Inyección directa de compuestos en ZF Vigo
Las exigencias de trazabilidad y transparencia para los productores de plásticos están aumentando con tanta intensidad como la presión sobre los costes. Por eso, la planta de ZF en Vigo también quiere tomar el control en el ámbito de los polímeros y ha apostado por la tecnología de Krauss Maffei que permite la inyección directa de compuestos. El nuevo proceso DCIM (siglas en inglés de moldeo por inyección directa de compuestos) de esta empresa representada en España por Coscollola es económicamente atractivo para componentes de entre 50 y 2.000 gramos, y con el mismo tiempo de ciclo.
Los polímeros convencionales, como PP, PE o ABS, están siempre disponibles a través de los principales fabricantes de materiales en calidades constantes. ¿Un PP con un 40% de fibra de vidrio, concentrado de color y tratamiento de modificación para resistir a los impactos? No hay problema, viene del preparador de compuestos. ¿Seguro? Achim Härtel, ingeniero de la sección Core Engineer Plastics de ZF en Aldorf (Alemania), se ha llevado más de una sorpresa en este ámbito: "En ocasiones, el PP se calentaba en exceso sin que nadie se diera cuenta. Hasta hemos llegado a encontrar más de una vez cuerpos extraños, como partículas metálicas, en los compuestos". Todos los que, al igual que ZF, se dedican a la fabricación de componentes de seguridad para el sector de la automoción conocen bien las implicaciones de las retiradas de productos o las paradas de la producción debidas a errores. Por lo tanto, es natural que se busque blindar al máximo la calidad de los productos; naturalmente, cuanto más económico resulte, mejor.
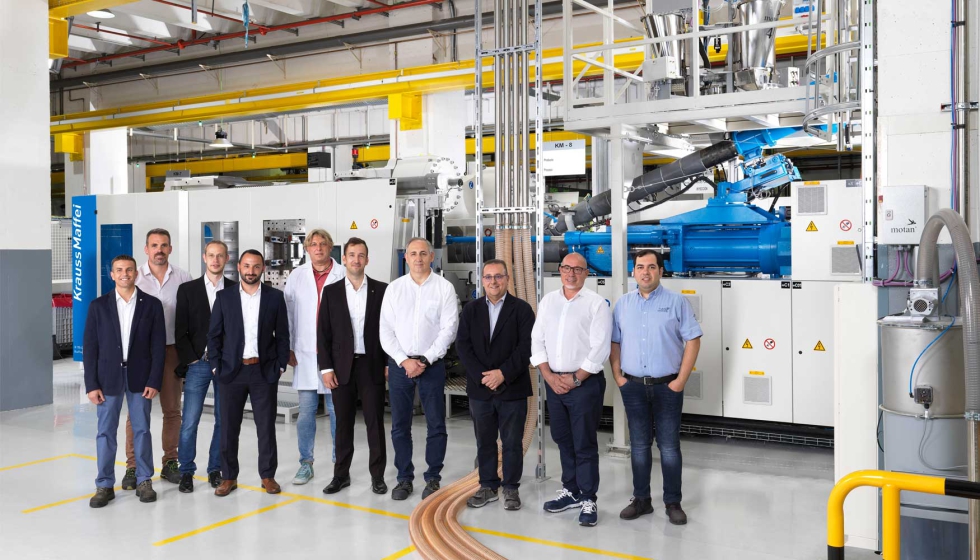
Equipo a cargo del exitoso proyecto de composición directa en ZF Vigo (desde la izquierda): Eduardo Casas (ZF, Injection Molding specialist), Edgar López (ZF, Manufacturing Engineer), Thomas Drogi (KraussMaffei, Process Engineer), Christian Seyferth (KraussMaffei, global expert sales), Achim Härtel (ZF, Core Engineer Plastics), Jacob Seco (ZF, Manufacturing engineer specialist), José Trasobares (ZF, Manufacturing Engineering manager), Ángel Lemus (Coscollola, director Post-Venta), Antonio Muñoz (Coscollola, director comercial Inyección), Ramazan Baser (Motan-Colortronic, Project Engineer)
Veinte años de experiencia en composición directa
KraussMaffei, firma representada por Coscollola, dispone de más de dos décadas de experiencia en el ámbito de una técnica que une la elaboración del compuesto y su inyección directa en un solo proceso. Su célebre instalación de inyección unida a una extrusora de doble husillo resultó especialmente económica para componentes de más de 1,5 kilogramos de peso, habida cuenta de los costes de inversión. Ahora, amplía sus posibilidades con el nuevo proceso DCIM que, gracias al uso de una extrusora monohusillo, es apropiado para artículos de entre 50 y 2000 gramos (a partir de PP natural).
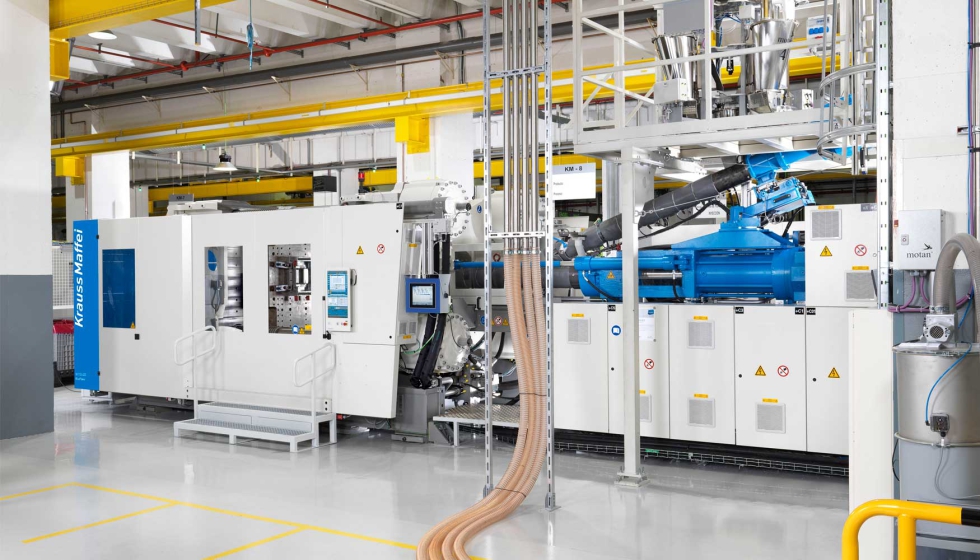
Los requisitos son los mismos: los polímeros se mezclan, se tratan con aditivos, se refuerzan o se rellenan y se incorporan al proceso de moldeo por inyección. Así se ahorran los costes asociados a las técnicas externas de compounding y, por otra parte, se brinda al transformador un control máximo sobre el material utilizado. Achim Härtel observa otra ventaja más: "Ahora, en nuevos proyectos o si cambian los requisitos, podemos crear por nuestra propia cuenta nuevas propuestas de formulación directamente adaptadas a las especificaciones del componente correspondiente. ZF se ocupa de la calidad de los materiales. Por nuestra parte, nosotros atesoramos nuestro propio saber hacer, que hemos documentado íntegramente y comprobado en nuestras propias instalaciones".
Una extrusora monohusillo que ofrece una mezcla perfecta
De la perfecta mezcla y homogeneidad de todos los componentes se encarga el husillo especial de la extrusora, que destaca no solo por su diseño optimizado, sino también por su extraordinaria longitud. Si, por lo general, la relación longitud-diámetro suele ser de 17-23 (en las máquinas estándar), en el proceso DCIM presenta una espectacular relación de 30 L/D. Puesto que los componentes técnicos que entran en juego en cuando se recurre a la técnica de la elaboración del compuesto y su inyección directa suelen tener tiempos de ciclo de 20 segundos o más, la preparación adicional de los materiales se realiza prácticamente con neutralidad de tiempo de ciclo.
El concepto DCIM ofrece la máxima flexibilidad a los procesadores de plástico. En una máquina hidráulica estándar (por lo general, de la serie GX), la extrusora monohusillo va integrada en un montaje superpuesto por encima de la unidad de inyección, para facilitar su uso. Ambas unidades producen de forma discontinua. Esto significa que la extrusora se detiene automáticamente cuando se alcanza el volumen de inyectada para el siguiente ciclo, y la masa fundida compuesta accede directamente al sistema de plastificación de la máquina de moldeo por inyección sin refrigeración ni almacenamiento intermedio.
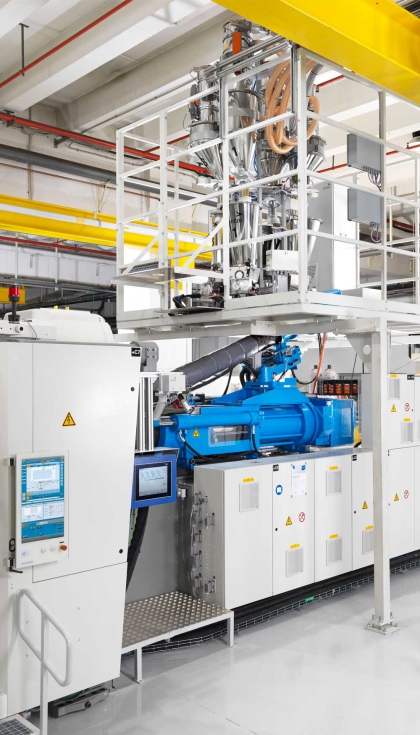
La producción a temperatura constante reduce la huella de CO2
El proceso de producción en un solo paso tiene lugar a temperatura constante, lo que no solo disminuye la degradación de polímeros, sino que permite ahorrar energía y reducir las emisiones de CO2. Cuando no se desea preparar compuestos, la máquina se puede utilizar para procesos estándar sin más complicaciones. Gracias a la estructura en Z de su conjunto, la máquina de inyección es muy compacta, por lo que ocupa muy poco espacio.
El sistema DCIM fue lanzado al mercado en 2019 y pese a la ralentización durante la pandemia de coronavirus, ahora despierta más interés que nunca. Según Achim Härtel, de ZF, frente a los sistemas de otros proveedores que impregnan fibras sin fin con material de matriz de baja viscosidad, el proceso destaca porque permite procesar también plásticos de viscosidad media que ofrecen mejores propiedades mecánicas para los componentes de seguridad. Se trata de una perspectiva de gran importancia para ZF Vigo, que pertenece a la división denominada 'R' (del inglés Restraint: 'contención') del grupo ZF y desarrolla equipos de protección personal. Además, el sistema DCIM está también disponible para máquinas con fuerza de cierre de entre 1.600 y 11.000 kN, por lo que también es apropiado para aplicaciones de mayor envergadura o para herramientas con múltiples cavidades.
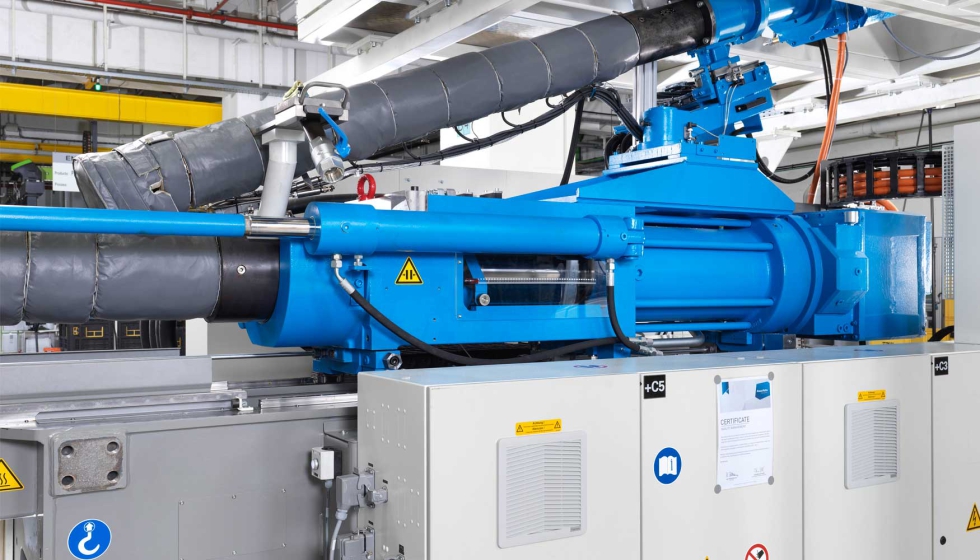
Reducción de los costes de material y retorno de inversión más rápido
Además del dominio de las propiedades de los materiales, un ejemplo de aplicación de KraussMaffei ilustra las ventajas en materia de ahorro de costes que ofrece el sistema: en el caso de un plato de plástico para el montaje de lana mineral, compuesto e inyectado a partir de PA6 con un 50% de fibra de vidrio, 2% de agente de flujo, 0,5% de concentrado de color y 0,5% de termoestabilizante, el proceso DCIM reduce los costes de material en un 20%. De este modo, la inversión adicional por la instalación DCIM (en comparación con un equipamiento estándar) se amortiza en menos de un año.
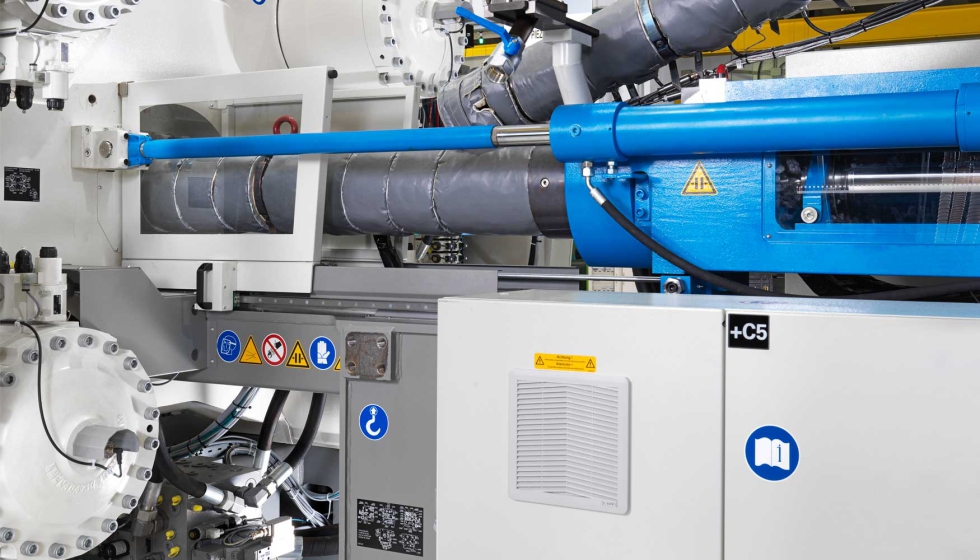
La masa fundida compuesta accede directamente desde la extrusora monohusillo a la unidad de plastificación de la máquina de moldeo por inyección, de modo que el proceso entero se realiza a una temperatura constante. De este modo, se disminuye la degradación de polímeros, se utiliza menos energía y se ahorra CO2.
Apto también para material reciclado y bioplástico
Esta tecnología resulta también de interés en el ámbito del reciclaje y el uso de bioplásticos y fibras naturales. Jacob Luis López, Manufacturing Engineer Specialist en ZF Vigo, tiene ya la vista puesta en estos ámbitos: «La competencia se ha vuelto tan exigente que es preciso estar siempre un paso por delante». Sin embargo, lo primero es consolidar la tecnología y llevarla a otras ubicaciones de ZF. La planta de ZF en Timișoara (Rumanía) ya ha encargado dos máquinas DCIM, mientras que la precursora planta de Vigo acaba de encargar una unidad más.
En la feria K 2022, el proceso DCIM ocupará el centro de atención para KraussMaffei. Se prevé exponer un embalaje de material reciclado como ejemplo de aplicación, así como una mezcla de polímeros de distintas viscosidades. Se trata de que los procesadores de plásticos puedan, en el futuro, tomar el control de su responsabilidad en lo que respecta a los materiales y las formulaciones.