Tecnologías avanzadas para operación y mantenimiento en plantas de cogeneración
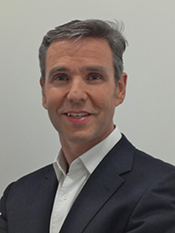
Por: Fernando Cámara Centeno, responsable de desarrollo de negocio en Energías, Oil&Gas e Industria, en Grupo Álava Ingenieros.
El presente artículo, no pretende ser un alegato en defensa de unas u otras maneras de generar electricidad. En mi opinión, con las necesidades de consumo que tenemos en la actualidad, debemos de tener presentes absolutamente todas las formas disponibles para generar energía. También creo que se deberán de analizar las repercusiones del uso de unas y otras fuentes, mirando el legado que dejamos a las generaciones venideras, pero considerando las necesidades actuales en materia de creación y mantenimiento del empleo local, que son al fin y a la postre, los que podrán garantizar un consumo de dicha energía en el futuro.
Que se diga que los tiempos han cambiado, es una frase recurrente que resume la evolución humana, y lo que también es cierto, la forma de consumir no es igual ahora que hace 30 años. La crisis económica actual, ha repercutido en la bajada del consumo y esto se traslada a todos los ámbitos, especialmente el industrial que es el de mayor demanda de energía. Por otro lado, unos precios bajos del petróleo, también obliga a las compañías dependientes de éste, a realizar reajustes en materias de inversión, especialmente en grandes proyectos de mejora en sus infraestructuras. Estos reajustes también repercuten en el consumo de productos manufacturados de materiales, lo que a su vez, además del aumento de la competencia, provoca un reajuste en las inversiones de estas compañías para contener el gasto. La forma de evolución tiene que pasar inevitablemente por ajustar los procesos productivos a las demandas cada vez más puntuales de los clientes: más flexibles, eficientes y competitivos. Además, se deberá de tener en cuenta los nuevos criterios en materia legislativa relativa a políticas medioambientales, de eficiencia energética y de calidad, lo que obligará a modernizar inevitablemente las instalaciones.
La cogeneración es la generación en un mismo proceso de electricidad y calor útil para producción. Las plantas de cogeneración, están instaladas físicamente en la propia fábrica o en sus aledaños, lo que hace que se clasifique también como una fuente de energía distribuida. El empleo, además de la generación de electricidad para consumo propio, aplica a sectores como el químico, papelero, alimentación o automoción donde utilizan mucho vapor, y también el sector de la cerámica y minería, para procesos de secado. Según los datos que publica Acogen (Asociación Española de Cogeneración) en su Balance 2015, la cogeneración produjo el 10% de la electricidad a nivel nacional, está presente en más de 600 instalaciones y en total consumieron el 22% de gas natural en España.
El objetivo que se pretende con este escrito, es dar una pincelada sobre diferentes técnicas y tecnologías que van a resultar útiles en el proceso de mantenimiento y modernización de las actuales plantas, así como recomendaciones para los nuevos proyectos.
1.- Plan de revisiones periódicas: Mantenimiento predictivo frente al preventivo
Desde hace muchos años, en el sector industrial, se aplican políticas de implantación de planes de mantenimiento predictivo con el objetivo de optimizar los costes destinados a las sustituciones periódicas rutinarias de elementos, tratando de evitar o reducir los costes ocasionados por averías no previstas.
Uno de los puntos clave para su implantación, es la concienciación por parte de la dirección para entender estas políticas como una mejora en sus procesos, tanto productivos como de mantenimiento. Otro factor importante, sería la adecuación de los recursos a las rutinas de inspección. Aunque pueda resultar evidente, para que un plan de predictivo sea fiable, lo primero que se debe tener son datos. Podrá haber situaciones que debidas a la velocidad de rotación, al número de maniobras, la potencia, el caudal… la evolución al fallo pueda ser muy rápida, y en este caso se requiera de sistemas de monitorización permanente; o por el contrario otras situaciones o elementos, cuya aparición del fallo conceda mucho más tiempo para reaccionar frente a la avería, y por lo tanto se pueda realizar inspecciones una vez al mes, o a los tres o seis meses, dependiendo de su uso. La determinación de esos tiempos, junto con las técnicas fiables de detección, serán las que marcarán un correcto plan.
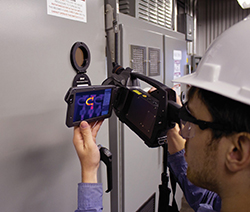
2.- Instrumentación específica
En toda cogeneración, como en cualquier planta industrial, se deberá disponer de sistemas de control para labores de operación, que vendrán gobernados por sensores repartidos en diferentes secciones la planta.
-Medida de temperatura
Hoy en día la medida de temperatura sin contacto mediante cámaras (termografía), podría no considerarse como una tecnología singular, dada la utilización cada vez mayor por parte del personal de mantenimiento de cualquier planta industrial.
Es una herramienta imprescindible para mantener, modernizar y operar cualquier planta de cogeneración. Resultará igualmente de una gran utilidad para el estudio de distribuciones de temperatura, y con la eficiencia energética. Válido también para la verificación de niveles en algunos tanques o depósitos, e incluso como una herramienta complementaria a las vibraciones y análisis de aceites o en la detección de averías en equipos rotativos (problemas de desalineación, detección de excentricidades rotor-estátor, calentamiento en conexiones de excitatriz…).
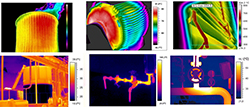
Pero si hay un uso por el que la termografía es reconocida, es en redes de distribución de electricidad y mantenimiento eléctrico en general. Cuando se producen deterioro en los conductores o fallos en las uniones o bornas, equivale a una disminución de la superficie de contacto y/o reducción de sección. Esto supone un aumento en la resistencia eléctrica, que al paso de la corriente y por efecto Joule, provocará un aumento de temperatura. Sin embargo, ¿qué sucede si se quiere controlar de manera permanente la temperatura sin contacto de una zona crítica? Existen soluciones de termografía online, dotadas de las máximas capacidades para la integración, con amplios rangos de medida y con diferentes grados de protección dependiendo de la zona de instalación.
-Medida de vibraciones
La toma de medida de vibraciones en equipos rotativos, se viene utilizando también en la industria desde hace muchos años. Cualquier problema mecánico va a originar una vibración y por ese motivo, si se disponen de datos fiables de sus niveles, se podrá hacer un diagnóstico de la maquinaría y con ello poder llegar a determinar su disponibilidad.
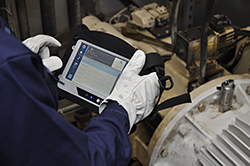
El análisis de vibraciones, además de su labor predictiva y de investigación de las causa raíz de fallos, es una herramienta muy utilizada en aplicaciones de mejora del diseño de instalaciones. Ejemplos de esto último, se pueden encontrar cuando se han tenido que modificar en una planta la disposición de equipos, canalizaciones o incluso velocidades de giro de motores, soplantes o bombas, y debido a las condiciones particulares de la instalación, dichos equipos han entrado en resonancia. Gracias a las lecturas de vibración, y a la determinación de las frecuencias naturales del entorno, se han podido averiguar las fuentes, y tras el correspondiente estudio, poner medidas correctoras para evitar averías futuras.
Para maquinaria rotativa, tipo bombas auxiliares y soplantes, se puede encontrar instrumentación cuyo elemento detector está basado por lo general en sondas piezoeléctricas (acelerómetros), y cuya señal se llevará a un equipo portátil (colector/analizador de datos para medidas periódicas) que procesará la señal, generalmente aplicando la transformada rápida de Fourier, y volcará los datos a PC para su almacenamiento y/o elaboración de informe. La señal del sensor, dependiendo de los casos, también puede llevarse a un equipo específico para visualización y registro de valores de forma permanente, o bien convertirse in-situ a señal 4-20mA (transmisor) para integrarlo en el sistema de control distribuido (DCS) de la planta. Unos datos predictivos fiables en este tipo de máquinas, deberán venir de la combinación de diferentes sondas como son de presión, vibración y temperatura, y un sistema que sea capaz de correlacionar todas de manera simultánea y con capacidad de diagnóstico.
-Medida de ultrasonidos
Los ultrasonidos son ondas mecánicas, cuyo rango de frecuencia está por encima del rango audible del ser humano (>20kHz). Al igual que los infrarrojos, son de naturaleza no ionizante, es decir, no poseen la suficiente energía para arrancar uno o más átomos, modificando la materia. Entre sus características más reseñables, se podría citar la gran direccionalidad (permitiendo rastrear una onda hasta encontrar el foco generador) y la atenuación producida por los cambios de medio (fronteras entre diferentes tipos de materiales).
Entre las principales aplicaciones de estas técnicas, para uso industrial, está la medición de espesores. Esta técnica utiliza el efecto eco y las propiedades de propagación de los diferentes materiales, de tal forma, que hay un emisor que lanza un impulso ultrasónico en el material y hay un receptor que recibe la señal del eco con el retardo proporcional al material. También basado en este principio, un sistema de georadar se utiliza para la localización de tuberías y servicios enterrados. Dicha aplicación utiliza antenas a modo de generador y receptor de alta frecuencia (MHz), y puede resultar de una gran utilidad a la hora de abordar proyectos de modificaciones de planta, especialmente en aquellos casos que no se tiene la certeza de por dónde están instalados los servicios (canalizaciones de agua, electricidad, gas…).
Aprovechando los principios de la direccionalidad, los ultrasonidos se utilizan para la detección de fugas de fluidos, mayormente aire comprimido y vapor. Cuando un fluido a presión atraviesa un orificio estrecho (poro), se produce un fenómeno de turbulencia que va acompañado de una emisión acústica ultrasónica. La intensidad dependerá de la viscosidad del fluido, del tamaño del orificio y de la presión diferencial. Hay estudios que demuestran ahorros cuantiosos, vigilando y reparando las fugas en las conducciones de producción y distribución de aire comprimido. También se aprovechan los fenómenos ultrasónicos, para la inspección válvulas, purgadores de vapor y en última medida, para detectar fases iniciales de fallos en rodamientos y cajas de engranajes debidos a problemas de lubricación y/o deterioro.
-Análisis de aceites
La lubricación es un fenómeno complejo resultante de la combinación de varios principios físicos y químicos, que busca entre otras funciones, la disminución del rozamiento en superficies en movimiento relativo, evacuar calor producido por el rozamiento, proteger las superficies frente a rayaduras o evitar formación de óxido.
Los objetivos que se buscan con los análisis de aceite son, por un lado el control de la degradación de las propiedades físico-químicas como la viscosidad o contenido en agua, con el objeto de optimizar rellenos o aditivación. También interesa el conocer el estado de la contaminación, para predecir algún tipo de avería en la instalación, y por último el detectar elementos metálicos procedentes del desgaste de los elementos de fricción de las máquinas y sus accionamientos.
-Calibración de variables de procesos
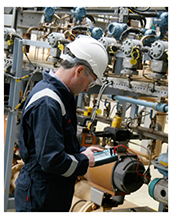
Atendiendo a una definición académica, podremos definir la calibración como un conjunto de operaciones que tienen por objeto establecer la relación que hay, en condiciones especificadas, entre los valores indicados por un instrumento de medida y los valores conocidos correspondientes al mensurando (magnitud particular sometida a medición).
En el caso de la cogeneración, asegurar por ejemplo que la turbina y el generador estén operando de la manera más eficiente, puede ser la clave para hacer la planta sea realmente competitiva. Reducir las incertidumbres de medida en la instrumentación instalada, puede llegar a mejorar la generación de energía a la salida hasta en un 2%.
-Sondas para la detección de humedad en el gas de entrada y detección de formación de H2 en aceites de transformador
Si se tiene en cuenta que en la actualidad el 22% del consumo de gas natural en España va destinado al sector de la cogeneración, éste representa un volumen muy importante para las compañías gasistas. Dependiendo del mantenimiento y conservación de algunas instalaciones, es posible que el gas suministrado no llegue a las plantas en las mejores condiciones; la combinación entre humedad y gas natural, da como resultado problemas (corrosión en circuitos y canalizaciones; a bajas temperaturas, o en altas temperaturas con cambios rápidos de presión puede generar también la formación de hidratos de metano y por supuesto, puede provocar una variación en las propiedades caloríficas del gas).
En la actualidad existen sensores para monitorizar en tiempo real la temperatura, humedad y la formación H2, libres de membranas, bombas y elementos sensibles de mantenimiento, con el objetivo de aumentar la fiabilidad del transformador y adaptar, si se desea, los planes de mantenimiento basados en tomas de muestra de aceite rutinario, a situaciones excepcionales o de riesgo de fallo potencial.
-Inspecciones rutinarias para visualización de gases
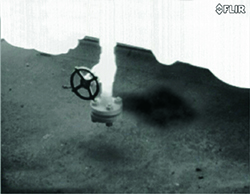
Los gases, en el momento que se escapan a la atmósfera, absorben radiación en una o varias longitudes de onda dependiendo del tipo que sea. En general, los gases formados por múltiples átomos (moléculas diatómicas heteronucleares o más), pueden absorber (y emitir) calor de manera más eficiente que los de una molécula simple. Esto quiere decir que su grado de “transparencia” podrá variar de unos a otros. Así, se pueden encontrar gases como el vapor de agua, que absorbe radiación en la zona del espectro de luz visible (0,4 y 0,75 μm), y por lo tanto somos capaces de verlos, y otros por el contrario, como sucede con el metano, que absorben radiación en otras longitudes de onda, siendo totalmente invisibles al ojo humano.
A diferencia de una cámara termográfica convencional, que trabaja en longitudes de onda donde sólo interesa medir temperatura superficial (normalmente de 8 a 14 μm), estas cámaras trabajan en zonas donde, además de la temperatura, son capaces de visualizar los gases.
Criterios de seguridad, reducción de costes debidos a paradas no programadas o fallos en el suministro, y criterios medioambientales por emisiones fugitivas (como es el caso de la nueva normativa de la EPA del 12/05/16 regulando nuevas emisiones de metano), van a ser las causas por las que se deberá de extender el uso de estas nuevas cámaras.
3.- Conclusiones
Si a los cambios en materia de energía y consumo como se comentó al inicio, añadimos que el sector de la cogeneración es un “sector maduro”, con más de 35 años desde su implantación en el tejido industrial español, y si a esto sumamos también un aumento considerable de nuevas instalaciones, especialmente fuera de nuestras fronteras como pronostican el GTM Research en Estados Unidos en su último informe 2016-2026, podemos concluir, que tenemos un gran reto, y una excelente oportunidad de crecimiento y mejora por delante.