Innomia utiliza la tecnología EOS para optimizar la fabricación de componentes de automoción
Uno de los sectores en los que opera la empresa Innomia a.s., con sede en la República Checa, es el sector de la automoción. La compañía se ha convertido en una gran defensora de los beneficios de la Sinterización Láser Directa de Metales (DMLS). Su cartera abarca la construcción de prototipos, la fabricación de insertos para moldes de inyección y herramientas de fundición, la reparación de herramientas y mucho más. Con la ayuda de la tecnología EOS, los profesionales del DMLS han apoyado al proveedor automotriz Magna en la optimización del proceso de producción de piezas de plástico moldeadas por inyección. Esto implicó una revisión del proceso de enfriamiento. El caso se refiere a la fabricación del reposabrazos situado entre los asientos delanteros.
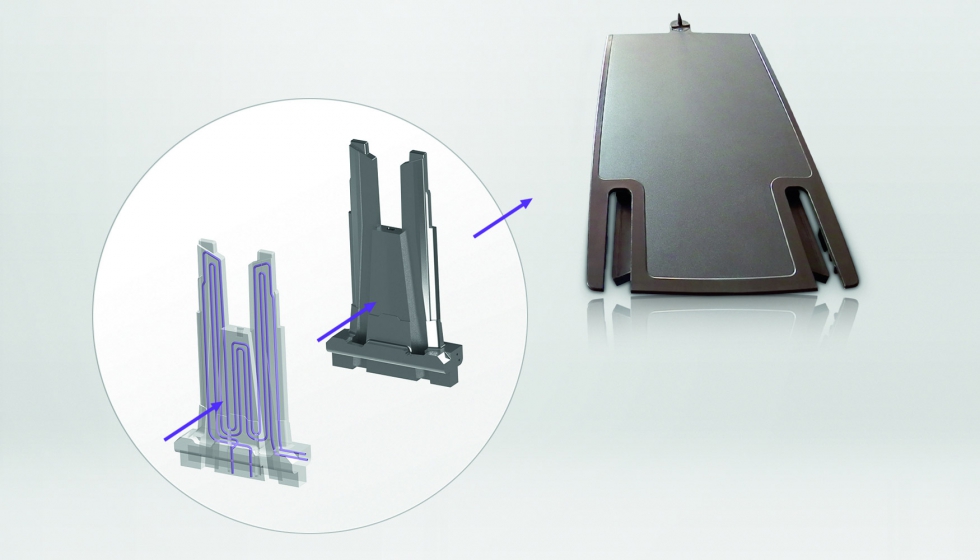
Inserto de herramientas fabricado con tecnología aditiva: el uso de la tecnología EOS contribuyó a prolongar el intervalo de mantenimiento y resolvió el problema de la condensación de la humedad del aire y la posible corrosión de la cavidad. Foto: Innomia.
Desafío: optimizar el proceso de enfriamiento para la fabricación de apoyabrazos para la construcción de automóviles. Reducir el período del ciclo de producción, mejorar la calidad de los componentes y aumentar los intervalos de mantenimiento.
Solución: construcción de canales de refrigeración de precisión en el molde de inyección y fabricación del núcleo optimizado con la EOSINT M 270.
Resultados:
- Fiabilidad: el mantenimiento de la planta de producción se extiende de cada dos semanas a cada cinco o seis.
- Calidad: el enfriamiento uniforme evita la deformación del producto final de plástico
- Reducción de costos: los costos se reducen a través de una reducción del 17% en los tiempos de ciclo de los moldes de inyección de plástico.
Desafío
La fabricación de los componentes de plástico para el reposabrazos central es realizada por el proveedor Magna, un cliente de Innomia. La producción se basa en un proceso clásico de moldeo por inyección. Se trata de plástico fundido lleno de fibras de vidrio, inyectado en la cavidad del molde y luego solidificado. El componente se puede desmontar posteriormente y está listo para su entrega al fabricante de automóviles o a otros proveedores de la cadena. Demasiado para la versión simplificada. En realidad, se trata de un proceso complejo en el que cada paso debe funcionar perfectamente.
La energía calorífica del material base líquido necesita ser disipada a través de la herramienta de fabricación para permitir que el plástico se solidifique. El proceso de enfriamiento dicta, entre otras cosas, la calidad del componente. Esto se debe a que la disipación irregular del calor puede provocar deformaciones. Además, el control de la temperatura juega un papel importante en la determinación de la duración del ciclo de producción. Cuanto antes se elimine el calor, antes se podrá extraer un componente y se producirá el siguiente.
El inserto para herramientas utilizado hasta la fecha se ha fabricado con una aleación de berilio-cobre que conduce el calor y sólo se podía enfriar desde un lado del inserto. Esto significaba que la distribución de la temperatura era desigual. El agua de refrigeración tenía que estar muy fría, a sólo 16 °C, para absorber el nivel de energía térmica. A través de las altas temperaturas de la superficie del inserto —hasta 120°C— la humedad subió en las inmediaciones, lo que, a su vez, aceleró la corrosión. Esto resultó en una limpieza intensiva y costosa que era necesaria cada una o dos semanas. La dureza del núcleo del molde fue todo lo que previno el daño de las superficies durante el proceso de limpieza regular.
Solución
Como consecuencia lógica, los diseñadores de Innomia comenzaron a desarrollar un nuevo sistema de enfriamiento de insertos de herramientas. La eliminación optimizada del calor generado en el proceso de producción ocupaba el primer lugar de la lista de prioridades. El equipo decidió optar por canales integrados de refrigeración de precisión, una aplicación probada y comprobada bajo la tecnología DMLS, y una de las soluciones que sólo los procesos de fabricación aditiva pueden ofrecer. El EOSINT M 270, un sistema probado durante muchos años, fue desplegado para Innomia.
El diámetro de los canales de refrigeración es de sólo 3 mm. El metal elegido fue Maraging Steel 1.2709. El proceso de fabricación —la aplicación por capas y la fusión del polvo metálico correspondiente a los datos 3D— permitió a los empleados de los especialistas checos aumentar el grado de dureza a más de 50 HRC a través del tratamiento posterior. Estas características mecánicas garantizan una alta resistencia al desgaste y reducen los costes de mantenimiento.
“El proceso DMLS, que utiliza la EOSINT M 270, nos ha permitido fabricar un componente extremadamente duradero, manteniendo al mismo tiempo con éxito las ventajas probadas del método en términos de diseño y reducción de los tiempos de ciclo”, explica Luboš Rozkošný, CEO de Innomia. “Gracias a los canales de refrigeración, integrados en el componente con una precisión óptima, hemos resuelto el principal reto del proceso de producción, y lo hemos hecho con un coste limitado”.
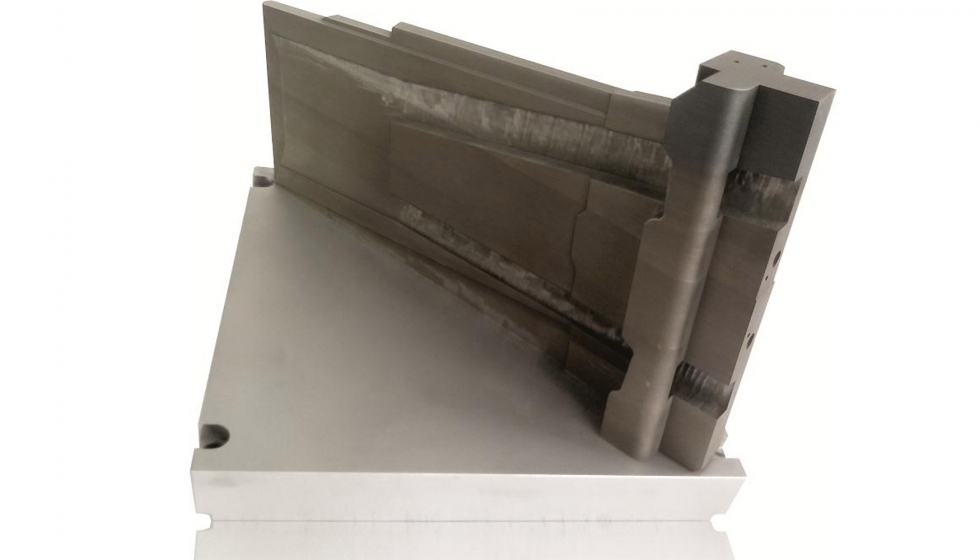
Resultados
El enfriamiento de precisión y la producción con tecnología de fabricación aditiva ha tenido los resultados deseados. La distribución de la temperatura y la disipación de calor asociada son ahora sustancialmente más homogéneas. Dado que el calor se distribuye y deja más rápido tanto la herramienta como el componente, una temperatura del agua de 60 °C es suficiente para refrigerar, lo que reduce la energía necesaria. La superficie del inserto no se calienta más allá de los 90 °C, lo que permitió a los ingenieros resolver los problemas de humedad en el área circundante.
Gracias a la tecnología de Innomia y EOS, Magna se beneficia de un intervalo de mantenimiento que se extiende entre cinco y seis semanas. El problema de la condensación de la humedad del aire y la posible corrosión de las cavidades fue resuelto completamente. Los canales de enfriamiento uniformes funcionan tan bien que el tiempo requerido para el ciclo de producción es ahora un 17% menor que antes. Gracias a la distribución y disipación uniforme y rápida del calor, los componentes ya no se deforman. Esto tiene una influencia directa y positiva en la calidad y rapidez de la fabricación. La reducción del tiempo del ciclo de producción y la mejora de la calidad del producto final son beneficios simultáneos. Después de 370.000 ciclos, Innomia y Magna han mejorado aún más los resultados. En este periodo el ahorro total ya ha alcanzado los 20.000 euros.
Pavel Strnadek, jefe de Mantenimiento de Herramientas de Magna, también se muestra satisfecho con los resultados: “El tema de la refrigeración es algo que hemos estado tratando de resolver durante mucho tiempo. Sabíamos cómo tendría que verse el producto animado, pero no era posible fabricarlo. La fabricación aditiva nos permitió hacer el gran avance. Pudimos planear los canales de enfriamiento tal como lo deseábamos y luego fabricar el núcleo del molde en consecuencia. El láser fusiona el polvo metálico capa por capa, de modo que en efecto cualquier forma es posible. El resultado nos ha convencido a todos los niveles. Mantenimiento, calidad del producto final, costos, disipación de calor. Ha sido el proyecto perfecto”.
“La industria del automóvil en Europa está sujeta a una fuerte competencia. Naturalmente, este hecho afecta a proveedores como Magna. Por eso es muy importante para nosotros poder producir con los más altos estándares de calidad al menor precio. Con la optimización de nuestra planta de producción a través de la refrigeración mejorada de nuestras herramientas, hemos creado un ejemplo de libro de texto de cómo la tecnología puede ayudar a aumentar la eficiencia. Hemos reducido los costes de mantenimiento de nuestra planta de producción, optimizado la calidad de nuestros componentes y aumentado el número de ciclos de producción. Esto nos permitió mantener la promesa de calidad que hicimos a nuestro cliente y, al mismo tiempo, satisfacer nuestras propias altas exigencias en cuanto a rentabilidad”, concluye Luboš Rozkošný, director general de Innomia.