Entrevista a Alberto Ruiz de Olano, CTO y cofundador de Optimus 3D
“Podemos imprimir cualquier pieza que imagines en diferentes materiales plásticos y metálicos”, sentencia la página web de Optimus 3D, rematándolo con un “Si se puede diseñar lo podemos fabricar”. Lo cierto es que esta empresa alavesa, especializada en el diseño e impresión de prototipos y piezas mediante tecnologías de fabricación aditiva, ha sabido adaptarse a los retos que un sistema de fabricación tan disruptivo le ha planteado desde que apostó por él hace ya cuatro años. Está en pleno plan de expansión tanto tecnológica, con la adquisición de nuevos equipos, y comercial, apuntando su mercado más arriba de los Pirineos.
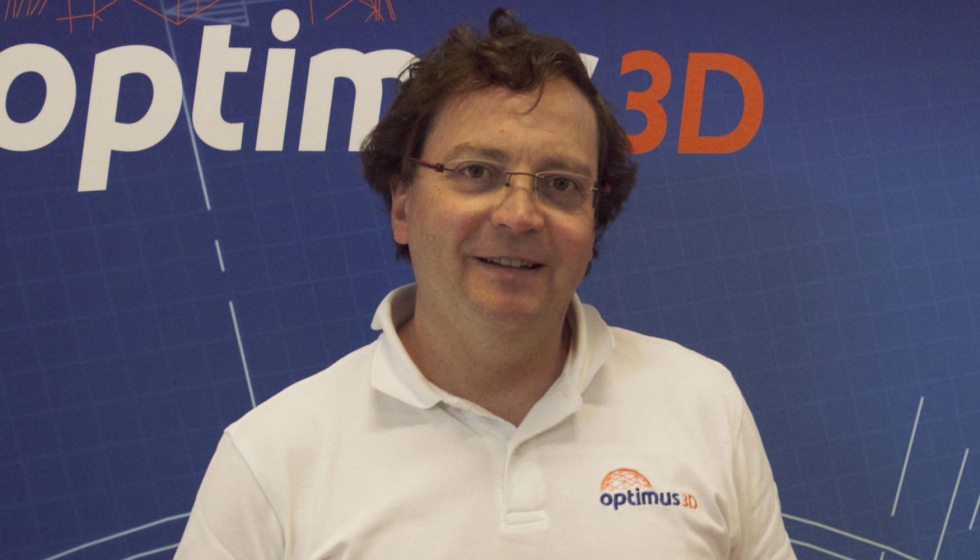
Cuéntenos un poco sobre Optimus 3D…
Hace ya cuatro años decidimos dar soluciones nuevas a los retos que nos encontrábamos en las empresas, como era la reducción de los ciclos de nuevos diseños y la búsqueda de nuevos procesos para reducir costes durante todo el ciclo de vida de producto. Descubrimos que la fabricación aditiva había dado el salto del laboratorio a convertirse en un proceso industrial y decidimos apostar por ello. Inicialmente sólo los socios promotores, descubriendo las 15 diferentes tecnologías que se agrupan bajo el término ‘3D printing’, y más tarde valorando los sistemas que hay en el mercado y que cumplen los estándar en el sector industrial. Nuestro objetivo hoy es ayudar a dar soluciones a nuestros clientes, donde la fabricación aditiva les permite ser más competitivos, imprimiendo un nuevo diseño de radiador en acero en 2 días, diseñando un utillaje ergonómico, ligero y en horas, o ayudando a un equipo médico a tomar decisiones quirúrgicas con la reproducción de un TAC de paciente. Actualmente no hay sector de actividad que monopolice esta tecnología sino que encontramos aplicaciones en todos, y el conocimiento de un sector se transfiere al resto. Desde el año pasado hemos empezado a incorporar ingenieros que debemos formar, y durante este año esperamos llegar a ser 6 personas en plantilla.
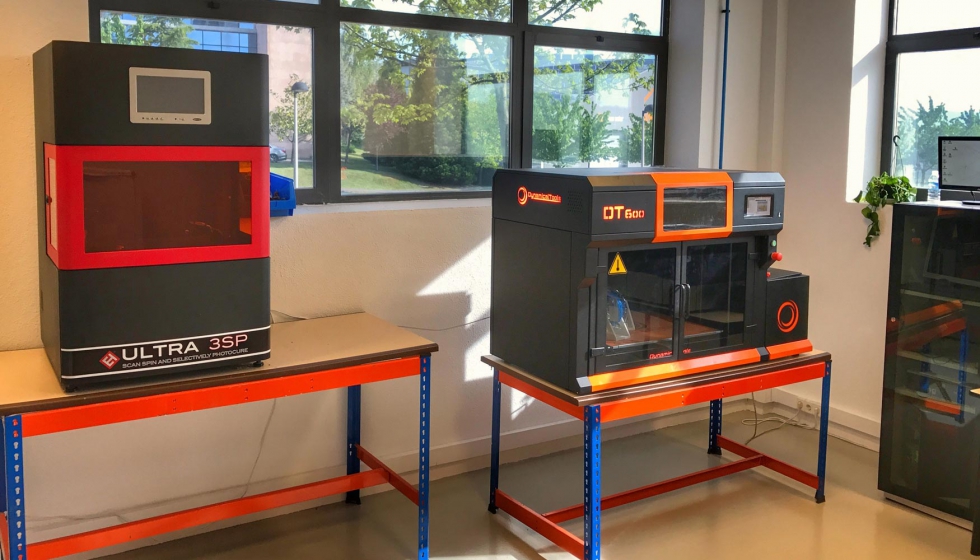
¿Qué servicios ofrecen?
Aportamos soluciones completas, desde el diseño y validación del nuevo concepto, hasta la fabricación. La fabricación aditiva y el conocimiento de su potencialidad permite un cambio en el paradigma del inventor. La forma queda supeditada a la función que debe ejercer; ya no diseñamos pensando en cómo fabricar. Las piezas suelen ser más caras que las tradicionales, pero si sumamos los costes de moldes, utillajes y herramientas necesarias pasa a ser una fracción del mismo.
¿Hacia qué sectores se dirige su actividad?¿Quiere destacar alguna empresa cliente que haya contado con sus servicios?
En el estudio de mercado con el que iniciamos la actividad advertimos que el sector era muy incipiente en el área del sur de Europa, en contraposición con el grado de uso en la zona Centro, sobre todo Reino Unido y Alemania. Actualmente podemos decir que somos una empresa transversal, puesto que tenemos clientes desde la educación y sanidad como Osakidetza, hasta en el sector aeroespacial como Airbus D&S, pasando por las industrias pequeñas y grandes tipo Daimler.
¿En qué se basa su ‘know how’?
Nuestro conocimiento se complementa de los más de 40 años que acumulamos los promotores en empresas multinacionales conociendo sus estándares, los más de 4 años visitando ferias para conseguir lo último de la tecnología y el conocimiento que hemos generado de las aplicaciones de esta nueva herramienta, que ha llegado para quedarse.
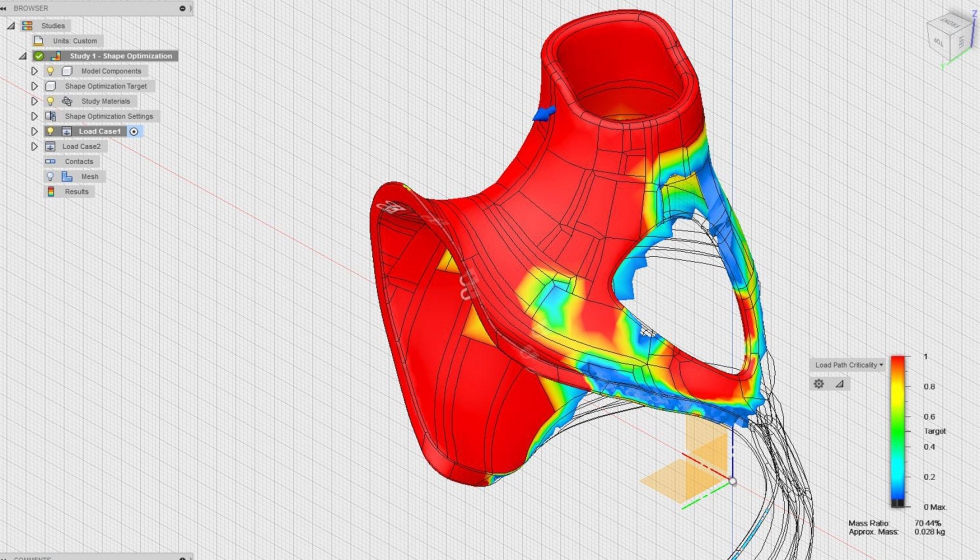
Diseño de Optimus3D de una pieza de órtesis para su impresión en 3D.
¿Con qué tecnologías de fabricación aditiva cuentan?
Actualmente tenemos 4 estaciones de diseño con software de Autodesk Fusion, que nos permite poder leer casi todos los formatos de geometría que nos envían, además de poder realizar estudios de FEM y optimizaciones topológicas para reducción de material no necesario. Disponemos de maquinaria industrial de Stratasys en tecnología de resina fotocurable por UV Poly-jet y de filamento FDM capaz de imprimir en Nylon, PC y Ultem, imprescindible en el sector aeronáutico. También disponemos de tecnología SLA, resina fotocurable mediante láser de la empresa Envisiontec. Para poder testear filamentos alternativos, como poliamida+fibra carbono o PET reciclado, disponemos de una máquina de gran formato DT600, y para este verano dispondremos de la primera máquina en el país vasco de HP de tecnología Jet Fusion.
Sobre la HP Jet Fusion 4200, ¿qué les aportará esta nueva máquina?
La fabricación aditiva no es un único proceso y nuestra vocación de dar soluciones nos dirige a tener en casa las más competitivas y usadas. El sector de poliamida sinterizada, donde el acabado de las piezas rivaliza con las de molde de inyección, se nos escapaba actualmente por el alto precio de los equipos. La incorporación de SPRI como socio nos permite poder adquirir este nuevo equipo, respaldado por la unidad mundial de aditivo del grupo HP situada en Barcelona.
Optimus3D tiene además planes de expansión hacia nuevos nichos de mercado e internacionalizar su empresa. ¿Nos puede contar un poco más sobre estos planes?
La constante vigilancia de la tecnología y los negocios relacionados con la fabricación aditiva nos está dando mensajes de por dónde va el mercado, que según las 4 mayores consultoras tecnológicas mundiales tendrá un crecimiento anual entre el 15 y 20% los próximos 3 años, y son el sector de series pequeñas/medias de inyección, utillajes y ayudas al montaje, y el aeronáutico. Desde hace unos meses trabajamos con un delegado comercial para Francia y queremos ampliar nuestra presencia en Alemania.
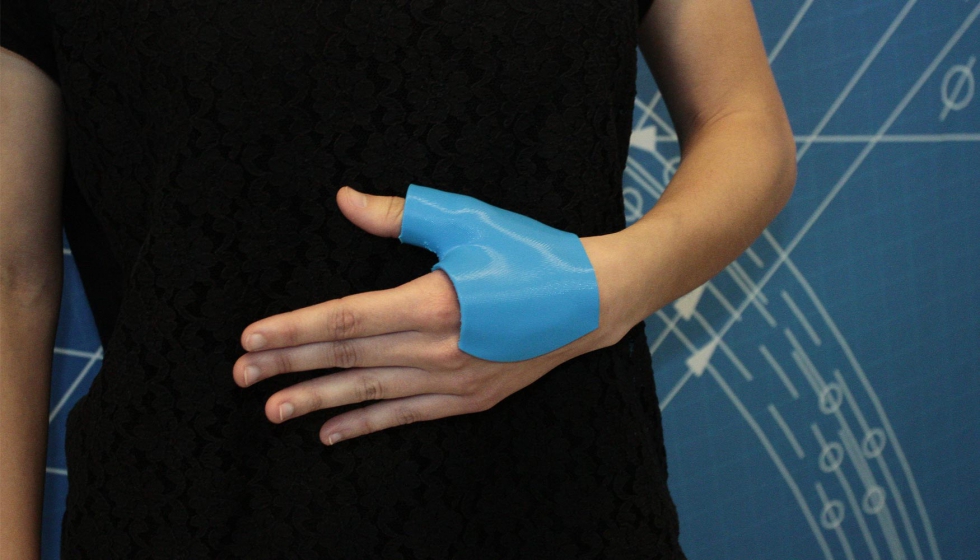
Además, buscan nuevos socios estratégicos. ¿Qué les demandan y qué les ofrecen a cambio a sus posibles partners?
La fabricación aditiva en el entorno empresarial necesita de equipos potentes y fiables, cuya amortización necesita de proyectos o clientes recurrentes que aporten viabilidad. Nuestro modelo de negocio pivota en la ingeniería y en los servicios añadidos al de la producción de las piezas, por eso hemos podido ir creciendo con recursos propios, pero vemos que el mercado y las empresas están acelerando el uso, y cada vez son más las compañías que se nos acercan para ver las sinergias que se pueden crear. Nosotros creemos en la colaboración entre empresas pero también entendemos el modelo de trabajo donde se busque algo más que intercambiar buenas prácticas.
Optimus3D es colaborador habitual de proyectos de I+D. ¿Puede explicarnos en qué proyectos de investigación colaboran en la actualidad?
El emprendimiento está en la forma de ser los promotores, y por ello, no nos gusta dejar pasar oportunidades de buenos negocios relacionados con lo que dominamos. Actualmente tenemos varios proyectos: Oseus, un sistema de regeneración ósea guiada donde la aditiva genera un soporte temporal mientras se crea el hueso definitivo; BIOferulas, un estudio con Bioef y Osakidetza en el Hospital de Basurto para mejorar las férulas de inmovilización de larga duración, adaptando a la geometría exacta del paciente; CAE, un cabezal de extrusión de material plástico desde granza o material reciclado; y otros dos proyectos, uno en el sector de arquitectura, analizando la estabilidad a la intemperie de elementos ornamentales impresos, y por otra parte con TKgune la viabilidad de moldes de inyección impresos en resina.
Participan como expositores en esta 2ª edición de Addit3D. ¿Qué podrán ver los visitantes en su stand?
Tenemos la colaboración entre empresas muy interiorizado, e innovamos hasta en organización empresarial puesto que compartimos stand con las empresas Addimen y Mufer de los que somos partners, y de esta manera aportamos soluciones integrales a nuestro clientes, fabricación aditiva en polímeros, metal y mecanizado especial.
¿Qué objetivos esperan cumplir en esta feria?
Esperamos poder superar el número de contactos de la última feria, y seguir transmitiendo a nuestros futuros ingenieros una nueva manera de hacer piezas y negocios.
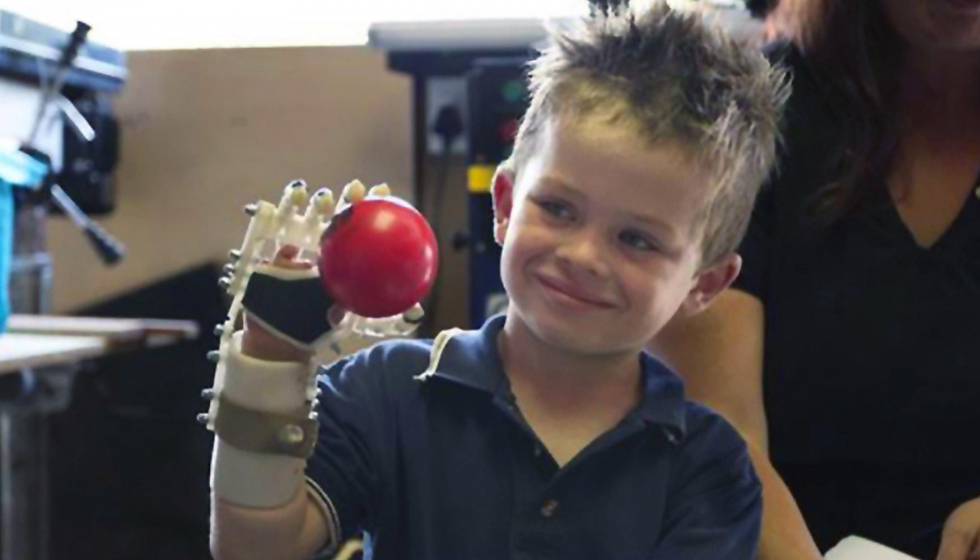