El Clúster Marítimo Español celebra un webinar centrado en la fabricación aditiva aplicada al sector
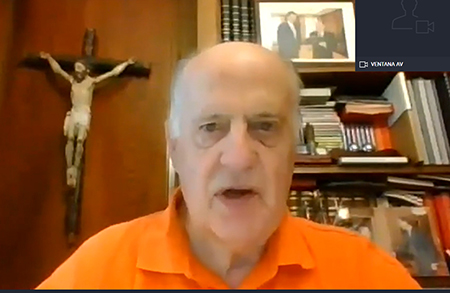
Hoy en día, la impresión 3D o fabricación aditiva FA (Additive Manufacturing, AM), de la mano de Internet de las cosas (IoT) y la inteligencia artificial (AI), está cambiando inexorablemente la naturaleza del proceso productivo, facilitando una miríada de ventajas a los creativos y a las empresas innovadoras, que vienen a generar cambios de paradigma y modelos de negocio. Este tipo de impresión de vanguardia representa un avance revolucionario y numerosas ventajas puesto que, entre otras cosas, cualquier cambio de diseño o modificación del CAD (diseño asistido por computadora) no conlleva un gasto en utillajes o modificación del molde, lo que aporta mayor flexibilidad en tiempo, adaptación al cliente, y ventajas respecto a la competencia.
Precisamente sobre “la Fabricación Aditiva (AM – 3D Printing) en el Sector Naval, ha pivotado la ponencia que ha celebrado el Cúster Marítimo Español y que ha presentado Federico Esteve, presidente de Honor de la entidad, quien ha introducido a los asistentes en la historia y evolución de esta técnica, que desde su aparición no ha dejado de crecer, introduciendo nuevos materiales, aplicaciones y modelos de negocio.
Sobre las ventajas, desafíos, limitaciones y confianza del mercado ha hablado José Allona, Business Development Manager del Area Iberia & Italy/Malta de DNV GL Maritime, firma asociada al Clúster, quien ha destacado las nuevas oportunidades de diseño, así como la reducción significativa en el tiempo de fabricación frente a la técnica tradicional de impresión. Y en este sentido se ha referido al nuevo modelo de negocio en relación a las piezas de repuesto, con una previsión para 2022 de un 85 % de suministradores que habrán incorporado para entonces la impresión 3D a su trabajo.
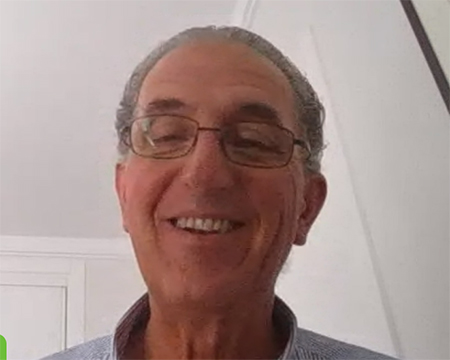
La rápida aparición de las tecnologías de FA en los últimos años, así como de fabricantes que ofrecen estos servicios, crea nuevas oportunidades para los usuarios finales, pero, asimismo, este proceso también genera una cantidad continua de cambio que podrían poner en peligro la calidad y la seguridad. A este asunto se ha referido José Allona al señalar que un sistema fiable de certificación actúa como una fuerza estabilizadora de calidad y seguridad, pero que, al mismo tiempo presenta “desafíos clave que podrían obstaculizar el avance de FA en los próximos diez años”,
En cuanto a la forma de generar la confianza necesaria en la tecnología de fabricación aditiva, José Allona ha destacado que “no todas las Sociedades de Clasificación están involucradas en la misma medida y que parámetros inapropiados del proceso pueden dar lugar a una inferior calidad de producto. Tan solo unas pocas normas son aplicables y la mayoría son demasiado generales”. Por lo tanto, el experto plantea en consecuencia la “necesidad de una tercera parte independiente que regule entre las empresas de FA, los talleres de impresión, así como los productos y los usuarios finales”. En este sentido, DNV GL aporta “expertos y laboratorios dedicados a FA, documentación de referencia de FA (reglas, etc.) y requerimientos de cualificación y de especificaciones técnicas”, según ha detallado.
Hace dos años, DNV GL creó el Centro Global de Excelencia de Fabricación Aditiva en Singapur. A través de este centro, la firma ha llevado a cabo trabajos de colaboración con Sembcorp Marine, SIMTech y NAMIC para desarrollar y certificar la tecnología de fabricación aditiva asistida por láser (LAAM) en la fabricación de estructuras a gran escala para buques de nueva construcción en esta próspera ciudad-estado de Asia. La firma ha publicado oficialmente normas y directrices de FA sobre calificación y certificación de piezas y ha modificado las reglas de buques. La firma está trabajando con más de 50 socios en Singapur y otros países de mundo, como Corea, Rotterdam o Noruega, donde ha fabricado piezas destinadas al sector marítimo que destacan por su reducción de peso y costes y, tal y como explica José Allona, con el plus para el usuario final de la “confianza en la calidad y la autenticidad del repuesto, a través de una trazabilidad transparente y documentada”.
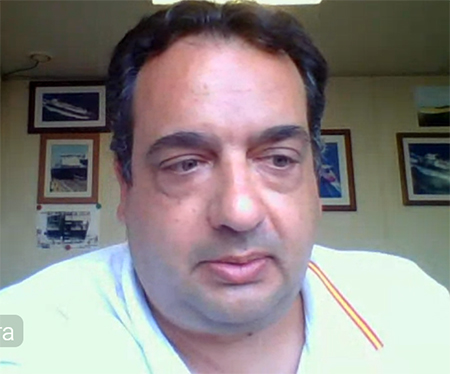
Tras la fase de lanzamiento de la FA y de expectación, llegamos a una rampa de consolidación o “meseta”, que es donde ahora nos encontramos, así lo explicaba en su exposición Víctor Casal, jefe del Taller de Habilitación del Astillero de Puerto Real y responsable del Centro de Excelencia de Fabricación Aditiva de Navantia (CEFAN), quien ha puntualizado que “a pesar de su curva ascendente, su implantación en el ámbito naval es lenta y, en los sectores en los que trabajan las grandes empresas de fabricación aditiva, apenas aparece este sector”.
En relación a la línea estratégica de I+D+i, Navantia ha puesto el foco en diferentes tecnologías como FDM, Fused Deposition Modeling; Selective Laser Sintering, SLS; Wire Arc Additive Manufacturing, WAAM; Laser Metal Depotition, LMD; o Estereolitografía, SLA, entre otras.
Las tecnologías de fabricación aditiva mediante soldadura plasma, WAAM, relacionan la soldadura con la fabricación aditiva, mientras que, en las FDM, por ejemplo, el material se dispensa por medio de una boquilla caliente y depositado sobre una superficie. La tecnología LMD, por su parte, utiliza la energía térmica focalizada para fundir el material mientras está siendo depositado. Los sistemas de deposición de energía dirigida, en este caso, pueden emplear materiales de construcción en diversos estados como el hilo o el polvo, así como diferentes fuentes de energía, aunque la más extendida es el empleo del láser. La SLA es una impresión con resina liquida que, tal y como ha explicado el experto, “aporta mucha precisión”. Por último, con la técnica SLD, el láser fusiona de forma selectiva el material en forma de polvo, en una cubeta, mediante el barrido de finas capas transversales que van, de esa forma, generando el objeto tridimensional. Si no se desea sustituir el elemento afectado, la impresión aditiva también facilita la reutilización de los componentes afectados.
Navantia inició su actividad de investigación en la tecnología de fabricación dentro del contexto de la estrategia Astillero 4.0. El primer proyecto abordado fue el desarrollo de materiales y tecnología de fabricación aditiva para la producción de cabinas de aseo (3DCabins). Navantia ha desarrollado también el proyecto Adibuque, con el que se ha puesto en valor la máquina de fabricación aditiva de gran volumen, dando continuidad a la línea de investigación iniciada con 3DCabins. Dentro de este proyecto la firma ha identificado las piezas potencialmente imprimibles en los distintos barcos y los materiales más adecuados a utilizar en cada caso. disminución del ruido. Además, destacan por ser más ligeras que las de acero, más duraderas y menos costosas”, explica Víctor Casal.
Otro de los proyectos llevado a cabo por Navantia es el 3D On Board para imprimir piezas de repuesto o recambio dentro del mismo buque durante su navegación, de la mano de las tecnologías más adecuadas, con el objetivo de imprimir dentro de un buque, eliminando los problemas por las vibraciones y movimientos de este durante la navegación”.