Gracias a la impresión 3D de Stratasys, Ambionics ha creado esta prótesis ahorrando un 90% de tiempo de diseño y producción
Un padre autodidacta desarrolla una prótesis hidráulica personalizada impresa en 3D para su hijo
La tecnología de impresión Stratasys 3D PolyJet de múltiples materiales y colores ha ayudado a Ben Ryan, fundador de Ambionics, a crear una prótesis hidráulica impresa en 3D y totalmente funcional para Sol, su hijo de dos años. Como parte de su investigación sobre el desarrollo de los niños con prótesis, Ben Ryan ha creado una exclusiva prótesis infantil que hace posible una aceptación más natural de las prótesis de brazo por parte de los niños pequeños.
El diseño y la producción personalizados de la prótesis hidráulica impresa en 3D, que ha constituido una innovación incomparable dentro de este campo de la medicina, ha supuesto un ahorro de costes de hasta el 76% y un ahorro en tiempo de diseño y producción del 90%, en comparación con los métodos tradicionales de fabricación. Esto es un avance muy importante puesto que permite usar las prótesis en una fase más temprana del desarrollo del niño.
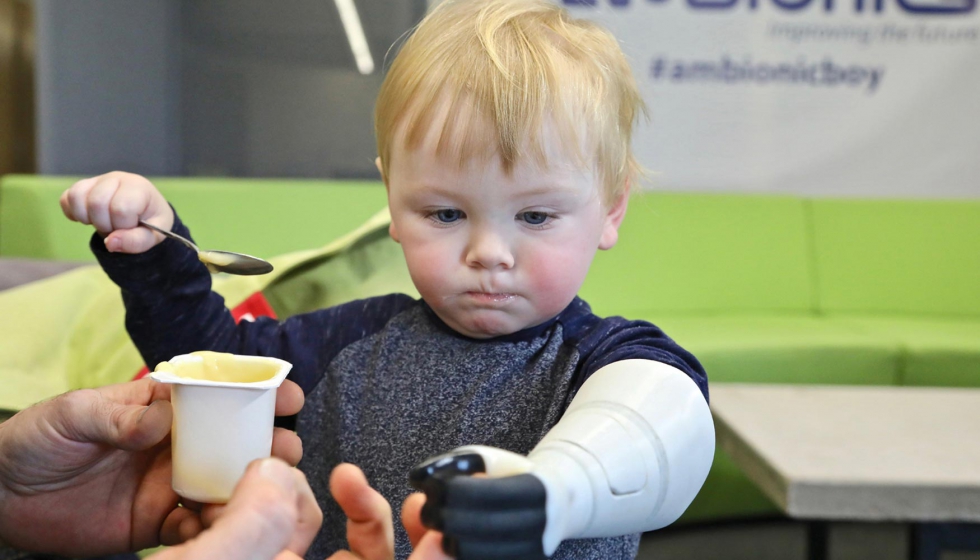
Las complicaciones que se produjeron durante el nacimiento de Sol, el hijo de Ben, en marzo de 2015 obligaron a amputarle el brazo izquierdo. Sol pudo conservar unos 2,5 cm del brazo pero hubiera tenido que esperar tres años para conseguir una prótesis mioléctrica del Sistema Nacional de Salud (NHS1) y un año para una prótesis cosmética sin funcionalidad. Como Ben observó que su hijo estaba perdiendo capacidad de reacción en el brazo izquierdo, decidió actuar.
Como fruto de su exhaustiva investigación sobre el desarrollo de los niños, Ben sabía que los índices de rechazo más altos se producen después de los dos años de edad2 y utilizar dispositivos funcionales antes de esa edad estaba favorecía el uso continuado de prótesis durante la infancia. Las conclusiones de otro estudio3 indicaban que los niños con prótesis colocadas antes de los dos años de edad tendían a aceptar mejor las prótesis motorizadas que los que las utilizan después de los dos años. Teniendo esto en cuenta, Ben empezó diseñando un brazo de espuma para su hijo y después una prótesis hidráulica para que Sol pudiera mover el pulgar por sí mismo.
Ben diseñó y creo su prótesis de brazo hidráulica impresa en 3D con la impresora 3D Connex de Stratasys. Empezó a practicar con prototipos del diseño e imprimió en 3D actuadores flexibles y una unidad de distribución de energía (fuelle helicoidal de doble acción o DAHB) para la prótesis. Según Ben, la unidad DAHB permite al usuario de la prótesis abrir y cerrar el pulgar en modo manual o con potencia asistida (aire comprimido o una bomba hidráulica y un depósito), pero la prestación de agarre sigue funcionando manualmente aunque se interrumpa el suministro de energía.
“El éxito de mi mecanismo DAHB patentado se basa en las prestaciones avanzadas de la impresora Stratasys Connex: la posibilidad de combinar materiales rígidos y blandos en una sola tirada de impresión fue esencial para sacar adelante el diseño”, explica Ben. “Tuvimos la suerte de poder acceder a esta tecnología, que nos permitió imprimir en 3D un prototipo del brazo de forma rápida y económica. El objetivo de Ambionics es garantizar que otros niños que carecen de algún miembro, como mi hijo, no tengan que enfrentarse a las limitaciones y los retrasos del proceso actual de fabricación de prótesis”.
Para desarrollar el diseño de la prótesis, Ben utilizó el software Autodesk Fusion 360.
“Se trata de un proyecto ambicioso e innovador, y ha sido muy estimulante trabajar con Ben", comenta Paul Sohi, experto en diseño de productos de Autodesk. “Es asombroso que aunque Ben no tiene formación ni experiencia en el diseño de productos haya aprendido lo suficiente como para crear un dispositivo que, además de ayudar a su hijo Sol, puede ayudar a otros niños que se enfrenten al mismo reto”.
Al igual que el ligero diseño impreso en 3D y que pesa menos que las alternativas mioeléctricas tradicionales, la prótesis hidráulica se acciona por tracción y los niños se acostumbran a su ‘brazo’ antes que a los ajustes y accesorios tradicionales. La posibilidad de funcionamiento sin necesidad de baterías o dispositivos electrónicos es otra característica exclusiva del diseño de Ambionics que reduce el riesgo de heridas.

- Sistema Nacional de Salud de Reino Unido
- J. Prosthet Orthot. 2005;17:119–124
- Toda M, Chin T, Shibata Y, Mizobe F (2015) Use of Powered Prosthesis for Children with Upper Limb Deficiency at Hyogo Rehabilitation Center. PLoS ONE 10(6): e0131746. doi:10.1371/journal.pone.0131746
Solo cinco días para pasar del escaneado del brazo a la prótesis ponible
El Sistema Nacional de Salud necesita 11 semanas para convertir el modelo de escayola del brazo en una prótesis ponible, pero Ben Ryan fue capaz de producir la prótesis en solo cinco días. Como el escaneado se puede guardar en un archivo, las prótesis de sustitución pueden producirse fácilmente mediante la impresión 3D.
“Básicamente, toda la prótesis se imprime en 3D", añade Ben. “La producción y el uso de las unidades DAHB es posible gracias a los materiales de impresión 3D similares a la goma y con soporte soluble de Stratasys. Las cavidades internas son complejas y hubiera sido imposible eliminar el material de soporte con medios mecánicos. Los materiales deben ser resistentes, pero también flexibles ya que se utilizan para transmitir la presión del fluido necesaria para que funcione el agarre”.
Ambionics, que ha patentado la tecnología DAHB en la que se basa la prótesis, tiene previsto ofrecer sus servicios a los proveedores de asistencia sanitaria de todo el mundo. La empresa, que continúa realizando estudios y pruebas sobre el desarrollo de los niños con prótesis, va a lanzar una campaña de financiación colectiva (crowdfunding) el 1 de marzo para poder realizar las pruebas de usabilidad necesarias para solicitar la autorización de comercialización del producto.
“Este caso es indicativo de la capacidad de la impresión 3D para mejorar la vida de las personas porque permite superar los obstáculos tradicionales de la fabricación de volúmenes pequeños”, comenta Scott Rader, director general de Healthcare Solutions de Stratasys. “Seguimos apoyando a los innovadores como Ben para que puedan llevar la personalización a la fabricación de prótesis”, concluye.