Viaje al reciclado del acero
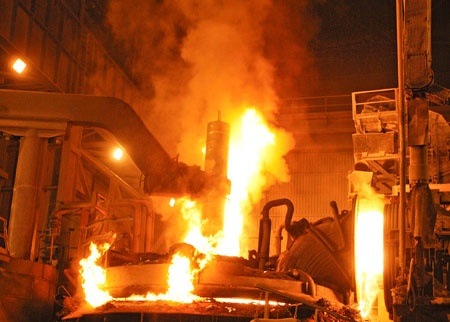
La fábrica en Zaragoza de ArcelorMittal, primer productor mundial de acero, se ubica en el Parque Tecnológico de Reciclado ‘López Soriano’, sobre una superficie de 220.000 m2, de los que 80.000 m2 son cubiertos. Estas modernas instalaciones han sustituido a las que anteriormente tenía la compañía en el centro de Zaragoza, a apenas 700 m de la Plaza de El Pilar, y han supuesto una inversión cercana a los 140 millones de euros. Para el traslado a la nueva planta se tardó cinco años, concluyéndose en 2007, pero con esta iniciativa ArcelorMittal ha conseguido duplicar la producción que tenía hasta entonces.
La nueva planta está dividida en dos grandes áreas, la acería, que trabaja con chatarra de origen nacional al 100%, y la zona de laminación, que convierte el semiproducto o palanquilla en un producto acabado.
Esta planta de ArcelorMittal se caracteriza por su alto grado de automatización, que le permite, además de agilizar sus procesos productivos, incidir en su objetivo de “0 incidentes”. Además, son instalaciones que demuestran una gran preocupación medioambiental, trabajando con intensidad en la reducción de las emisiones de CO2.
Acería
La visita a la fábrica de ArcelorMittal en Zaragoza se inició en el depósito de chatarra, con capacidad para 35.000 toneladas de material (el consumo anual de esta planta está entre las 600.000 y 800.000 toneladas).
Antes de entrar en este depósito, la chatarra debe cumplir con una serie de requerimientos de seguridad como que no incluya elementos que puedan producir explosiones (depósitos cerrados…), la ausencia de materiales peligrosos e inflamables y estar libre de contaminación. También ha de estar libre de elementos estériles no férricos y adecuadamente separada y clasificada para facilitar tanto su almacenamiento en el parque de chatarra de la acería como su posterior manipulación.
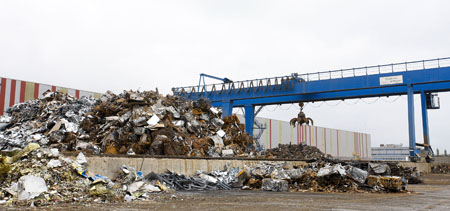
La vigilancia de la entrada de chatarra en las acerías para su reciclaje se realiza a través de un sofisticado sistema de detección radiológica, de materiales peligrosos, impropios, etc., con el que se garantiza la seguridad del proceso.
Una vez clasificada la chatarra, mediante una cesta de 95 toneladas de capacidad se hace una selección del material, de acuerdo a sus diferentes calidades. Mediante grandes grúas se lleva elevada la cesta hasta la parte superior del horno, una “enorme cazuela”, donde se deposita el residuo. Para cada ciclo de fusión se necesitan alrededor de 135 toneladas de material, por lo que es habitual emplear dos cargas por ciclo.
En el caso de la acería de ArcelorMittal Zaragoza se trabaja con un horno eléctrico que incorpora un gigantesco electrodo de grafito (esta planta tiene contratada una potencia de 100 MW). El horno eléctrico era un proceso que se utilizaba inicialmente para la fabricación de aceros especiales, pero que en la actualidad facilita el reciclaje masivo de chatarra para producir cualquier tipo de acero, con el único límite de la calidad de la materia prima.
En España hay 21 acerías de horno eléctrico, que producen el 75% del acero total fabricado en nuestro país y consumen alrededor del 90% de la chatarra que el sector utiliza como materia prima. El restante 10% se utiliza en las 2 acerías LD que producen acero básicamente a partir de mineral de hierro, utilizando un cierto porcentaje de chatarra con efecto refrigerante.
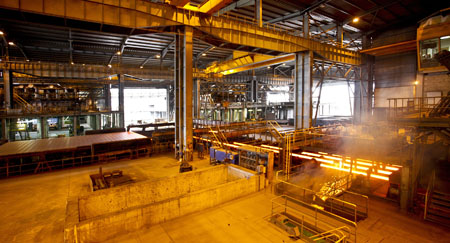
El proceso de fusión, para el que se alcanzan temperaturas en el horno de 1.600 °C y que requiere ciclos de 1 hora aproximadamente, se completa con la oxidación de ciertas impurezas para eliminarlas, ayudado por la inyección de oxígeno. El proceso implica la formación de una costra de óxidos, que evita las pérdidas de energía y protege el acero líquido. Esta costra se retira posteriormente, formando la denominada escoria, que tiene distintas aplicaciones como por ejemplo su uso como sustrato para carretera. Después de la fusión, el acero pasa a un segundo horno más pequeño, en el cual se ajusta la composición de los múltiples aleantes que determinan cada tipo de acero.
Como otra prueba más de su alto compromiso medioambiental, la fábrica de Zaragoza cuenta con una moderna instalación de depuración de humos, que a partir de diferentes filtros permite separar materiales como el zinc para su posterior valorización.
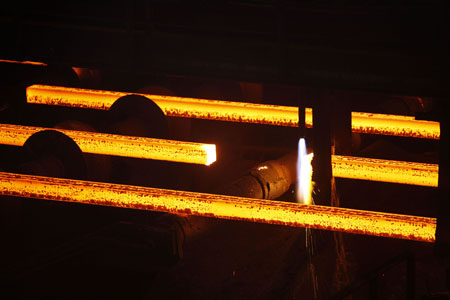
Palanquillas y laminación
A continuación se solidifica el acero líquido en el proceso de colada. Se puede colar el acero sobre moldes con la forma de la pieza que se quiere fabricar (acero moldeado) o bien sobre lingoteras para su transformación posterior por deformación en caliente (laminación, forja…). Y hay un tercer método de colada, el más moderno y que en España representa el 90%, denominado colada continua, que consiste en colar el acero en un molde de fondo abierto, cuya sección transversal tiene la forma que se desea obtener, y del que se va extrayendo de modo continuo el acero solidificado en palanquillas, redondos, planchones… Este último caso es precisamente el que emplea ArcelorMittal Zaragoza, que solidifica el acero líquido mediante agua y que corta las palanquillas mediante sopletes de oxígeno.
Una vez que las palanquillas rebajan su temperatura hasta los 400 °C aproximadamente, ya pueden ser manipuladas a través de grúas imantadas, para pasar al siguiente proceso de laminación.
Finalmente, los semiproductos obtenidos a través de la colada se laminan en caliente, haciendo pasar el material entre dos rodillos en un proceso continuo de deformación. Esta técnica de laminación permite obtener productos de sección constante (perfiles, barras, alambrón…) y producto planos (chapas, bobinas). En el caso de ArcelorMittal Zaragoza, uno de sus productos más conocidos son las secciones que componen las torres de alta tensión.
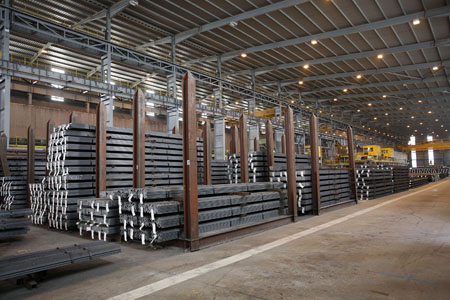
El producto terminado pasa al almacén, listo para ser cargado en alguno de los numerosos camiones que llegan diariamente a esta fábrica. Todos los artículos cuentan con su correspondiente certificado de calidad y, gracias a un sistema de códigos, se puede seguir al 100% su trazabilidad.
La visita concluyó precisamente en el laboratorio que tiene ArcelorMittal en estas instalaciones, donde se analizan mecánica y químicamente todos los materiales, de tal forma que se pueda mejorar el proceso y lograr productos ajustados a las necesidades específicas de cada uno de los clientes.
En 2011 las acerías españolas reciclaron un total de 12,5 millones de toneladas de acero (chatarra férrica), de las cuales 7,7 millones de toneladas eran de procedencia nacional y los restantes 4,8 millones de toneladas procedían de la importación.
Estas cifras colocan a España como líder del reciclaje en la UE, junto con Italia. El 75% del acero fabricado en España es acero reciclado, mientras la media europea es del 50% y la media mundial del 40%.
Por su gran capacidad recicladora y la alta tecnología de sus acerías, la industria siderúrgica española está en condiciones de garantizar el reciclaje de toda la chatarra recogida en nuestro país. El sector siderúrgico cierra el ciclo del reciclaje del acero, más que duplicando el valor añadido con respecto a la materia prima (chatarra férrica).
El acero es el material que más se recicla. En España, la industria siderúrgica recicla más acero que la suma de todos los demás metales, el vidrio, el papel y el plástico juntos y la tasa global de reciclaje en nuestro país supera ya el objetivo del 90% fijado sectorialmente para 2050 a nivel mundial.
Al final de su ciclo de vida se recoge y se recicla el acero procedente de la construcción, el automóvil, los electrodomésticos, los barcos, los envases de hojalata… y prácticamente la totalidad del acero que utilizamos en muy distintos productos y aplicaciones.
El acero tiene una particular característica que facilita su recogida para el reciclaje: es magnético, de modo que con un electroimán puede ser fácilmente separado del resto de los residuos.
La recogida del acero para su reciclaje se produce por muy distintas vías: desde los centros de transferencia y las recogidas selectivas, a la recogida a pie de calle o la separación por imanes en vertederos, entre otros.
A lo sencillo de su recuperación se une la gran capacidad recicladora de la industria siderúrgica que da nueva vida al acero para transformarse otra vez en parte de un automóvil, de una viga de un edificio, de una lavadora, de un aerogenerador, de una bicicleta, en una lata, en un clip, en una cuchara, en un tornillo…
Y ese ciclo de reciclaje, gracias a que el acero es un recurso permanente, es un ciclo potencialmente sin fin, en el que la industria siderúrgica recicla una y otra vez el acero sin pérdida de su calidad y sin apenas merma, en un eterno renacer. De hecho actualmente se sigue reciclando acero fabricado hace 150 años.
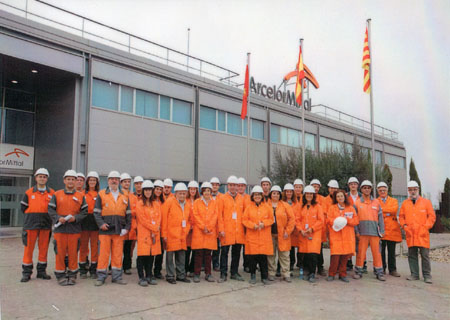
El acero, según se señalaba en rueda de prensa, es el segundo material en comercio, sólo por detrás del petróleo, y el segundo también en volumen (el primero es el cemento), consolidándose como un elemento imprescindible en la mayoría de productos que nos rodean, desde un pequeño clip hasta los más modernos aviones, pasando por el revestimiento de los neumáticos, el sector naval, los aerogeneradores, etc.
La industria siderúrgica española supone el 4,6% del PIB industrial. Con datos de 2011, produjo 15,5 millones de toneladas de acero bruto (tercer productor europeo por volumen tras Alemania e Italia); el consumo aparente de productos siderúrgicos fue de 13 millones de toneladas. El sector es netamente exportador -63% de las ventas-, alcanzando el 3,9% de las exportaciones españolas de bienes.
Innovación, eficiencia, sostenibilidad y seguridad laboral son principios que rigen la estrategia del sector, que se reconoce como un actor fundamental de la nueva economía verde. Cada tonelada producida conlleva aproximadamente 4,5 euros en inversiones medioambientales. La industria realiza un uso eficiente de los recursos hasta aprovechar casi el 80% de los residuos y subproductos que genera en el proceso.
El sector siderúrgico se caracteriza además por ser el mayor operador logístico tras el petróleo y sus derivados.
Unesid es la asociación empresarial de la siderurgia española que aglutina 46 empresas, que emplean a 60.000 personas (empleo directo e inducido) –además de las 20.000 que intervienen en la recolección de chatarra- y facturan en su conjunto 14.000 millones de euros.