Geonovatek consolida el terreno de una escuela en Jaén
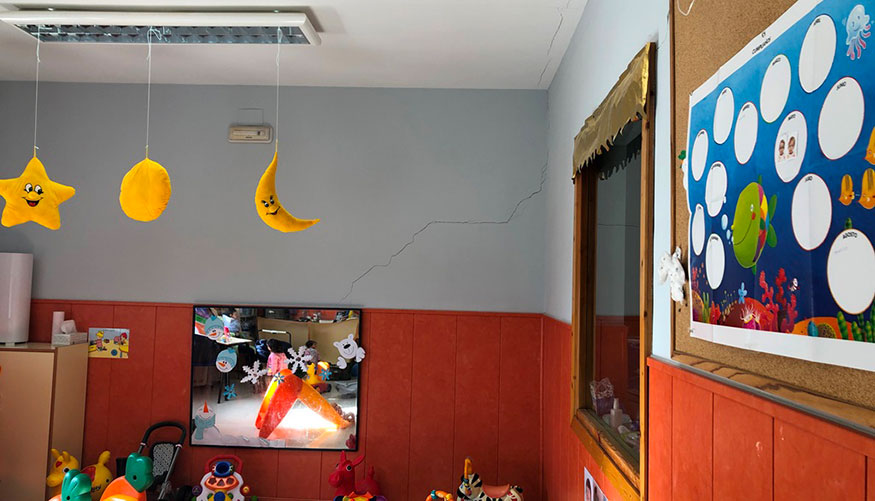
Es lo que ha ocurrido en un caso de éxito que llevó a cabo GeoNovatek, en Jaén, donde el edificio de una escuela pública sufría numerosas grietas, que afectaban a la vida diaria de la escuela. Se trata de un edificio escolar aislado, construido en 2005, que consta de una superficie de 403 metros cuadrados distribuidos en una sola planta sobre rasante. La estructura se resolvió mediante muros de carga de fábrica de ladrillos, y forjados de viguetas unidireccionales. Asimismo, el edificio cuenta con un forjado sanitario visible.
Según los datos obtenidos, la cimentación del edificio se diseñó con zapatas corridas de hormigón armado de 1,10 metros de canto. Además, cabe resaltar que la cimentación del edificio apoya a distintas cotas, adaptándose de esta forma a la pendiente del terreno.
La patología de este caso se debió al terreno expansivo que hay bajo la escuela, lo que provoca que, en los meses de invierno, con época de lluvias, el terreno se expanda, mientras que durante los meses de veranos se contrae, provocando la aparición de las grietas y su agravamiento debido a este efecto. Tras el estudio, gracias a la instalación de varios fisurómetros, se confirmó un aumento del ancho de las grietas, lo que constató el asentamiento del terreno y que debía llevarse a cabo un recalce de la cimentación.
Consolidación y realce
La intervención de consolidación y recalce, ejecutada por GeoNovatek, consistió en el uso de la resina expansiva HDR300 y los micropilotes MP60 de acero con adherencia mejorada, hincados a presión.
La primera fase de los trabajos consiste en la realización de una serie de perforaciones de 26 mm de diámetro que atraviesan verticalmente la cimentación y penetran en el terreno.
Por cada una de dichas perforaciones se introducen tubos, a través de los cuales se realiza la inyección de la resina expansiva HDR300 en el terreno bajo el plano de apoyo de la cimentación. Durante la fase de inyección, la resina ultracompacta HDR300 se encuentra en estado líquido, lo que permite que penetre en el terreno, empujada por la presión de las bombas.
Posteriormente, y en pocos segundos, la reacción química produce una expansión de la resina haciendo aumentar su volumen entre nueve y doce veces, rellenando los intersticios, comprimiendo y estabilizando el subsuelo.
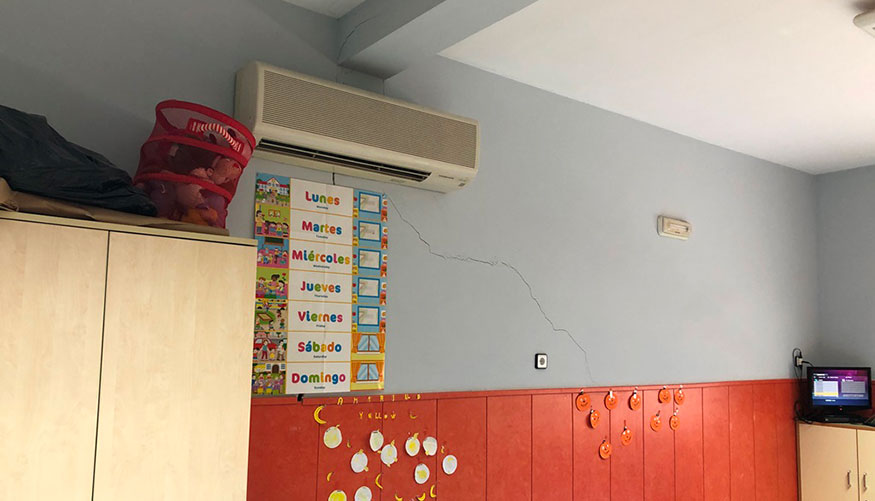
La operación de estabilización de la estructura se realiza gracias a la hinca a presión de los micropilotes MP60 de acero con adherencia mejorada.
La puesta en obra de los micropilotes se produce de la siguiente manera:
- Realización de una perforación de 65 mm de diámetro que atraviesa verticalmente la zapata.
- Realización de dos anclajes a los lados de la perforación anterior, fijando en la cimentación dos varillas roscadas de acero de diámetro 20 mm.
- Puesta en obra de los elementos que componen el micropilote de un metro de longitud a través de la perforación central. Dichos elementos serán hincados en profundidad dentro del terreno, gracias a la presión ejercida por un pistón hidráulico y a los dos anclajes laterales que actúan como contraste. El primer elemento fijado en el terreno puede estar dotado de una puntaza cónica para facilitar la introducción del micropilote en aquellos estratos más compactos. La conexión entre los elementos se dispone mediante el empleo de una rosca especial maciza de acero de alta resistencia.
- Durante la fase de hinca del micropilote se produce un efecto de compactación radial del terreno respecto de la barra de penetración, causada por la compresión del terreno que ocupaba el volumen del pilote. El pistón hidráulico está dotado de un manómetro, que permite leer la presión para el hincado de los micropilotes de acero en el terreno, gracias a lo cual queda comprobada la capacidad de los micropilotes uno a uno.
- Cuando el micropilote encuentra una formación que le permita resistir la fuerza del hincado, previamente especificada en proyecto, que es de un máximo de 271 kilonewton (kn), se desengancha el pistón, dándose por finalizada la fase de hinca.
- Fijación del micropilote en el interior de la cimentación por medio de lechada de hormigón de lata resistencia compensada para anclar los módulos al elemento de cimentación.
- El proceso de roscado externo del micropilote le otorga una mayor rugosidad y adherencia, aumentando la superficie de fricción en un 46%. El corrugado se realiza mediante un moldeado plástico a partir de cuerpos giratorios sin que se produzcan virutas ni rebabas y sin eliminación del material. De este modo se obtiene una mejora en las propiedades (resistencia a tracción, a torsión y a fatiga).