La tecnología de rectificado en el punto de mira
En su segunda edición, GrindingHub congregó de nuevo en Stuttgart toda la tecnología de rectificado con alrededor de 500 fabricantes de renombre procedentes de 31 países presentando numerosas innovaciones a lo largo de toda la cadena de procesos de la tecnología de rectificado. La atención se centró en reducir el consumo de energía y materias primas, así como en mitigar la escasez de trabajadores cualificados mediante la automatización y la digitalización. A continuación, se recogen las principales tendencias que marcarán a este segmento.
Las nuevas rectificadoras y conceptos de rectificado aumentan la variabilidad
Erwin Junker Maschinenfabrik GmbH, de Nordrach, presentó por primera vez rectificadoras basadas en la Plataforma 3, de nuevo desarrollo. Se trata de rectificadoras que pueden adaptarse de forma flexible a su aplicación mediante diversas configuraciones. Un kit de construcción modular permite la implementación de rectificadoras y procesos diseñados para diversas aplicaciones sobre una base uniforme y utilizando tantas piezas idénticas como sea posible. Algunos ejemplos son las rectificadoras de alta velocidad para el mecanizado con herramientas de CBN y diamante o las rectificadoras para procesos convencionales de rectificado con corindón. Esto no sólo aumenta la rentabilidad, sino que también reduce el rendimiento y los plazos de entrega. Además, el mayor número de piezas idénticas aumenta la disponibilidad de piezas de repuesto. La base es una bancada de máquina fabricada como fundición mineral. A partir de ella, pueden montarse distintos conjuntos de mesa, guías, husillos portapiezas y contrapuntos adaptados a cada aplicación. Pueden utilizarse hasta tres husillos de rectificado. Las máquinas están equipadas con un sistema de medición durante el proceso que mide las dimensiones de la pieza durante el proceso y calcula los datos de corrección sobre esta base para compensar las influencias del proceso, como el desgaste de la herramienta y las fluctuaciones de temperatura. Una característica especial de esta clase es el uso de un sistema de medición absoluto para el reavivado interno de la máquina. Además, las rectificadoras de la Plataforma 3 disponen de un concepto de automatización integrado. Esto incluye enfoques para la carga manual, así como la carga mediante robots industriales o la carga mediante cargadores de pórtico internos y externos.
En el campo del rectificado cilíndrico exterior, el grupo NSH de Chemnitz expuso su último modelo Wotan S3A en GrindingHub. Se trata de una rectificadora cilíndrica externa compacta para procesar piezas de trabajo pequeñas y medianas de hasta un máximo de 600 kg y una anchura central seleccionable de entre 600 y 2.000 mm, según la versión. Además de una bancada de granito, la máquina dispone de dos ejes lineales controlados por CNC con cojinetes hidrostáticos en las direcciones z y x. En combinación con un accionamiento lineal, presentan un desgaste reducido en comparación con los accionamientos de husillo de bolas o las unidades de recirculación de rodillos. En función de los requisitos de precisión, la máquina puede equiparse con un husillo accionado por correa, directo o hidrostático. Otras opciones de adaptación se refieren a la tecnología de reavivado integrada, la tecnología de medición y la configuración de la unidad de rectificado. Rollomatic SA, de Suiza, presentó su nueva máquina GrindSmart 630 RS. Se trata de una rectificadora de herramientas de 6 ejes para la producción de herramientas de hasta 500 mm de longitud total en una gama de diámetros de 0,1 a 20,0 mm y una longitud máxima de ranura de 140 mm. Estas herramientas se utilizan, por ejemplo, en tecnología médica en forma de taladros óseos operados con robots quirúrgicos. La manipulación de las herramientas dentro de la máquina está controlada por robots. En el lado del husillo pueden realizarse diversas configuraciones con y sin cambiador de muelas. Los ejes se accionan mediante motores lineales.
Con el fin de reducir las emisiones contaminantes y de partículas, la norma Euro7 establece un límite máximo para las emisiones de partículas procedentes de los sistemas de frenado. Por ello, este es uno de los puntos centrales de los actuales proyectos de desarrollo e investigación. Uno de los métodos de aplicación son los discos de freno con revestimiento duro. Éstos ofrecen la posibilidad de reducir la abrasión hasta en un 90%. Sin embargo, el revestimiento de material duro plantea retos durante el mecanizado debido a la matriz relativamente blanda con carburos incrustados y al diferente comportamiento de mecanizado de los dos materiales. Entre otros, la cadena de procesos para fabricar rotores de freno con revestimiento duro incluye el torneado, el revestimiento por láser y el rectificado. Estos pasos del proceso dan lugar a otros factores de influencia que deben tenerse en cuenta en el control del proceso de rectificado. Esto requiere una visión holística y la coordinación de los pasos del proceso. En GrindingHub, el grupo Emag de Salach presentó piezas de la cadena de mecanizado para rotores de freno con revestimiento duro, como la VLC 450 DG, una máquina especial para el rectificado de alta precisión de rotores de freno con revestimiento duro. En este caso se utiliza el rectificado de doble cara. Debido a su alta productividad gracias al mecanizado simultáneo de ambas superficies del anillo de fricción, su alto rendimiento y los cortos tiempos de ciclo, el proceso se utiliza principalmente en la producción de rotores de freno. Las estructuras rectificadas en cruz creadas perpendicularmente al eje de rotación mejoran el comportamiento tribológico de rodaje de los rotores de freno en comparación con las estructuras en la dirección circunferencial. La disposición vertical del husillo facilita la eliminación de las partículas de material duro, al tiempo que permite una buena accesibilidad para los trabajos de ajuste y mantenimiento. La herramienta de rectificado está diseñada como un anillo intercambiable que, gracias a su reducido peso de menos de cinco kg, permite un manejo relativamente sencillo al cambiar de herramienta. La máquina dispone de carga y descarga automatizadas mediante una lanzadera de alimentación y un elevador de piezas. Esto permite su integración en la línea de producción.
Muchos fabricantes más pequeños también presentaron sus productos en GrindingHub. Por ejemplo, Avyac Machines de Veauche (Francia) y la empresa suiza G-Elements GmbH. Avyac presentó su rectificadora de brocas CNC de 5 ejes NC18. Se trata de un concepto de máquina compacta totalmente automatizada para la producción de brocas de HSS y carburo sólido con diámetros de 1 a 8 mm, que pueden ampliarse opcionalmente hasta 14,5 mm. La longitud máxima de la herramienta es de 320 mm. Un cargador circular permite utilizar hasta 90 herramientas, que se cargan y descargan por gravedad gracias a un diseño especial. Se utilizan muelas de diamante o CBN con un diámetro de 100 mm. El sensor de medición integrado permite escanear los filos de corte, lo que a su vez permite determinar la posición de corte para los procesos de reafilado de herramientas.
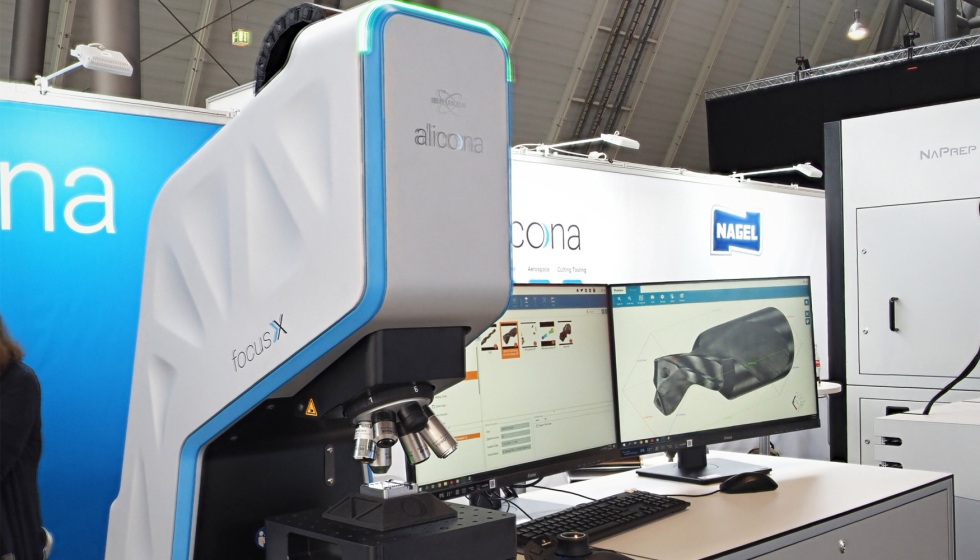
La variación de enfoque avanzada también permite la medición óptica de superficies muy reflectantes. Foto: VDW/Nicholas Det.
Las nuevas soluciones de software permiten simplificar el diseño y la planificación de los procesos
Además de las rectificadoras de herramientas, también se presentaron numerosos desarrollos de software para la planificación y el diseño de procesos. Un ejemplo es la implementación de herramientas de rectificado mecánico en el software SIGSpro de Alfred H. Schütte GmbH & Co. La introducción de los datos de la pieza, la muela y la tecnología permite generar automáticamente programas CNC que pueden transferirse al control de la máquina y procesarse allí. El tallado mecánico es un proceso alternativo
producción de engranajes. Los ejes de la herramienta y de la pieza están dispuestos en ángulo entre sí. Como resultado del posicionamiento de la herramienta, un avance axial definido y la velocidad acoplada de la herramienta y la pieza de trabajo, se produce un movimiento relativo, por el que el espacio del diente se desprende de la herramienta a lo largo de la dirección de corte principal. Las ventajas de este proceso son la producción de engranajes externos e internos, una pequeña excentricidad y la producción de diferentes engranajes en un único proceso de sujeción.
Dos empresas de nueva creación, Ai-omatic solutions GmbH, de Hamburgo, y Tetralytix GmbH, de Hannover, presentaron sus soluciones de software para optimizar los procesos de producción. El software Toolyzer de Teralytix permite analizar y evaluar cualquier geometría de herramienta y proceso de mecanizado. Además de predecir las fuerzas del proceso, el par y la potencia, también se pueden detectar las condiciones críticas de engrane y predecir la calidad de la pieza de trabajo. Entre otras cosas, esto ofrece la posibilidad de acortar los tiempos de desarrollo y ahorrar costes. Otra forma de minimizar gastos en el proceso de producción es garantizar un proceso de producción estable y evitar tiempos de inactividad de la máquina. Para ello, la empresa ai-omatic ha desarrollado un software que utiliza modelos probabilísticos para ofrecer una alternativa a los enfoques de mantenimiento convencionales. Para ello, se detecta el estado de las máquinas en tiempo real y se realizan predicciones sobre los requisitos de mantenimiento de los sistemas de la máquina a partir de diversas fuentes de datos integrables.
Una visión holística de la rectificadora y los periféricos permite un control eficaz del proceso
Una rectificadora capaz no es el único factor decisivo en la producción de piezas de alta calidad. El diseño de un proceso de rectificado eficiente y con optimización de recursos requiere una visión holística de la rectificadora junto con sus periféricos. Cuando se trata del suministro de lubricantes, por ejemplo, cabe distinguir entre el lubricante en sí, las estrategias de suministro correspondientes y el filtrado y reprocesado de lubricantes tras el proceso de rectificado. Numerosas empresas presentaron sus productos de estas áreas en GrindingHub. Entre ellas figuran Oelheld GmbH de Stuttgart, Carl Bechem GmbH de Hagen, la empresa suiza Blaser Swisslube AG y Knoll Maschinenbau GmbH de Bad Saulgau.
El husillo es un componente importante de todas las máquinas herramienta y rectificadoras. GMN de Nuremberg, por ejemplo, presentó su nueva serie de husillos UH para procesos de rectificado cilíndrico interior y exterior. Se caracteriza por importantes optimizaciones de las principales características de rendimiento en todas las versiones. Por primera vez, GMN utiliza motores síncronos con una potencia máxima de 32 kW y velocidades de hasta 120.000 rpm en un husillo de serie. Gracias a su mayor par, los motores síncronos consumen en la mayoría de las aplicaciones un tercio menos de potencia instalada que los motores asíncronos. El resultado es un mejor aprovechamiento del rango de potencia disponible y una mayor eficiencia. La mayor densidad de potencia, combinada con un menor consumo de energía, también se traduce en diversas ventajas en el diseño del husillo. Los agujeros de eje, rodamientos de bolas y diámetros de eje más grandes, junto con ejes más cortos, dan como resultado un funcionamiento más suave. Además, el potencial resultante de la mejora de la rigidez dinámica y la capacidad de carga puede aprovecharse mediante interfaces de herramienta más grandes o velocidades máximas más elevadas. Como el rotor se calienta menos, hay menos desplazamiento térmico del eje y se necesita menos refrigeración. Esto reduce la cantidad de aire y aceite que necesita el husillo.
Además de la nueva serie de husillos, GMN también presentó su nueva unidad de lubricación Prelub GPi Plus para suministrar lubricante al husillo. Al igual que el propio husillo, incorpora la tecnología IloT ‘Integrated Data Evaluation and Acquisition for Spindles’, o IDEA-4S para abreviar. Durante el proceso, el husillo proporciona datos como la temperatura del rodamiento y del refrigerante, la velocidad, así como datos sobre las vibraciones y, opcionalmente, también sobre cualquier desalineación. La unidad de control de la máquina identifica el husillo mediante su placa de características digital, lee los datos relevantes para la lubricación y los transmite a la unidad de lubricación. De este modo, la lubricación del husillo puede automatizarse y controlarse en función de los parámetros de lubricación preestablecidos. Esto permite interrumpir el ciclo de lubricación, lo que ahorra lubricante en caso de parada del husillo. Además, la información disponible se utiliza para regular la ventilación y supervisar el suministro de aceite automáticamente.
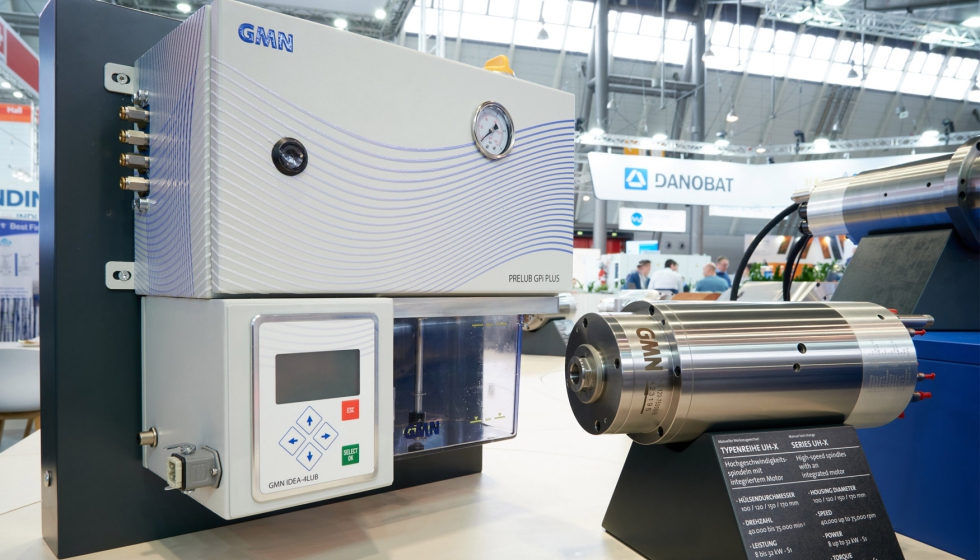
Mayor eficacia gracias a las nuevas generaciones de tecnología de husillos y periféricos de máquina. Foto: VDW/Nicholas Det.
La tecnología IloT subyacente es un sistema integrado desarrollado por GMN. El sistema de sensores del husillo determina continuamente los parámetros más importantes del proceso, que se envían bidireccionalmente en tiempo real a través de IO-Link al sistema de control de la máquina y a las redes de producción. Esto permite una optimización permanente de la implantación y reacciones rápidas ante evoluciones no deseadas. También permite la optimización integral de todos los procesos, lo que
a su vez mejora la eficacia de los componentes y minimiza el consumo de recursos. Además de la serie de husillos UH y la nueva generación de dispositivos de lubricación Prelub GPi Plus, GMN también presentó en GrindingHub su herramienta de cálculo en línea SpiOnline. Esta herramienta permite seleccionar la combinación óptima de herramienta y husillo para el proceso de rectificado correspondiente antes de proceder al mecanizado. No sólo es posible buscar una herramienta óptima para un husillo existente, sino que también se puede determinar el husillo adecuado para aplicaciones que requieren herramientas especiales. La selección de una herramienta óptima permite, por ejemplo, alcanzar un rango de velocidad específico y obtener resultados de mecanizado óptimos.
Los procesos de fabricación aditiva abren nuevas posibilidades de diseño para los abrasivos
Además de los conceptos de máquina, así como los husillos integrados y los sistemas de alimentación, la muela abrasiva es el elemento clave en los procesos de rectificado. Está en contacto directo con la pieza y tiene una gran influencia en el resultado del mecanizado y en la productividad del proceso. Por este motivo, los avances en el campo de las muelas abrasivas y su preparación para el proceso de rectificado se impulsan de forma continua.
La fabricación aditiva de abrasivos es actualmente un tema candente. El cuerpo básico de la herramienta, la muela abrasiva o ambos pueden producirse mediante procesos de fabricación aditiva. En comparación con los procesos de fabricación convencionales, los procesos de fabricación aditiva permiten una libertad de diseño significativamente mayor en cuanto a los componentes producidos. A diferencia de los procesos de fabricación con un filo de corte definido geométricamente, en los que es posible suministrar lubricante refrigerante a través de la herramienta cerca del punto de acción, esto suele asociarse a grandes retos en los procesos de rectificado. En este caso, los procesos de fabricación aditiva ofrecen la posibilidad de diseñar sistemas de muelas con un suministro interno de lubricante refrigerante.
3M presentó muelas abrasivas cerámicas CBN estructuradas del tipo 1PVP para procesos de rectificado cilíndrico interno. La acumulación adaptativa de capas finas crea estructuras impresas en 3D. Estas permiten una mayor libertad de diseño en comparación con las herramientas fabricadas convencionalmente, ya que no hay que tener en cuenta los límites del procesamiento mecánico. De este modo se pueden fabricar casi todas las formas y estructuras tridimensionales, ranuras y orificios de lubricante refrigerante. Además, las herramientas de fabricación aditiva presentan una distribución homogénea de granos y poros. Los grados de libertad en cuanto al diseño y el diseño específico asociado para la aplicación respectiva, así como las propiedades de los materiales de las herramientas de rectificado fabricadas aditivamente, significan que se puede lograr una mayor eficiencia y un potencial de rendimiento mejorado en comparación con las herramientas de rectificado convencionales.
Riegger Diamantwerkzeuge GmbH, de Affalterbach, presentó otro ejemplo de los avances actuales en la fabricación de recubrimientos para muelas abrasivas de fabricación aditiva. En el marco de un proyecto financiado por el Programa Central de Innovación para PYME (ZIM) del Ministerio Federal de Economía y Acción por el Clima, se están desarrollando enfoques para la producción de recubrimientos abrasivos para muelas de CBN y diamante de resina sintética mediante procesamiento digital de luz (DLP). Gracias a este proceso, se pueden crear perfiles de muelas abrasivas individuales cuyas dimensiones sólo están limitadas por las capacidades de la impresora 3D. La ventaja es que no se necesitan piezas mecanizadas, montaje manual ni rellenado del molde de la muela. Esto abre la posibilidad de ahorrar costes. Los retos actuales incluyen la producción de recubrimientos abrasivos homogéneos y altamente concentrados y la adición de aditivos para optimizar la unión. Además de los nuevos conceptos para la producción de muelas abrasivas, la preparación de la muela es un factor importante. La preparación de la muela da a la muela su contorno final, mientras que al romper los granos abrasivos del aglomerante se exponen nuevas partículas abrasivas y, por tanto, se crea la base para la topografía de la muela. En GrindingHub, numerosos fabricantes, como Cleveland, de Löffingen, y GWD Industrial, de Austria, presentaron enfoques convencionales para el reavivado de muelas abrasivas, por ejemplo, utilizando herramientas de reavivado de SiC o diamante. Estos procesos de reavivado de herramientas de rectificado pueden llevarse a cabo externa o internamente y, en muchos casos, requieren un proceso de afilado posterior para restablecer el aglomerante y aumentar el rendimiento de corte de la muela.
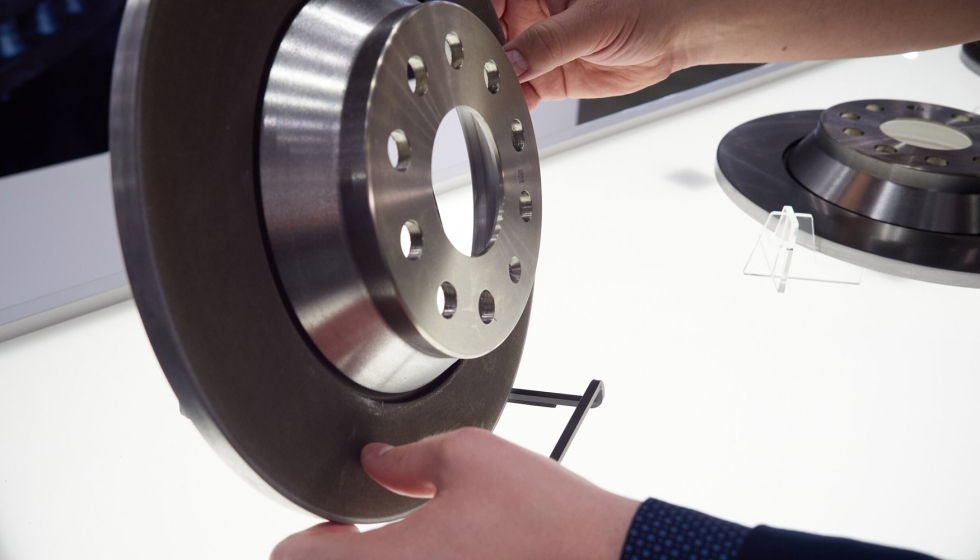
La producción de rotores de freno con revestimiento duro requiere soluciones innovadoras en la cadena de procesos. Foto: VDW/Nicholas Det.
Otro enfoque de la preparación de muelas abrasivas se basa en los procesos de erosión por chispas. En el caso de recubrimientos abrasivos con un componente de aglomerante conductor, el aglomerante se elimina en el arco sin afectar a las partículas abrasivas no conductoras. De este modo, la geometría del perfil y la topografía de la superficie de las muelas se crean sin contacto y, por tanto, sin fuerza. Entre otras, las ventajas de este proceso incluyen la posibilidad de producir geometrías que no pueden producirse con los procesos de reavivado convencionales, así como la generación de una protuberancia de grano significativamente mayor. El resultado es una topografía más favorable para el corte, que permite alcanzar mayores velocidades de arranque de material y alargar la vida útil de la muela. Tanto el fabricante japonés Mitsubishi Electric como la empresa Häberle de Laichingen expusieron máquinas de corte por hilo para preparar muelas abrasivas con sistemas de aglomerante conductivo. Häberle está realizando aquí una ampliación de eje basada en una máquina de erosión por hilo Robocut C400iC de la empresa japonesa Fanuc para permitir la erosión rotativa de muelas abrasivas. Häberle presentó una solución para el reavivado automatizado de muelas abrasivas bajo el nombre de producto Häberle Robocut Plus-Big-R. En combinación con una gran célula robotizada con el robot Fanuc M20, se almacenan nuevas piezas de trabajo y el robot Häberle Robocut 400 ROT de 6 ejes se carga y descarga automáticamente. La célula puede cargarse con nuevas piezas de trabajo en paralelo a la producción mediante una estación de preparación.
La automatización aumenta la productividad y ofrece respuestas a la escasez de trabajadores cualificados
Además, un amplio abanico de fabricantes presentó otras muchas técnicas/enfoques de automatización para una gran variedad de procesos. Häberle también presentó un enfoque para la alimentación de piezas en bruto como material a granel en GrindingHub. Estas se introducen sin clasificar a través de una cinta transportadora en la zona de trabajo de un robot. Se utilizan sistemas basados en cámaras para registrar la orientación de los componentes, evaluar esta información y transmitirla al robot. Basándose en la información de posición, el robot recoge los componentes de la cinta transportadora y los coloca en su dispositivo de sujeción. La cinta transportadora realiza movimientos de vaivén para cambiar la posición de los componentes en la cinta transportadora y permitir que el robot agarre todos los componentes. De este modo se elimina la necesidad de realizar otros pasos mecánicos del proceso para conseguir una orientación adecuada de los componentes. En el stand de United Grinding Group, de Berna (Suiza), se presentó ‘ATP - Automated Tool Production’, una solución de automatización para herramientas cilíndricas de precisión de Walter Maschinenbau GmbH, de Tubinga. Consta de al menos una célula robotizada accesible desde la parte delantera para la carga y descarga automáticas de las máquinas y al menos un robot móvil autónomo para transportar los palés de herramientas o piezas individuales entre las estaciones de procesamiento y almacenamiento. El sistema puede integrarse en los diseños de sistemas existentes y es apto para todas las máquinas de rectificado, medición y erosión de Walter. También puede servir de interfaz para máquinas de otros fabricantes. El robot de transporte retira el palet o la pieza individual de la estación de transferencia de la máquina respectiva y lo transporta a su destino correspondiente. Para ello se utiliza un sistema de control de datos y procesos de nivel superior, así como un modelo de comunicación estandarizado.
Las soluciones de automatización de este tipo son una forma de contrarrestar la escasez de trabajadores cualificados y, al mismo tiempo, aumentar la productividad. La automatización de procesos ofrece la posibilidad de mantener y ampliar los procesos de fabricación con una menor dependencia de la mano de obra disponible, especialmente en las áreas de manipulación de piezas de trabajo dentro de la máquina de procesamiento, así como la carga/descarga y el equipamiento de las máquinas.
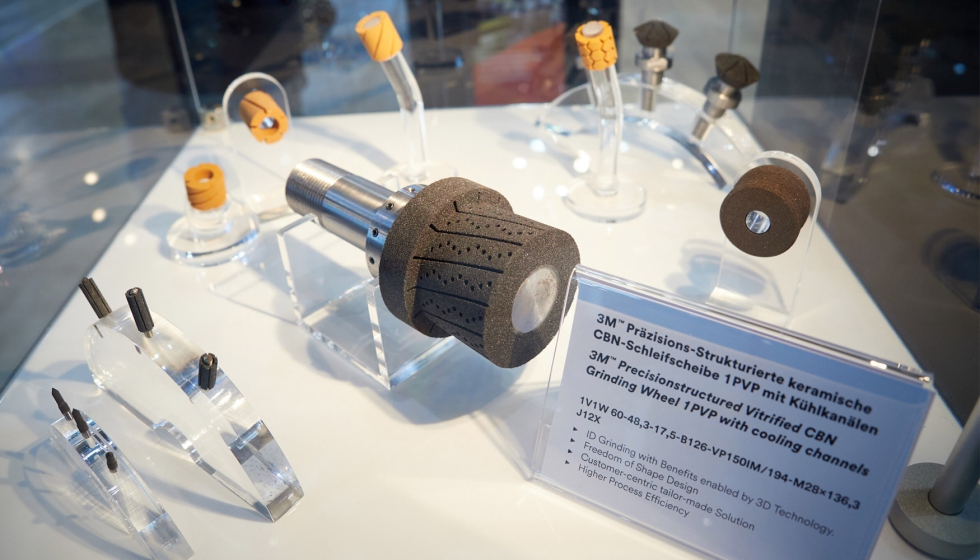
Ampliación de las opciones de diseño y aumento del potencial de rendimiento de los abrasivos gracias a la fabricación aditiva. Foto: VDW/Nicholas Det.
Herramientas de corte de alto rendimiento gracias a la modificación de bordes y superficies
La modificación de bordes y superficies representa un paso importante en la fabricación de herramientas con bordes de corte geométricamente definidos. Hay muchas razones para realizar estas modificaciones, pero su objetivo principal es mejorar el comportamiento durante el uso y aumentar la vida útil de las herramientas de corte. Se distingue entre los procesos de preparación de los filos de corte y los de modificación de las superficies funcionales. La modificación de superficies funcionales suele llevarse a cabo después de un proceso de rectificado para mejorar la adherencia del recubrimiento para el proceso de recubrimiento o después del proceso de recubrimiento como parte de un tratamiento posterior al recubrimiento. El tratamiento posterior al recubrimiento se lleva a cabo para reducir los defectos superficiales, como las gotas, y mejorar así la calidad de la superficie. La calidad superficial de las caras de corte puede influir en el arranque de viruta y, por tanto, también en la fiabilidad del proceso y la vida útil de la herramienta, especialmente en procesos de taladrado o perforación profunda. A menudo, las aristas de corte se preparan mediante redondeo. Esto sirve para reducir posibles defectos en la zona de las aristas afiladas y para aumentar la estabilidad de las aristas. El resultado es un efecto positivo en el comportamiento de desgaste de las herramientas y un aumento de su vida útil.
Un enfoque para el tratamiento de superficies y la preparación de filos de corte es el uso de procesos de acabado en barril. La tecnología de acabado en barril es un proceso nuevo. Las piezas de trabajo giratorias se introducen en un recipiente giratorio lleno de agente abrasivo o de pulido. Estos procesos ofrecen la ventaja de que incluso las geometrías pequeñas pueden procesarse por completo.
Basándose en esta tecnología, el fabricante australiano Anca presentó en GrindingHub su nueva máquina de acabado por corriente EPX-SF. Se trata de una máquina para la preparación de filos de corte y la modificación de superficies que puede integrarse en células automatizadas. Dispone de tres husillos y once ejes. Es capaz de reducir la rugosidad del filo a menos de 100 nm y ajustar los radios del filo a unos pocos micrómetros con un factor K controlable. Junto con el sistema de carga totalmente automático, la automatización permite preparar y modificar hasta 1.800 herramientas al día. La máquina también está equipada con una estación de limpieza de herramientas y sistemas de supervisión del proceso. Con ello se pretende garantizar una calidad constante de las herramientas ajustando continuamente el nivel de los medios.
Además de este nuevo proceso, también se mostraron métodos convencionales para redondear aristas de corte, como el cepillado. La empresa suiza Dynamic Finishing presentó una solución para la producción industrial de formas y superficies de filo de corte definidas que puede integrarse en la rectificadora. El proceso de cepillado se realiza en la rectificadora. GDS, de Ofterdingen, adopta un enfoque diferente. Aquí se presenta un proceso de cepillado controlado por robot para el redondeo selectivo del filo de corte de herramientas de mango y plaquitas indexables. Se trata de una célula robotizada con el nombre de Magicedge. En términos básicos, se utiliza un robot para cepillar la herramienta de forma dirigida. La cinemática del robot influye en la forma, el tamaño y el curso del redondeo de la arista de corte. A diferencia del acabado en tambor, los procesos de cepillado permiten preparar los bordes de corte y las zonas cercanas a los bordes de corte sin afectar a las zonas distantes. En la célula robotizada pueden implementarse otros requisitos específicos del cliente, como pick and place, granallado de perlas de vidrio, control de calidad y pulido.
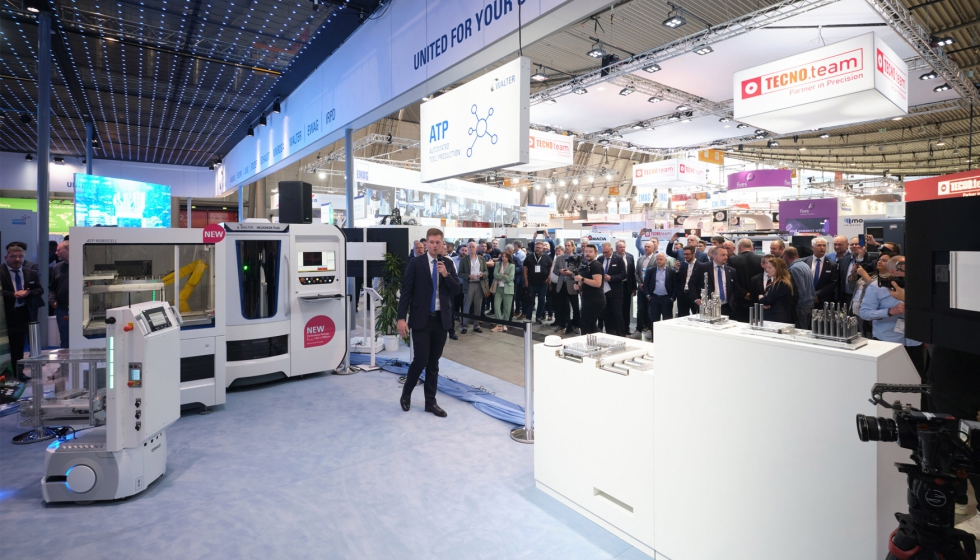
Las técnicas de automatización ofrecen la posibilidad de aumentar la productividad y contrarrestar la escasez de trabajadores cualificados. Foto: VDW/Nicholas Det.
Nagel de Nürtingen presentó un proceso similar en cooperación con Bruker Alicona de Austria bajo el nombre de NaPrep. Aquí también se prepara una herramienta robóticamente. Los bordes individuales se preparan selectivamente utilizando cepillos de procesamiento revestidos. A continuación, se realiza un proceso de pulido opcional. El proceso automatizado permite flexibilidad en cuanto a tipos de herramientas gracias a una estación de agarre, así como el funcionamiento sin personal del sistema. La integración de un sistema de medición permite realizar mediciones de las herramientas durante el proceso, lo que posibilita el ajuste autorregulado de los parámetros del proceso: un bucle cerrado. Aquí se utiliza un EdgeMaster de Bruker Alicona para medir la forma del filo de corte. Se trata de un dispositivo de medición óptico que, basado en la variación de enfoque y en combinación con el software de evaluación correspondiente, permite tanto la detección como la medición de los filos de corte y sus formas.
Control específico de procesos y componentes mediante sistemas de medición adecuados
Para registrar y evaluar los resultados de mecanizado de los procesos de fabricación se requieren mediciones durante y después del proceso. Además de la tecnología de medición para registrar las fuerzas o el comportamiento del proceso, los sistemas de medición se utilizan en particular para determinar las dimensiones, la posición y la forma, así como para analizar las propiedades de las superficies. Además del concepto para la preparación de filos de corte, Bruker Alicona presentó en GrindingHub su nuevo dispositivo de medición óptica FocusX. La medición sin contacto que ofrecen los dispositivos de medición óptica es una de las principales ventajas frente a los dispositivos de medición táctiles, ya que también es adecuada para analizar componentes sensibles. Por ejemplo, el proceso de medición debe descartar cualquier riesgo de alteración de la superficie de los componentes utilizados en tecnología médica. FocusX utiliza la Variación de Enfoque Avanzada, que se introdujo por primera vez con el dispositivo de medición óptica μCMM.
No solo es más rápida que la anterior tecnología de Variación de Enfoque, sino que también es especialmente adecuada para superficies lisas. Sin embargo, también se pueden detectar formas complejas, radios pequeños, ángulos agudos y flancos pronunciados hasta taladros con una relación diámetro-profundidad de 1:3 a 1:10. Los ejes de rotación e inclinación permiten medir componentes desde distintos ángulos y ensamblarlos en una imagen 3D mediante la integración de software adecuada. También pueden realizarse mediciones de rugosidad conformes a la norma ISO.
Los sistemas de medición externos ofrecen varias ventajas sobre los sistemas de medición internos de la máquina. Por ejemplo, el uso paralelo al tiempo principal o las condiciones de medición controladas pueden implementarse más fácilmente. En muchos casos, sin embargo, la medición en la máquina de procesamiento también puede ser un enfoque eficaz. Un ejemplo de ello es el Laser Contour Check, que Walter integra en sus rectificadoras y erosionadoras. Esto permite medir sin contacto diversos parámetros de cilíndricas sin contacto y, en caso necesario, corregir automáticamente el diámetro y el perfil de la herramienta. Diversos institutos de investigación del ámbito de la tecnología de producción presentaron en el GrindingSolutionPark los resultados de sus actuales proyectos de investigación. Dos proyectos del Instituto de Tecnología de Fabricación (MIT) de Aquisgrán son buenos ejemplos de ello. En el marco de un proyecto de investigación sobre el ‘Análisis de las condiciones tribológicas en el rectificado de diamante policristalino (PCD) con un lubricante refrigerante mezclado con agua’, se determinan mediante una gran variedad de ensayos de aplicación los parámetros que, a su vez, se utilizan para desarrollar leyes matemáticas de fricción para el contacto monograno y multigrano y para la simulación numérica del colectivo de cargas termomecánicas. En un paso posterior, se deriva de ello un modelo explicativo para el rectificado de PCD con un lubricante refrigerante mezclado con agua.
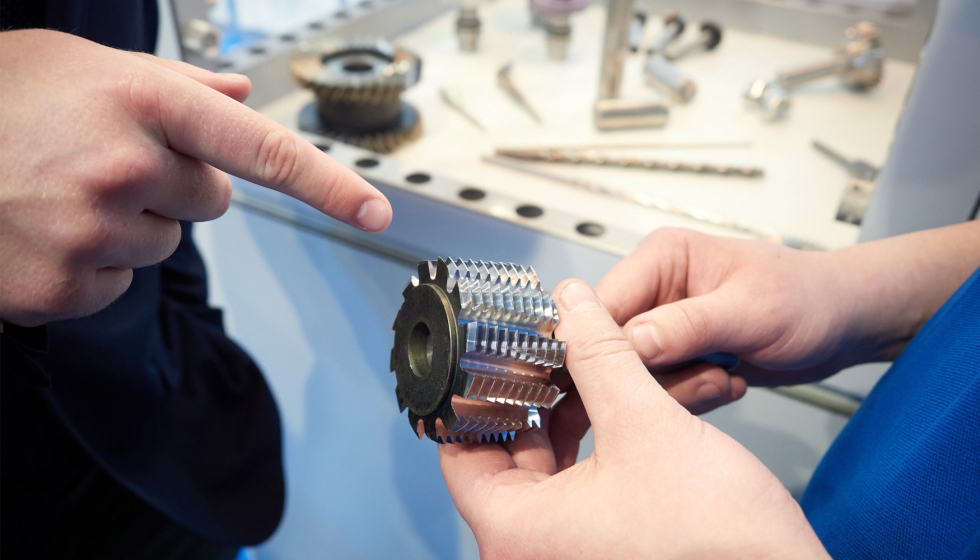
Las soluciones de software permiten una producción más eficiente de herramientas de corte complejas. Foto: VDW/Nicholas Det.
El segundo proyecto se centra en las ‘Investigaciones de las tensiones termo-mecánicas-químicas durante el rectificado transversal circunferencial externo de 100Cr6’. Este material se utiliza con frecuencia en rodamientos de rodillos, que están sujetos a requisitos cada vez más estrictos debido al cambio hacia la electromovilidad. Según las pruebas realizadas hasta la fecha, el control selectivo del proceso de rectificado debería favorecer la formación de una capa límite inicial en las superficies de los rodamientos. El objetivo es aumentar la protección contra el desgaste y reducir la cantidad de rodaje necesaria para formar una capa de protección contra el desgaste inducida por aditivos. El Instituto de Ingeniería de Producción y Máquinas-Herramienta (IFW) de Hannover presentó ‘Métodos de análisis en la producción de herramientas de rectificado’. Aquí se realizan, por ejemplo, ensayos de flexión, mediciones de dureza, análisis de fases, mediciones de densidad, imágenes topográficas de superficies, ensayos de rayado y cizallamiento de grano único, así como exámenes con microscopio electrónico de barrido en el ámbito de la caracterización de aglomerantes, granos y poros. El proyecto ‘Evaluación in situ del estado de tensión residual en el proceso de rectificado de engranajes: An Artificial Intelligence Approach’ del IWF de Berlín describe un enfoque para evaluar las tensiones residuales en componentes basado en métodos de la Industria 4.0. Para ello, se llevan a cabo procesos de rectificado con tecnología de medición en proceso, seguidos de mediciones de tensión residual. Los datos recopilados sirven como variables de entrada para una red de IA. De este modo, debería ser posible realizar predicciones sobre el estado de la tensión residual en procesos de rectificado posteriores sin tener que realizar nuevas mediciones de tensión residual. El Instituto de Tecnología de Mecanizado (ISF) de Dortmund presentó los actuales “Desarrollos tecnológicos de rectificado en la cadena de procesos aditivo-sustractivo”. Las posibilidades del postprocesado, a menudo necesario, de componentes impresos de componentes impresos aditivamente mediante rectificado, microacabado y chorreado en húmedo, al tiempo que se desarrollan enfoques para el control de procesos específicos de los respectivos procesos para el postprocesado de componentes impresos aditivamente.
En el Startup Hub, jóvenes empresas expusieron sus conocimientos y servicios. Weber Technologies, de Potsdam, presentó recubrimientos de diamante para herramientas de carburo de precisión. Los recubrimientos de diamante WT-DIA se utilizan para el mecanizado de diversos materiales, como CFK, GFK, CFK/material sándwich de Al, cerámica, grafito y materiales de aleación de Al, y mejoran potencialmente el rendimiento de las herramientas. El recubrimiento se lleva a cabo mediante el proceso CVD de hilo caliente. Los gases del proceso se introducen en la cámara se introducen en la cámara de recubrimiento al vacío y se descomponen a alta temperatura. Los átomos de carbono liberados se acumulan en la superficie del sustrato, de modo que durante el proceso de recubrimiento crece una capa cristalina de diamante. La capa puede construirse en el rango microcristalino y nanocristalino, así como con una estructura graduada en un grosor de 3 a 20 μm.
Afrontar los retos actuales con innovaciones
GrindingHub 2024 se centró especialmente en la automatización y digitalización de los procesos de fabricación. Al fin y al cabo, estos pueden ayudar a contrarrestar la actual escasez de trabajadores cualificados y, al mismo tiempo, aumentar la productividad. Se mostraron numerosas mejoras detalladas para aumentar la eficiencia de diversos componentes, sus periféricos y las herramientas de rectificado utilizadas como forma de contrarrestar los problemas asociados a la escasez de trabajadores cualificados, la presión de los costes y el deseo de crear procesos y productos sostenibles. Ejemplos de ello son las herramientas de rectificado impresas aditivamente y las mejoras de eficiencia en la tecnología de husillos. Los procesos de la tecnología de rectificado son extremadamente importantes en el contexto de la transición hacia modos de transporte más ecológicos y el objetivo de lograr finalmente una movilidad neutra en emisiones. Además de los nuevos conceptos de propulsión, la atención se centrará también en los sistemas de freno de bajas emisiones y su producción. El rectificado de rotores de freno con revestimiento duro es un sector en expansión que requiere amplias innovaciones en cuanto a rectificadoras, herramientas de rectificado y control de procesos.