho que la industria puede compartir en el marco de la transformación digital.
AFM, por ejemplo, cuenta con una estrategia 4.0, colabora activamente con start-ups y trabaja para acercar a las empresas, sensibilizarlas y monitorizar la situación del sector en el entorno del 4.0, también dinamizando y lanzado proyectos de I+D.
Por su parte Gaia cuenta con experiencia, conocimiento y herramientas que se pueden aplicar en diferentes entornos, especialmente en el ámbito industrial. En el clúster trabajan con el convencimiento de que, con inteligencia, con sensórica, se pueden mejorar mucho los procesos. Eso sí, parece cada vez más claro que hay que manejar el dato de una forma más inteligente.
En lo que se refiere al sector aeronáutico Hegan puso de manifiesto el reto al que se enfrenta el sector con la previsión de que en 2036 se duplicará el número de aviones de pasajero. Es decir, hay fabricar más, mejor y más rápido. Se trata de un sector muy intenso en actividades de I+D y entre las líneas prioritarias de su plan de I+D para el periodo 2017-2020 se encuentran la automatización de procesos, el mecanizado convencional avanzado, la fabricación aditiva, la fábrica inteligente y conectada y la mejora de procesos especiales (inspección, NDTs...).
Finalmente, el reto de Habic, clúster de equipamiento de edificios, incluyendo el software de un edificio, es encontrar la fórmula para que toda tecnología 4.0 aporte valor en su sector.
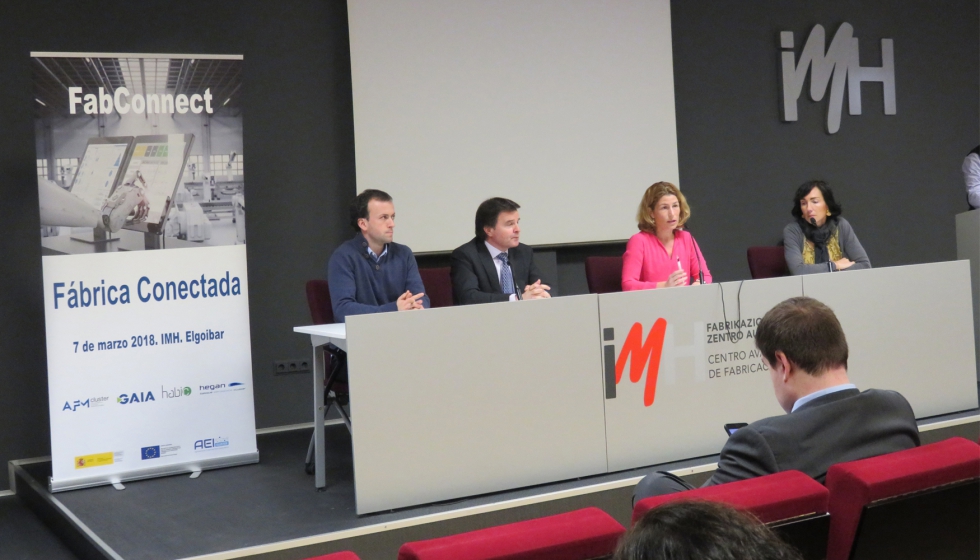
Experiencias
La asistencia remota con realidad aumentada para operaciones de mantenimiento y soporte remoto fue la primera experiencia presentada en la jornada. David Moreno, EMEA Business Development Manager de Virtualware profundizó en las posibilidades de la realidad aumentada para operaciones de mantenimiento y soporte remoto. Como ejemplo, habló del soporte remoto con realidad aumentada realizado para sus diferentes fábricas en Antzuola, China y México del Grupo Elay (Gipuzkoa), con una funcionalidad es similar al skype. El sistema implantado permite que el usuario de China y el de Antzuola estén viendo la misma imagen al mismo tiempo para así identificar el problema con más facilidad. Expuso asimismo el ejemplo de Petronas Gas Berhad (Malasia), empresa para la que se ha hecho una localización de activos en planta con realidad aumentada.
A continuación, el tema se centró en la conectividad para la máquina-herramienta. Vixion, una empresa que nace de Tecnalia y Spyro ofrece un sistema de monitorización basado en la nube que almacena datos. Está dirigido a fabricantes de máquinas y al cliente final de la máquina y se compone de tres subsistemas: el hardware industrial de captura de datos instalado en la máquina, la aplicación web alojada en el servidor y las herramientas avanzadas de análisis. En el primer caso trabajan con Beckhoff, que aporta un equipo ultracompacto de 82x82x40mm y registra de forma automática señales de la máquina. Cuenta con diversos módulos para ver muchos de los parámetros de la máquina y facilita el mantenimiento predictivo.
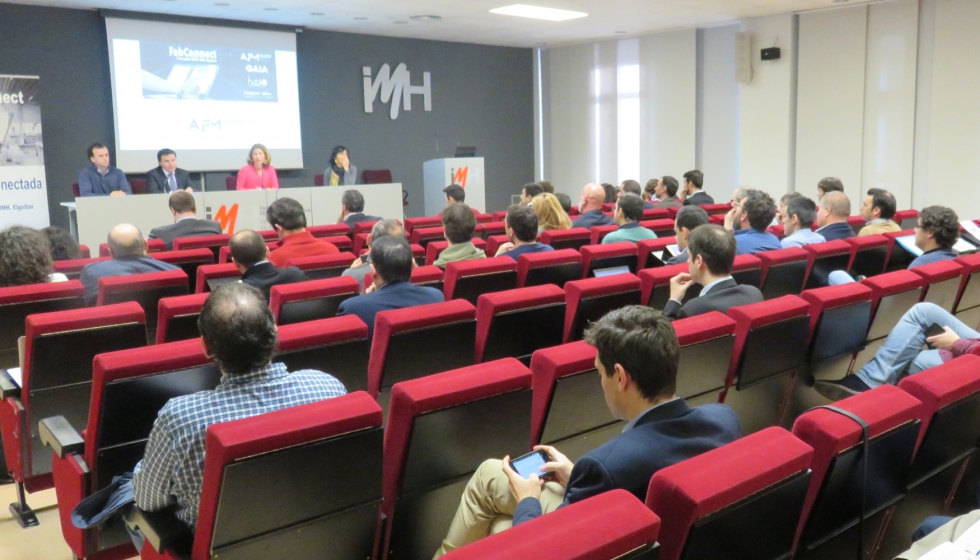
También se presentó el ejemplo de un mecanizador especializado en mecanizados de alto valor e interesado en medir e identificar la productividad. Dicho de otra forma, la empresa necesitaba saber qué estaba ocurriendo con su producción. En este caso, el producto Vixion evalúa el proceso por su nivel de vibración, que indica posibles mejoras, evalúa también el proceso por el nivel de carga en electromandrino. En el caso de Zayer, una de las partes más relevantes es el mantenimiento predictivo. Por ejemplo, se puede detectar si hay desvíos en las trayectorias de las herramientas. Zayer ha logrado integrar desarrollos suyos en la plataforma Vixion.
El control de procesos y mantenimiento en ejemplos realizados con Danobat Group (Soraluce y Danobat) y Airbus Defence & Space y ABB fue el tema de Digital Twins, una empresa que desarrolla productos y soluciones basados en realidad aumentada y realidad virtual. En el caso del trabajo con Danobat, el objetivo era aplicar la realidad en un entorno de trabajo productivo real para proporcionar al trabajador información precisa y fácilmente interpretable. A través de un tablet se monitoriza lo que está ocurriendo en la máquina en tiempo real. Otros ejemplos expuestos fueron los de Airbus y ABB, en los que se han desarrollado un sistema avanzado de asistencia al mantenimiento para generar ayudas y apoyo a los técnicos en campo. También se ha procedido a la digitalización del conocimiento de los procesos de intervención, contenidos avanzados como 3D y realidad aumentada.
La jornada se cerró con presentaciones sobre ciberamenazas (ITS Security), Industria Syncro e interoperabilidad en la industria por parte de Fran Manzano, presidente de Gaia Net Exchange y CEO de Igarle y, finalmente, Centralización y digitalización de procesos. Los cimientos para la Industria 4.0, a cargo de Gorka Ortega Pildain, director de Marketing en Lanik.