Dynasol invierte 15 millones de euros en la logística de su fábrica de Cantabria
Dynasol inauguró el pasado 12 de mayo, oficialmente, su nueva plataforma de optimización logística en su fábrica de Gajano, reforzando el compromiso que tiene esta empresa con sus clientes y, en definitiva, con su única planta en España, ubicada en Cantabria.
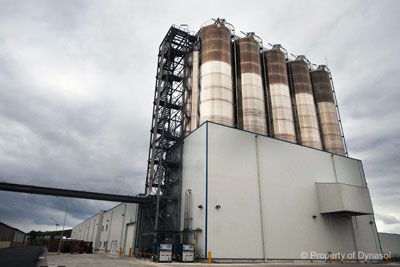
La nueva instalación es sorprendente, por sus dimensiones, pero también por el nivel tecnológico que incorpora. Se trata de un nuevo esquema de gestión logística que incorpora, entre otros, un sistema de alta tecnología de homogenización del caucho sintético a granel, almacenaje, carga y envasado del mismo. Durante la inauguración, presidida por el consejero de Industria y Desarrollo Tecnológico del Gobierno de Cantabria, Juan José Sota Verdión y el presidente del Consejo de Administración de Dynasol, Jesús Guinea Rodríguez, tanto los clientes como las autoridades presentes y Plásticos Universales / Interempresas.net tuvieron la ocasión de ver las nuevas instalaciones durante una visita guiada. Esta innovadora plataforma ha supuesto para Dynasol una inversión de 15 millones de euros, lo que la convierte en una de las mayores inversiones logísticas realizadas en la industria del caucho sintético a nivel mundial en los últimos años. Pero las grandes cifras no son probablemente tan importantes como las ventajas que la nueva instalación suponen para los clientes y la industria, ya que mejora la calidad de las entregas, teniendo, a la vez, muy presente el impacto sobre el medio ambiente.
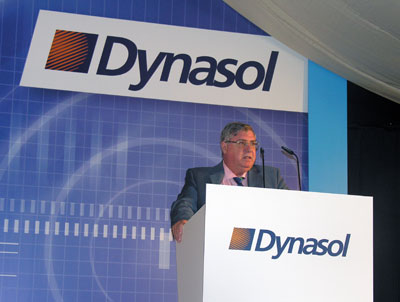
Otras ventajas derivadas del nuevo sistema son el incremento en la seguridad de las operaciones de carga y descarga, debido a la reducción de los movimientos dentro del área de envasado, y la reducción de las emisiones de CO2, gracias a que el producto es transportado mediante aire directamente a los silos. También mejora la homogeneidad del producto, con lo cual se asegura la consistencia de la calidad, y la preservación del producto.
La instalación cuenta con diez silos (capacidad de 150 toneladas cada uno) y cinco muelles de carga, así como con cuatro líneas de transporte neumático con capacidad de transportar siete toneladas por hora, que se encargan de introducir el material de los silos en sacos o 'big bags'.
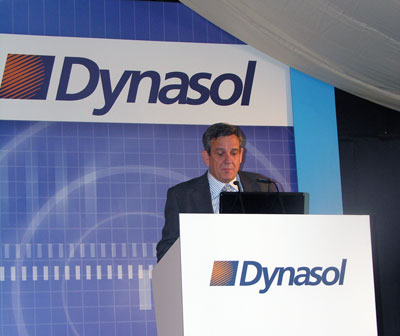
La tecnología de las líneas, la organización de los silos, bajo los cuales se encuentra un sistema flexible que deja cabida a futuras ampliaciones, aporta un valor añadido muy significativo, pero a los ojos de cualquiera, el almacén alcanza unas dimensiones más que llamativas. Son 15.000 metros cuadrados con estanterías cargadas de productos Dynasol.
Aplicaciones del caucho de Dynasol
El caucho sintético producido por Dynasol se destina, entre otras, a aplicaciones tan variadas como los adhesivos y sellantes, los asfaltos para carreteras y láminas asfálticas para impermeabilización de suelos y tejados, aplicaciones médicas, cables, envases y embalajes y para infinidad de objetos cotidianos destinados a la higiene personal; aportando así mayor confort, salud y seguridad a nuestra vida diaria.
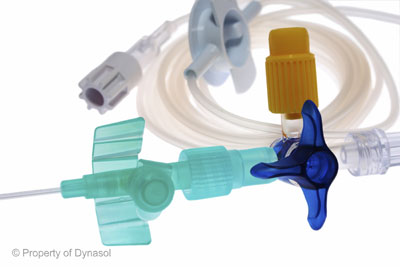
Según afirmaron los responsables de la compañía en los actos oficiales, Dynasol se aleja de los productos “commodities” para destinar sus materiales a aplicaciones que requieren un cierto valor añadido. Aprovechan para ello el Centro de Tecnología Repsol en Madrid, así como el de Kuo en México, y el resultado son materiales homologados, por ejemplo, por la Nasa. No en vano la compañía invierte al año 3,5 millones de euros en tecnología.
La gama de Dynasol
Dynasol es uno de los líderes en el mercado global de una amplia variedad de copolímeros estireno-butadieno incluyendo SEBS, SBS lineal y radial y SBR en solución, comercializados bajo las marcas Solprene y Calprene.
Es el resultado de un joint venture de la división de cauchos sintéticos de Repsol y Kuo (antes Desc).
Sus innovadores productos se utilizan en una gran variedad de aplicaciones como formulación de adhesivos y selladores, compuestos termoplásticos, modificación de plásticos, modificación de asfaltos (pavimento y membranas impermeabilizantes), calzado, artículos vulcanizados y otros.
Los SEBS, por ejemplo se utilizan cuando se requiere estabilidad duradera a la oxidación térmica y cuando es necesaria la compatibilidad con otros adhesivos de baja polaridad.
Los SBS copolímeros de bloque se utilizan principalmente cuando hay que reducir costes o cuando se tienen que mejorar las propiedades adhesivas en la formulación del adhesivo.
En cuanto a los SBC copolímero de bloque se recurre a ellos en adhesivos para una amplia gama de aplicaciones, como cintas, etiquetas, construcción, selladores o transporte.