DQBD revoluciona el sillín de ciclismo con la impresora 3D Stratasys H350
La galardonada empresa de diseño alemana DQBD GmbH está aprovechando la impresora 3D Stratasys H350 para producir sillines de ciclismo totalmente personalizados que ofrecen un mayor nivel de comodidad y eficiencia de rendimiento en comparación con las versiones normales. DQBD está fabricando de forma aditiva varias de las piezas de carga del sillín a escala, ahorrando miles de euros en costes y reduciendo los plazos de entrega de meses a solo varios días en comparación con los métodos de moldeado tradicionales.
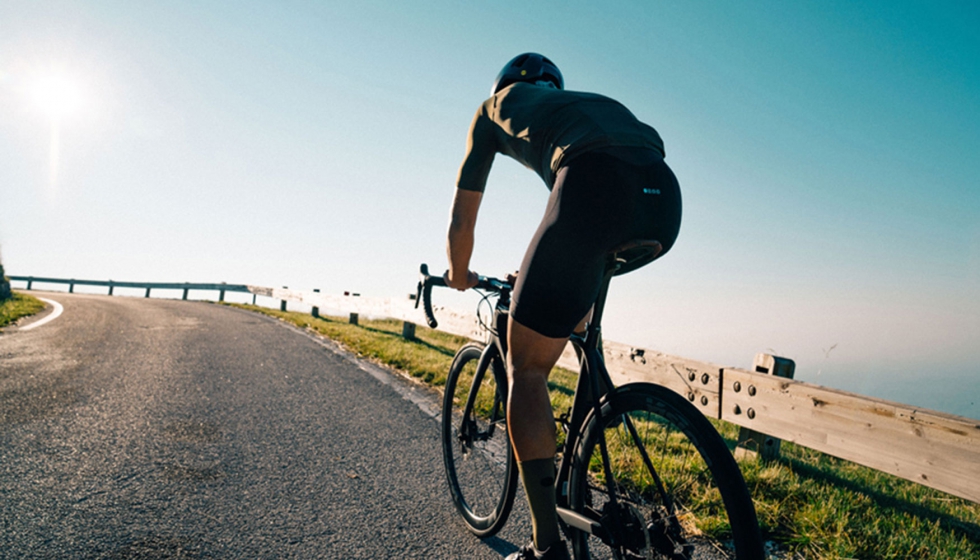
DQBD se ha consolidado como un sólido socio de diseño y desarrollo para muchas grandes marcas mundiales. La impresora 3D H350, con tecnología SAF, proporciona a la empresa la flexibilidad de diseño y la calidad de producción que necesitaba para hacer realidad su visión de un sillín de ciclismo completamente personalizado. También ofrece una alta repetibilidad a escala de producción, a la vez que impulsa la eficiencia en tiempo y costes.
“Siempre habíamos previsto que la AM desempeñara un papel fundamental en la creación de SAM, nuestro sillín de ciclismo”, afirma Sebastian Hess, director general de DQBD. “De hecho, diseñamos el sillín pensando en la fabricación aditiva. Además de ofrecer piezas precisas y de calidad de producción en volumen de forma rápida y asequible, la tecnología ofrece una oportunidad única de personalizar los productos de una forma que no puede reproducirse con los métodos tradicionales”.
“Al utilizar el H350, hemos observado un ahorro de costes en todo el proceso de desarrollo del producto de hasta 22.000 libras esterlinas (25.868€, aproximadamente) en comparación con los métodos de moldeo por inyección, ya que eliminamos por completo los costes de utillaje”, explica Hess. “También hemos acortado nuestros plazos de entrega a unos 10 días en comparación con los 3-6 meses que puede llevar la fabricación tradicional”.
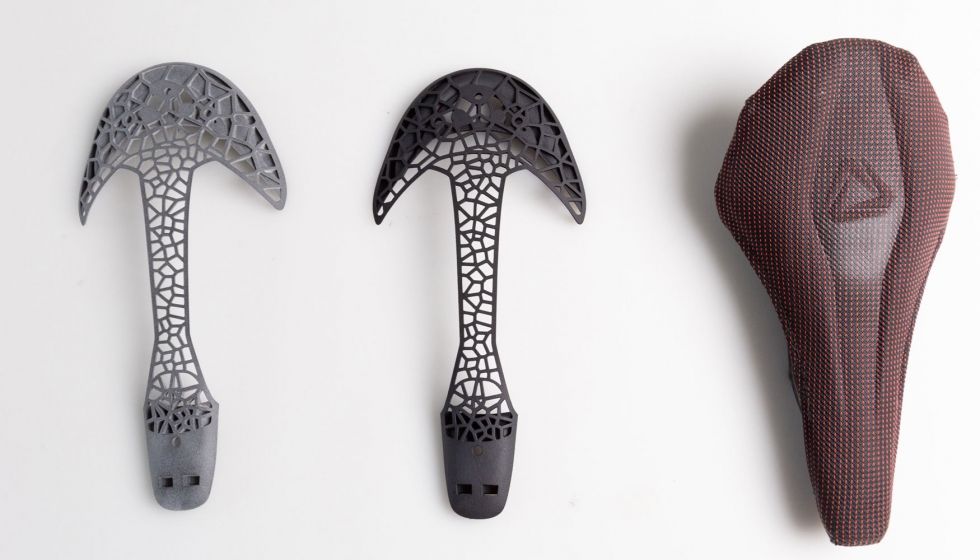
SAM – saddle additive manufacturing (fabricación aditiva de sillines)
“Sometimos el sillín a rigurosas pruebas que incluían la resistencia a los impactos, la presión y la fatiga para asegurarnos de que cumplía los estándares de la industria y nuestras propias expectativas”, afirma Hess. “El material PA11 de la H350 encajaba a la perfección con las piezas fabricadas de forma aditiva, ya que nos ofrece una gran ductilidad, un alto impacto y una gran resistencia a la fatiga, lo que era esencial para nuestro diseño”.
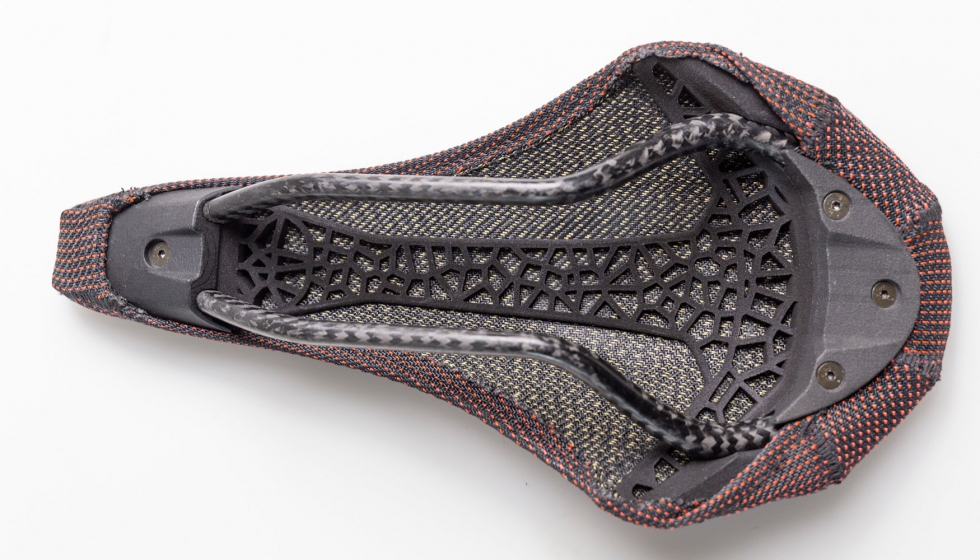
La sostenibilidad fue una consideración clave en el diseño. Todo el conjunto del sillín no tiene cola y, al final de la vida útil del producto, los componentes pueden separarse fácilmente y reintroducirse en la producción. El material Stratasys High Yield PA11 es un plástico de base biológica fabricado con una materia prima renovable derivada del aceite de ricino cultivado de forma sostenible.
“La consistencia y la precisión de alta calidad de la impresora 3D H350 ha hecho realidad la idea de la personalización a escala y nos permite llevar el ciclismo a un nuevo nivel”, comenta Hess. “Ahora podemos crear un sillín que maximiza el rendimiento a escala de cada ciclista, al tiempo que mejora la comodidad. De hecho, la comodidad que proporciona hace innecesario el acolchado de los culottes, lo que redunda en una mayor reducción de peso”.
Yann Rageul, director de la unidad de negocio de Fabricación para EMEA y Asia de Stratasys, añade: “Estamos viendo una tendencia definitiva en la preparación de las empresas para la producción en volumen de piezas de uso final. DQBD está mostrando cómo la H350 y su tecnología SAF no sólo pueden optimizar todo el proceso de producción con un valioso ahorro de tiempo y costes, sino que también muestra el despliegue de la AM para diseños verdaderamente únicos y avanzados, listos para la producción a escala. Estamos orgullosos de ver que el diseño del sillín SAM creado por DQBD muestra los avances de la fabricación aditiva dentro del ciclo de desarrollo del producto - ya que el concepto del producto fue diseñado en torno a la AM desde el principio”.