Lortek y Euskabea desarrollan un sistema para la fabricación aditiva de composites termoestables
El proyecto AM-AVANZA (acrónimo de nuevos procesos de Additive Manufacturing eficientes para el diseño de estructuras singulares mediante la utilización de materiales AVANZAdos), liderado por la División de Tecnologías de la Construcción de Tecnalia, se ha basado en el desarrollo de técnicas de fabricación aditiva (Additive Manufacturing en inglés (AM) o comúnmente Impresión-3D), con materiales avanzados basados en composites termoestables.
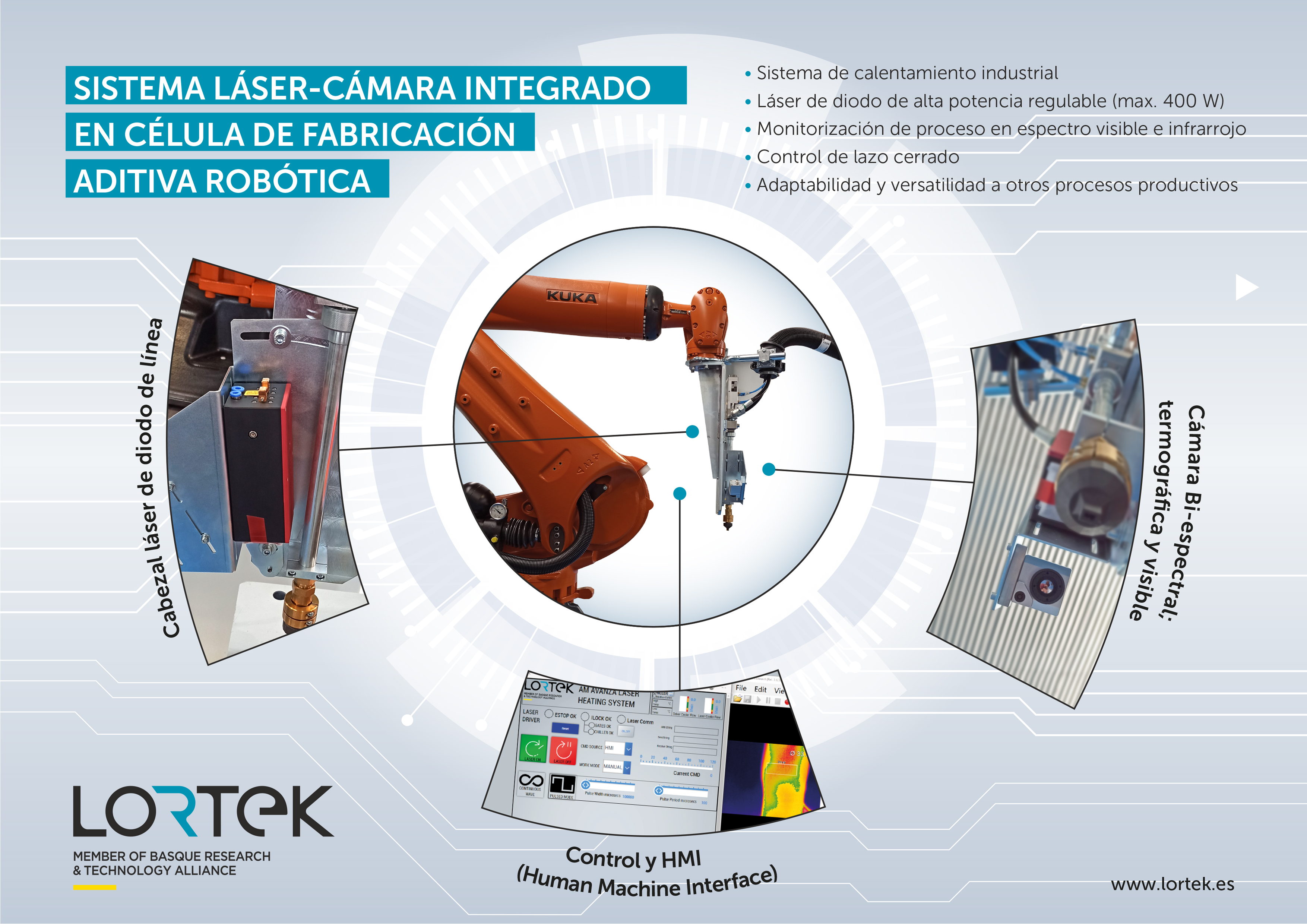
La impresión 3D o AM es una técnica de fabricación con interés creciente en sectores donde la creación de productos customizados, relativos al aspecto estético y la personalización, son el gran elemento diferenciador. Sectores como la automoción, el ferroviario, el naval y la arquitectura demandan cada vez más este tipo de estructuras personalizadas, pero la forma, el gran tamaño y las necesidades estructurales de sus productos hacen que las tecnologías y materiales actuales no permitan ser fabricados por impresión 3D.
Para responder a este reto, uno de los saltos tecnológicos cualitativos del proyecto ha sido el desarrollo de materiales avanzados basados en composites termoestables. Aunque estos materiales ya son utilizados en procesos de fabricación para aeronáutica, automoción o naval, todavía no existía tecnología para ser aplicados mediante fabricación aditiva.
Uno de los puntos clave de cualquier proceso de AM es conseguir el pegado de las sucesivas capas aplicadas o la adhesión layer-by-layer. Los composites termoestables no son ajenos a este proceso y, teniendo en cuenta que el objetivo final de AM-AVANZA es fabricar piezas de gran tamaño, será fundamental que las capas sucesivas superpuestas se adicionen y peguen adecuadamente con las inferiores sin que la estructura tridimensional completa sufra colapso y se desmorone.
Los composites termoestables se basan en la combinación de dos materiales en estado semi-líquido o viscoso; una resina termoestable y una serie de fibras o reforzamientos. En el momento de su mezcla comienza una reacción exotérmica la cual, pasado un tiempo determinado (tiempo de curado), pasa de ese estado viscoso a un endurecimiento completo, consiguiendo unas prestaciones mecánicas únicas. Este proceso de curado no ocurre de forma instantánea, por lo que la fabricación de grandes piezas requerirá de un calentamiento capaz de activar y acelerar ese proceso de forma eficiente y efectiva.
Para conseguir este objetivo Lortek, centro tecnológico experto en digitalización y monitorización de procesos y fabricación aditiva por tecnología láser, y Euskabea empresa líder en el desarrollo de soluciones integrales de electricidad y control, han desarrollado un sistema de calentamiento controlado para composites termoestables basado en tecnología láser. La radicación láser es capaz de excitar el material compuesto y calentarlo de forma selectiva, acelerando el proceso de curado. Este proceso calentamiento-curado dependerá de la potencia láser aplicada, por lo que es necesario medir la temperatura alcanzada por el material y controlar, en consecuencia, la potencia suministrada por el láser.
Con estas premisas, se ha diseñado e integrado un sistema basado un cabezal láser de diodo de línea (21 mm de ancho x 5 mm de largo) emitiendo a 808 nm (longitud de onda de alta eficiencia absortiva en composites termoestables) con una potencia de salida variable (MAX. 400 W) que permite el calentamiento eficiente a altas velocidades de fabricación (3000 mm/min). La monitorización y medición de la temperatura alcanzada por el composite se realiza por medio de una cámara termográfica infrarroja (7.5 … 13 µm), de alta precisión (160 x 120 px) y velocidad de adquisición (128 Hz) con rango de medición adaptable (-20 … + 100 °C / 0 … + 250 °C) que integra además una pequeña cámara visible que permite evaluar fenómeno del proceso identificables por técnicas de visión artificial.
El sistema ha conseguido resultados exitosos en el calentamiento eficiente de cordones de 1 y 2 mm de espesor con velocidades de trabajo cercanas a las reales (2000 mm/min) con potencias láser medias (200 W), lo que indica márgenes de mejora en la performance global del sistema.
Más allá de las aplicaciones para materiales plásticos termoestables, este sistema de calentamiento controlado tiene gran potencial para otro tipo de aplicaciones, como puede ser la termografía activa para metales, donde es necesaria una fuente de excitación externa que caliente el material de forma controlada a una determinada temperatura.