Entrevista a José Ramón Ramírez, director técnico-comercial de Dyfa
Dedicada al diseño y la fabricación de utillajes para sectores de altos requerimientos tecnológicos, como el aeronáutico, el naval y la automoción, la empresa Dyfa puede presumir de haber participado en proyectos de gran envergadura para firmas del sector aeronáutico como Airbus, Aernnova y Aciturri. Aviones y helicópteros de primeras marcas cuentan en sus estructuras con piezas de la empresa vizcaína, como los paneles exteriores Shell del estabilizador vertical del modelo A350 XWB, todo un reto técnico que hacen de esta empresa un referente en el ámbito de la subcontratación en la aeronáutica.
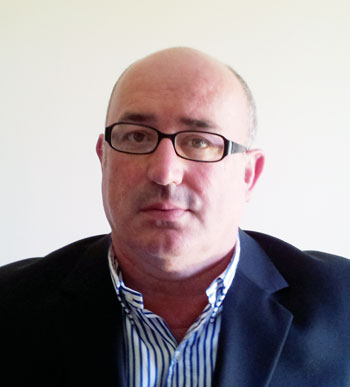
¿Qué tipo de piezas fabrican para el sector aeronáutico?
Desde útiles de moldeo en acero, níquel e invar, útiles de estirado en acero y aluminio, y útiles de recanteado y taladrado en acero, aluminio y materiales compuestos (manual y CNC), hasta cáscaras de fresado químico, cáscaras de fibra, útiles prensa de goma y aceite, útiles conformado y soldadura para tubería, moldes de termoconformado, calibres de control, modelos master y prototipos, útiles de montaje y ensamblaje final, así como mecanizado, recanteado y taladrado de piezas tanto metálicas como compuestas por CNC.
¿Qué destacaría?
Este último: el mecanizado, recanteado y taladrado piezas metálicas y compuestas por CNC. Además, somos la única empresa homologada en España por Airbus para el diseño y la fabricación de utillaje de moldeo en níquel.
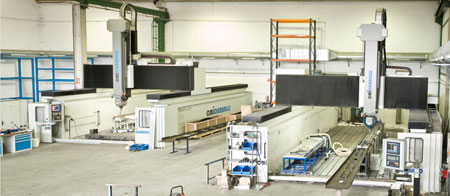
Trabajar para el sector aeronáutico y la automoción requiere de altos estándares de calidad, ¿cómo lo certifican?
Mediante certificaciones internacionales. Dyfa está certificada en diseño y fabricación de utillajes Airbus para el mecanizado, recanteado y taladrado piezas materiales compuestos. Además, contamos con las certificaciones ISO9001 e ISO9100.
¿En qué proyectos han participado y con qué firmas aeronáuticas?
Los proyectos de colaboración que Dyfa ha desarrollado en el sector aeronáutico han sido diversos y con firmas como Airbus, Aernnova y Aciturri para el suministro de elementos del estabilizador horizontal y vertical de los A350 XWB, A320, A330, del nuevo modelo de Bombardier, del helicóptero NH 90, Embraer 145, 170-190, KV-390 y Falcon.
¿Qué exigen las grandes firmas a las empresas que subcontratan? ¿Es complejo formar parte de estos proyectos?
No es sencillo. Fundamentalmente, se exige a las empresas una alta cualificación y que, además, cuenten con medios productivos y con amplios conocimientos técnicos.
Si tuviese que aconsejar a una empresa de mecanizado que quisiera entrar en este mercado, le diría que la penetración en el sector aeronáutico es complicada. Requiere fuertes inversiones tanto en el ámbito de la ingeniería como en el de fabricación, por lo tanto, los plazos son largos.
¿Cuál es la pieza más compleja que han realizado y qué medios necesitaron para su fabricación?
Sin duda, una de las piezas que han supuesto un reto tecnológico han sido los paneles exteriores Shell del estabilizador vertical del modelo A350 XWB.
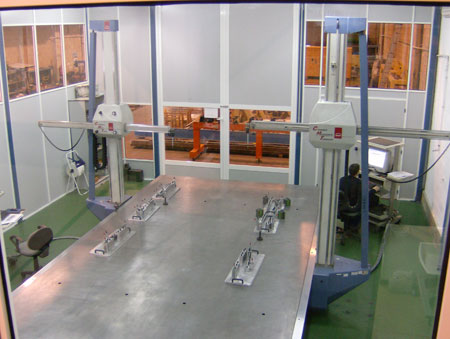
También fabrican componentes y pieza primaria para sectores como el aeronáutico, automoción y naval. ¿Qué parte suponen estos mercados en su facturación?
El mecanizado de piezas de serie para el sector aeronáutico es el área más representativa. Ésta supone un 55% de la facturación total de Dyfa. Asimismo, el diseño y fabricación de utillajes para el sector aeronáutico representa un 30% de la facturación, mientras que el diseño y fabricación en el sector automoción es el 15%. Por otro lado, y a diferencia de otras empresas de actividad similar, nosotros no exportamos directamente .
¿Qué proyectos destacaría para los próximos tres años?
Son varios los proyectos que tenemos de aquí a tres años, como son los relacionados con los modelos A350 XWB, A330, NH90, Embraer 170-190 y KC390.
¿Cuáles son los principales retos en materia de diseño y fabricación de utillajes para el sector aeronáutico?
Creemos que uno de los principales retos tecnológicos en el diseño y fabricación de utillajes en este segmento es la mejora de herramientas para el mecanizado de materiales compuestos.
¿El sector aeronáutico español está en un buen momento? ¿Aún queda margen de crecimiento?
Dyfa entiende que la ejecución de nuevas inversiones dependerá de la obtención de pedidos aeronáuticos actualmente en negociación y cuya captación conllevará el incremento de la capacidad de taller ante el alto nivel de ocupación de su capacidad industrial.
Y ya para concluir, ¿qué tipo de productos y servicios ofrecen para el sector de la automoción?
Para esta industria que, como comentaba, representa el 15% de nuestra facturación, diseñamos y fabricamos maquetas de control de piezas y modelos prototipo.
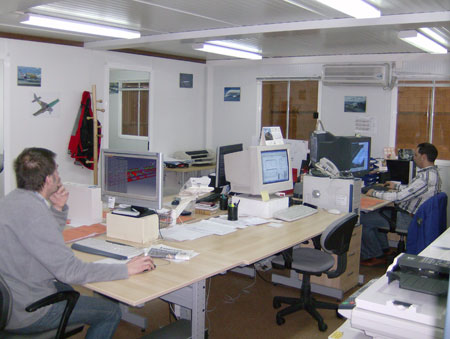
El equipo humano y tecnológico
Dyfa cuenta con una plantilla de 34 personas dedicadas al diseño y fabricación de utillaje aeronáutico y mecanizado de piezas aeronáuticas en materiales compuestos. Para ello, dispone de una fresadora Jobs Gantry 5 ejes (7.000x3.200x2.000) con CNC Fidia de 16.000 rpm, un KXP Gantry DMC100 5 ejes (10.000x4.000x1.500) con CNC Fagor de 20.000 rpm y un KXP Gantry FGB510 de 5 ejes (6.000x3.500x1.700) con CNC Fagor de 20.000 rpm.
En el ámbito del control, cuenta con un Laser Tracker Faro con software Metrologic y una máquina tridimensional de 2 brazos (6.000x3.000x1.800) y software Metrologic. En cuanto al CAD/CAM, la empresa hace uso de dos unidades Catia V.5, una unidad Catia V.4 y una Tebis.