Afilado de herramientas por láser
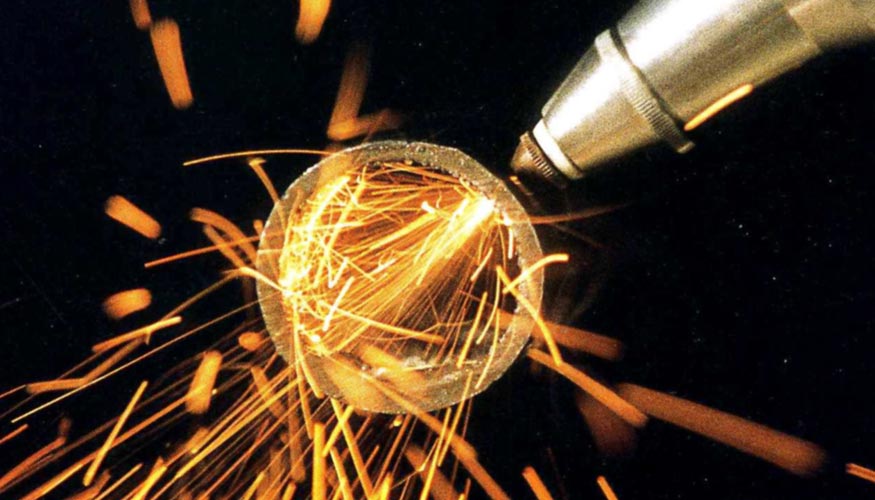
Perforación de un tubo con láser CO2.
El láser genera un haz de luz coherente tanto espacial como temporalmente. El primer láser fue el de rubí en 1960, construido por Teodoro Maiman. El láser consta de 3 elementos básicos: Una cavidad óptica resonante formada por dos espejos, uno es de alta reflectancia, y el otro conocido como acoplador, que permite la salida del rayo láser. Dentro de esta cavidad hay un medio activo ópticamente, que puede ser sólido, líquido o gaseoso, que amplifica la luz, produce la emisión estimulada de radiación.
Para esa amplificación hace falta un aporte de energía, que llamamos bombeo. El bombeo puede ser óptico o por descarga eléctrica. El medio activo absorbe la energía de bombeo y aumenta el nivel energético de una parte de los electrones a un estado cuántico excitado. Las partículas reaccionan con la luz emitiendo fotones estimulados.
El medio activo determina la longitud de onda del láser y la emisión contínua o pulsada. Solemos decir que el láser emite en una sola onda pero podemos modificarla dentro de unos límites.
Se denomina luz coherente cuando dos puntos de una onda guardan una relación de fase constante, conocido el valor instantáneo del campo eléctrico en uno de los puntos, es posible predecir el del otro. El láser de emisión continua (CO2) produce evaporación, combustión o disociación química de los materiales.
El láser visible tiene una longitud de onda entre 400 y 700 nm. Pero el láser de corte, taladrado de agujeros y soldadura opera normalmente en el infrarrojo. El más conocido y usado es el de CO2, de onda contínua, no pulsada. En nuestro caso lo mejor para el afilado de herramientas. Requiere una fuente de alimentación y un sistema de refrigeración.
El primer láser de corte apareció en 1965 para practicar agujeros en el diamante (Western Electric), y en 1970 se creó el láser de gas para cortar titanio, para la industria aeronáutica.
El láser de CO2
Fue desarrollado por Kumar Patel, de los laboratorios Bell, en 1964 y resiste hasta hoy día la competencia de otros láseres de infrarrojo. Consta de un tubo de vidrio por el cual circula una mezcla de gas, con electrodos en cada extremo, los cuales producen una descarga de alto voltaje. Es muy eficaz si observamos la relación entre la potencia de bombeo (poder de excitación) y la potencia de salida: 20%. Su longitud de onda abarca de 9,4 a 10,6 micras.
El medio amplificador es gas CO2 y nitrógeno en el que se produce una descarga eléctrica. La proporción de nitrógeno es de 10-20%.Con pequeños porcentajes de hidrógeno, helio y xenón.
En su funcionamiento ocurre la inversión de la población, un estado de un grupo de átomos y moléculas del medio activo, en el que los miembros en estado excitado son más numerosos que los miembros de menor energía. El concepto es fundamental en la ciencia del láser, necesario para el funcionamiento de un láser común.
La colisión de un electrón induce un estado excitado vibratorio en el gas nitrógeno. Como éste es una molécula homonuclear, no pierde su energía por la emisión de un fotón, y por tanto sus niveles de excitación vibratoria tienen gran periodo de vida. La transferencia de la energía de colisión entre el nitrógeno y el CO2 induce una excitación del CO2, que impulsa la inversión de población.
El gas permanece en un estado excitado, y el retorno a su estado fundamental se hace mediante las colisiones con el helio frio. Como el láser CO2 emite en el infrarrojo sus espejos son del tipo multicapa, fabricados en silicio, en molibdeno y en oro. Las ventanas y las lentes son de germanio o seleniuro de cinc. Se pueden encontrar ventanas y espejos de diamante, de buena conductividad térmica, necesaria para la alta potencia.
En el láser de CO2 tiene un espejo de transparencia al 100%, enfriado por agua, y un semiespejo transparente recubierto con seleniuro de cinc. La potencia del láser CO2 va desde varios milivatios a cientos de kW, e incluso hasta 1 GW. Y cortar láminas hasta 50 mm. En la industria la aplicación más importante es corte y soldadura. El corte por vaporización ocurre porque el láser calienta la superficie hasta el punto de ebullición y genera un agujero que va aumentando su diámetro. La soldadura requiere una potencia del láser de al menos 1,7 kW. A mayor potencia más capacidad de penetración en el material.
Para rectificar una herramienta o un disco cortante se le recubre de nanopolvos, que el láser de CO2 funde sobre el substrato. A continuación se añaden sucesivas capas para dar forma óptima a la herramienta. Se evita el oxígeno atmosférico.
La longitud de onda del infrarrojo es muy absorbida por el agua, y por eso el CO2 se usa en cirugía láser.
La ranura es la anchura del material eliminado. En el láser de CO2 la ranura varía entre 0,15 y 0,5 mm en función del espesor de la chapa. Aunque la ranura es muy pequeña, es más ancha en la parte superior del corte. Con el láser CO2 se consiguen rebordes agudos sin deshilachamientos.
El láser CO2 ofrece un corte prácticamente sin rebaba hasta un determinado espesor. El mecanizado por CO2 posibilita trabajar piezas de pequeñas dimensiones, herramientas permitiendo esquinas vivas y agujeros de pequeño tamaño, formas geométricas complejas, que no es posible obtener por procesos convencionales. Permite la creación de cavidades. La principal desventaja del corte por láser es el alto consumo energético, una eficiencia del 20%.
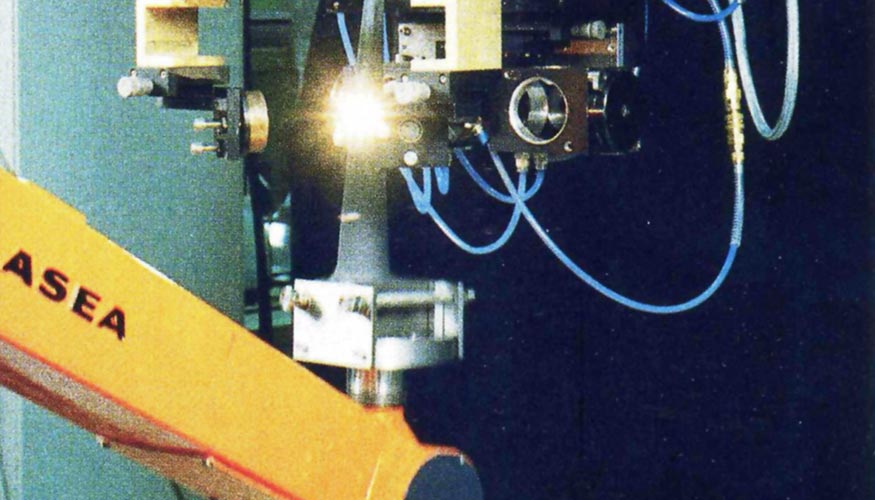
Hoja de una turbina recubierta con nanopolvo endurecida con láser CO2.
También existe el corte por plasma. El plasma es el estado en que se encuentran las estrellas por su elevada temperatura, y en la industria, el corte requiere elevar la temperatura del material hasta 20.000 °C. Como la atmósfera terrestre es transparente en el infrarrojo, el láser de CO2 se usa con fines militares de telemetría.
El ejército tiene láseres para destruir proyectiles, misiles y morteros en vuelo, que causan la fusión del material, el láser Nautilus de alta energía. En la industria las máquinas de corte láser no están sujetas a desgaste. Por supuesto el láser se usa mucho para grabar cristal y espejos.
Hay otros trabajos en la industria que no se resuelven fundiendo el material, por ej.: perforación de un túnel, afilado de herramientas y discos de corte de la máquina tuneladora, con un consumo energético no tolerable.
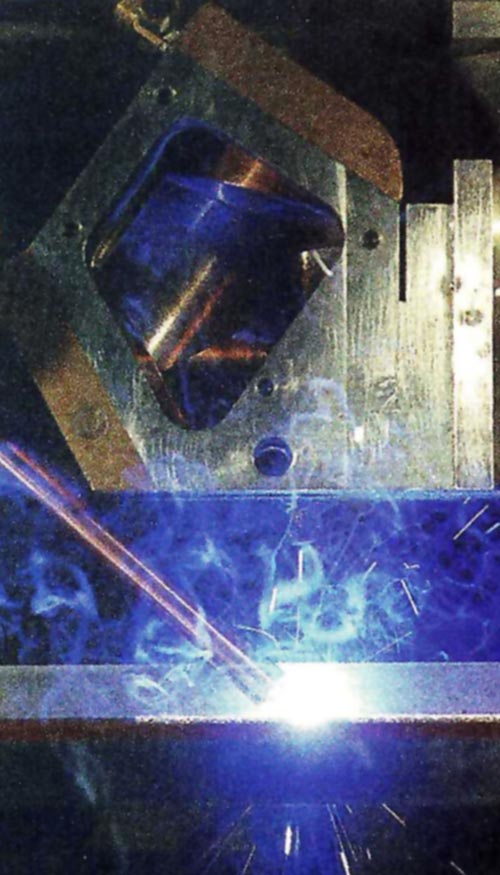
Soldadura de una chapa de aluminio de 2,5 mm a una velocidad de 6 m/min con láser CO2.
Discos de corte
Para los discos más antiguos el láser no existía. Recordemos el disco de corte reforzado con fibra de vidrio, de 36 mm. El desgaste obliga a substituir el disco con frecuencia. El problema se resolvió con el corte de diamante, un recubrimiento de polvo de diamante en los bordes del disco.
El diamante
El diamante sintético se consiguió en calidad gema en grandes tamaños y diversidad de coloraciones. Los diamantes amarillo y marrón son más económicos. En 1964 General Electric consiguió el primer diamante sintético usando el método de la cristalización del carbono a altas presiones (50-60 kbar) y temperaturas (1.300-1.600 °C) que son las condiciones de formación del diamante en el manto terrestre a profundidades de unos 200 km. Así se lograron para la industria diamantes de baja calidad para abrasivos.
Hacia 1970 se logró el primer diamante hasta 1 quilate de peso. Se logró un método para el diamante sintético sin necesidad de altas presiones y temperaturas, fue la deposición química de vapor (DQV). Como fuente de carbono se usa gas metano, que se mezcla con hidrógeno, y se ioniza mediante el plasma. Los iones de carbono se depositan sobre una superficie creando una capa muy fina de diamante. Se logró la creación de nanodiamantes, y la deposición de esas capas tiene muchas aplicaciones. En el año 2005 apareció la primera Empresa que comercializaba el producto. En España el Instituto Gemológico Español estudia esos nanocristales de carbono, DQV. El láser funde el nanodiamante sobre el substrato metálico, una aleación especial de aluminio. Y se ha llegado al límite en tecnologías de afilado y electroerosión. Esos límites pueden superarse, para producir contornos de herramientas, la formación de cavidades en 3D, o rompe virutas.
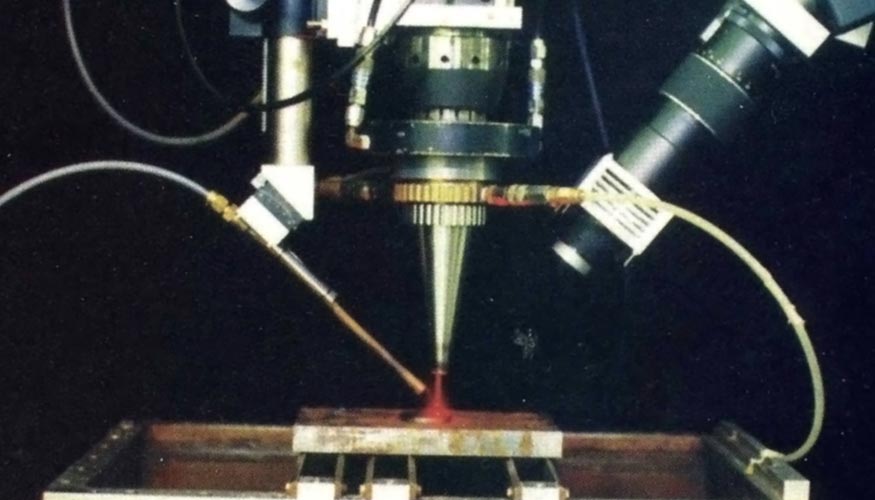
Láser CO2 corta una chapa de titanio. A la izquierda un tubo suministra nitrógeno.
Para el sector del automóvil tenemos el NanoShield, un recubrimiento de nanopolvo de vidrio, de partículas muy duras, que recubren la carrocería. Repelen fuertemente el agua y la humedad y evitan que se depositen sobre el metal. El recubrimiento dura un año El vidrio es como un líquido sobreenfriado, con viscosidad muy elevada, que impide el desarrollo de la estructura cristalina. El vidrio es una mezcla de silicatos preparados por fusión y posterior enfriamiento rápido de mezclas que incluyen óxidos de sílice, calcio, sodio y boro.
El disco cortante de la tuneladora
En el medio urbano el túnel substituye al puente. El túnel más conocido es tal vez el del Canal de la Mancha que une Francia con Inglaterra. La máquina tuneladora tiene una cabeza cilíndrica, con diámetros hasta 10 m, una placa circular giratoria con decenas de discos cortantes, 50 o más, la corona, que pulverizan la piedra. El desgaste del disco es tan rápido, que obliga a substituir el disco con frecuencia, cada varios días según el tipo de roca. Un mantenimiento costoso en tiempo y dinero de una máquina de más de 100 toneladas. El disco recubierto con nanopolvos permite mayor velocidad de la tuneladora.
Importa alargar la vida del disco de corte, con un recubrimiento el más duro posible. Tengamos presente que el disco durante su rotación contra la roca experimenta una combinación de tensiones y compresiones. Pero gracias al láser y su economía y los nanopolvos sobre el disco, hemos extendido la duración del disco hasta un 20%.
No es lo mismo que el nanopolvo sea amorfo o cristalino, que fundirá el láser con el substrato del disco, y formará una unión metalúrgica. Es un éxito el SAM, Structurally Amorphous Materials Program, de Oak Ridge National Laboratory, EE UU. Si usamos nanocristales, como polvo de recubrimiento, en la aleación cristalina los átomos forman una red cristalina tridimensional, que permite que la red se ensanche o comprima, se deforme el metal. Al contrario, en la estructura amorfa del material, por ej.: una aleación amorfa de hierro, tiene la estructura atómica desordenada del vidrio, es más dura y resistente al desgaste.
El SAM ha desarrollado esa aleación amorfa, excelente para la tuneladora, por sus características de dureza, ductilidad y resistencia al desgaste. Para producir la aleación se usa la atomización del gas, y forma parte del recubrimiento NanoShield. A esa técnica de afilamiento de herramienta llamamos ‘manufactura aditiva’, en vez de arrancar material para dar a la herramienta la forma que deseamos con el sistema convencional. Con el nanopolvo SAM y el láser resolvemos el problema. La adición de un polímero mantiene el polo Sam sobre el disco cortante, mientras el láser va fundiendo el recubrimiento. Pero podemos prescindir del polímero, si depositamos el polvo Sam con gas argón, y el polvo se solidifica sobre el borde del disco.
El polvo se aplica sobre el disco de corte formando tiras, no en forma continua, y permite la distorsión o deformación del substrato metálico. Equivale a las juntas de expansión en el cemento, que se adapta a las tensiones térmicas. Para proteger el disco contra el desgaste basta que el espesor del recubrimiento sea de 0,1 a 0,7 mm. Ese recubrimiento puede tener una dureza superior a la del acero, hasta 7 veces, sin afectar a la elasticidad del substrato. Colorado School of Mines, EE UU. ha experimentado tal recubrimiento para cortar granito (Complejo de cuarzo, feldespato y mica), simulando las condiciones del corte de roca. Después de 100 cortes no se ha apreciado deterioro.
El recubrimiento de nanopolvo SAM y láser requiere una máquina de pequeñas dimensiones, para afilado de herramientas.
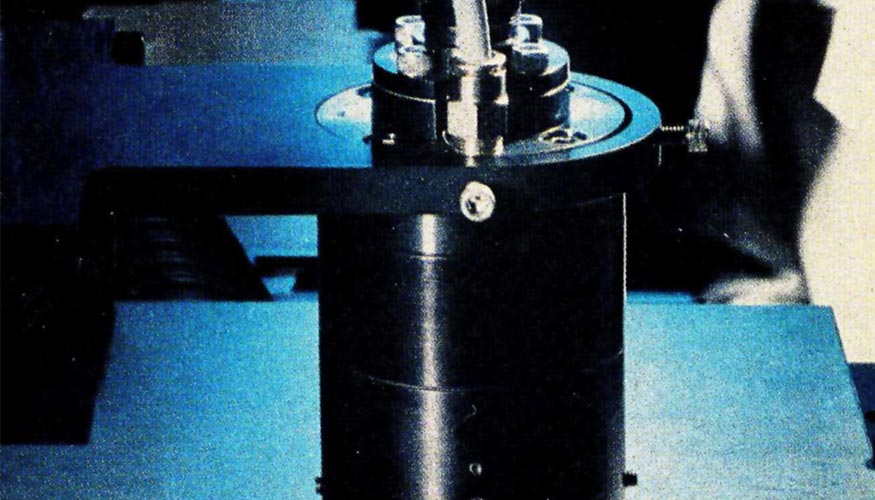
El láser Nd:YAG en 1992 ya compite con el láser CO2 en perforar chapa de acero.
Referencias
- Basting, C. Excimer laser technology. 2nd International Symposium on Laser precision microfabrication.
- Duarte F.J. Tunable laser handbook, New York 1995.
- Martin L.L.Laser emission in ND3 doped barium titanium-silicate microespheres under wave pumping.iop.science. 2007.
- Onaik-artículos de informática, Láser. 2009.
- Podesta, R. Understanding the properties of matter. CRC Press 2008.