Las enormes ventajas de ‘hipear’
La multinacional burgalesa Hiperbaric, fundada en 1999 y especializada en el diseño, construcción, instalación y mantenimiento de equipos de altísima presión, ha desarrollado una nueva tecnología, denominada Hot Isostatic Pressure (HIP) (prensado isostático en caliente) que permite mejorar las prestaciones de materiales con aplicaciones en la industria automovilística, aeroespacial, sanitaria y protésica, entre otras muchas posibilidades.
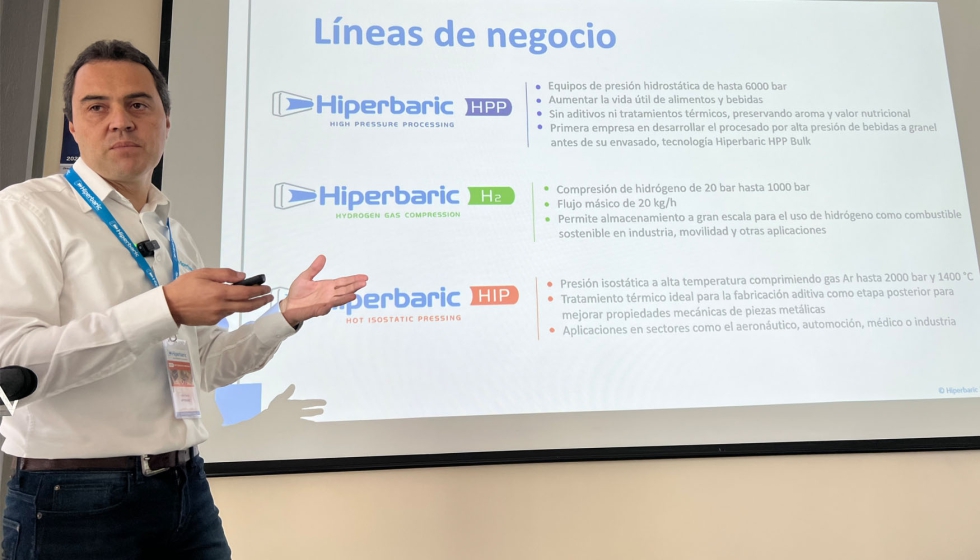
La tecnología HIP (de la que deriva el término ‘hipear’) aplica presiones de 2.000 bar de presión a 1.400 grados centígrados de temperatura, condiciones en las que desaparecen los microporos de componentes de alto rendimiento obtenidos mediante fabricación aditiva. Desde la compañía liderada por Andrés Hernando, consejero delegado y fundador de Hiperbaric, se apunta que HIP “impulsará el crecimiento mundial de la fabricación aditiva o impresión 3D”, un mercado con crecimientos anuales previstos del 17% hasta 2025.
La compañía burgalesa convocó recientemente a un grupo de periodistas para mostrarles el “primer Centro de Innovación del sur de Europa”, inaugurado en 2021 y ubicado en la factoría de Hiperbaric en las afueras de la capital burgalesa. Durante la visita pudimos comprobar el resultado logrado tras ‘hipear’ piezas de diferentes materiales y aplicaciones que, después de ser sometidas a estas condiciones de presión y temperatura, mejoran sus propiedades.
El director de Materiales y Fabricación Aditiva del Centro de Estudios e Investigaciones Técnicas, Íñigo Iturriza, quien realizó una breve exposición ante los visitantes a las instalaciones de Hiperbaric, afirmó que “HIP tiene un enorme potencial como tecnología de fabricación avanzada”. Entre otros logros, ‘hipear’ piezas de distintos materiales permite obtener uniones por difusión.
Por su parte, el HIP Project Manager de Hiperbaric, Rubén García, explicó en una brillante y didáctica exposición que “aplicando HIP a las piezas metálicas fabricadas mediante impresión 3D conseguimos eliminar cualquier posible defecto en piezas destinadas a sectores muy exigentes, como el espacial o el protésico”.
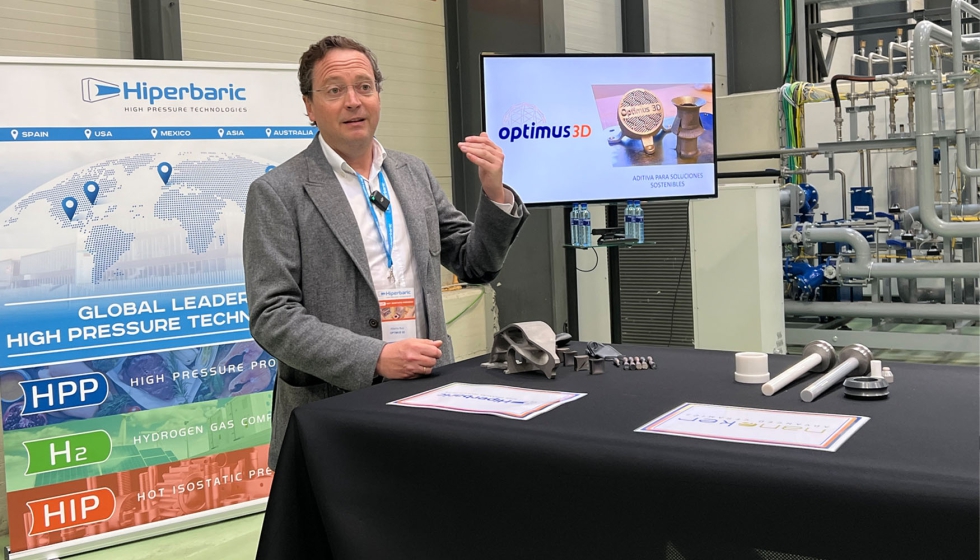
Múltiples ventajas
La compañía prevé comercializar sus primeros equipos HIP en 2023 y las previsiones auguran unas ventas anuales, en el periodo 2024-2027, de entre tres y cinco equipos HIP, lo que al final de esos cuatro años podría suponer una facturación anual superior a los 10 millones de euros.
Aplicar la tecnología HIP mejora las prestaciones de las piezas, “aumenta la resistencia a la fatiga y da lugar a piezas con microestructuras de grano fino con buenas propiedades mecánicas. Esta tecnología elimina la porosidad y otros defectos internos, da mayor consistencia a materiales de alto rendimiento, permite recuperar piezas defectuosas y hace posible diseños más ligeros”, explican desde Hiperbaric.
Además de las ventajas directas, la utilización de tecnología HIP propicia beneficios medioambientales, puesto que reduce el consumo de material y los costes asociados a los controles de calidad, ya que permite implementar el control estadístico por ensayos no destructivos, reduciendo así la cantidad de unidades que necesitan ser probadas antes de su fabricación definitiva.
La suma de la fabricación aditiva o la impresión 3D y la tecnología HIP permitirá el diseño y fabricación de piezas mucho más ligeras, una cualidad de particular interés para la industria aeronáutica, en el punto de mira por sus elevadas emisiones de CO2 a la atmósfera. En este sentido, la utilización de piezas más resistentes gracias a su ‘hipeado’ permite su aligeramiento sin comprometer la seguridad.
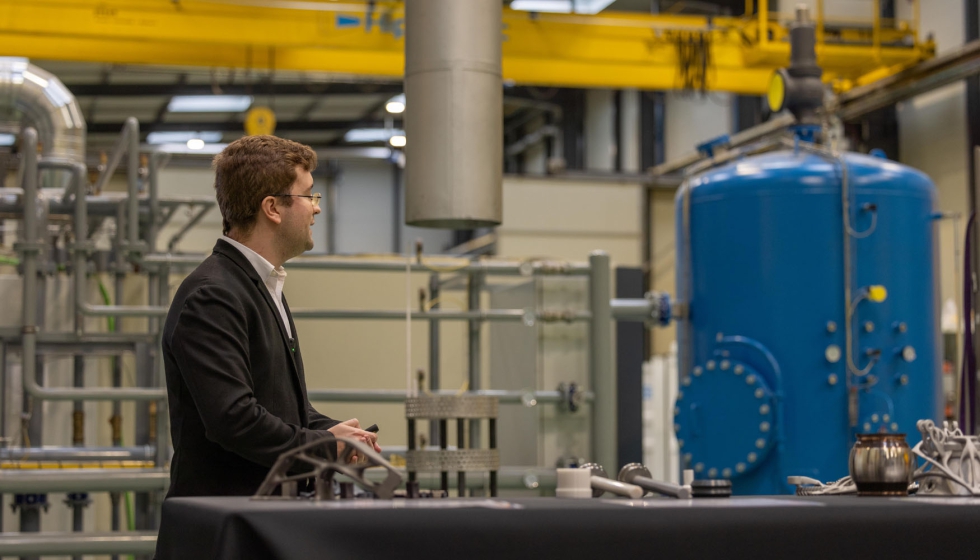
Variedad de aplicaciones
Representantes de varias empresas que utilizan la tecnología HIP para mejorar la calidad de las piezas que fabrican expusieron las posibilidades de esta tecnología, así como las mejoras que aporta a sus realizaciones. El primero en exponer los beneficios que aporta el ‘hipeado’ fue el cofundador de Optimus 3D, Alberto Ruiz, quien explicó que la empresa vitoriana, fundada en 2014, cuenta con equipos de fabricación para polímeros y metales.
Ruiz señaló que la fabricación aditiva está propiciando un cambio de paradigma en el diseño industrial. Si antes las piezas y componentes se diseñaban teniendo en cuenta el proceso de fabricación, ahora los diseños se supeditan a la función que van a realizar. En ocasiones, prosiguió, algunas aplicaciones exigen fabricar piezas que, en esa optimización “van tan al límite” que requieren recibir “tratamientos como el HIP para lograr que la pieza sea resistente”.
Hace dos años Optimus 3D creó una división dedicada a la salud (Optimus Health) que desarrolla productos personalizados a cada paciente. Se trata de realizaciones que sustituyen partes del cuerpo humano, tales como piezas dentales, partes de la mandíbula u óseas, entre otras muchas posibilidades.
Ortiz apuntó que la compañía ha desarrollado, junto a Cinfa y Orliman, un inmovilizador para atenuar los efectos de la artritis o el reuma del pulgar de la mano, una dolencia para la cual no hay una solución terapéutica, por lo que los pacientes deben intentar dejar de mover ese dedo, “pero los inmovilizadores son engorrosos y se terminan no usando durante el tiempo necesario”, explicó Ruiz, quien añadió que Optimus Health ha desarrollado un guante elaborado con polímeros de plástico y adaptado a la morfología de cada mano que se ajusta a la geometría de la misma, lo que incrementa el confort del guante, logrando así una mayor utilización del mismo, alcanzado mejores resultados terapéuticos.
Otros ejemplos expuestos por Ruiz del ‘hipeado’ de algunos de sus diseños fueron componentes de útiles quirúrgicos fabricados en titanio que, para reducir su tamaño sin comprometer su firmeza son ‘hipeados’ o un implante cervical que gracias a la tecnología de Hiperbaric pasa de ofrecer una vida útil de 150.000 a siete millones de ciclos, mejorando en 33 veces la longevidad del implante discal.
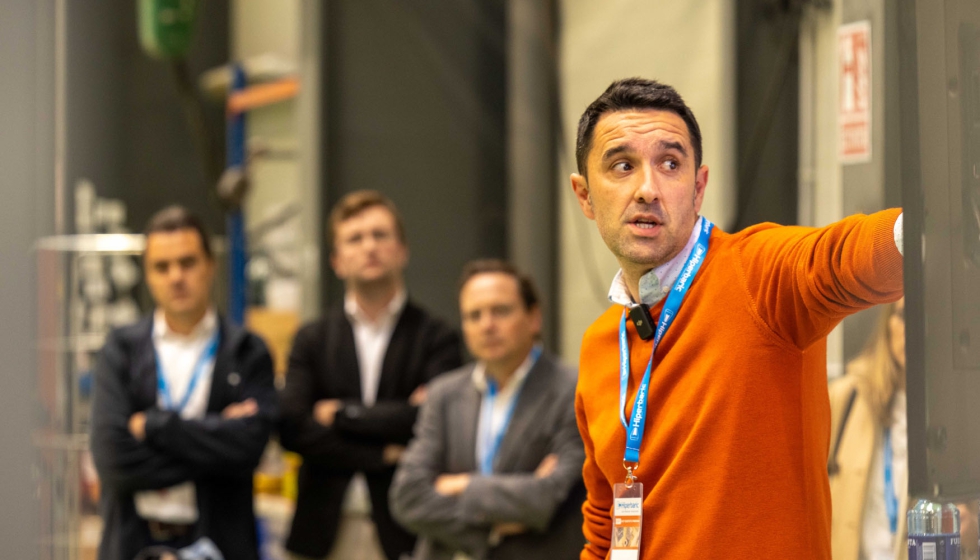
Del interior del cuerpo humano al espacio
El consejero delegado de Aenium, Miguel Ampudia, empresa vallisoletana creada en 2018 que fabrica componentes para, entre otras, la industria aeroespacial, dijo que en la actividad que lleva a cabo Aenium la tecnología HIP, “más que interesante, es necesaria. De los más de mil quinientos componentes que tenemos en órbita, muchos de ellos no podrían haber obtenido las certificaciones emitidas por la NASA o la Agencia Espacial Europea, que avalan su rendimiento en unas condiciones tan extremas, sin haber recurrido a la tecnología HIP”.
La compañía -cuya sede se encuentra en la localidad de Boecillo y cuyos productos están presentes en nueve países de tres continentes- suministra piezas a empresas presentes en la industria aeronáutica, espacial, energética y de defensa, entre otras. En el caso de la industria aeroespacial, Aenium fabrica componentes que forman parte de satélites, cohetes, motores de cohetes, turbomáquinas, quemadores…, que requieren materiales muy avanzados para realizar su función en unas condiciones extremas, sometidas, por ejemplo, a cambios de temperatura muy bruscos.
Ampudia (quien apuntó que, de los últimos siete lanzamientos realizados por la empresa Space X, la compañía castellano leonesa suministró componentes en cuatro de sus misiones espaciales), explicó que el motor de un cohete espacial genera temperaturas muy altas, de hasta 3.000 grados centígrados, “y no hay material que sea capaz ahora mismo de transferir calor de la manera en la que necesitamos y soportar estas temperaturas. Necesitamos materiales y tecnologías que nos puedan asegurar que podemos extraer todo el calor generado dentro de la combustión del cohete, porque si no somos capaces de evacuarlo el motor se funde en medio segundo”.
Aenium ha patentado una tecnología “que permite programar cómo comportará un material térmica y mecánicamente. A través de tecnologías láser y de algoritmos somos capaces de cambiar la microestructura del material en diferentes zonas y definir sus propiedades allí donde se necesita”.
En este ámbito, la tecnología HIP permite que “materiales que no pueden ser procesados utilizando tecnologías convencionales”, dotando a esos materiales de las propiedades mecánicas y térmicas que requiere para poder realizar su función en condiciones excepcionales. “Aquellos componentes de calificación más compleja Es necesario que pasen por un proceso de HIP para asegurar así que el componente no nos va a fallar”, agregó.
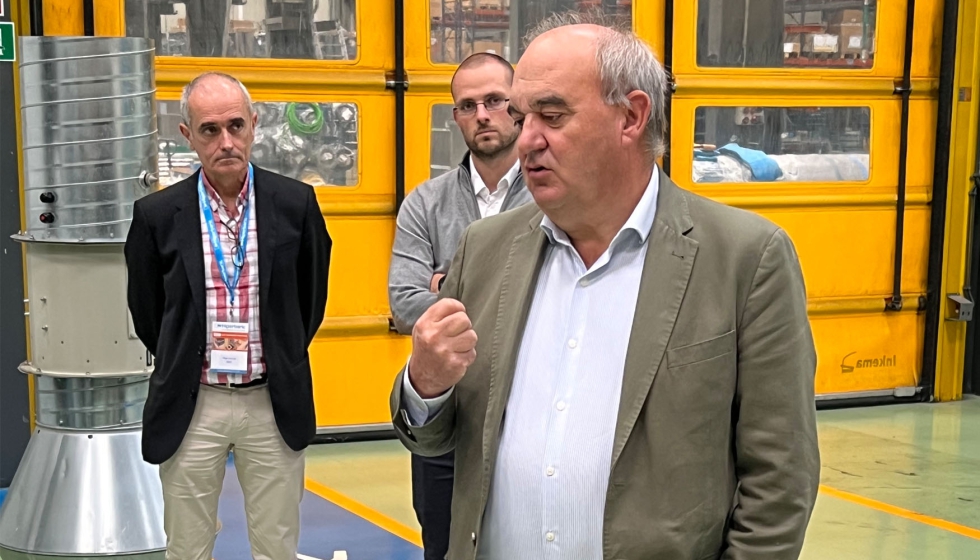
El ‘hipeado’, aplicable en diversos materiales
El director de desarrollo de negocio de Nanoker, Sergio Rivera, relató que la compañía, fundada en 2011 y que con una plantilla de veinte empleados logrará este año una facturación aproximada de 2,5 millones de euros, está especializada en la fabricación de piezas y componentes de cerámica técnica que recurre al HIP en muchos de sus procesos.
La empresa ovetense, que el pasado año elaboró 35.000 piezas, exporta alrededor de la mitad de su producción, mientras que el otro 50% se comercializa en España, donde cuenta con unos 120 clientes. Las industrias que recurren a Nanoker operan en sectores industriales en los que son necesarias piezas que ofrezcan una gran resistencia a altas temperaturas, a la corrosión, a la abrasión y al desgaste.
Además, la empresa asturiana suministra componentes al sector de la biomedicina, en algunas de cuyas aplicaciones se utiliza cerámica gracias a su biocompatibilidad y compatibilidad en tomografía. Aunque a día de hoy este segmento de actividad representa un 5% de la facturación de Nanoker, “creemos que es donde está el crecimiento de nuestra empresa”, auguró Rivera, quien explicó que “fabricamos producto de alto valor añadido y nuestro objetivo es obtener nuestros materiales, para lo cual nos apoyamos en tecnologías de fabricación avanzadas y en nuestro saber hacer de fabricación directa”.
“Nuestro producto base es polvo de cerámica que, tras ser sometido a distintos procesos, debe incrementar su densidad, para lo cual recurrimos a la tecnología HIP de Hiperbaric”, remarcó Rivera quien apuntó que la cerámica de uso biomédico se utiliza en prótesis de cadera y de rodilla o implantes dentales, entre otras posibilidades, aplicaciones “en las que se logra aumentar sustancialmente el tiempo de funcionalidad”.
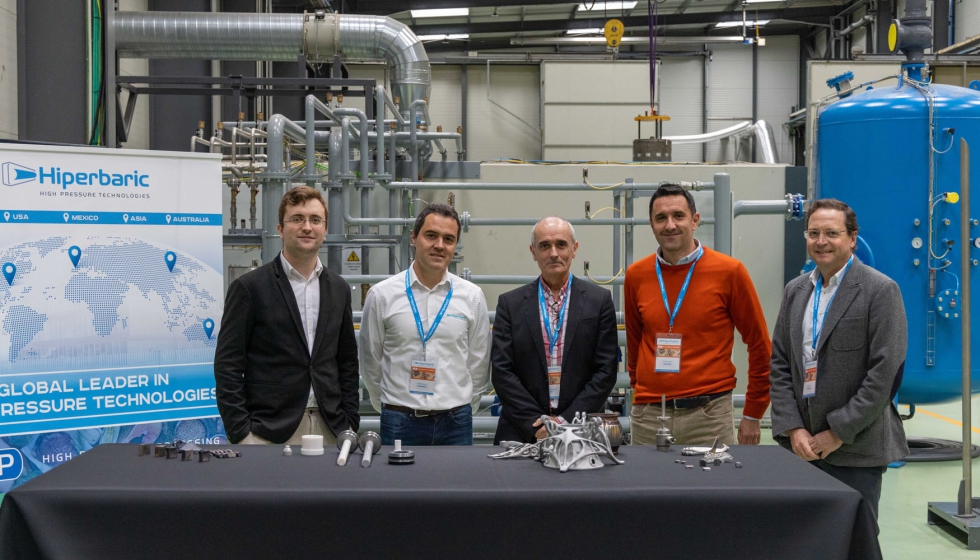