La Semana de los Moldes ofrece directrices a la industria para superar los actuales retos internacionales
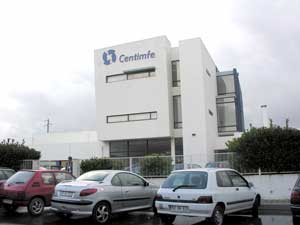
Aprovechando la presentación de importantes instituciones y universidades internacionales, se llevaron a cabo reuniones en el ámbito de los proyectos E-learning Hybrid Moulds y Eurotooling 21, así como los proyectos Memmolde Norte y Safework en los que se halla inmersa la industria moldista portuguesa.
El poder de atracción de este evento es siempre espectacular. No en vano, esta industria es una de las más dinámicas del país vecino y una de las fabricantes de moldes para la inyección de plástico más representativas del mundo. Exporta el 90 por ciento de su producción para cubrir la constante demanda de multinacionales que adquieren moldes “Made in Portugal” para la fabricación de productos para grandes marcas. En 2005, las exportaciones alcanzaron los 298 millones de euros, de un total de la producción de cerca de 330 millones.
Tal concentración de empresas del sector y de expertos en la materia, sumados a los cientos de invitados de otros países, elevan este evento a la categoría de cita fundamental para el sector, donde los profesionales pueden conocer de primera mano muchos de los retos o incertidumbres que atraviesa la industria internacional.
En 2020 China será un jugador de primer nivel
Ana Wittek, del Laboratorio de Moldes para Máquinas y Gestión de Producción Gestão de la Universidad de Aachen, comentó que los fabricantes de moldes europeos deben hacer frente a este crecimiento excepcional de la industria china en su capacidad de alcanzar los patrones internacionales como un desafío y no como una amenaza. "La mejor manera de lidiar con este desafío de China es que las compañías se diferencien unas de otras a través del perfeccionamiento de sus competencias tecnológicas, de la producción más rápida de moldes y de la reducción de la complejidad".
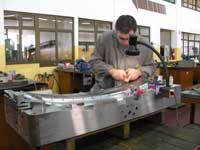
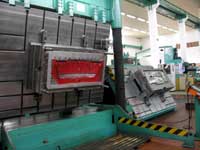
El tejido moldista portugués, concentrado en los polos de Oliveira de Azemeis (86 compañías y 1.600 trabajadores) y Marinha Grande (190 compañías y 5.000 trabajadores), lo que supone el 29 por ciento y el 63 por ciento del total de la industria, respectivamente.
Francia fue el principal mercado para la industria moldista portuguesa en 2005 con un 22 por ciento de la producción, seguido de Alemania con el 16 por ciento, España con el 14 por ciento y Estados Unidos con el 7 por ciento. Los siguientes destinos de los moldes portugueses en 2005 fueron Reino Unido, Suecia, Bélgica, Holanda, México, Turquía y otros.
La creación de redes de cooperación entre empresas para asumir grandes proyectos es uno de sus puntos fuertes, así como la formación de los trabajadores y la constante inversión en tecnología. Innovación y tecnología, son dos conceptos clave que definen la industria moldista portuguesa. La constante inversión en nueva maquinaria de alta velocidad y tecnología punteras como el láser, así como la implantación de la innovación en todos sus procesos, posicionan a este segmento industrial en una posición más que ventajosa en el panorama internacional.
Si existe otro factor que defina esta industria es su capacidad de ofrecer toda la cadena de valor al cliente, desde el diseño, pasando por la ingeniería de desarrollo de producto, prototipado rápido y “rapid tooling” e ingeniería simultánea.
Asimismo, para alcanzar nuevas soluciones la industria moldista lusa está preparada para ofrecer moldes multicomponente, multicavidades, inyección de gas asistida, “sheet moulding compounds” (SMC), unidades de inyección y mesas rotativas, insertos, moldes de compresión y otros.
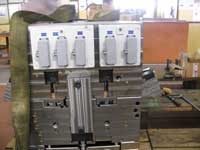
La formación como garantía de éxito; los tres desafíos de Portugal
Las nuevas formas de pago presionan al sector
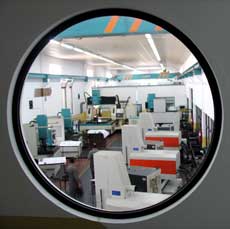
"Los fabricantes de moldes tienen la necesidad de volverse socios activos en todo el proceso de desarrollo de los productos en total cooperación como diseñador de productos", se refería Elsa Henriques. "Ser ágil significa integrar el personal de la empresa, la tecnología y la gestión de una empresa, de forma que se puedan comportar eficazmente ante cambios imprevisibles".
Los moldes inteligentes
El representante de la Fundación Ascamm afirmó que es necesaria una nueva concepción de proceso de inyección de plásticos que integre los tres componentes básicos de la cadena de suministro - pieza, molde y proceso- de manera que "el molde se vuelva un nexo del flujo de conocimiento". Este "proceso de moldeo por inyección inteligente y flexible" sería posible a través de moldes equipados con varias funcionalidades de avanzado valor añadido". Los moldes inteligentes serían capaces de adaptarse automáticamente a los cambios de condiciones físicas y químicas durante el proceso de moldeo y reconfigurarse ellos mismos para diferentes variantes de productos y tipologías. Estos moldes conseguirían interactuar con otros componentes de la cadena de moldeo para optimizar todo el proceso de producción, añadió Manuel León. Deberían tener la capacidad de incorporar servicios adicionales en el producto moldeado final, tales como sistemas de rastreabilidad utilizando tecnología innovadora con base en web. Este paso de moldes pasivos y tradicionales a moldes activos e inteligentes requiere la integración de sensores en el molde y el desarrollo de diagnósticos específicos para monitorizar en tiempo real el sistema de control que permitirá monitorizar y controlar a través de control remoto. Estos sistemas de monitorización darían origen a información que podría ser dirigida a un fichero (archivo) grabando la firma del molde y sus condiciones d funcionamiento (caja negra). Este fichero sería la base de mantenimiento preventivo. Como se refiere Manuel León, en un futuro próximo, la disponibilidad de moldes inteligentes puede introducir descubrimientos importantes en las tecnologías de producción tradicionales de piezas de plástico y también en la industria de los moldes.
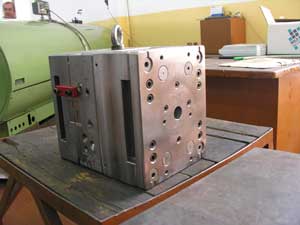
El “Ying-Yang” del desarrollo del automóvil
Según sus propias palabras, era también un factor clave que permitiría a los fabricantes de moldes continuar recibiendo instrucciones de los productores de piezas de automóviles, a pesar de los precios competitivos verificados en otras partes del mundo.
El peso medio de los plásticos utilizados en los automóviles ha crecido cerca del 20 por ciento durante la útima década, mientras que el peso del acero y de otros materiales ha decrecido un 10 por ciento y un 13 por ciento, respectivamente.
“El cambio era mucho mayor en términos de volumen”, añadió Javier Castany. “Las nuevas exigencias de desarrollo en ambientes acústicos, interiores y de seguridad, como las presiones para reducir los costes de fabricación conducirán a la utilización de nuevos materiales en procesos de interiores de automóviles”, comentó.
Las piezas plásticas de automóviles desempeñan un papel cada más estructural en el diseño del automóvil. Al mismo tiempo, las nuevas tecnologías con importantes aplicaciones estéticas indican que se da una enorme atención a los aspectos decorativos, de color y de textura de las piezas automóviles.
Estas tecnologías incluyen: pintura, IMD, decoración hot foil, inyección, textura de moldes, revestimiento de vinilo, procesos de inyección híbridos y línea de montaje de moldes.
De acuerdo con Javier Castany, la solución para conseguir un mejor equilibrio entre las especificaciones técnicas y estéticas es la contracción.
Durante la jornada, se visitaron diversas empresas. La empresa Plasdan, de Marinha Grande, mantiene un concepto de empresa basado en la creación de una estrecha colaboración en la industria del molde entre grandes compradores y pequeños y medianos fabricantes, aportando servicios de ingeniería y de desarrollo de producto. Su estrategia continúa basada en el concepto de ofrecer innvación internacional y ”know how” en sectores clave como la automoción, aeronáutica, equipamiento de inyección multicomponentes y packaging. La compañía tiene varias patentes para procesos relacionados con la inyección multicomponente.
Por otro lado, TJ Moldes es un ejemplo claro de estrategia empresarial en Portugal. Ubicada en Marinha Grande, forma parte de un grupo de empresas con capacidades de producción que van desde moldes de pequeñas dimensiones hasta moldes de gran tamaño y complejidad.
Asismimo, Simoldes, ubicada en Oliveira de Azeméis, es uno de los mayores grupos moldistas en todo el mundo. El grupo Simoldes es conocido por la calidad de sus moldes y por una rica cartera de clientes en la que destacan grandes partners automovilísticos de primer nivel, como Volvo.
Por último, Azemoldes, Moldes de Azeméis, es un empresa característica por sus modernas instalaciones. Fundada en 1987 ofrece en un área de 5.500 metros cuadrados, avanzada tecnología y servicios desde la concepción hasta el ensayo final de los moldes, dirigidos principalmente a los sectores de la automoción y electrodomésticos, entre otros.
Según sus propias palabras, era también un factor clave que permitiría a los fabricantes de moldes continuar recibiendo instrucciones de los productores de piezas de automóviles, a pesar de los precios competitivos verificados en otras partes del mundo.
El peso medio de los plásticos utilizados en los automóviles ha crecido cerca del 20 por ciento durante la útima década, mientras que el peso del acero y de otros materiales ha decrecido un 10 por ciento y un 13 por ciento, respectivamente.
“El cambio era mucho mayor en términos de volumen”, añadió Javier Castany. “Las nuevas exigencias de desarrollo en ambientes acústicos, interiores y de seguridad, como las presiones para reducir los costes de fabricación conducirán a la utilización de nuevos materiales en procesos de interiores de automóviles”, comentó.
Las piezas plásticas de automóviles desempeñan un papel cada más estructural en el diseño del automóvil. Al mismo tiempo, las nuevas tecnologías con importantes aplicaciones estéticas indican que se da una enorme atención a los aspectos decorativos, de color y de textura de las piezas automóviles.
Estas tecnologías incluyen: pintura, IMD, decoración hot foil, inyección, textura de moldes, revestimiento de vinilo, procesos de inyección híbridos y línea de montaje de moldes.
De acuerdo con Javier Castany, la solución para conseguir un mejor equilibrio entre las especificaciones técnicas y estéticas es la contracción.
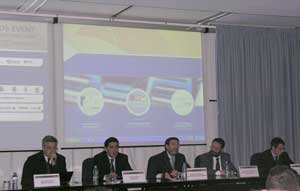