Mecanizado de engranajes únicos en fresadoras multieje
Los engranajes cónicos son los que presentan una mayor complejidad en su fabricación, enfatizándose esta dificultad para el caso particular de los engranajes cónicos espirales (espirocónicos). Esta tipología de engranajes normalmente es generada mediante un procedimiento continuo de corte usando máquinas especiales de generación, las cuales, además de suponer una elevada inversión, suponen también una restricción tanto de tamaño como en forma de los mismos. Gracias a la mejora de los CNC multieje, de las máquinas 5- ejes/multitarea, y de los softwares CAD/CAM, se presenta el medio adecuado para la generación de estos elementos de geometría compleja en máquinas de propósito general y con herramienta estándar. La principal ventaja que se desprende de la fabricación de estos componentes en máquinas de propósito general es el aumento de la versatilidad en la fabricación, tanto en términos de tipología como de tamaño, además de hacer factible la realización de modificaciones arbitrarias sobre los dientes que componen el engranaje. El uso de herramienta estándar también constituye una ventaja a tener en cuenta, como es la reducción tanto en coste como en los tiempos de entrega, parámetros de vital importancia en producción.
1. Introducción
Los engranajes espirocónicos de gran tamaño son frecuentemente utilizados en aplicaciones donde se requiera una elevada transmisión de potencia, y donde esta transmisión debe ser lo más suave y silenciosa posible, como es el caso de aplicaciones de generación de energía térmica, sistemas de propulsión de barcos, turbinas eólicas o la transmisión de potencia en el sector aeronáutico, entre muchas otras.
Los engranajes espirocónicos son generados en su mayoría mediante procesos de corte continuos en máquinas específicas [1], clasificadas en función del método de fabricación utilizado. Existen diferentes métodos de fabricación, como son: 1. Generación mediante hobbing con fresas de plato con cuchillas de corte perimetral (sistema Gleason); 2. Generación continua mediante hobbing espiral con fresas de plato con cuchillas de corte perimetral (sistema Cyclo-Palloid de Klingelnberg y sistema Oerlikon); 3. Generación continua mediante hobbing espiral con fresa-madre del tipo cónica (sistema Palloid de Klingelnberg). En la figura 1 se puede observar cada uno de los métodos descritos anteriormente.
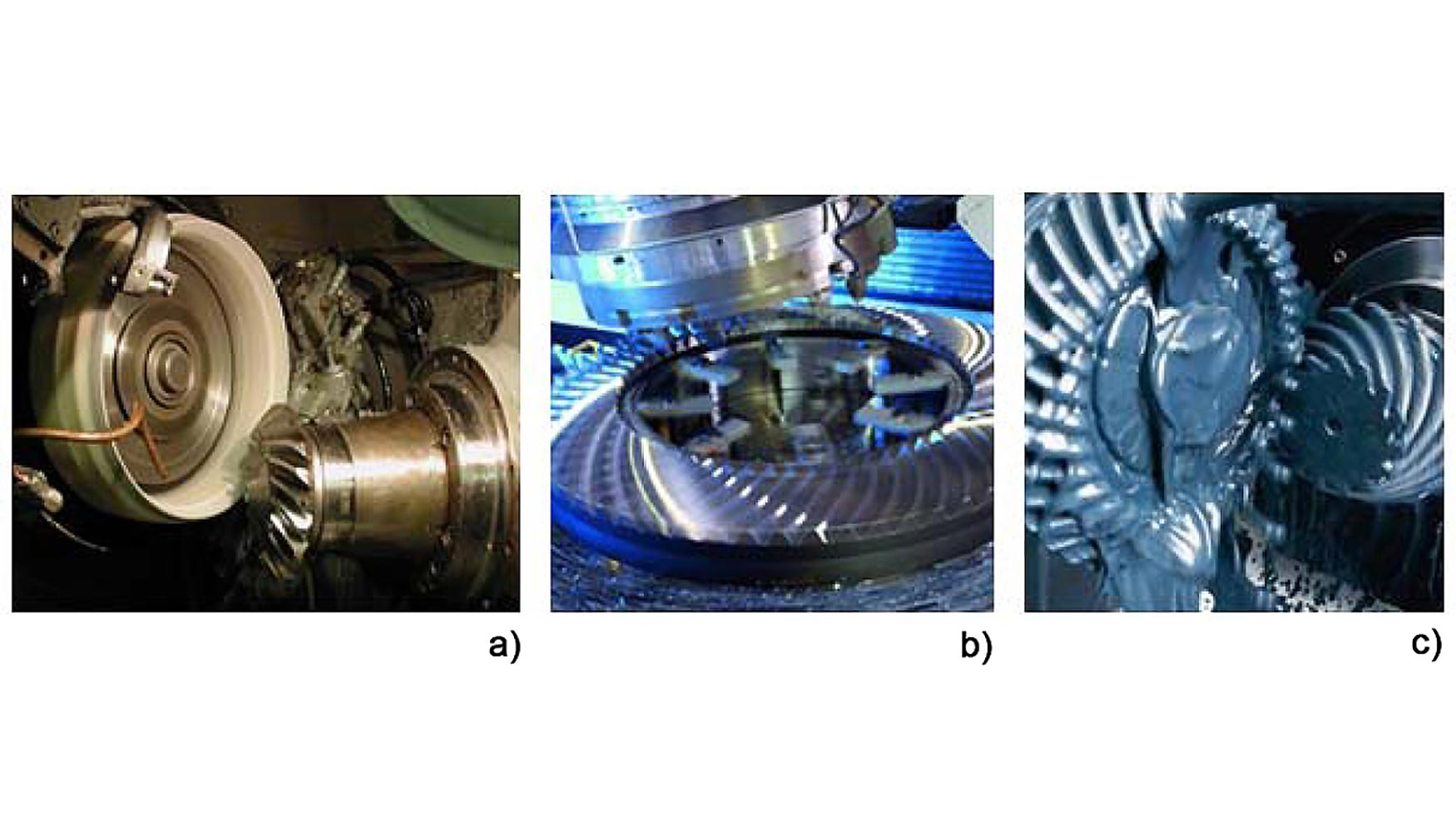
La mejora continua de los CNC multieje, de las máquinas 5-ejes/multitarea, y de los softwares CAD/CAM ha propiciado la aparición de un medio adecuado para la generación de estos elementos de geometría compleja en máquinas de propósito general y con herramienta estándar.
Algunas ventajas que se desprenden de esta idea son el aumento de la versatilidad en la fabricación, tanto en términos de tipología como en tamaño, además de hacer factible la realización de modificaciones arbitrarias sobre los dientes que componen el engranaje (tip relief, root relief, angular profile variance…). El uso de herramienta estándar también constituye una ventaja a tener en cuenta, como es la reducción tanto en coste como en los tiempos de entrega, parámetros de vital importancia en producción.
El uso de máquinas 5-ejes/multitarea proporciona la flexibilidad de usar el mejor método de fabricación, satisfaciéndose así las necesidades de los clientes, y son capaces de conseguir engranajes de mayor calidad que los obtenidos mediante los métodos tradicionales en operaciones previas al tratamiento térmico [2]. La figura 2 muestra las dos máquinas que han sido utilizadas en la realización del estudio que se está presentando, siendo una un centro de mecanizado 5-ejes (a) y la otra una máquina multitarea (b).
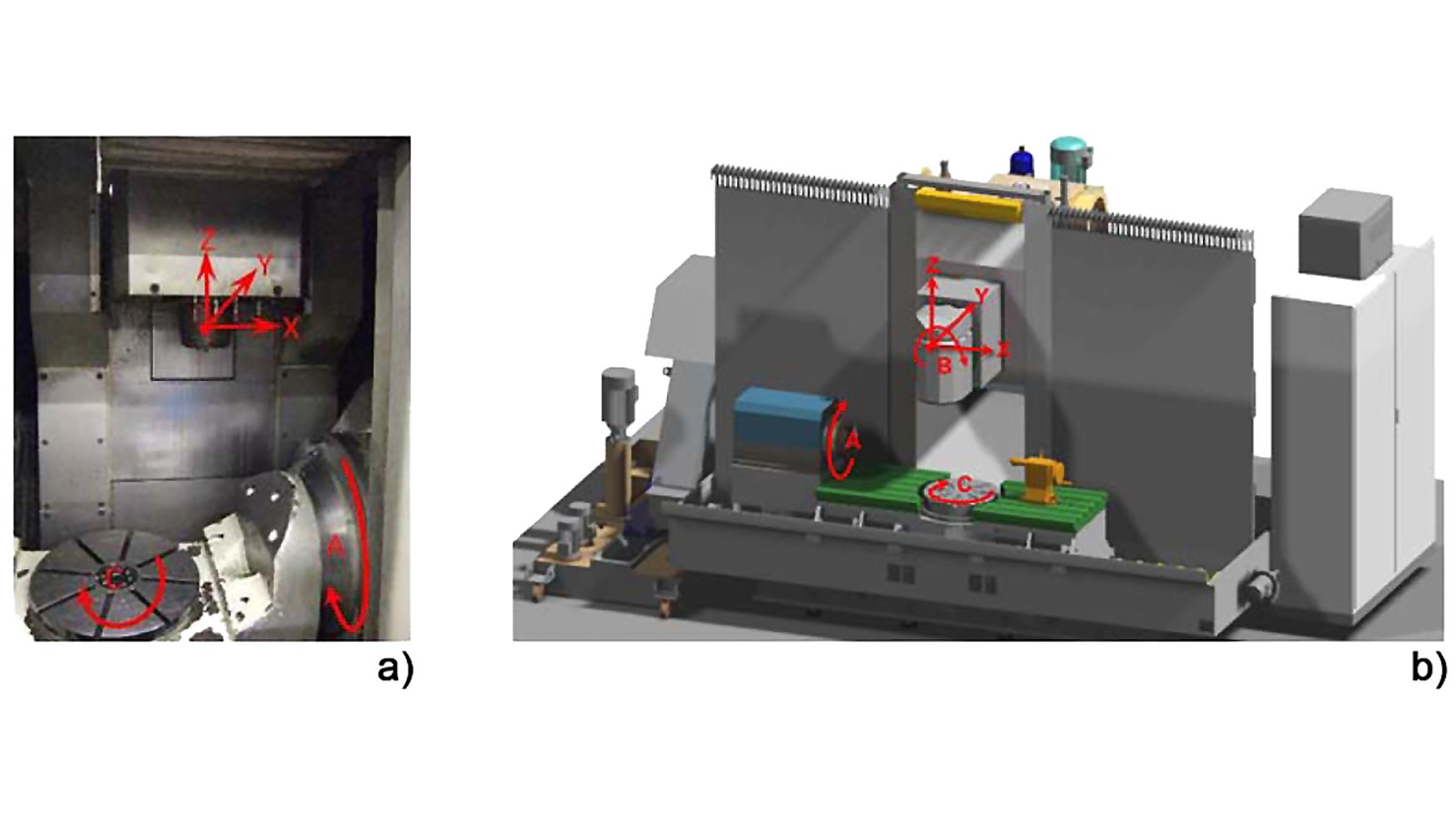
Para llevar a cabo el mecanizado de los engranajes espirocónicos, se precisa de modelos sólidos viables de los mismos. Sin embargo, hay que ser conscientes de la complejidad de la geometría cinemática de los engranajes espirocónicos, en conformidad con la variedad de métodos de corte existentes (Gleason, Klingelnberg, Oerlikon). Tampoco es fácil de generar el modelo 3D necesario para el mecanizado [3]. Existe una gran variedad de softwares de cálculo comerciales útiles para generar la geometría 3D. Algunos de ellos, una vez se ha generado la geometría 3D, esta debe ser importada a un software CAM. También existen softwares que son capaces de integrar diseño + CAM, pero suelen tener un coste muy elevado. En nuestro caso particular, se ha optado por un software de bajo coste para el diseño del engranaje espirocónico de gran tamaño, y una vez este ha sido diseñado ha sido importado a un software CAM, en el cual han sido evaluadas diferentes estrategias de mecanizado. El software permite al usuario elegir entre diferentes métodos de fabricación, como son Gleason y Klingelnberg (Figura 3), para la generación de los dientes. Piñón y corona son generados al mismo tiempo, debido a que los engranajes cónicos son siempre producidos en pares y a partir del mismo proceso de mecanizado con el fin de conseguir un buen patrón de contacto en la práctica.
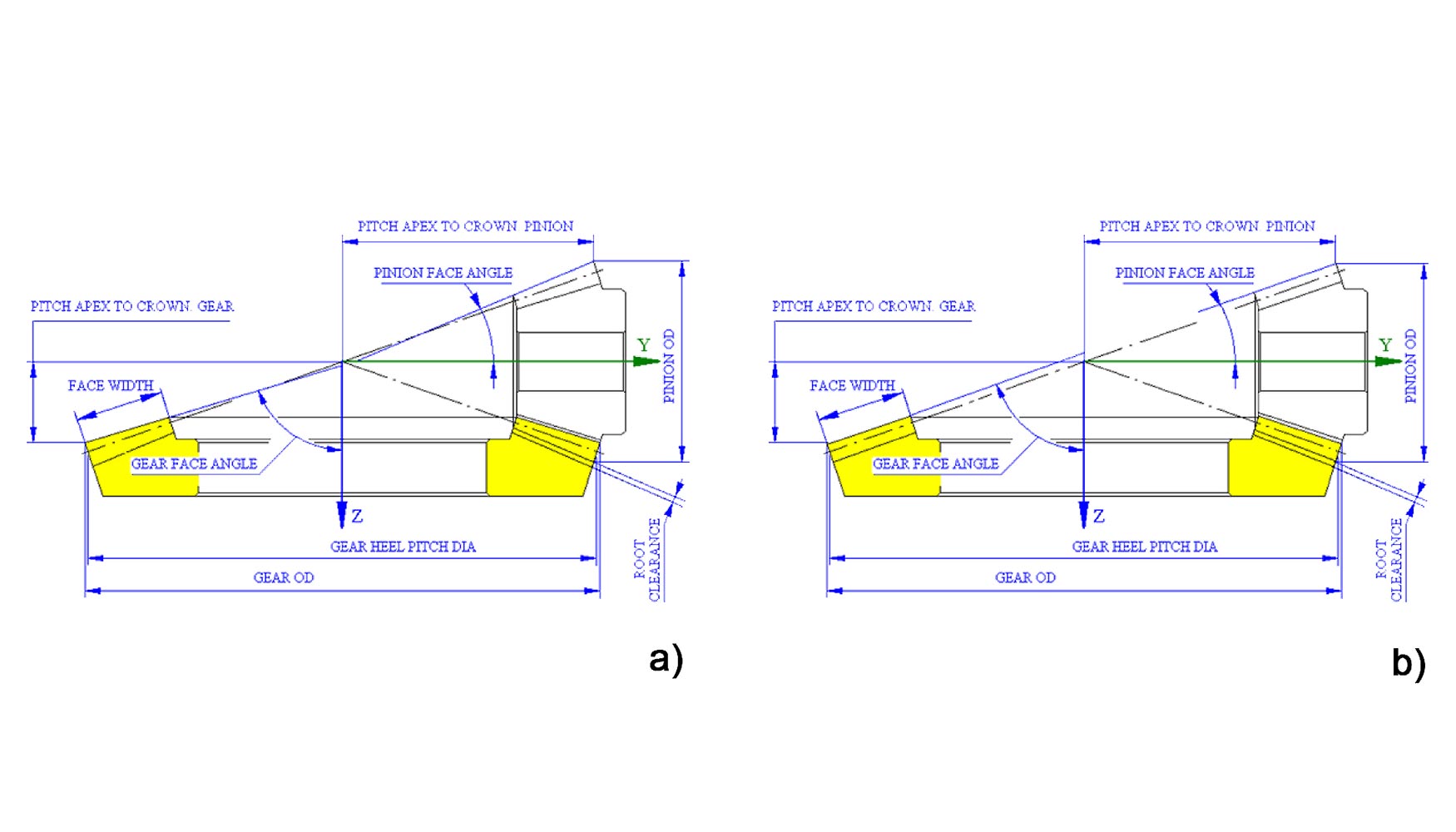
El método de fabricación seleccionado ha sido el método Gleason, y el software CAD/CAM utilizado ha sido el Siemens NX 9.0. Se ha mecanizado el mismo engranaje en cada una de las máquinas expuestas anteriormente, lo que ha permitido plasmar las ventajas del mecanizado en una máquina multitarea frente al mecanizado en un centro de mecanizado 5-ejes.
Además de ser utilizadas herramientas estándares, las cuales presentan un mayor número de proveedores y consecuentemente un menor coste, una nueva tecnología ha sido evaluada, la turbina de aire. La turbina de aire, debido a su alta velocidad y par constante, va a permitir la evaluación de diferentes herramientas de acabado con el fin de obtener una mayor calidad en la superficie final del diente.
2. Metodología y proceso experimental
El caso de estudio es un engranaje espirocónico de un tamaño considerable (Figura 4), la tipología de engranaje que presenta mayor complejidad en su fabricación. El material utilizado ha sido el F1550, un acero de cementación. En la tabla 1 de muestran los parámetros de diseño del engranaje realizado.
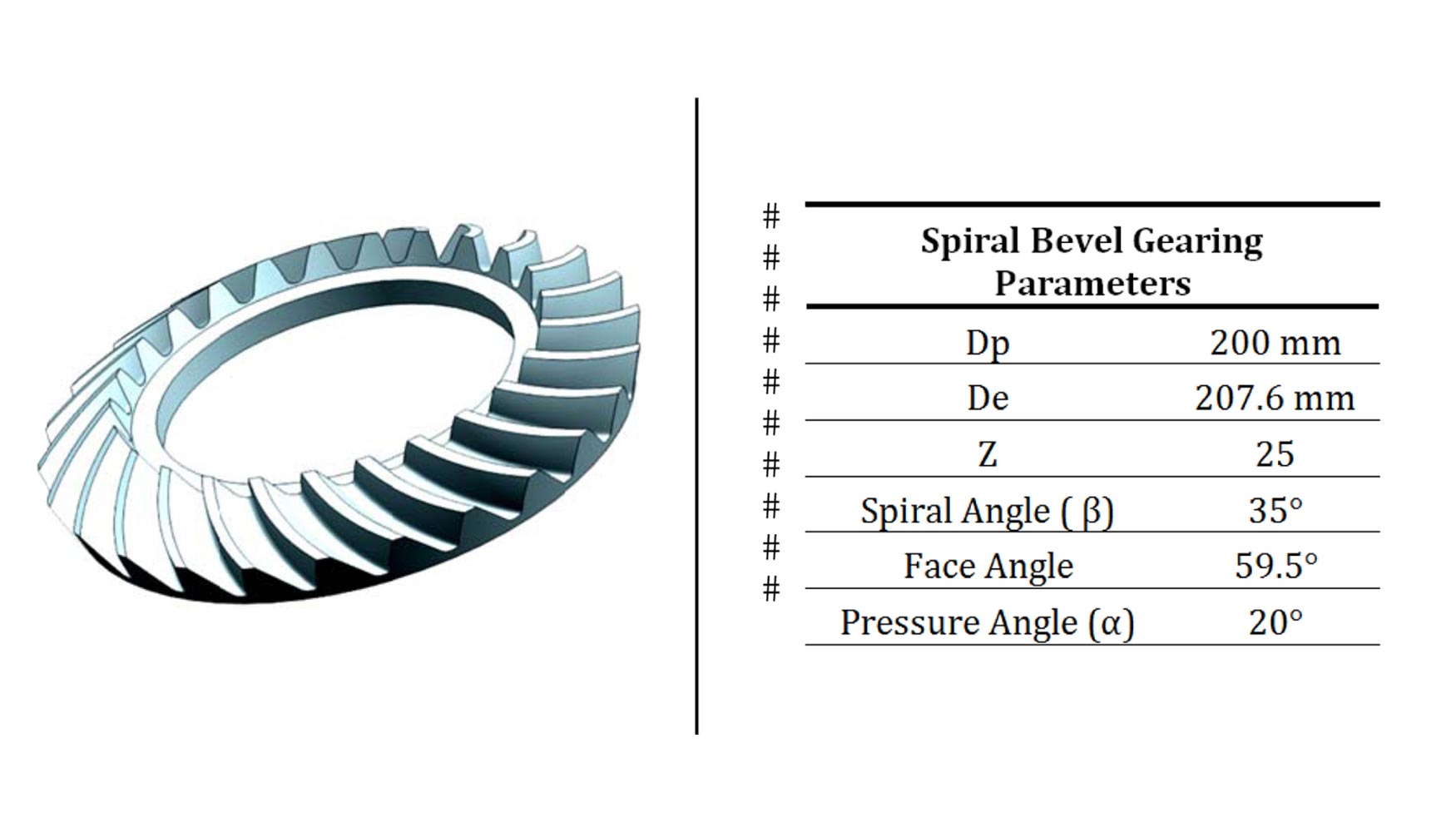
A la izq., figura 4: Engranaje espirocónico. A la dcha., tabla 1: Parámetros de diseño.
El mecanizado de un mismo engranaje ha tenido lugar en dos máquinas diferentes. El primero de ellos ha sido mecanizado en un centro de 5-ejes (Ibarmia Z V25/U600). El segundo, en cambio, ha sido mecanizado en una máquina multitarea (Ibarmia ZVH38 /L1600 Mu ltiprocess). En el centro de mecanizado de 5-ejes se ha utilizado una mordaza autocentrante de precisión, especialmente adecuada para trabajar en máquinas universales de 5-ejes. Por otro lado, debido a que en las máquinas multitarea pueden ser realizados múltiples procesos de mecanizado y con varias tipologías diferentes de herramientas, el usuario tiene la flexibilidad de elegir el proceso de mecanizado basándose en requerimientos de calidad y productividad. La existencia de un divisor de torneado vertical, para casos como el que nos ocupa, donde se dispone de una geometría circular, el sistema de amarre de la pieza se simplifica al no ser necesario el uso de sistemas de amarre externos. Esto permite realizar el engranaje espirocónico de principio a fin en una sola atada, consiguiéndose: reducción o eliminación de transferencia de piezas entre máquinas, reducción de la puesta a punto, menor tiempo de ejecución por pieza, reducción del número de máquinas, reducción en el número de cambios de herramienta y, por consiguiente, un aumento de la competitividad de las empresas [4]. El mecanizado de la pieza en una sola atada también supone la obtención de un producto de una mayor calidad. Debido a la flexibilidad que presentan, los engranajes espirocónicos presentados en este trabajo se han mecanizado con herramientas estándares. Para las operaciones de desbaste han sido utilizadas fresas frontales y, para las operaciones de semi-acabado y acabado, han sido seleccionadas fresas cónicas de punta esférica, las cuales permiten un acceso más limpio a la zona a mecanizar, evitando en gran medida la posible interferencia entre herramienta y pieza. El uso de herramienta estándar presenta una serie de ventajas respecto a las herramientas especiales utilizadas en las tecnologías de generación tradicionales. Al existir un mayor número de proveedores en el mercado, se consigue una reducción de los tiempos de entrega y un aumento de la oferta de las mismas, lo que conlleva la existencia en el mercado de precios mucho más competitivos.
Hay que ser conscientes que cada una de las tipología de engranaje existentes no son otra cosa que una sucesión de ranuras, todas ellas con la misma forma. Por esta razón, con el objetivo final de optimizar el proceso de mecanizado de engranajes en máquinas de propósito general, se han evaluado diferentes estrategias de mecanizado, parámetros de corte y herramientas. Cada una de las estrategias de mecanizado evaluadas ha sido realizada en dientes consecutivos con el objetivo de comprobar la repetibilidad de la máquina, parámetro de gran importancia en el mecanizado de esta tipo de componentes.
Como el engranaje a mecanizar tiene 25 dientes, 5 grupos diferentes de operaciones de mecanizado han sido evaluados. Cada grupo de operaciones será aplicado en 5 dientes consecutivos, como ya se ha comentado anteriormente. La tabla 2 muestra las diferentes operaciones de mecanizado llevadas a cabo por cada grupo de dientes.
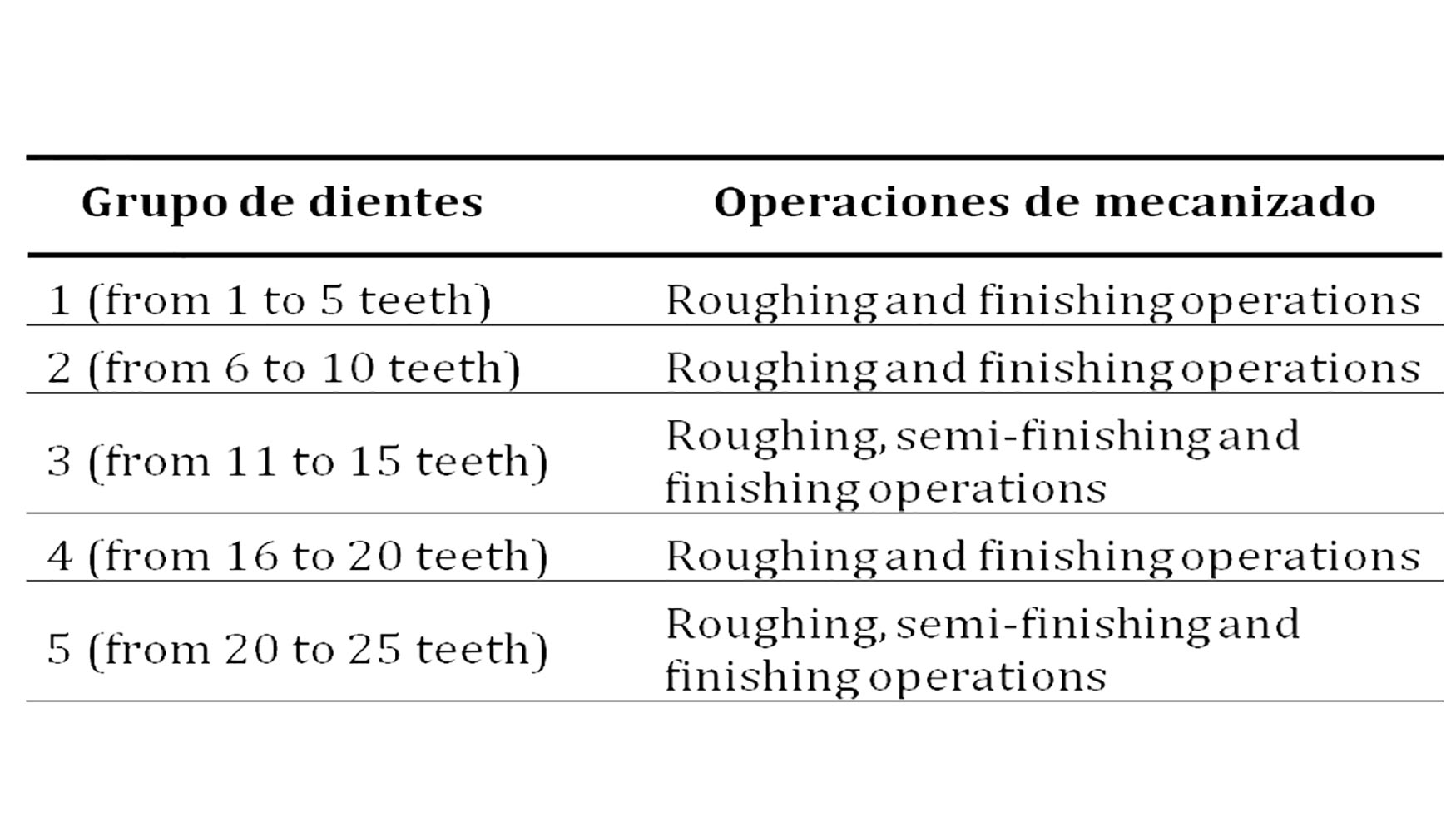
Para la operación de desbaste, han sido evaluadas 5 estrategias de mecanizado diferentes (Figura 5) para una misma tipología de herramienta, una fresa frontal. Después del desbaste con cada una de las 5 estrategias evaluadas, parámetros como el tiempo de mecanizado y el desgaste de la herramienta han sido tenidos en consideración con el objetivo final de obtener cuál de ellas es la que optimiza de manera más pronunciada el proceso de desbaste del engranaje.
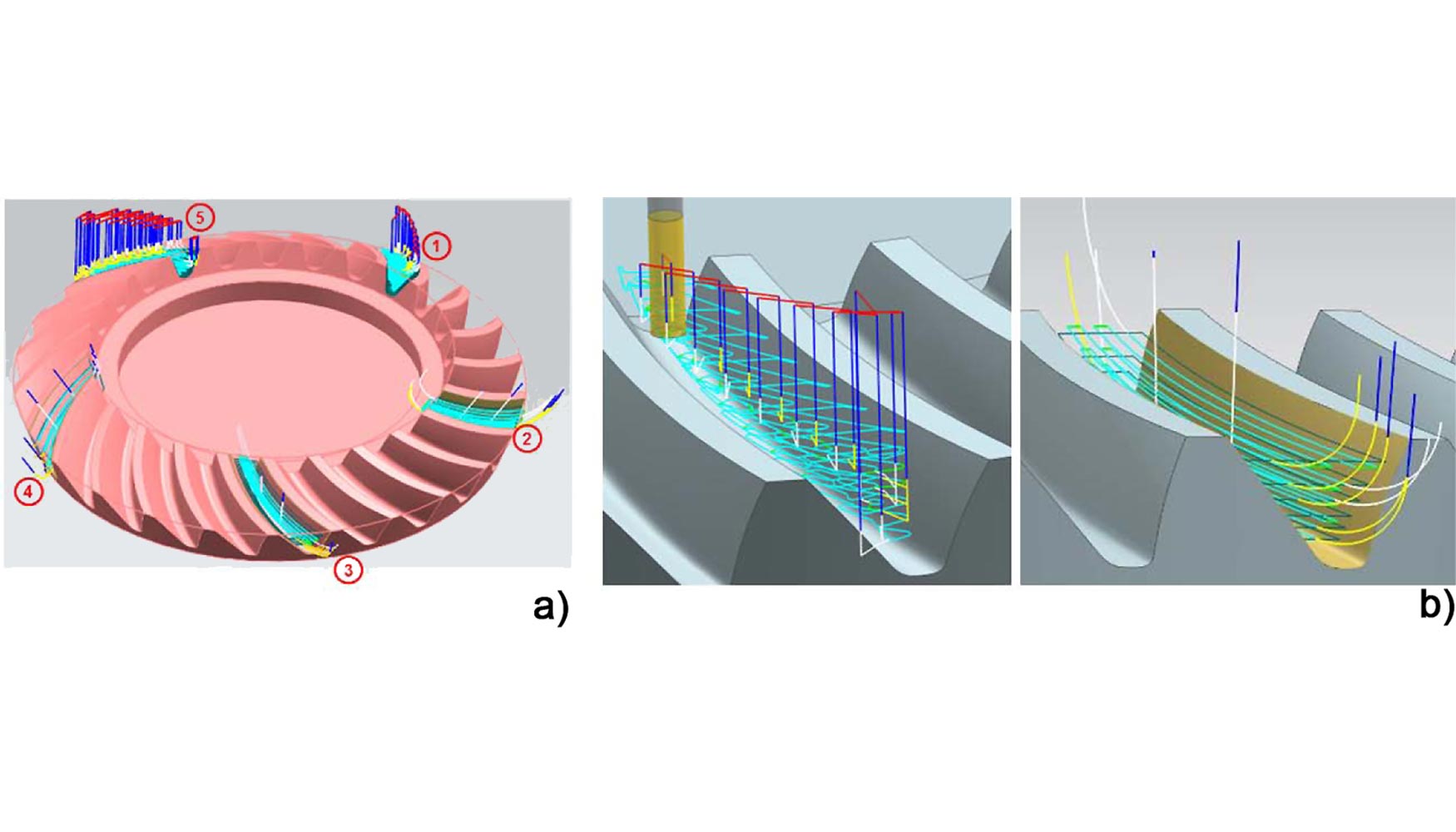
Por otro lado, uno de los grupos de operaciones incluye una operación de semi-acabado. El objetivo es evaluar si la inclusión de esta operación supone una mejora de los parámetros de calidad medidos en la superficie final obtenida. La herramienta utilizada es una fresa cónica de punta esférica estándar.
Por último, para la operación de acabado del engranaje espirocónico se ha utilizado una misma tipología de herramienta para dos diámetros diferentes, con el único fin de detectar mejoras en el proceso de mecanizado. Se han estudiado dos estrategias diferentes de mecanizado, una para el engranaje realizado en el centro de mecanizado 5-ejes y otra para el engranaje realizado en la máquina multiproceso. Han sido evaluados también diferentes ‘maximum scallop heights’ y diferentes patrones de corte (Zig y Zig-zag) (Figura 6). Mediante la programación CAM, el usuario tiene la opción de elegir diferentes niveles de precisión en el mecanizado, pero una mejora en la calidad superficial conlleva un aumento del tiempo de mecanizado. Han sido evaluados 8 diferentes ‘maximum scallop heights’, de 0,5 hasta 0,002 mm, analizándose cada uno de los diferentes niveles de calidad obtenidos.
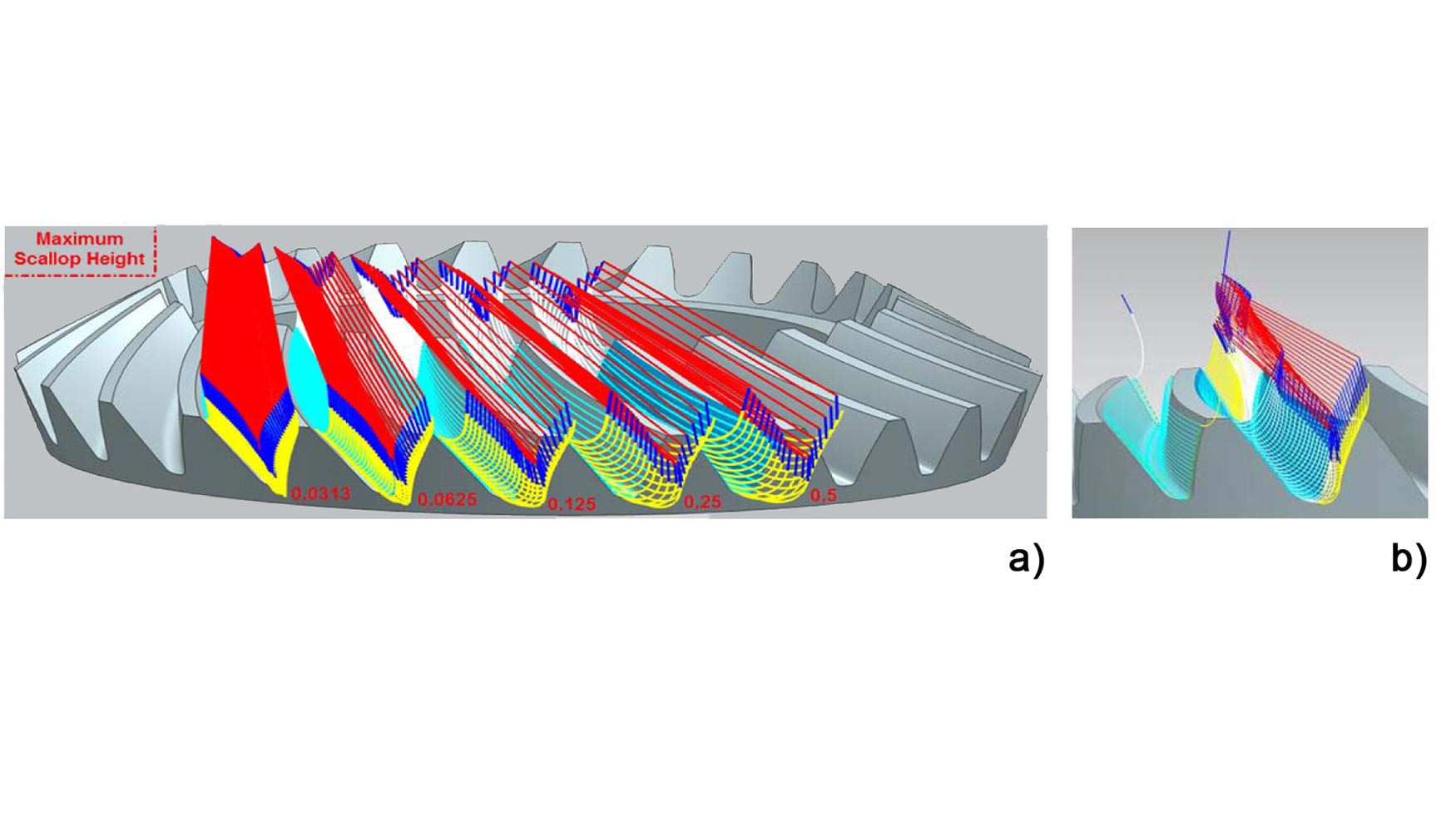
Como herramienta de acabado, aparte de la típica fresa esférica, una nueva tecnología ha sido evaluada: la turbina de aire (Figura 7). La razón principal por la que esta nueva tecnología de mecanizado ha sido evaluada, es porque es fácilmente integrable en cualquier máquina CNC, y puede presentar una mejora en el proceso de mecanizado de engranajes en máquinas de propósito general. La turbina de aire, debido a su alta velocidad y par constante, va a permitir la evaluación de diferentes herramientas de acabado con el fin de obtener una mayor calidad de la superficie del diente. Diferentes muelas esféricas de CBN y una fresa multidiente de metal duro son las herramientas que han sido evaluadas, siempre tras un semi-acabado previo realizado con una fresa cónica esférica estándar. La superficie final obtenida será evaluada tras ser aplicados diferentes diámetros de herramienta y diferentes estrategias de acabado.
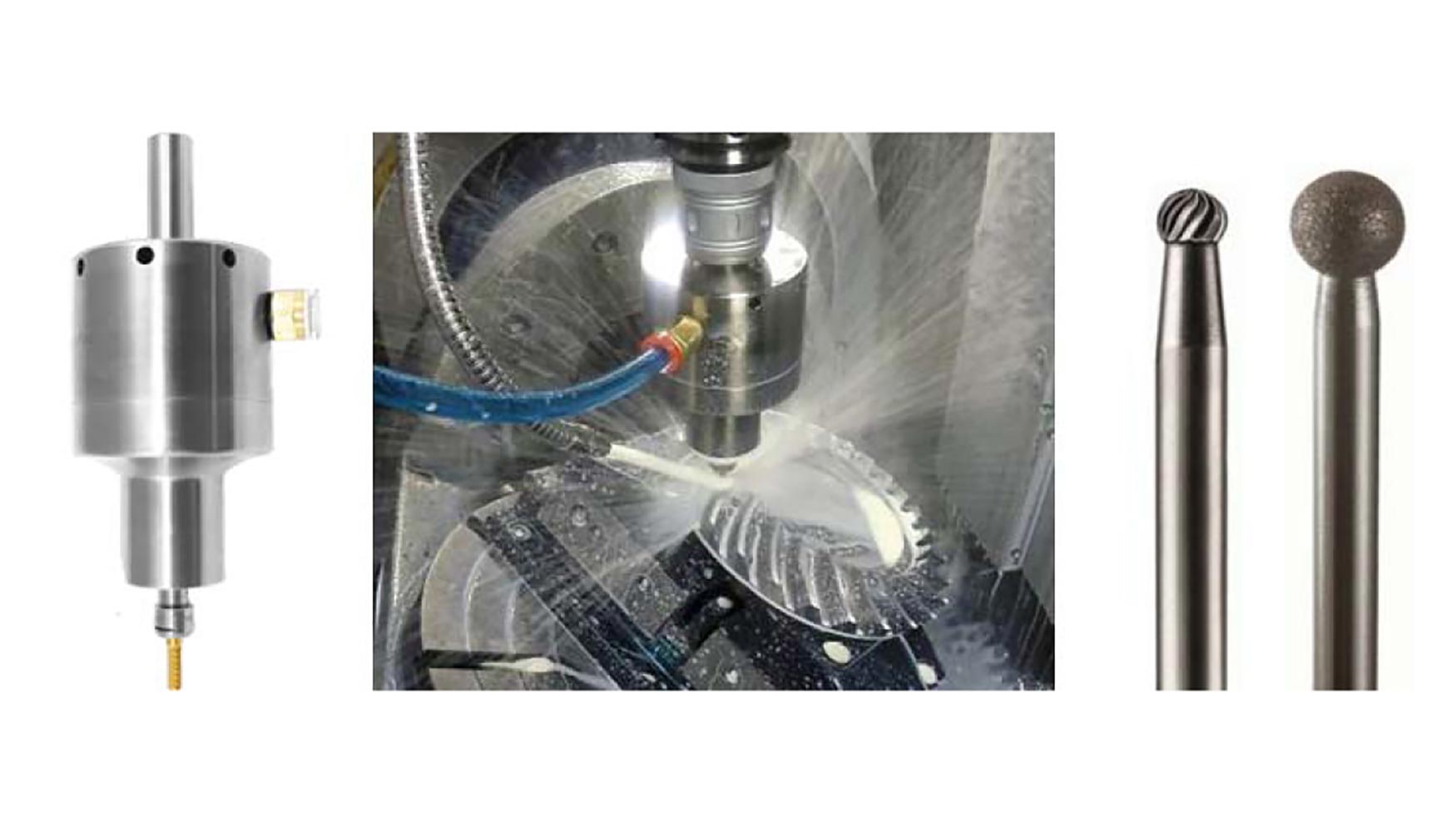
3. Resultados
Con la única finalidad de evaluar cuál de las estrategia de desbaste evaluadas en el mecanizado del engranaje espirocónico hace óptimo el mecanizado, la tabla 3 muestra los resultados tanto del tiempo por diente como del desgaste sufrido por la herramienta para cada una de las 5 estrategias evaluadas. Para la elección de la estrategia óptima entre las estrategias presentadas y evaluadas, se va a buscar un compromiso entre el tiempo por diente y el desgaste de herramienta.
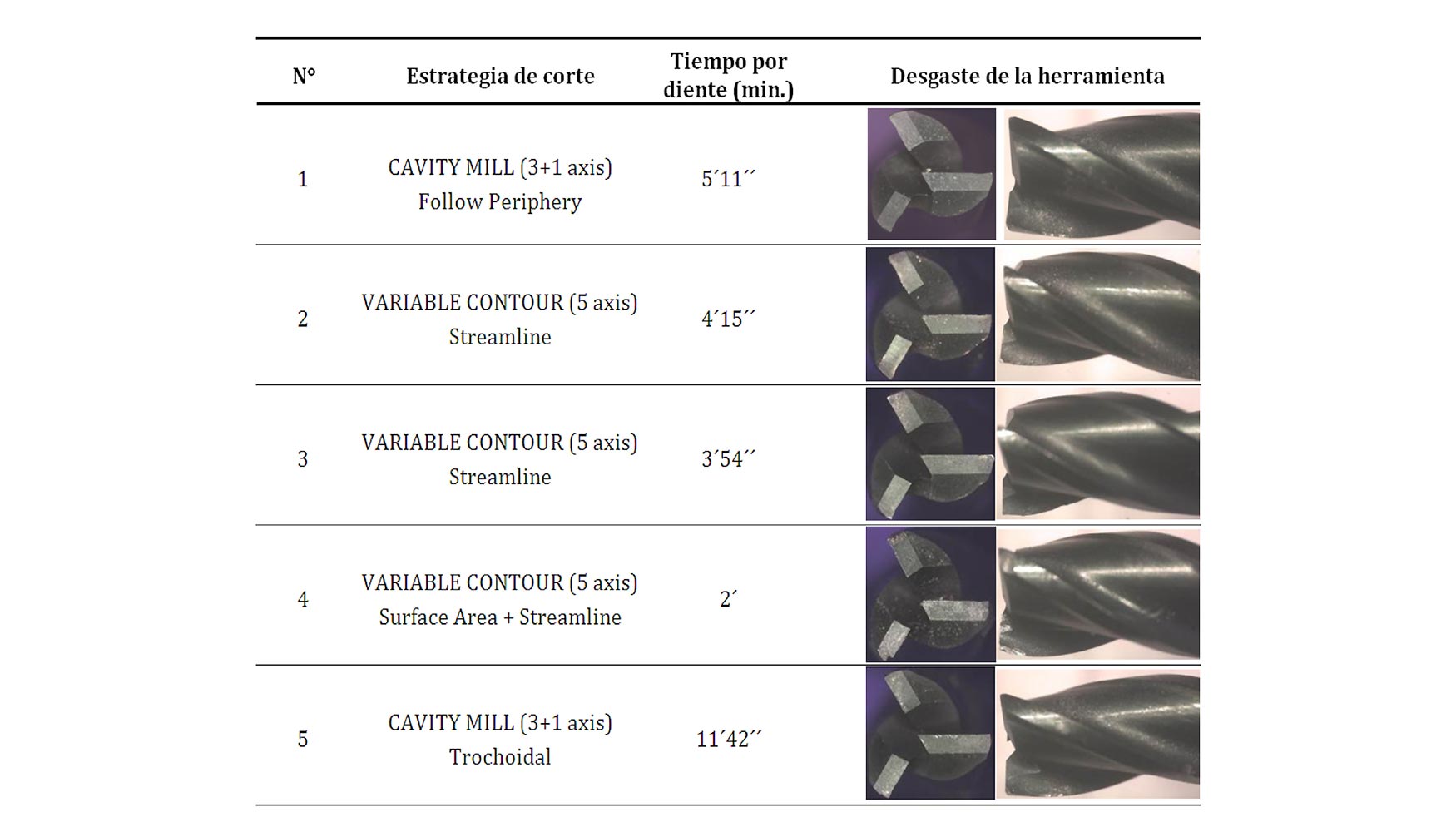
Después del proceso de acabado de cada uno de los diferentes dientes, en los que se han evaluado diferentes estrategias de corte, diferentes patrones de corte (Zig y Zig-zag) y diferentes ‘maximum scallop heights’, se ha procedido al análisis de los parámetros de calidad de cada una de las superficies finales obtenidas. Mediante sistemas de medida ópticos, como el perfilómetro tridimensional con focal Leica DCM 3D (Figura 8. a) y sistemas de medida de rugosidad por contacto, como es el caso del Taylor Hobson Form Taylorsurf (Figura 8. b), han sido obtenidos valores de rugosidad en 2D/3D, además de ser obtenidas topografías de cada una de las diferentes superficies generadas (Figura 8. c). El uso de otras tecnologías, como una CMM de Zeiss y un escáner óptico Atos Gom, van a permitirnos una rigurosa inspección en 3D de otros parámetros muy relacionados con la calidad, al poder ser comparado el engranaje final obtenido tras el mecanizado con el archivo CAD de partida del mismo.
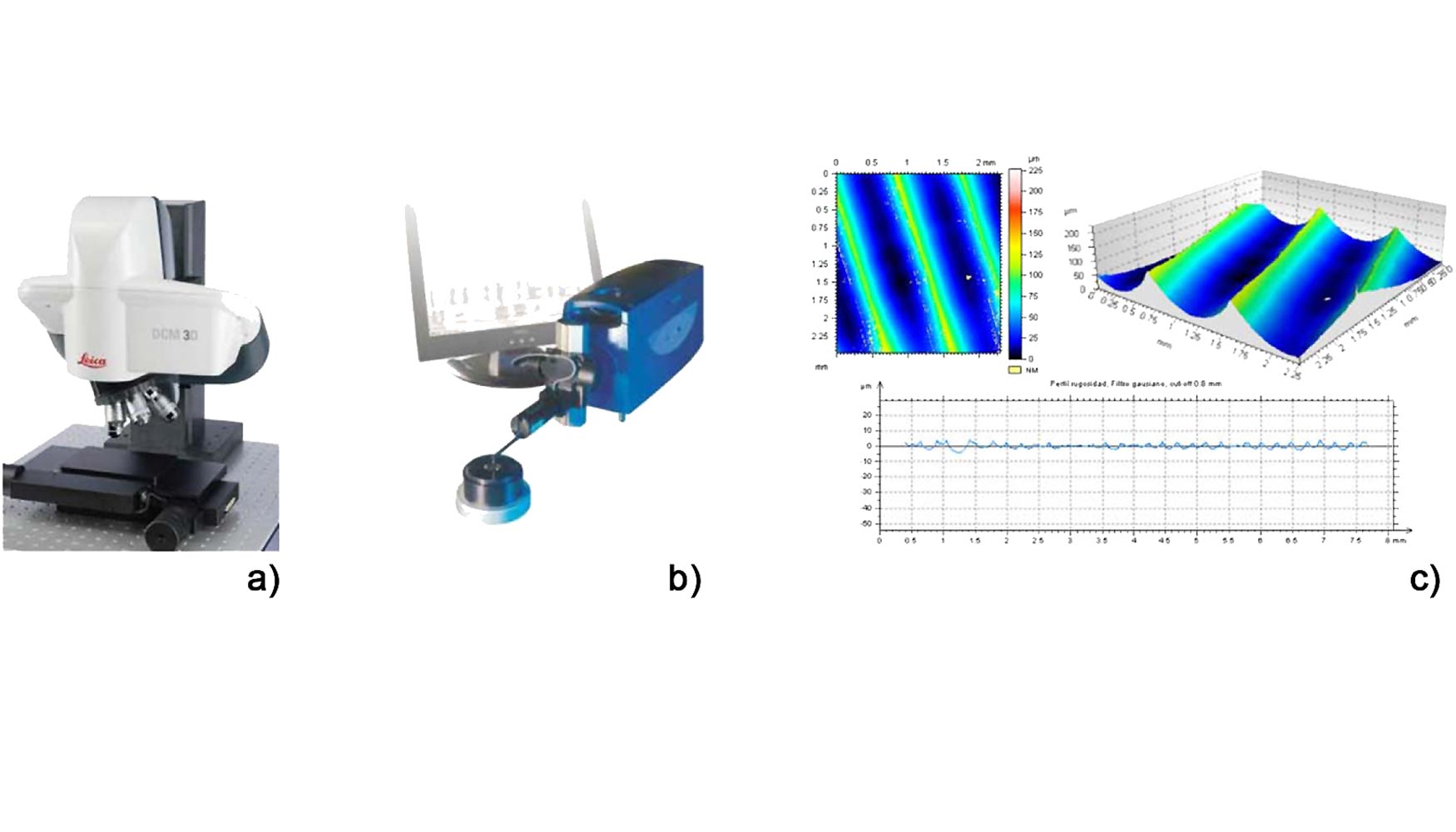
En las tablas 4 y 5 se muestran tanto el tiempo de mecanizado como los diferentes parámetros de rugosidad obtenidos (Ra y Rz) para cada una de las estrategias de mecanizado, patrones de corte y herramientas evaluadas. La tabla 4 muestra los resultados obtenidos tras el mecanizado del engranaje espirocónico en el centro de mecanizado de 5-ejes (Ibarmia ZV25/U600), mientras que la tabla 5 corresponde a los resultados obtenidos tras el mecanizado en la máquina multitarea (Ibarmia ZVH38/L1600 Multiprocess). Bajo cada una de las tablas se han añadido diferentes fotografías, ordenadas de manera cronológica, de cada uno de los procesos de mecanizado realizados en cada una de las diferentes máquinas evaluadas.
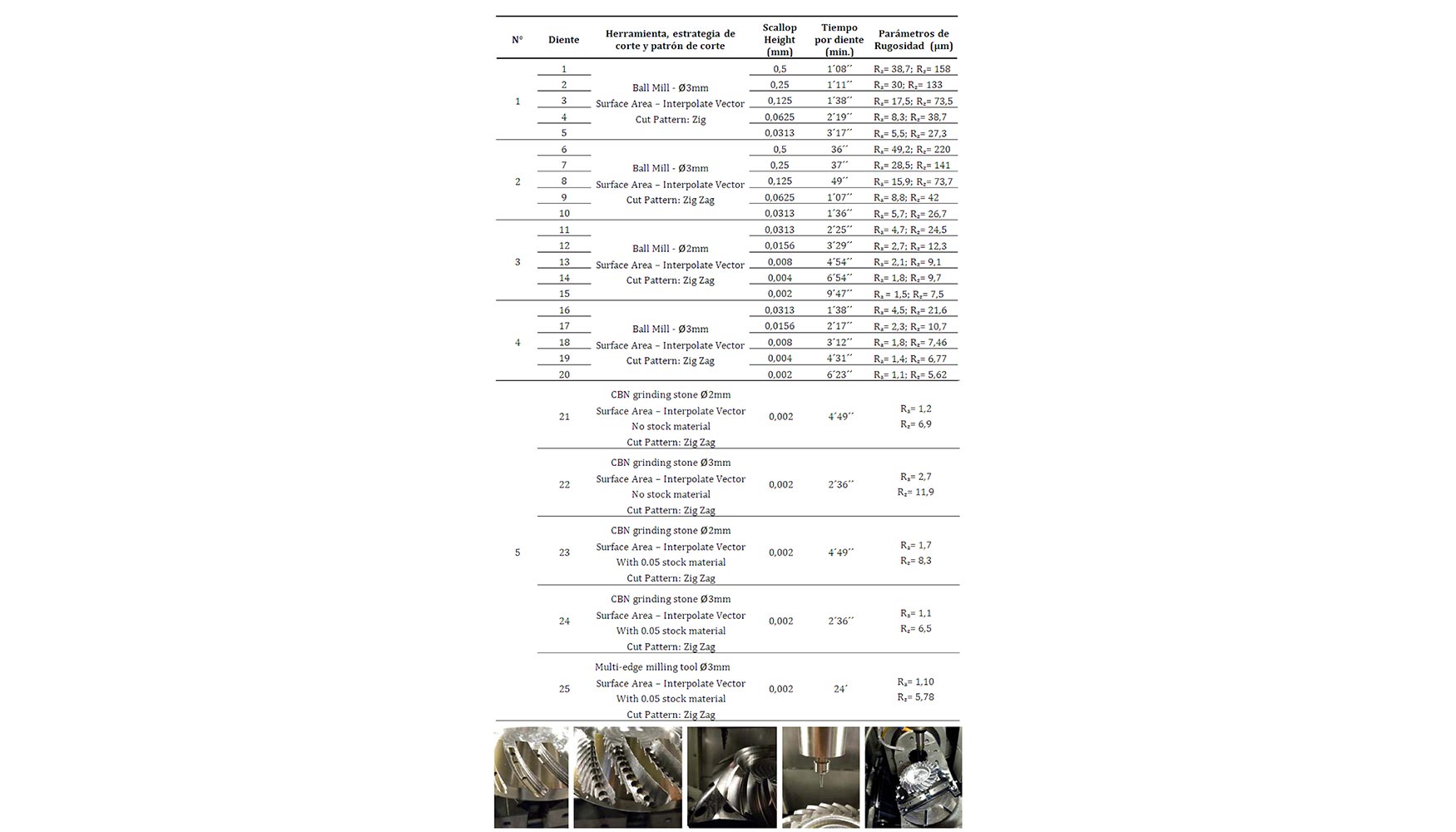
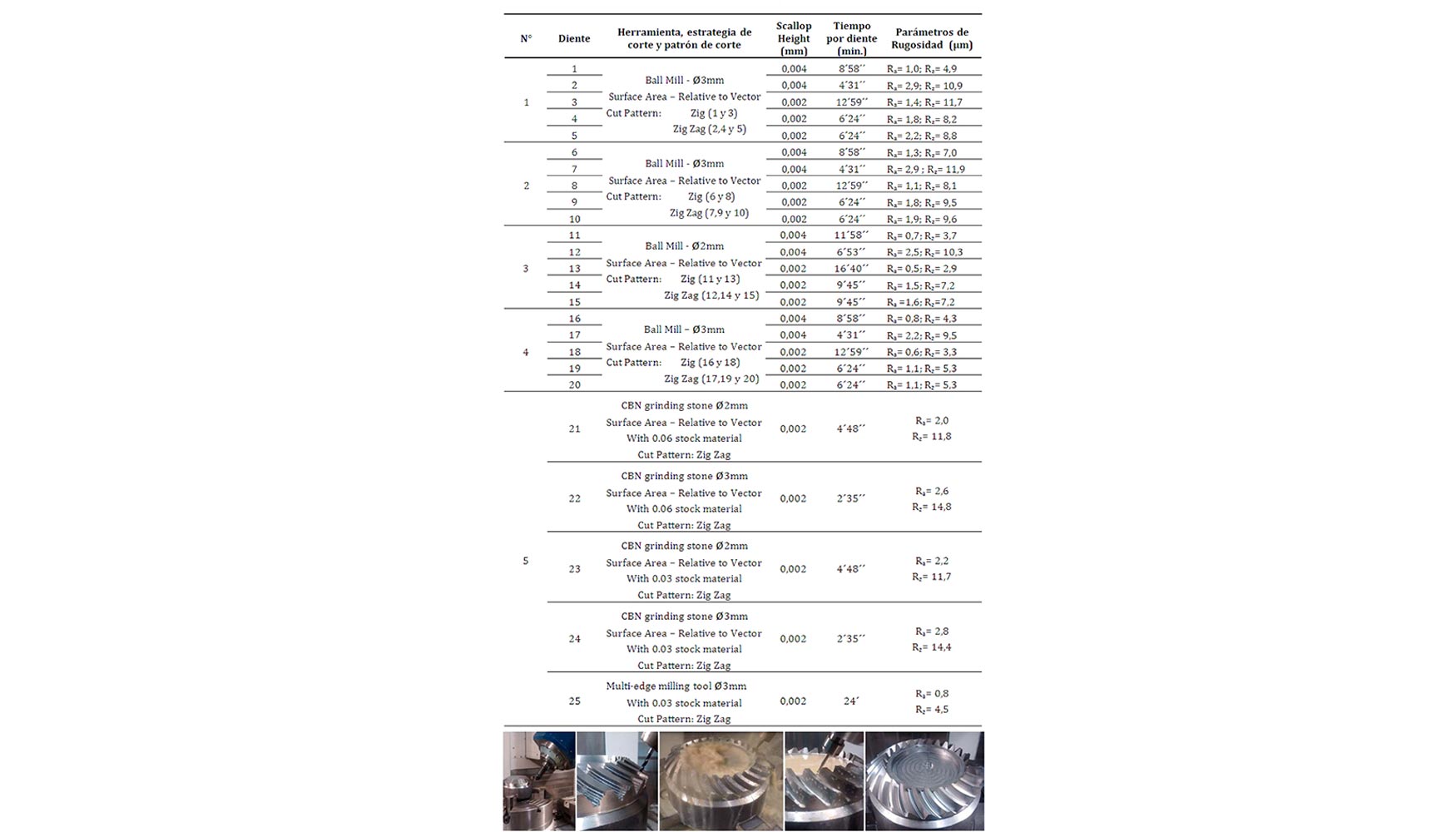
Como resultado de los avances tecnológicos de la última década, y observándose los resultados obtenidos en este trabajo, el mecanizado de engranajes de gran tamaño en máquinas de propósito general se presenta como un proceso totalmente factible. Al ser mecanizados dos engranajes idénticos (mismo archivo CAD) de dos máquinas diferentes, estas pueden ser comparadas. La máquina multitarea ha permitido que todo el mecanizado del engranaje espirocónico se realizara en una sola atada, con sus consecuentes ventajas. La primera de ellas es la realización de todas las operaciones, tanto las de torneado como las de fresado, en una misma máquina. Al ser sólo necesaria una máquina, se elimina la transferencia de piezas entre máquinas, reduciéndose así el tiempo de ejecución por pieza. Cabe destacar también la simplicidad de amarre de la pieza, que nos permite amarrar la pieza sin ser necesarios sistemas de amarre externos ni preformas previas (Figura 9). Al no ser necesaria una preforma, el material sobrante puede ser utilizado para posteriores mecanizados, lo cual supone un ahorro tanto en material como en herramientas.
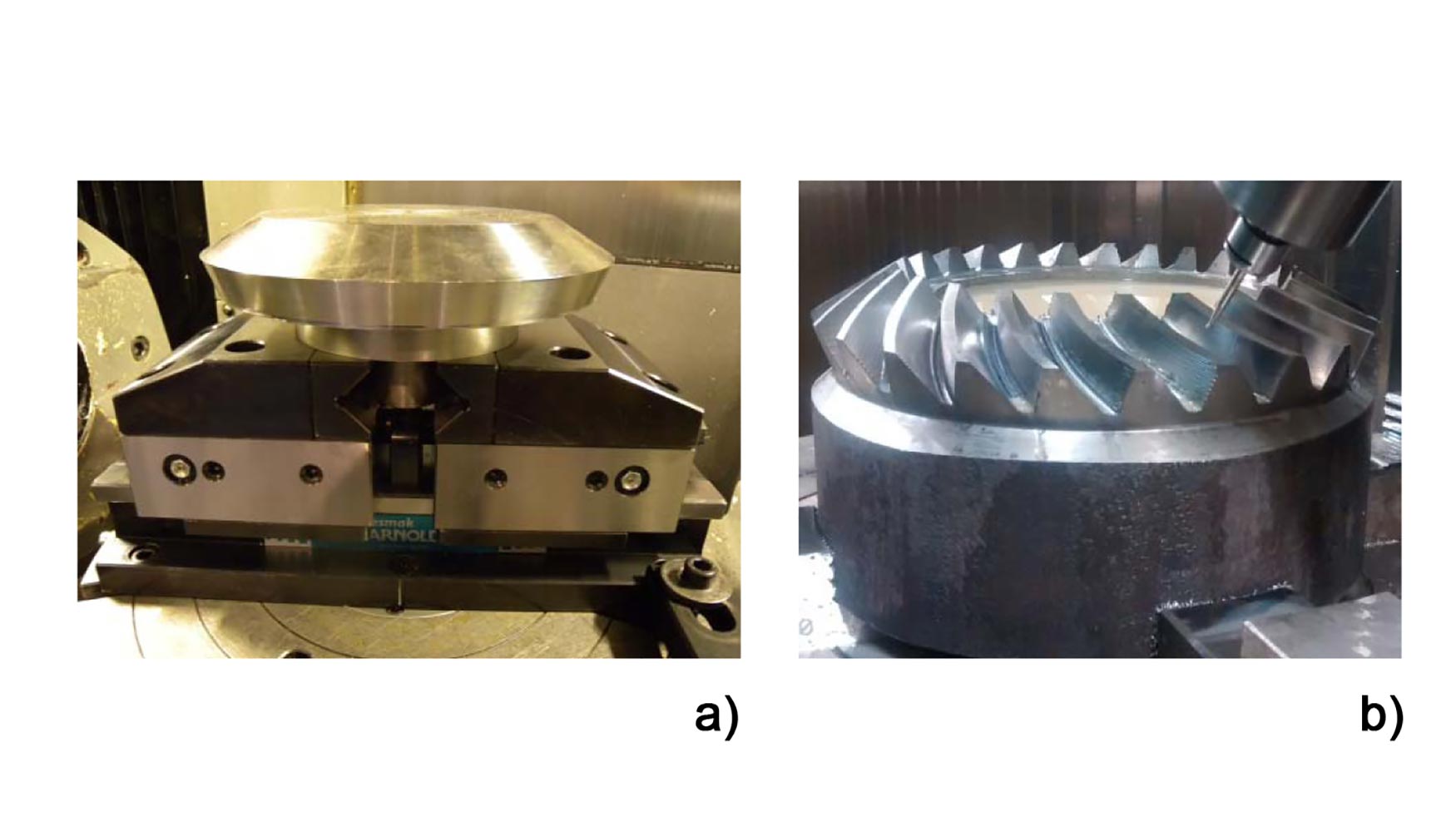
En cada uno de los diferentes ‘maximum scallop heights’ evaluados (de 0,5 hasta 0,002 mm), se ha podido comprobar que los valores de rugosidad se han ido mejorando progresivamente hasta alcanzarse valores de Ra = 1 μm y de Rz = 5μm. Una mejora de la rugosidad superficial conlleva también un aumento del tiempo de mecanizado, por esta razón es importante conocer la calidad final requerida por el cliente.
En el tercer grupo de dientes mecanizados se ha introducido una operación de semi-acabado previa a un acabado con fresa cónica de punta esférica de ø2 mm, un milímetro más pequeña que la utilizada en el resto de los acabados. Como se puede observar en los resultados, los parámetros de rugosidad obtenidos son ligeramente mayores, lo cual verifica el cumplimiento de la ecuación de obtención de la Ra teórica, dónde el radio de la herramienta se encuentra en el denominador y un incremento del mismo supone una reducción de la rugosidad.
Los resultados muestran que la calidad superficial obtenida tras la aplicación de las dos estrategias de acabado, tanto la utilizada en el centro de mecanizado 5-ejes (Surface Area – Interpolate Vector) como la utilizada en la máquina multiproceso (Surface Area – Relative to Vector), es prácticamente la misma. Mientras que una de ellas supone un mecanizado continuo en 5 ejes, la otra supone un mecanizado continuo en 3 ejes tras un previo posicionamiento de los ejes B y C.
El mecanizado en la máquina multitarea también nos permite verificar la mejora, en lo que a rugosidad superficial se refiere, cuando el patrón de corte seleccionado es Zig en vez de Zig-zag. El patrón de corte Zig permite que la herramienta corte en todo momento en concordancia, aunque también conlleva un aumento considerable en el tiempo de mecanizado.
La viabilidad de la turbina de aire como tecnología de acabado para engranajes espirocónicos ha sido evaluada. Su alta velocidad y par constante permite mecanizar la superficie final de los dientes mediante el uso de herramientas especiales, como son las muelas de CBN, con rangos de velocidades de corte del orden de 2 o 3 veces mayores a las utilizadas con las fresas cónicas estándares utilizadas en el resto de las estrategias. Los resultados obtenidos han sido relativamente buenos, debido a que se obtienen valores de rugosidad muy aceptables. Una disminución de la longitud de la herramienta (mayor rigidez) y/o una elección de muelas de CBN con una mayor concentración de grano y/o un menor tamaño del mismo permitirían la obtención de superficies finales con rugosidades inferiores a las expuestas en las tablas de resultados.
Agradecimientos
Los autores quieren mostrar su agradecimiento a los fondos para personal investigador en cooperación con el entorno productivo y social del programa Zabalduz, lanzado en 2013 y financiado en su totalidad por el Gobierno Vasco. Este agradecimiento se quiere hacer extensible a la financiación recibida por la UPV/EHU bajo el programa UFI 11/29. También es destacable el apoyo del Dpto. de Ingeniería Mecánica de la UPV/EHU, especialmente del grupo de Fabricación de Alto Rendimiento. También se quiere agradecer la estrecha colaboración con otras entidades, como son Ibarmia, el Instituto de Máquina Herramienta (IMH) y Tecnalia, que han participado de manera activa en la realización de este trabajo.
Referencias
[1] Kawasaki K. Manufacturing Method for large-sized bevel gears in cyclo-palloid system using multi-axis control and multi-tasking machine tool. Proceedings of international conference on gears, Munich (Germany), 2010.
[2] Gregory Hyatt, Markus Piber. A Review of New Strategies for Gear Production. CIRP International Conference on High Performance Cutting, 2014.
[3] I. Bae, V. Schirru. An Approach to Find Optimal Topological Modification to Duplicate Tooth Flank Form of the Existing Gear. Gear Solucions Magazine (www.gearsolucions.com), December 2014, pp. 34–43.
[4] J. A. Marañón. Las claves multitasking. IMHE, January/February, 386, (2012), 16-22.