Un congreso impulsa las respuestas a las exigencias del creciente sector del WPC
Fabricar perfiles de WPC de forma rentable
21 de noviembre de 2011
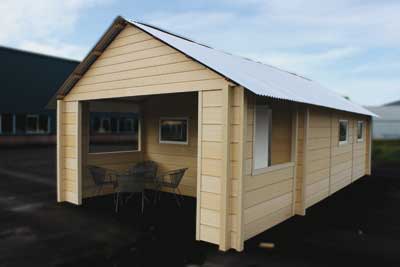
El tema principal en el campo del WPC es hoy en día la reducción de los gastos de fabricación, especialmente de los de material que, con aproximadamente dos tercios de los costes totales de fabricación, constituyen el principal coste del total del producto. Por ese motivo, los fabricantes buscan soluciones, como el uso de materiales reciclados o de dosificadores más precisos, la ampliación de la ventana de procesado, y el control exhaustivo y la valoración de alternativas para la minimización de los índices de rechazos.
Hacia la coextrusión
Estos desarrollos han llevado a una fuerte tendencia hacia la coextrusión de WPC. Se pueden reducir los costes entre un 20 y un 25% mediante ahorros en las recetas del material del núcleo, es decir, el material no visible (por ejemplo, mediante el uso de material reciclado). Las formulaciones de coextrusión utilizadas en la capa exterior tienen habitualmente un mayor contenido de estabilizantes y pigmentos, y se desarrollan y producen a la medida de las respectivas exigencias de los mercados a los que se dirigen. En el núcleo, invisible, se recurre a formulaciones más baratas.
El mercado del WPC presenta crecimientos anuales de entre el 10 y el 40%. Tableros para terrazas y suelos son, más que nunca, el segmento de productos más importante, con una cuota de mercado del 75%. Para poder continuar en el futuro con estos índices de crecimiento, el sector busca constantemente nuevas aplicaciones que presenten un elevado volumen de producción, con el fin de seguir ampliando este segmento de mercado con un desarrollo tan dinámico.
battenfeld-cincinnati ha hecho suyos todos estos desarrollos y ha presentad0, junto con su partner Beologic, una línea de coextrusión de alto rendimiento para la fabricación de tableros de WPC para suelos, así como un sistema de módulos desarrollado por Delta-Wood para hacer casas completas.
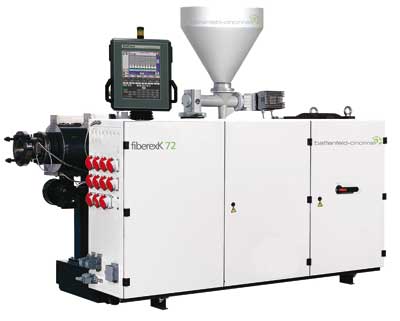
La línea de extrusión se compone de una extrusora principal fiberEX 92 y una fiberEX 38 con configuración ‘Space-Saber’ (ahorro de espacio), como coextrusora, que destaca por su construcción extremadamente compacta. Las hileras y el material para la producción de los tableros para suelos de 160 milímetros de anchura y 30 de grosor, con siete cámaras, los realiza Beologic, mientras que los equipos para procesos complementarios provienen de la probada serie baseBEX de battenfeld-cincinnati.
Casa completa
Trabajo conjunto
La colaboración entre battenfeld-cincinnati y Delta-Wood comenzó hace ya más de diez años. Ambas empresas desarrollaron conjuntamente un proceso para el procesado de composites WPC con fibra larga y disponen de patentes conjuntas de líneas especiales para la transformación de composites con fibra de madera (WFC).