Filtración del aire de salida con contenido en lubricantes provenientes del mecanizado de metales por arranque de virutas
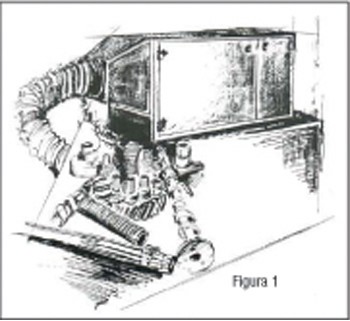
Requisitos que se le exigen a un procedimiento moderno de limpieza del aire
Buena limpieza del aire de salida: Los sistemas o aparatos de depuración del aire utilizados para la limpieza del aire de salida que contiene fluidos de corte y que se instalan en o junto a máquinas y centros de mecanizado, suelen reintroducir por lo general el aire de salida limpio nuevamente en la nave de producción. Lo mismo puede decirse de las instalaciones centrales de aspiración en las que, con el fin de evitar pérdidas de calor en invierno, se sopla de nuevo el aire dentro de la nave de producción con el aire de salida limpio recirculado.
Para disponer de este aire limpio en el interior de las naves de fabricación es imprescindible que el sistema de filtración consiga purificar el aire de forma continuada durante el proceso de mecanizado, eliminando la mayor cantidad posible de todas las sustancias “ajenas al aire“, tales como neblinas de emulsiones y aceites, carbonillas, micropartículas metálicas o materiales abrasivos, no solamente con el fin de cumplir las disposiciones de normativas legales (valores TRGS y MAK), sino también, y en primer lugar, para proteger a las personas que se encuentran en los puestos de trabajo y evitar afecciones a su salud (p. ej. irritaciones cutáneas alérgicas, enfermedades de las vías respiratorias).
Desde el punto de vista de los riesgos que pueden afectar a la salud humana tienen sobre todo una importancia considerable los aerosoles contenidos en el aire de salida contaminado, es decir las partículas de líquido suspendidas y finamente repartidas en el aire (neblina) o sustancias sólidas (carbonilla, polvos, partículas metálicas) con unas dimensiones < 0,5 µm. Estas partículas finísimas pueden ser inhaladas por las personas con el aire que respiran, llegando hasta los pulmones. A pesar de que, tal y como se muestra en la Figura 2, la parte proporcional de las mismas en la masa total de impurezas del aire es muy pequeña, es relativamente elevada la cantidad de dichas partículas.
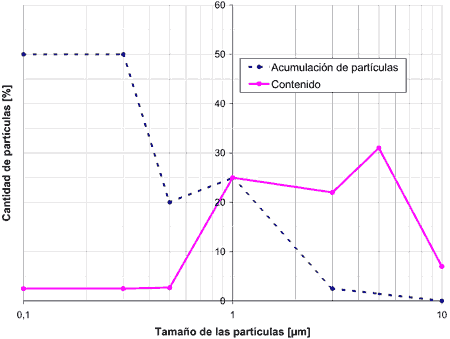
Aparte de proteger la salud de las personas debe impedirse también en el entorno de las máquinas de mecanizado la precipitación de la neblina de lubricantes de refrigeración con el fin de evitar focos de riesgos tales como el peligro elevado de resbalamientos, efectos perjudiciales sobre instalaciones de producción y climatización, así como sobre elementos de vigilancia y control eléctricos y electrónicos o un riesgo elevado de incendio debido a sedimentos o depósitos de aceite.
Costes de explotación y mantenimiento bajos: A los procedimientos y equipos de filtración y depuración del aire que se utilicen en la práctica deberá exigírseles una buena limpieza del aire de salida no solo cuando la instalación sea nueva y tras la realización de trabajos de mantenimiento, sino de la forma más continuada posible durante períodos largos de utilización de las máquinas herramientas.
Esto quiere decir que los fluidos de corte separados en los aparatos de filtración o depuración del aire junto con las partículas de sustancias sólidas que se separen, se retiren o filtren de forma tal que los componentes o elementos internos de los separadores filtrantes utilizados no queden incapacitados para su correcto funcionamiento, sino que consigan auto-limpiarse en gran medida durante el proceso de filtración.
En caso de que esto no sea factible, las consecuencias por todos conocidas serán:
- Una depuración reducida del aire hasta que se limpien los aparatos.
- Una potencia reducida de aspiración del aire, es decir saldrá neblina de fluido de corte (lubricante de refrigeración) de los habitáculos internos de las máquinas herramientas.
- Elevados costes de mantenimiento y limpieza a la hora de regenerar los filtros.
Procedimiento universal de separación: Las máquinas herramientas que se emplean actualmente para el mecanizado de metales por arranque de viruta no se utilizan únicamente para el mecanizado en húmedo o en seco, sino que, dependiendo del material que haya de mecanizarse, se realiza tanto un mecanizado en húmedo con emulsión o aceite, así como un mecanizado con lubricación mínima (MQL) o mecanizado en seco.
Esta flexibilidad de las máquinas herramientas implica también que los aparatos de separación- filtración que se empleen deberán obtener como algo absolutamente indispensable realizar la correspondiente depuración del aire sin problema alguno, con el equipo de separación instalado.
Seguridad funcional y de procedimiento: Para obtener una aspiración y limpieza plenamente operativa, satisfactoria y segura del aire de salida procedente de máquinas herramientas con contenido en fluidos de corte, deberán tenerse en cuenta u observarse los puntos siguientes:
- El equipo de aspiración instalado junto a o en la máquina de mecanizado deberá colocarse lo más cerca posible del punto en el que se origina la neblina fluidos de corte, con lo que podrá mantenerse a una distancia mínima del volumen de aire que ha de aspirarse. Ello permitirá también impedir su propagación por el entorno, de manera que puedan mantenerse las condiciones marco establecidas por las disposiciones legales.
- La potencia de aspiración indicada por el fabricante del aparato de filtración deberá ajustarse al volumen de aire aspirado en la entrada del aparato y no a la potencia del ventilador en estado de no instalación o medida en el banco de pruebas.
- El volumen de aire aspirado mientras trabaja la máquina herramienta deberá mantenerse de manera segura y fiable, con un valor constante con el fin de tener completa seguridad de que en el espacio de mecanizado de la máquina herramienta o en el entorno no se forman concentraciones excesivamente elevadas de sustancias inflamables.
- El aire de salida depurado y filtrado podrá contener, según la ZH 1/248, cuando se trate de fluidos de corte y se trabaje con aire recirculado, un máx. de 2 mg de sustancias ajenas al aire por cada m3 de aire, es decir 1/5 de los valores MAK admisibles.
Deberá garantizarse este valor incluso cuando el aparato separador haya de trabajar durante períodos prolongados de tiempo.
- El conjunto de dispositivos de aspiración, tanto si se trata de un aparato individual como si se trata de una instalación de aspiración de grupos o individuales (por máquina), no deberá influir negativamente ni sobre los procesos de mecanizado con los correspondientes equipos o dispositivos de carga y descarga, ni sobre el entorno. Los dispositivos de aspiración deberán adaptarse de acuerdo con ello a los procesos operativos de producción y no a la inversa.
Situación y realización técnica
- Separador por vía húmeda
- Separador centrífugo
- Separador electrostático
- Separador mecánico de filtración
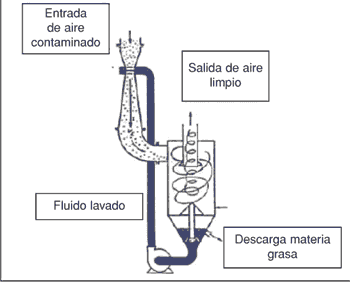
- Separadores por vía húmeda. En comparación con los otros tres procedimientos de separación o filtración únicamente se utilizan los separadores por vía húmeda en algunas ocasiones para la limpieza de aire conteniendo fluidos de corte; hablaremos también de ellos, no obstante, aunque solo sea brevemente.
En los separadores por vía húmeda se acelera el aire de salida contaminado dentro de una tobera Venturi a elevadas velocidades, rociándolo al mismo tiempo con líquido de lavado fluidos de corte. De esta forma se produce una humectación de las partículas sólidas y un aumento de tamaño de las partículas finas de líquido; es decir, se forma una cortina densa de agua de gotitas muy finas. Dentro de un separador de gotas montado a continuación se separa bajo la acción de la fuerza centrífuga el aire purificado del agua de lavado. El aire de salida purificado tras el separador por vía húmeda contiene todavía una parte residual considerable de partículas líquidas muy finas, siendo, por otro lado, muy elevada la humedad relativa del aire. Aparte de ello resultan claramente más elevados los costes de adquisición y explotación si se comparan con los de los otros procedimientos o equipos de separación.
Los separadores por vía húmeda se emplean por ello preponderantemente en el mecanizado en seco, en aquellos casos en los exista riesgo de explosiones o de incendio a causa de los depósitos o sedimentación de polvos (p. ej. en el rectificado o lijado en seco de aluminio) o cuando haya de limpiarse aire de salida muy caliente.
- Separadores centrífugos. Tal y como el propio nombre lo indica trabajan los separadores centrífugos de acuerdo con el principio de la fuerza centrífuga; véase Figura 5.
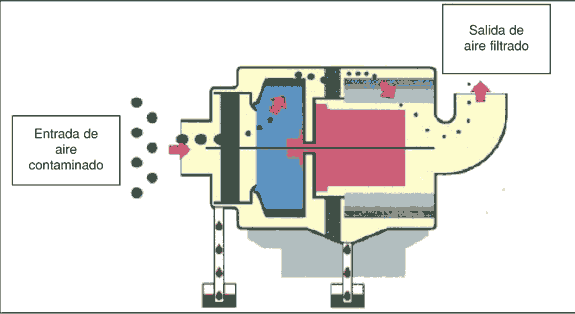
La corriente de aire aspirada de la máquina herramienta se ve acelerada hacia afuera por medio de un rodete radial rotativo con un filtro de material de esponja centrífugo, lo que da lugar a que las partículas contenidas en el aire se vean proyectadas hacia afuera como en una centrifugadora contra la carcasa o envoltura fija del separador. La película de líquido que se forma en la pared de la carcasa se escurre, gracias a la fuerza de gravedad, hacia abajo saliendo, a través de un sifón, fuera del aparato.La potencia separadora de los separadores centrífugos es, de acuerdo con las leyes de la física, tanto mayor cuanto mayores son las gotitas que han de separarse. Para la separación de neblina de fluidos de corte con un espectro o gama de partículas de aproximadamente 0,1-10 µm significa esto que únicamente se podrán separar la parte de partículas de mayores dimensiones. Según la evaluación BIA en el informe fluidos de corte-BIA, el separador centrífugo no es apropiado, y únicamente puede utilizarse con ciertas reservas como separador previo para la separación de aerosoles y humos. Esta es la razón por la que algunos fabricantes recomiendan utilizar complementariamente otro filtro para salas limpias o estériles, instalándose a continuación del primero.
En caso de paradas prolongadas existe el riesgo en los separadores centrífugos de que el fluidos de corte acumulado en el filtro de material esponjoso centrífugo se desplace hacia abajo debido a la fuerza de gravedad provocando, al volver a poner el aparato en servicio, vibraciones que influyen negativamente sobre los apoyos de los elementos giratorios.
En caso de montaje en un centro de mecanizado pueden influir negativamente dichas vibraciones sobre las tolerancias de fabricación. Es por ello por lo que los separadores o filtros centrífugos no deberán ser montados sobre las mismas máquinas de mecanizado, sino adosarse a los centros de mecanizado montándolos sobre un bastidor de apoyo independiente.
- Separadores electrostáticos. Los separadores electrostáticos aprovechan el efecto físico de que las partículas cargadas eléctricamente se ven desviadas dentro de un campo eléctrico. Tal y como puede apreciarse en el esquema de principio con la estructura de un separador electrostático que se muestra en la Figura 6, atraviesa el aire de salida, previamente limpiado en un separador previo mecánico, una zona denominada de ionización, que se encuentra sometida a una alta tensión de 6-12 kV, en la que las partículas arrastradas en el aire se cargan eléctricamente en unos alambres de wolframio a través de una descarga de efecto corona o descarga por las puntas.
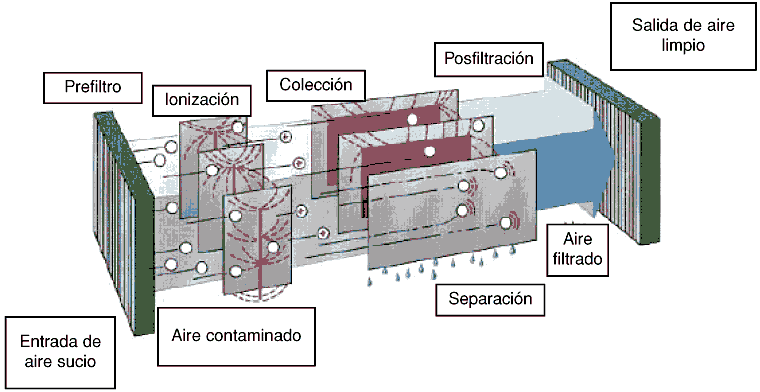
Entre las placas metálicas cargadas positiva y negativamente se crea un campo de alta tensión que provoca la desviación de las partículas cargadas hacia las placas metálicas. A través de una precipitación cada vez mayor se va formando una película de líquido que se escurre hacia abajo dentro del aparato debido a la fuerza de la gravedad y puede salir del mismo a través de un sifón. Las partículas eléctricamente cargadas que permanecen sin separar en la corriente de aire se neutralizan en un separador de tejido metálico montado a continuación, expulsándose a continuación mediante soplado.El rendimiento de separación de los separadores electrostáticos depende del tamaño de las partículas de sustancias extrañas contenidas en el aire. Con unas placas separadoras limpias se pueden conseguir los rendimientos de limpieza exigidos por la BG (mutua profesional de accidentes) < 2 µm / m3 de aire cuando se trabaja según un sistema de recirculación del aire.
Especialmente en la separación de neblina de aceite puro se consiguen unos buenos niveles de separación, siempre y cuando la película de aceite separada pueda escurrirse o deslizarse bien por las placas separadoras y se de, por tanto, un efecto de autolimpieza de las mismas.
Si, por el contrario, se ensuciasen las placas separadoras debido a partículas en forma de polvo, aceites de alta viscosidad o residuos viscosos de emulsiones, dará ello lugar a a que se vaya reduciendo progresivamente y cada vez en mayor medida la eficacia de la separación, es decir a que pueda salir del aparato aire sucio o contaminado. Además se pueden producir en las placas, debido a partículas metálicas o polvo de rectificado que se hayan adherido, descargas eléctricas que pueden provocar una desconexión no deseada de la alta tensión.
Para impedirlo deberán limpiarse los separadores electrostáticos estableciendo unos intervalos de mantenimiento no demasiado largos, con un sistema de ultrasonidos, para no dañar los componentes internos.
Se plantea otro problema cuando se utilizan separadores electrostáticos para la limpieza de aire de salida que contenga neblina de emulsiones. Debido a la buena conductibilidad eléctrica del agua pueden producirse descargas eléctricas no deseadas como consecuencia de humedades relativas del aire elevadas y de la acumulación de gotitas de agua en las placas de separación. Ello provoca igualmente desde una reducción de la capacidad de separación hasta la desconexión de la parte de alta tensión, lo que no es detectado con frecuencia por el usuario en el momento oportuno, pudiendo salir aire sin limpiar.
Es por ello por lo que se hace también referencia en el Informa BIA a la capacidad insuficiente de separación de los separadores electrostáticos cuando se trata de limpiar fluidos de corte emulsionables y no puros.
- Separadores mecánicos con filtros. Los separadores con filtros que trabajan mecánicamente están formados generalmente por una combinación, ver Figura 7, de separadores de placas de impacto o rebotamiento de distintas configuraciones para la limpieza previa del aire y de elementos filtrantes montados a continuación (generalmente filtros de salas limpias o asépticas) para la separación posterior de las partículas más finas contenidas en el aire de salida.
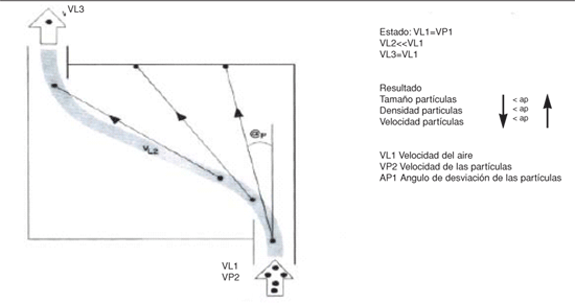
Limpieza o separación previa:
En los separadores de placas de impacto o rebotamiento instalados en sentido transversal con respecto a la dirección de la corriente de aire se canaliza la corriente de aire a través de unas estructuras interiores especiales, p. ej. perfiles desviadores o de inversión cóncavos o en forma de V desplazados correlativamente entre sí o de placas perforadas, un cambio brusco de dirección; ver modelo.
Debido a la fuerza centrífuga que se genera de esta forma y actúa sobre las partículas líquidas o sólidas se ven separadas éstas de la corriente de aire y se ven proyectadas contra las paredes de las estructuras interiores, precipitándose en dichas paredes. La película de líquido que se forma de esta manera se escurre hacia abajo, debido a la fuerza de gravedad, por las estructuras interiores verticales y puede fluir fuera de los aparatos separadores a través de un sifón. Gracias a este efecto de autolimpieza de los separadores de placas de impacto se alcanzan unos intervalos largos de empleo sin necesidad de tener que realizar costosos trabajos de limpieza y mantenimiento.
Un buen rendimiento de separación de los separadores de placas de impacto o rebotamiento lavables y que trabajan sin sufrir desgaste es de significativa importancia para el tiempo de duración de los elementos filtrantes montados a continuación y que suelen ser generalmente piezas de desgaste. En la Figura 8: que mostramos a continuación se pretende mostrar qué parámetros influyen concretamente en estos casos sobre el grado de separación de los separadores previos, tomando para ello como ejemplo un separador de placas perforadas.
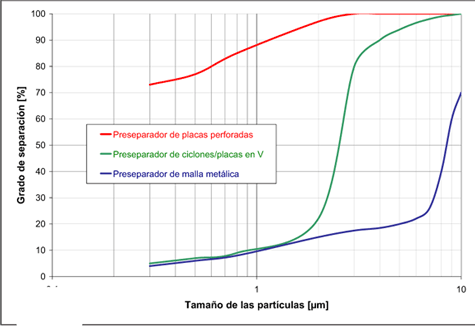
Presentación con ayuda de modelos:
- Figura 9: separador de placas perforadas: resultado positivo
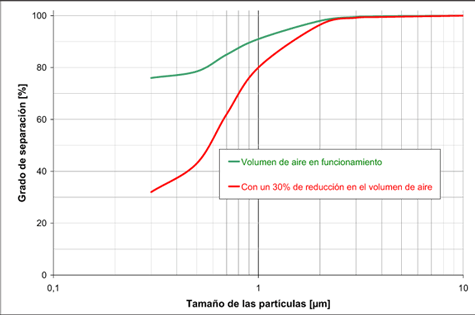
Comparativamente, Figura 10:
- Separador de tejido metálico
- Separador de inversión en V
- Separador de placas perforadas
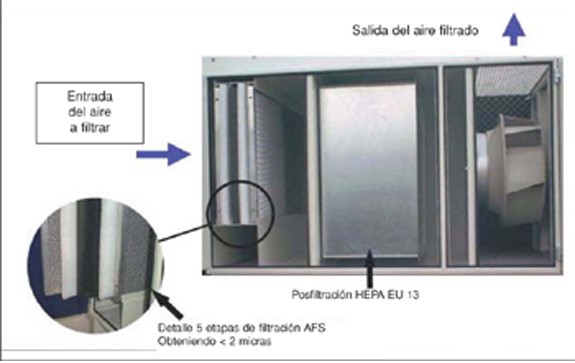
Además se da una peculiaridad del mundo de los separadores de placas de impacto o rebotamiento que he observado mientras preparaba esta conferencia, Figura 11: y que me agradaría presentarles como lo que podríamos denominar un separador ciclónico “a la derecha antes que a la izquierda“.
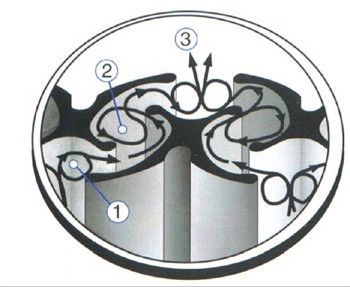
Filtración ulterior:
Tal y como ya hemos mencionado suelen instalarse preferentemente como filtros posteriores, con el fin de conseguir un aire de salida realmente limpio, filtros para sustancias en suspensión del tipo EU 13. Con estos filtros altamente eficientes para salas limpias o asépticas, con una capacidad de separación del 99,99 por ciento referida a unas dimensiones de partículas de 0,3-0,5 µm, puede garantizarse prácticamente el filtrado de todas las partículas de la neblina de emulsión o de aceite, de humos o de polvo finísimo de rectificado, de manera continua y con una elevada potencia de filtración permanente. Se aplica tambiény especialmente a la gama de partículas inhalables o respirables de menos de 0,5 µm. Con ello se garantizan de manera permanente y durante todo el tiempo de empleo de los filtros unos valores que quedan claramente por debajo del valor de tolerancia establecido oficialmente para la limpieza del aire de salida de un máximo de 2 mg de partículas residuales / m3 de aire en circulación. No hay posibilidad de realizar un "soplado“ de los filtros para partículas en suspensión en el aire.
El inconveniente que presentan estos filtros para sustancias en suspensión consiste en que las sustancias ajenas al aire que se separan del mismo (especialmente productos aceitosos) se depositan de tal forma en el tejido filtrante que no se pueden eliminar mediante lavado, reduciendo por tanto el tiempo o duración de vida de los filtros. A causa de ello es necesario sustituir los filtros para partículas en suspensión usados por otros nuevos con el fin de proceder a su eliminación.
Alternativas a la filtración ulterior:
Como alternativa a la filtración ulterior por medio de filtros para partículas en suspensión puede utilizarse, especialmente en procesos de mecanizado con emulsión y poca formación de neblina, un separador posterior que trabaje sin desgaste alguno y que consista en un separador de tejido metálico o de tejido combinado hecho de tejido metálico con tejido de poliéster integrado. En estos separadores posteriores se realiza una limpieza ulterior adicional mediante adhesión y condensación de las partículas líquidas.
En la siguiente Figura 12 (aparato de AFS): la realización de un sistema combinado de placas de impacto y filtros en un aparato utilizado en la práctica.
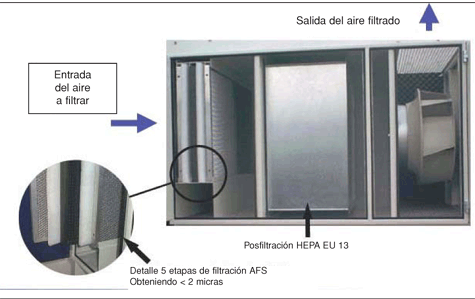
Empleo en la práctica de sistemas de limpieza del aire
Aparatos individuales:
Con los separadores individuales se puede realizar la aspiración de una o dos máquinas de mecanizado adyacentes. El aire de salida depurado se proyecta nuevamente en la nave de producción. Deberán cumplirse, por tanto, las disposiciones legales relativas a la recirculación de aire (máx. 2mg/m3).
Las siguientes Figuras (13-16) muestran el montaje adosado o el montaje en los centros de mecanizado de los separadores:
- Figura 13: AFS 600 Stama
- Figura 14: AFS 1100 DMG
- Figura 15: AFS 1100 Pfauter
- Figura 16: AFS 4000 B & W
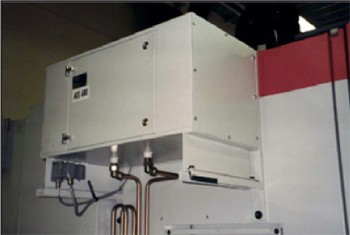

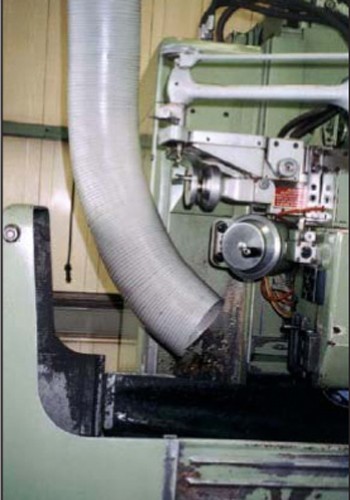
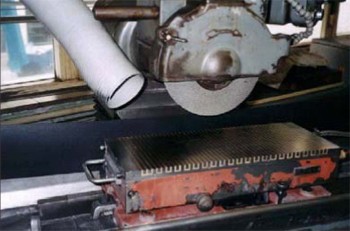
Instalaciones de aspiración de grupos de máquinas:
Si hubiera de aspirarse el aire de salida de varias máquinas de mecanizado que no se encuentren excesivamente alejadas entre sí, podrá hacerse con una instalación de aspiración por grupos. Pueden ver la estructura o configuración de una instalación de aspiración de grupos de este tipo.
También cuando se trata de grandes instalaciones de aspiración centrales es similar la estructura que presentan a la de una instalación de aspiración de grupos; Figura. 19:
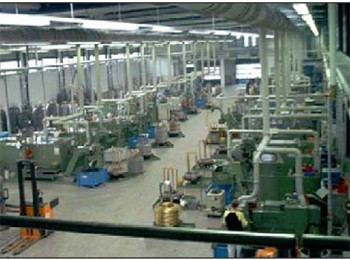
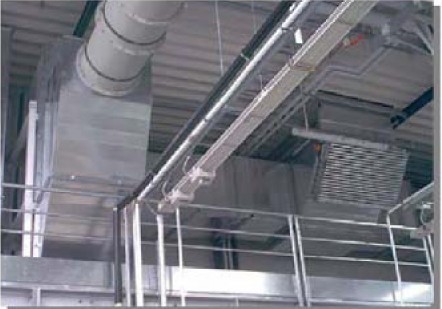
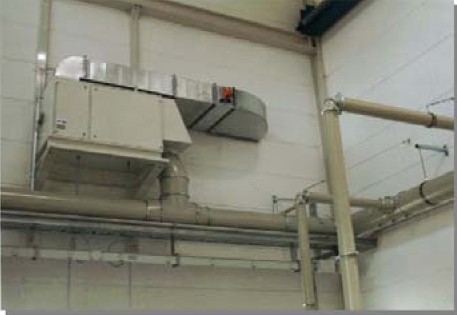
Sistema de recirculación de aire (en los meses de invierno):
Para evitar pérdidas de calor durante los meses de invierno a través del aire caliente expulsado al exterior cuando se trabaja con sistemas de expulsión directa del aire a la atmósfera, puede proyectarse de nuevo a la nave de producción el aire purificado desde los aparatos AFS, es decir, el aire se mantiene dentro de los locales. Gracias a esta recirculación del aire se puede prescindir del calentamiento, necesario en los demás casos, de aire frío del exterior para sustituir al aire expulsado al exterior, necesitándose para ello 1,0 l de fuel-oil aproximadamente por cada 1.000 m3 de aire frío exterior. Los valores límite máximos admisibles establecidos para el funcionamiento con aire recirculado se mantienen plenamente e incluso se consiguen unos valores claramente inferiores.
Funcionamiento con expulsión de aire al exterior (en los meses de verano):
En los meses de verano se puede trabajar con la modalidad de funcionamiento con expulsión de aire al exterior a través de un canal de aire de salida que conduce directamente al exterior (y que se puede montar también en un momento posterior). El aire caliente, purificado, se expulsa al exterior, permitiendo al mismo tiempo la entrada de aire fresco del exterior a través de puertas, portones o ventanas abiertas con el fin de mantener una climatización natural de la nave de producción sin necesidad de ventiladores adicionales. En correlación con el ahorro de energía durante el invierno se podrá expulsar comparativamente al exterior una cantidad de calor de aproximadamente 1,0 l de fuel-oil cada 1.000 m3 de aire de salida.
Además se podrá sustituir o cambiar el filtro ulterior para salas limpias instalado cuando se trabaja con el sistema de recirculación del aire (filtro para partículas en suspensión de tipo EU 13) por un separador posterior de tejido metálico que trabaje sin desgaste alguno, y su posible limpieza en una lavadora con un agente alcalino.
Resumen
Tal y como hemos mostrado en la exposición anterior, no existe “el“ separador óptimo para los numerosos casos individuales específicos que se plantean en la práctica con los más diversos lubricantes.
El separador mecánico combinado con filtro desarrollado por la empresa AFS se aproxima sin embargo bastante a ello. Gracias a la combinación con efectos complementarios de separadores de placas de impacto o rebotamiento con vellones filtrantes adicionales integrados y con filtros para salas limpias o asépticas montados a continuación ouede garantizarse, incluso cuando ha de trabajarse durante largos periodos de tiempo con distintos casos de aplicación, tanto un elevado rendimiento de limpieza constante como unos largos periodos de duración de vida de los medios filtrantes: Esta es también la razón por la que la compañia AFS Air Filter Systeme GmbH se dedica a la fabricación de este tipo de aparatos de limpieza del aire, distribuyéndolos desde hace años, con pleno éxito en el mercado junto con la casa Bantleon entre otros.