La mejora en el día a día, clave para la cuenta de resultados en la producción de los componentes del motor
El tráfico aéreo está creciendo a un ritmo del 4-5% por año, tanto en el transporte de mercancías como de pasajeros, con unas previsiones para los próximos 15 años de prácticamente el doble del tráfico actual. Las previsiones de mercado tanto de Airbus como de Boeing para el periodo de 2012 – 2032 son de duplicar la flota de aviones de pasajeros. En el caso de Airbus, el crecimiento mayor lo espera en sus aviones de gran capacidad, de simple y doble pasillo para tráfico internacional. En el caso de Boeing, su estrategia de mercado se centra en aviones de pasillo único de varios tamaños para vuelos regionales. Este crecimiento en la fabricación de aeronaves revierte directamente en los grandes motoristas como Rolls-Royce o GE Aviation. Por otro lado, las necesidades de mantenimiento y reparación de los motores también experimentarán un crecimiento relevante.
Otro de los retos, además de satisfacer la demanda del mercado, se encuentra en cumplir con las normativas medioambientales cada vez más restrictivas. Las próximas generaciones de motores deben proporcionar mayor empuje con un consumo más eficiente de combustible, reduciéndolo en más de un 15%. En lo que respecta a emisiones de gases contaminantes, se fijan como metas para el 2050 la reducción del 75% de emisiones de CO2 y del 90% las de NOx, así como reducir las emisiones acústicas en un 65% en relación al año 2000. La posibilidad de alcanzar con éxito estas metas reside en gran medida en el aumento de la temperatura de funcionamiento de los nuevos motores, diseñando elementos y empleando materiales capaces de soportar esas altas temperaturas.
Cierta clase de materiales poseen capacidad de mantener sus propiedades mecánicas a altas temperaturas, estos son conocidos como materiales termorresistentes. El uso de estos materiales es múltiple y variado, pero uno de los ejemplos más significativos de su aplicación se encuentra en las turbinas, cohetes e intercambiadores de calor. Para estas aplicaciones, las características de rendimiento están limitadas por las condiciones de trabajo que pueden tolerar las aleaciones utilizadas.
Entre las características principales que debe tener un material termorresistente se encuentra la capacidad de soportar esfuerzos a temperaturas de funcionamiento cercanas al punto de fusión. Si la temperatura de operación se denota como Tt y el punto de fusión como Tm, la relación Tt/Tm debe ser mayor que 0,6 para que el material sea considerado apto. A modo de ejemplo, una superaleación de base níquel con una temperatura de fusión entorno a los 1.455 °C, cuya que temperatura de trabajo es de 1.000 °C, tiene una relación de temperaturas de 0,75, por lo que es posible clasificarla como un material termorresistente.
Una segunda característica es la resistencia a la degradación mecánica durante largos periodos de tiempo. Para aplicaciones a alta temperatura, es necesario tener en cuenta el comportamiento del material cuando está sometido a cargas constantes durante un lapso de tiempo prolongado. En tales circunstancias, el material puede experimentar una deformación continua mientras la aplicación de la carga se mantiene constante, a esta deformación se denomina fluencia o 'creep'. La deformación experimentada puede llegar hasta el punto de incapacitar el correcto funcionamiento de componente. Este tipo de deformaciones pueden ser imperceptibles, pero crecen durante todo el ciclo de vida de la pieza y llevan a la rotura, aunque no se experimente un incremento en la carga de trabajo. Además, se deben mantener en el tiempo otras propiedades mecánicas del material como son la tensión de fluencia, resistencia a la tracción y tensión última o de fractura.
Otra característica de este tipo de aleaciones es la capacidad de soportar ambientes de trabajo agresivos. Por ejemplo, soportar los gases calientes generados en el proceso de combustión de un motor aeronáutico, los cuales son altamente corrosivos. Además, las altas temperaturas de trabajo favorecen los procesos de oxidación, ocasionando la degradación de la superficie del componente y por tanto reduciendo la su vida útil.
Las superaleaciones como materiales resistentes a alta temperatura
Las superaleaciones de base níquel se han convertido en la elección por excelencia cuando el material debe presentar buena resistencia a cargas estáticas, fatiga y fluencia en componentes diseñados para aplicaciones con alta temperatura de funcionamiento. Estas aleaciones son consideradas cuando las temperaturas de funcionamiento son próximas a los 800 °C o superiores.
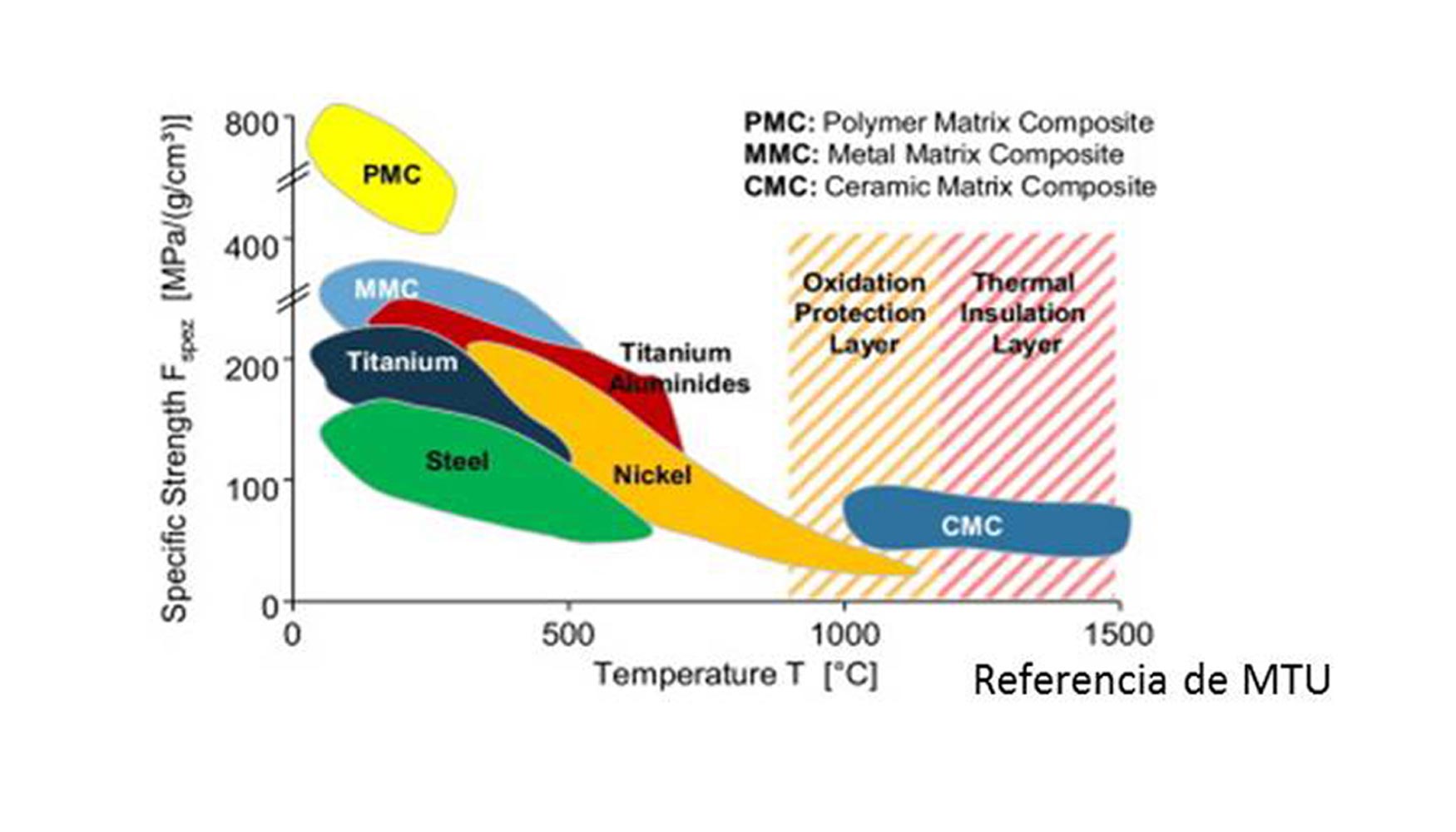
Cuando la temperatura de trabajo se encuentra por debajo de los 700 °C, son las aleaciones de Titanio los materiales a tener en cuenta. Por encima de esta temperatura presentan una escasa resistencia a la oxidación. Una de las ventajas más sustanciales de la aplicación de estas aleaciones es la reducción del peso del componente, ya que la densidad de estos materiales es significativamente inferior a las aleaciones de base níquel.
Uno de los sectores en el que el empleo de superaleaciones es más significativo es el aeronáutico. Estos materiales se emplean para la fabricación de partes estructurales de la aeronave, como es el caso de las aleaciones de titanio. La baja densidad del material en relación a sus propiedades mecánicas es una de las características más apreciadas a la hora del diseño. La reducción de peso de los componentes de la aeronave es un reto constate en el diseño. Por otro lado, las aleaciones de base titanio también son empleadas en ciertos componentes del motor, allí donde las temperaturas de trabajo no son excesivamente altas. Es aquí, en el motor, donde el empleo de superaleaciones cobra mayor relevancia. Siendo por excelencia uno de los sectores que mayores esfuerzos invierte en la investigación de estos materiales y cuya incorporación al diseño sirven para posibilitar motores más eficientes, con mayores potencias de empuje y consumos más reducidos.
En la siguiente imagen se muestra la sección de un motor aeronáutico, en concreto un turborreactor de doble flujo o turbofan. Se trata del modelo Trent XWB, uno de los últimos desarrollos de Rolls-Royce. El motor se divide en una serie de secciones, cada una de ellas con una función específica' y unas características de funcionamiento propias. Así pues, en el extremo izquierdo, se encuentra el fan, encargado de introducir el aire exterior. La temperatura de este elemento no es excesiva, por lo que es posible el empleo de materiales compuestos para fabricar los álabes del fan con excepción del borde de ataque que está realizado en titanio ya que esta parte del álabe debe ser capaz de resistir la erosión y posibles impactos. El empleo de materiales compuestos ayuda a reducir tanto el coste del componente como el peso del conjunto motor. En el diseño de un turborreactor de flujo doble, como es el caso del Trent XWB, el aire de entrada se divide en dos. Una parte circula por el exterior del motor (by-pass), volviéndose a encontrar con los gases generados en la combustión a la salida de la turbina. Este flujo de aire genera una cantidad de empuje considerable sin necesidad de combustión, lo que permite que el porcentaje de empuje debido a los gases de combustión pueda ser menor, haciendo posible así reducir las dimensiones del motor mejorando los consumos de combustible. Por este motivo, en los nuevos diseños se tiende a incrementar el porcentaje de by-pass, aumentando el diámetro del fan e introduciendo el concepto de engranajes en la transmisión del movimiento (Gear Turbo Fan). Además, el aire que circula por el 'by-pass' ayuda a la refrigeración de las partes calientes mediante de absorción de calor.
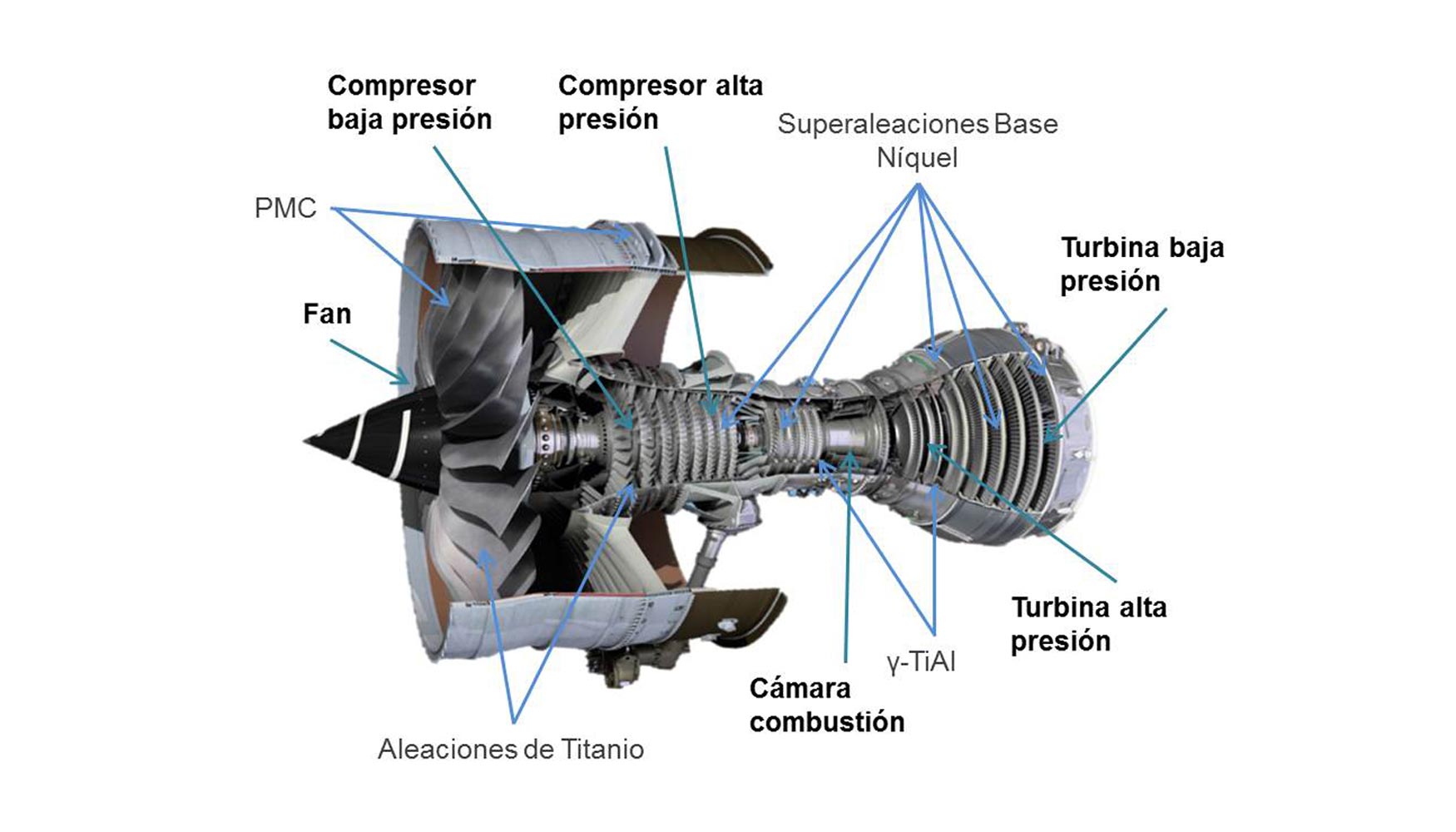
El flujo de aire primario acaba en el compresor, constituido por discos rotativos y estáticos en los que se alojan una serie de álabes que comprimen el aire aumentando su presión. En las primeras etapas de compresión es posible empelar aleaciones de titanio, mientras que en las últimas se suelen emplear aleaciones de base níquel. Tras la etapa de compresión el aire pasa a la cámara de combustión, donde se mezcla con el combustible y se produce el encendido. Se trata de uno de los elementos más calientes del motor, para soportar las condiciones de trabajo normalmente el material empleado es una superaleación de base cobalto ya que presentan buena soldabilidad. Además, se proporcionan recubrimientos que actúan de barrera térmica entre la zona caliente y el elemento metálico. A continuación los gases calientes pasan a la etapa de turbina donde se produce la expansión. Es en esta etapa donde se extrae el trabajo mecánico para accionar la etapa de compresión, por lo que las dos etapas están unidas al mismo eje que trasmite el par necesario. El flujo de gases a la salida de la turbina es considerablemente superior al exterior, lo que proporciona un segundo empuje.
El punto crítico a la hora del diseño de un motor de turbina de gas se encuentra en la temperatura de los gases de combustión a la entrada de la turbina. Se trata del punto con la mayor temperatura, ya que a partir de ese punto los gases se expanden generando trabajo mecánico y reduciendo su temperatura a medida que pasan por las diferentes etapas de la turbina. Son las superaleaciones de base níquel las que en mayor porcentaje se emplean en la zona de turbina. En este caso también es necesario emplear en ciertas zonas recubrimientos cerámicos que protejan el núcleo metálico del elemento, permitiendo así que la temperatura de trabajo pueda ser superior a los límites del material. En los nuevos motores en desarrollo, las aleaciones Gamma-TiAl encuentran su elemento de aplicación en los álabes estáticos.
Cuando mayor es la temperatura de los gases a la entrada de la turbina, mayor será el rendimiento del motor. La temperatura de entrada a la turbina varia en gran medida durante el ciclo de vuelo de una aeronave, siendo más elevada durante la fase de despegue y ascenso a altitud de crucero. Es por este motivo por lo que el sector aeronáutico invierte grandes esfuerzos en la investigación de superaleaciones capaces de soportar temperaturas cada vez más elevadas con las que realizar el diseño de estos componentes más ligeros. Un ejemplo son los materiales monocristalinos, que presentan mejor comportamiento a fluencia que un material policristalino, por lo que su temperatura de trabajo puede ser mayor. También, los composites de matriz metálica (MMC) y composites metal cerámicos (CMC), así como los recubrimientos que adicionalmente proporcionan una barrera térmica para los elementos realizados en estos materiales.
Existe una relación de materiales de aplicación por excelencia en la mayoría de las turbomáquinas, como pueden ser:
- Aleaciones de acero: X22CrMoV211; X12CrNiWTiB16-13
- Aleaciones de base Titanio: Ti–6Al–4V (Ti64/Ti6Al4V); Ti–6Al–2Sn–4Zr–2Mo–0.1Si (Ti6242); Ti6246; Ti–5Al–2Sn–2Zr–4Mo–4Cr (Ti17)
- Gamma TiAl (γ-TiAl): TNM; GE 48-2-2; 45 XD
- Superaleaciones de base níquel: Inconel 718 (In718); IN100; Inconel 738; Inconel 939; MAR-M002; MAR-M247; Waspalloy; Udimet 720; Nimonic 105; Nimonic 713; Rene88; RR1000; CMSX4; LEK94
- Composites de matriz cerámica (CMC): SiC; SiBN3C; Al2O3; ZrO2;
El empleo de estos materiales acarrea serios problemas a la hora de realizar las operaciones de mecanizado. La mayoría de estos materiales presentan una baja maquinabilidad. Su mecanizado por métodos tradicionales representa un reto, a menudo se emplean bajas tasas de arranque, con velocidades de corte muy inferiores a las empleadas en otros materiales, elevadas fuerzas de corte, alto coste en herramientas que experimentan un desgaste muy rápido lo que hace que pierdan su capacidad óptima de corte en muy poco tiempo. Por otro lado, si el estado de la herramienta no es el óptimo, se puede ver afectada la integridad superficial de las piezas después del proceso de mecanizado, siendo este aspecto de vital importancia cuando de se trata de componentes cuyo destino final es formar parte de un motor aeronáutico.
Herramientas para el mecanizado superaleaciones
Entre los diferentes factores involucrados en las operaciones de mecanizado, la herramienta de corte, aunque pequeña y relativamente barata, es uno de los puntos más críticos. Para el mecanizado de superaleaciones las herramientas deben cumplir una serie de requisitos básicos como son la resistencia al desgaste, alta resistencia mecánica y tenacidad, capacidad de soportar choques térmicos, mantener su dureza así como una estabilidad química adecuada a alta temperatura. Es posible distinguir tres grandes grupos de materiales de herramientas que son capaces de satisfacer los requisitos mencionados: cerámicas, CBN y metal duro. Dentro de cada uno de estos materiales genéricos existe gran variedad de alternativas, pero no todas aplicables al mecanizado de superaleaciones. Con objeto de identificar dentro de cada fabricante de herramientas los productos aptos para ser empleados existe la denominación ISO S, enfocadas a materiales de base níquel y aleaciones de titanio.
Es posible emplear herramientas cerámicas con velocidades de corte muy altas, lo que permite reducir significativamente los tiempos de mecanizado, entre 3 y 5 veces más rápido si se compara con herramientas de metal duro. La dureza de estos materiales es muy superior a la de las piezas a mecanizar y su coeficiente de fricción es inferior al del metal duro. Por debajo de 1.200 °C de funcionamiento mantienen su estabilidad química y evitan fenómenos de adhesión. Tienen una buena resistencia a la abrasión pero su tenacidad no es muy alta. El proceso de mecanizado debe ser lo más uniforme posible, sin cortes interrumpidos y eligiendo correctamente la preparación del filo de corte de la herramienta.
Las herramientas de CBN son capaces de soportar temperaturas de trabajo cercanas a los 1.400 °C manteniendo buena estabilidad química. Es un material de gran dureza y su empleo está más extendido para el mecanizado de aceros templados. El empleo de estas herramientas representa una alternativa al rectificado cuando se trata de operaciones de acabado de piezas con geometría compleja. El empleo de herramientas de CBN para el mecanizado de superaleaciones no es un proceso extendido por causas como el coste de la herramienta o falta de tenacidad del material que bajo grandes cargas de mecanizado puede llegar a provocar la rotura o astillado del filo de corte. Se realizan grandes esfuerzos en investigación dirigidos a mejorar este tipo de materiales, sobre todo desde el punto de vista de tenacidad y nuevas geometrías en el filo de corte que previenen la rotura.
El uso de herramientas de metal duro para el mecanizado de superaleaciones de base níquel está asociado al empleo de condiciones de corte muy conservadoras. La estabilidad térmica del metal duro es relativamente baja. Es necesario trabaja con condiciones de corte más bajas que cuando se emplean herramientas de CBN o cerámicas. En una operación de torneado con velocidad de corte de 30m/min, es posible superar los 1.000 °C en la zona de contacto entre pieza y herramienta. A esta temperatura el metal duro pierde capacidad de resistir cargas mecánicas lo que lleva al fallo de la herramienta por deformación plástica del filo de corte. Además, posee una pobre estabilidad química a alta temperatura, se desencadenan procesos de difusión que perjudican la integridad de la herramienta.
El empleo de recubrimientos permite incrementar el rendimiento de las herramientas de metal duro, a través de un aumento de las condiciones de corte y prolongando la vida útil de la herramienta. En la actualidad, el 99% de las herramientas del mercado, independientemente del material que vayan a mecanizar, llevan algún tipo de recubrimiento que mejora su capacidad para mecanizar. Por lo general el recubrimiento representa una capa de mayor dureza que el material base, por lo que se mejora la resistencia a la abrasión. También es posible reducir la fricción entre herramienta y pieza, por lo que se disminuye la temperatura del proceso de corte. Los esfuerzos de corte con una herramienta recubierta son inferiores a los de la misma herramienta sin recubrir Tienen mejores propiedades a alta temperatura que el metal duro, ofreciendo mayor resistencia a procesos de difusión, oxidación y manteniendo su nivel de dureza.
La selección del material de la herramienta y los parámetros de corte empleados en la producción de componentes de turbomaquinaria, están condicionados por las restricciones del material de trabajo y su maquinabilidad. Además otros requisitos como la calidad e integridad superficial a obtener han de ser tomados en consideración. Las limitaciones impuestas por otros factores del proceso como son la máquina herramienta en la que se va a ejecutar el mecanizado, la geometría de la pieza, su rigidez, el sistema de amarre o el diseño de la herramienta, condicionan las condiciones de corte a emplear.
Para obtener buenos resultados en las operaciones de desbaste hay que conseguir un buen equilibrio entre las fuerzas de corte que genera la geometría de la herramienta seleccionada y la dinámica del conjunto frente a los parámetros de mecanizado impuestos. El empleo de materiales cerámicos en las herramientas, como son las cerámicas de alúmina reforzadas con filamentos de CSi, permiten alcanzar velocidades de corte mayores de 250m/min en el mecanizado de superaleaciones de base níquel. El empleo de nuevas herramientas cerámicas con avanzados recubrimientos posibilita alcanzar velocidades de corte cercanas a los 600m/min. La velocidad de corte en operaciones de desbaste es consecuencia de un conjunto de criterios, principalmente es un equilibrio entre el número de herramientas necesarias para hacer toda la operación, el volumen de material a eliminar y el estado de desgaste de las herramientas que se puede asumir sin perjudicar el material de pieza. Por lo general se evita llegar a un desgaste excesivo que pueda ocasionar la rotura del filo de la herramienta, o condiciones que desemboquen superficies no deseables en la pieza o deformaciones inducidas por el abuso en las condiciones de desbaste. Por lo general, para conservar el buen estado de la herramienta cerámica y reducir el riesgo de roturas, se aumenta la velocidad de corte y se reduce la velocidad de avance. De esta manera se mantiene constate la tasa de arranque de material.
En las operaciones de acabado en piezas de superaleaciones de base níquel es necesario emplear herramientas con una excelente resistencia al desgaste. Aun así, es necesario reducir la velocidad de corte para conservar la integridad del filo de corte. La constante investigación en nuevos recubrimientos y metales duros más resistentes permiten optimizar las condiciones de corte en operaciones de acabado. Por lo general, un recubrimiento multicapa en combinación con un metal duro con grano ultra-fino proporciona un mayor rendimiento que una herramienta de metal duro sin recubrir. Es posible duplicar la velocidad de corte, lo que conduce a una mejora significativa en los tiempos de mecanizado y consecuentemente en la productividad. Nuevos desarrollos de herramientas de PCBN permiten alcanzar altas velocidades de corte en algunas superaleaciones de base níquel. Es posible alcanzar velocidades de corte próximas los 300m/min. Se trata de herramientas de alto coste, pero a cambio proporcionan un comportamiento frente al desgaste estable y predecible, mayor tiempo de vida y tiempos de producción significativamente menores comparados con las herramientas de metal duro. Al mismo tiempo es posible reducir el número de herramientas empleadas y mejorar los tiempos improductivos.
Mecanismos de desgaste
La temperatura alcanzada en el proceso de corte de superaleaciones es la principal causa que provoca el desgaste de la herramienta. Al tratarse de un material termorresistente un porcentaje muy pequeño de la energía del proceso es absorbida por la pieza o la viruta en forma de calor, de forma que el mayor porcentaje es evacuado a través de la herramienta de corte.
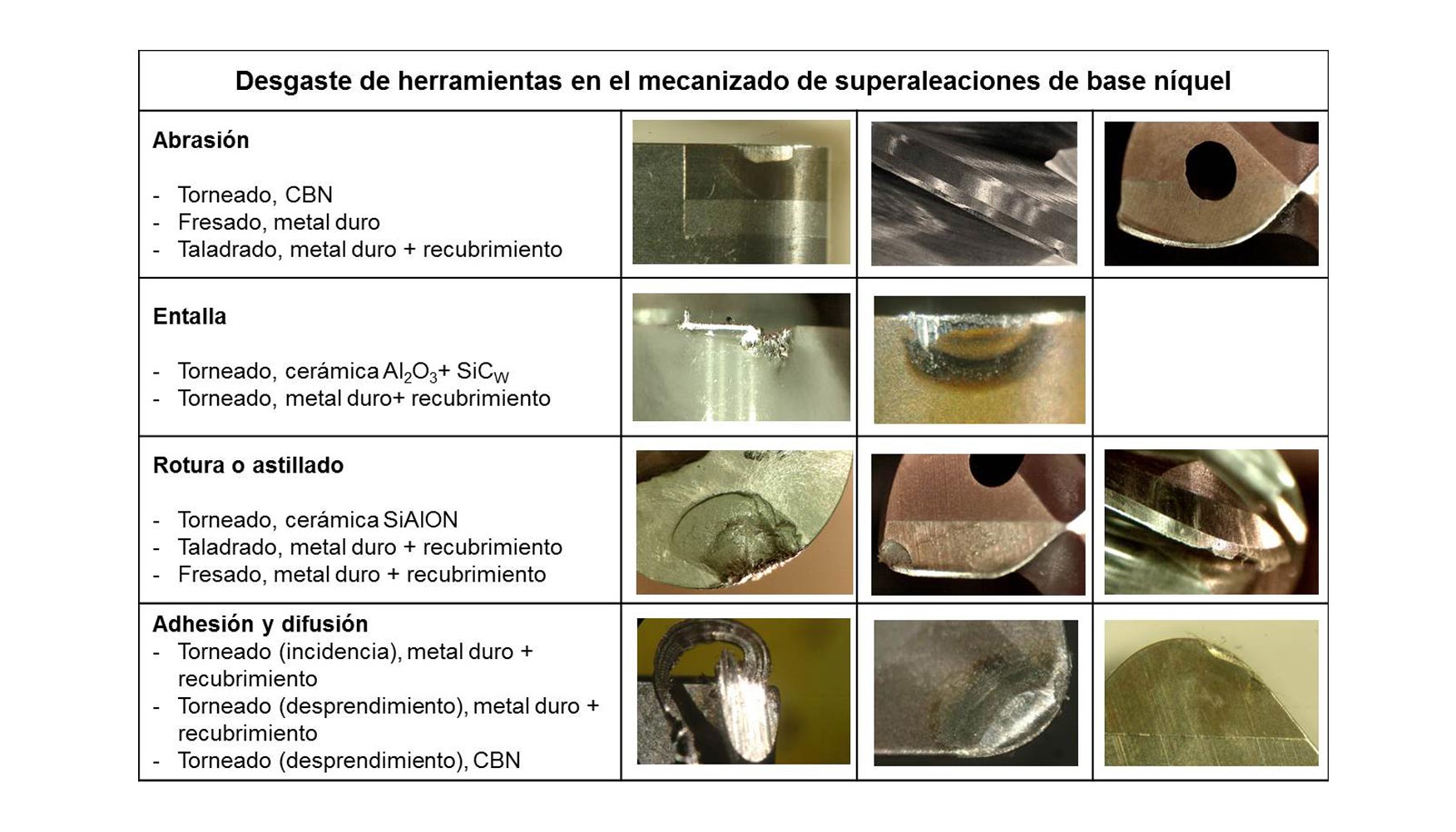
Las herramientas de corte experimentan desgaste de tipo mecánico, por adhesión, difusión y oxidación, siendo estos procesos de desgaste más severos cuando se trata de superaleaciones de base níquel, acortando la vida útil de la herramienta. Los mecanismos de desgaste que experimenta una herramienta son simultáneos, aunque normalmente alguno de ellos es dominante sobre los demás, puesto que siempre hay algún aspecto de la herramienta que la hace más sensible a un mecanismo de desgaste que a otro. Por lo general se considera que el desgaste puede ser explicado por tres tipos de interacciones entre la herramienta y la pieza, una de tipo mecánico, por abrasión; otra de tipo termodinámico, por la temperatura alcanzada en el corte y por último de tipo químico, por difusión.
El daño experimentado en la superficie de la herramienta está relacionado con un desgaste por abrasión, se produce como consecuencia del movimiento relativo entre la herramienta y las inclusiones de alta dureza existentes en la superficie de la pieza. También hay que tener en cuenta que las superaleaciones de base níquel se endurecen como consecuencia de la deformación plástica ocasionando, sobre todo en operaciones de torneado, la aparición de desgaste por entalla en la región de la herramienta que coincide con la profundidad de corte.
La existencia de fenómenos de adhesión entre herramienta y material de pieza es consecuencia de la deformación plástica bajo presión y temperatura suficiente como para ocasionar un proceso de soldadura en frío. Parte del material de pieza queda soldado a la superficie de la herramienta formándose una capa de material adherido. Existe un movimiento relativo entre el material de la pieza y la herramienta, como consecuencia del proceso de corte, en este proceso la capa adherida es arrastrada por el flujo de material eliminado de la pieza en forma de viruta. Las uniones soldadas no se revierten en este proceso, sino que al eliminar la capa adherida arrastra con ella parte de la herramienta.
Otro de los mecanismos de desgaste que tienen lugar es el de difusión. Cuando se mecanizan superaleaciones de base níquel, la temperatura alcanzada en la zona de corte es muy alta, convirtiendo las zonas de contacto de herramienta con pieza en un medio propicio para que el proceso de difusión tenga lugar. La velocidad a la que se produce la difusión dependerá tanto de la temperatura alcanzada como de la composición química de herramienta y pieza. La velocidad de corte empleada para el mecanizado de este tipo de aleaciones suele ser relativamente baja, en comparación con otros materiales, con objeto de mantener controlada la temperatura alcanzada en el proceso y evitar así el fenómeno de difusión en lo posible. En concreto, cuando de herramientas de metal duro se trata, el Co presente en el sustrato de la herramienta es el que con mayor facilidad se pierde por difusión, debilitando las uniones de los carburos. También se observan problemas de difusión cuando se emplean herramientas cerámicas, aunque el fenómeno de difusión en estos materiales se produce a mayores temperaturas, permitiendo aumentar la velocidad de corte del proceso. Así pues el desgaste en forma de cráter que se observa en la cara de desprendimiento de las herramientas puede ser achacado en gran medida a un fenómeno de difusión.
El desgaste por rotura o microfracturas en la herramienta es un modo de desgaste más frecuente en las operaciones de fresado. Los esfuerzos de corte alcanzados cuando se mecanizan superaleaciones de base níquel son aproximadamente el doble que las obtenidas en aleaciones de acero bajo las mismas condiciones de corte. Los esfuerzos de corte tienden a deformar el filo de la herramienta, favoreciendo de esta manera la rotura del filo por microfracturas o astillado, especialmente en las operaciones de corte interrumpido.
Sistemas de refrigeración y lubricación
El empleo de un sistema de refrigeración eficiente, capaz de eliminar la mayor parte del calor generado en la zona de corte, es uno de los factores clave para prevenir o minimizar el desgaste de la herramienta cuando se mecanizan superaleaciones. El empleo de líquidos refrigerantes permite intervenir en la zona de contacto de la viruta caliente con la herramienta, influyendo en la reducción de formación de grietas en el filo y minimizado la microfracturas durante el mecanizado. Si la eliminación de calor no se realiza de manera constante se producirá la rotura de la herramienta como consecuencia de un proceso de fatiga térmica. La herramienta está sometida a un proceso continuo de expansión y contracción, lo que favorece la formación de grietas y su propagación hasta alcanzar la rotura. Una solución se encuentra en el material a emplear en la fabricación de la herramienta, cuanto mayor sea su coeficiente de dilatación térmica se llegará a fin de vida sin que este proceso tenga consecuencias negativas.
Otra vía de mejora se encuentra en el sistema de refrigeración mediante la introducción de un caudal constate a la zona a refrigerar, a mayor velocidad y de manera muy precisa. La refrigeración a alta presión presenta ventajas a la hora de evacuar el calor generado en el corte, tanto en la cara de desprendimiento como de incidencia, por lo que es posible incrementar la velocidad de corte empleada en el mecanizado de estos materiales. Además, la refrigeración actúa como lubricante de las zonas de contacto, disminuyendo la componente de la fuerza de corte asociada a la fricción, en definitiva aumentando lo vida de la herramienta. El diseño de salidas de refrigeración en los portaherramientas que permitan llevar un flujo coherente de líquido a zonas muy concretas de la herramienta, representa un concepto en el que se ha introducido grandes mejoras en los últimos años. La correcta orientación del líquido refrigerante a la cara de incidencia permite realizar un mejor control de la viruta, llegando incluso a fraccionar la viruta. La introducción de esta técnica en el proceso productivo ha sido lenta ya que en un principio suponía sistemas adicionales costosos, la forma de llevar la refrigeración hasta la herramienta era engorrosa, incluso el carenado de las máquinas no estaba preparado para soportar las consecuencias de emplear refrigerante a alta presión. El diseño de la máquina debe contemplar la manera de evacuar las partículas en suspensión de líquido refrigerante, en forma de aerosol, que se produce al incidir el chorro a alta velocidad contra una superficie sólida. Se genera un flujo de ventilación forzado mediante la incorporación de sistemas de extracción de humos y vapores, que liberan la atmosfera de las partículas líquidas retornándolas al depósito de taladrina. Además, la ventaja de este sistema de refrigeración es que permite aumentar la velocidad de corte, pero las máquinas existentes cuando esta técnica se lanzó al mercado no era capaces de proporcionar condiciones de alta velocidad de mecanizado. Técnicamente esos inconvenientes están prácticamente superados por lo que su aplicación industrial es una realidad.
El empleo de líquidos refrigerantes proporciona ventajas en el proceso de mecanizado; en lo que respecta a lubricación, la refrigeración previene la oxidación de la pieza. También tiene una serie de inconvenientes, sobre todo medioambientales. Es necesario realizar una correcta gestión de estos líquidos como residuos contaminantes, siendo varios los puntos de salida a controlar. La viruta que se genera en el proceso de mecanizado arrastra un porcentaje de estos líquidos, por lo que es necesario realizar una operación de secado antes de poder gestionar la viruta como residuo sólido. Otro porcentaje del líquido refrigerante puede salir del circuito de la máquina a través de las piezas mecanizadas, debiendo poner medidas de contención en el punto de almacenaje que controlen los posibles vertidos incontrolados. Por otro lado, en función de los requisitos de la pieza, puede ser necesario introducir un ciclo de limpieza para eliminar los restos de estos líquidos de la superficie, ya que pueden influir negativamente en los sucesivos procesos. Estos inconvenientes suponen un sobre coste por el empleo de líquidos refrigerantes, si a esto se le añade que la legislación medioambiental es cada vez más estricta, da como resultado la necesidad de introducir nuevos sistemas de refrigeración que penalicen en menor medida al proceso productivo, como por ejemplo sistemas MQL (minimal quantity lubrication) o refrigeración criogénica.
El empleo de sistemas de MQL reduce en gran medida el volumen de líquido refrigerante que se emplea en el proceso de corte, pasando de emplear unidades de l/min a ml/h. De forma muy general, un sistema de refrigeración y lubricación MQL se basa en llevar pequeñas gotas de aceite a la zona de corte portadas por una corriente de aire. Una línea de investigación en la que se invierten grandes esfuerzos consiste en la aplicación de aceites vegetales mediante esta técnica, identificando el tipo de aceite idóneo para cada proceso de mecanizado. La introducción de aceites vegetales o biodegradables proporciona grandes ventajas desde el punto de vista medioambiental.
Existen varios métodos para generar el aerosol, por ejemplo Steidle conduce de manera separada, a través de dos tuberías coaxiales, el aceite y el aire hasta la punta de la lanza de refrigeración. En este punto la corriente de aire arrastra a la gota de aceite fraccionándola en múltiples gotas de menor diámetro, este método permite su aplicación de manera exterior. Si se desea aplicar este sistema a herramientas con refrigeración interna, existen otros equipos en el mercado como los del fabricante SKF que generan la mezcla de aire a presión y gotas de aceite en un depósito previamente a su conducción a través de la tubería correspondiente. La aplicación de cualquiera de los dos métodos, en comparación con la refrigeración convencional, supone una reducción del espacio en planta ocupado por los sistemas de bombeo, depósito de taladrina, etc.
El empleo de una corriente de aire a alta velocidad y el pequeño diámetro de las gotas de aceite permite que se alcance la zona de corte de manera precisa, al igual que ocurría con la refrigeración a alta presión. En este caso, la refrigeración es consecuencia de la evaporación de las gotas de aceite al entrar en contacto con las zonas calientes, siendo una refrigeración de alta eficiencia. Si el flujo de aire y aceite llega de manera correcta a la zona de corte es posible optimizar la vida de la herramienta, reducir fuerzas de corte y mejorar rugosidad superficial.
La aplicación del MQL como sistema de lubricación y refrigeración para el mecanizado de superaleaciones de base níquel reporta buenos resultados en lo que respecta a la vida de herramienta. Es posible igualar o mejorar los resultados obtenidos empleando sistemas de refrigeración convencional. Algunos casos prácticos de aplicación son por ejemplo las operaciones de torneado de piezas de Inconel 718 con herramientas de metal duro recubiertas. Cuando las condiciones de corte son de acabado, la zona de contacto es reducida y se genera el calor de forma muy localizada. Si en este caso se emplea un portaherramientas que proyecte las gotas de aceite tanto en la cara de desprendimiento como de incidencia es posible obtener resultados satisfactorios. Se reduce el desgaste en incidencia ya que el aceite del proyectado por el sistema MQL alcanza esta zona de la herramienta de manera más eficiente que con la refrigeración convencional. Además de lubricar la cara de desprendimiento se consigue una reducción de temperatura que obstaculiza los procesos de difusión, abrasión y adhesión.
La aplicación del MQL a operaciones de fresado también es factible. En la siguiente gráfica, se muestra la influencia en el desgaste de la fresa y las fuerzas de corte para dos refrigeraciones experimentadas: convencional y MQL. Al igual que la aplicación anterior el material de pieza es Inconel 718, con herramienta de metal duro sin recubrir. Las condiciones de corte empleadas son de acabado, condiciones que permiten una buena refrigeración y lubricación de la zona de contacto entre pieza y herramienta.
En la gráfica de la izquierda, se recoge el desgaste en incidencia experimentado por el filo de corte para diferentes tiempos de mecanizado, así como una imagen del filo en final del ensayo. En la primera evaluación del desgaste se puede observar que el empleo de MQL, como sistema de refrigeración, proporciona un desgaste en incidencia menor que en el caso de la refrigeración convencional. Si atendemos al desarrollo completo del ensayo, la velocidad a la que evoluciona el desgaste con MQL es de significativamente menor, VB menor de 0,15 mm en 65 min. Mientras que para la refrigeración convencional tenemos un VB mayor de 0.2 en 65 min. En la gráfica de la derecha se recoge el esfuerzo de corte en función del tiempo de mecanizado. En cualquier punto de evaluación, se observa que los esfuerzos de corte resultantes son menores cuando se emplea el sistema de MQL. Este hecho es debido por una parte a la lubricación que proporciona del sistema MQL frente al sistema convencional, pero principalmente se debe a que el desgaste en incidencia es menor. El filo conserva sus características geométricas durante más tiempo, realizando la operación de fresado de forma más eficiente.
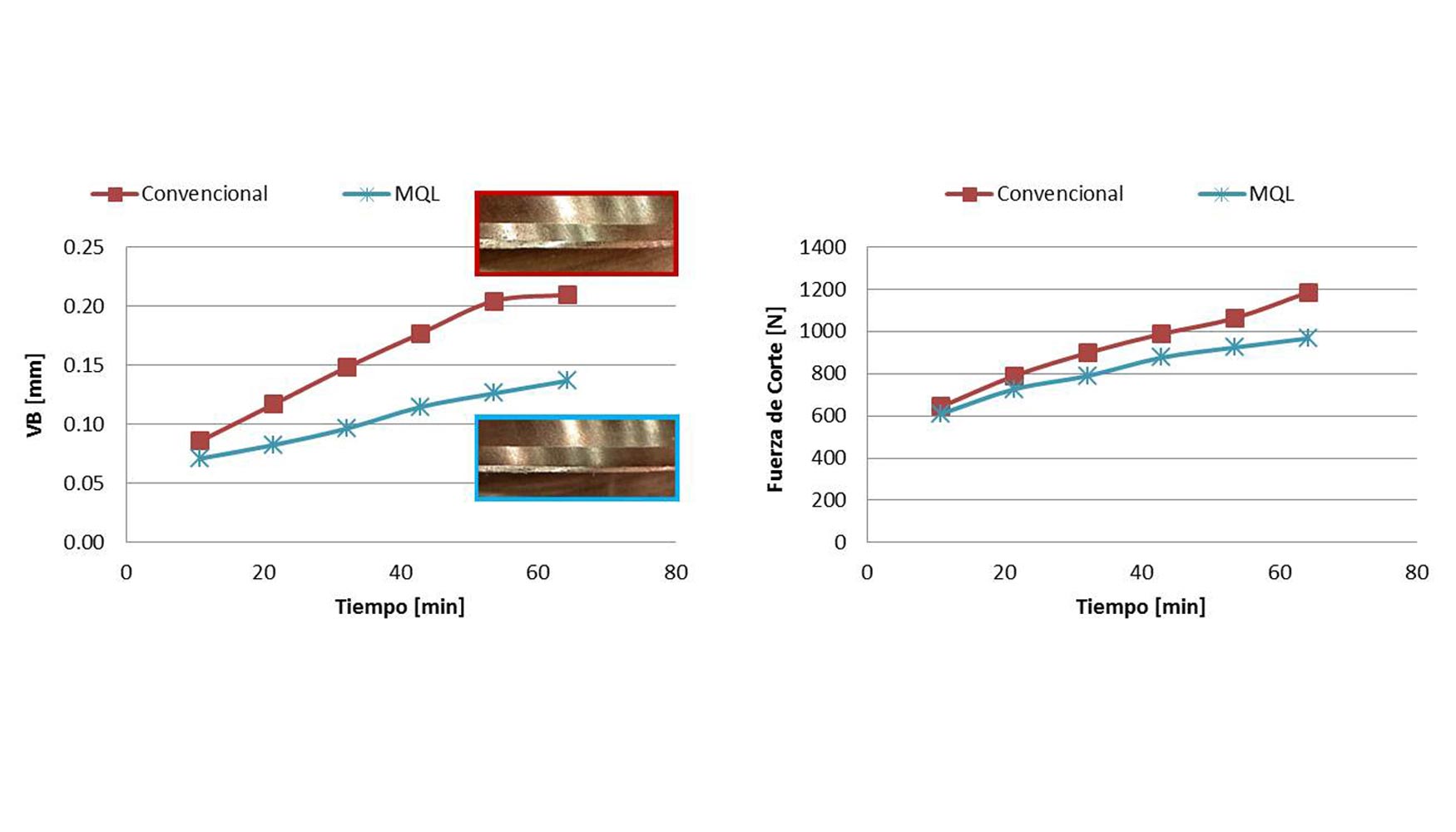
El mecanizado criogénico se presenta como un método de refrigeración alternativo a los sistemas ya presentados. En función de cual sea el medio empleado para realizar la evacuación de calor existe dos alternativas, LN2 o CO2. A pesar de la existencia de otros gases que pueden realizar la función de refrigeración de manera semejante, estos dos se destacan porque su manejo es relativamente seguro. El equipamiento necesario para llevar la refrigeración criogénica hasta la herramienta es específico para cada uno de ellos. Probablemente el más conocido es el LN2, para su empleo es necesario que se encuentre en estado líquido ya que tiene punto de ebullición cercano a -195,8 °C a presión atmosférica. El estado óptimo para el empleo del CO2 es a partir de su estado sólido, ya que su temperatura de sublimación es de -78,5 °C. El empleo de estos sistemas de refrigeración incide en el control de la temperatura alcanzada en la zona de corte, principal desencadenante del desgaste de la herramienta a la hora de mecanizar superaleaciones de base níquel. Así pues, es posible reducir los procesos de desgaste por difusión entre material pieza y herramienta. Es posible reducir la temperatura de la zona de corte de una manera más drástica que mediante otro método, permitiendo aumentar la velocidad de corte del proceso. Una ventaja relevante de la aplicación de sistemas criogénicos es que el medio que elimina el calor gasifica durante la operación de mecanizado, dejando las virutas, pieza e interior de la máquina limpia y seca.
Los primeros estudios de mecanizado con la implementación de refrigeración criogénica se llevaron a cabo a principios de 1960, continuando hasta hoy la investigación en esta área. La mayoría de los estudios realizados emplean la refrigeración criogénica en operaciones de torneado, puesto que el contacto entre pieza y herramienta se realiza de manera ininterrumpida alcanzando temperaturas de operación más elevadas. Existen trabajos de torneado de aleaciones de titanio con herramientas de metal duro en los que se compara el empleo de sistemas de lubricación convencional y criogénico, en sus dos alternativas LN2 y CO2. Se observa que el empleo de cualquiera de las dos alternativas criogénicas aumenta la vida de la herramienta, minimizando la aparición de desgaste de entalla en la cara de incidencia y reduciendo la adhesión. Entre el los dos medios criogénicos, el LN2 genera menor desgaste de herramienta. La mejora del desgaste es consecuencia de la temperatura del medio, el LN2 tiene una temperatura menor de funcionamiento, por lo que presenta mayor capacidad de absorber el calor generado en el corte.
En la actualidad la implantación industrial de sistemas de refrigeración criogénica se encuentra en la misma situación que la alta presión en sus comienzos. La mayoría de las máquinas no están diseñadas para su implementación por lo que es necesario realizarlo a partir de equipamiento externo, en ocasiones costoso, engorroso de introducir en máquina y de acceder a la zona a refrigerar. De todas formas, este método de refrigeración ha demostrado ser eficiente a nivel experimental, ya que tiene una gran capacidad de reducir la temperatura de la herramienta durante el proceso de corte.
Un inconveniente del mecanizado criogénico está en la falta de lubricación que es necesaria en determinadas ocasiones o procesos. La desventaja del MQL reside en la capacidad de refrigeración cuando la cantidad de calor a eliminar es superior a la que puede robar el flujo de lubricante. Las ventajas de una técnica cubre las carencias de la otra y viceversa. La solución pasa por combinar los dos procesos, MQL más Criogénico. De esta manera es posible satisfacer las necesidades de un mayor número de procesos de mecanizado. Existen en el mercado herramientas diseñadas para la combinación de estas dos técnicas, es el caso de Walter. La herramienta de fresado, modelo F2334R Cryotec de Walter, conduce de forma separa el flujo de gas criogénico, en este caso CO2 del flujo de MQL. La gran innovación que presenta este producto reside en que los dos flujos son conducidos a través del interior de la fresa. Permitiendo así, por cada filo de corte de la fresa, disponer de las dos salidas, una de MQL y otra de CO2. El flujo de refrigerante y de lubricante están orientados de forma precisa al filo de corte en todo momento ya que forman parte de la herramienta y se mueven con ella.
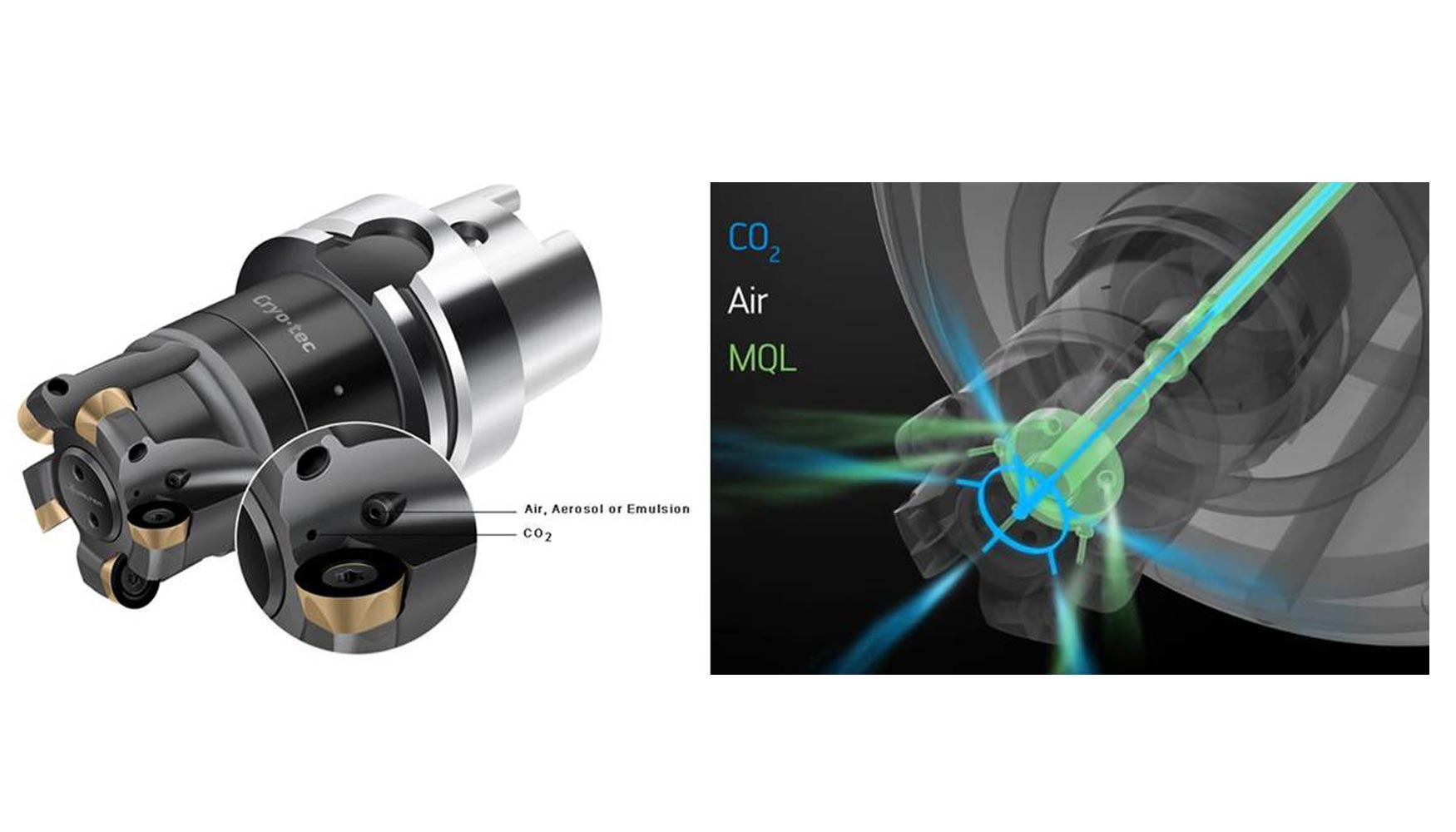
Sector de herramienta de corte
El sector de la herramienta de corte es muy dinámico y competitivo. De manera periódica las empresas fabricantes de herramientas presentan nuevos artículos destinados a ocupar un hueco en su oferta por diferentes motivos: por estar diseñadas para ser empleadas en nuevos procesos, para su aplicación en nuevos materiales de pieza, porque permiten modificar las condiciones de corte... El desarrollo de nuevas herramientas se realiza de manera continua, pero su incorporación a la oferta de cada fabricante suele realizarse cada 6 meses o 1 año, dependiendo de su capacidad de desarrollo.
Otra causa común de actualización es la debida a la incorporación de una mejora de la calidad de la herramienta, bien porque se sustituye el material en el que está realizada, o bien porque se incorpora un nuevo recubrimiento. En cualquiera de los casos supone una mejora en el rendimiento del conjunto de la herramienta respecto de la referencia que se encuentra en la oferta del fabricante. En este caso, la incorporación del nuevo desarrollo provoca la desaparición de la herramienta existente en el catálogo. Desde el punto de vista del fabricante de herramientas, este proceso de sustitución es lógico, ya que presenta una herramienta que además de cubrir el rango de trabajo de la anterior lo mejora en algún aspecto. Por otro lado, si el fabricante de herramientas no elimina referencias anteriores de su catálogo, acabaría con un gran número de productos en su oferta, provocando problemas en su sistema de fabricación, stock y suministro.
La actualización y eliminación de herramientas para la mayoría de los sectores no supone un gran inconveniente. En un alto porcentaje de ocasiones, el procedimiento de sustitución es muy básico, consistente en realizar el cambio directamente en el proceso productivo, sustituyendo una herramienta que desaparece por la nueva referencia. Este cambio en el 99.9% de los casos proporcionará mayor tiempo de vida de la herramienta o reducción en los tiempo de producción. Pero este procedimiento, independientemente de todas las ventajas productivas que proporcione la nueva herramienta, no es trasladable al sector aeronáutico donde los requisitos de seguridad, certificación y homologación son muy exigentes. El procedimiento de aceptación de la nueva herramienta dependerá de diferentes factores como tipo de pieza y su criticidad en el motor, así como de la operación de mecanizado que se vea afectada, siendo la operación de acabado la más rígida ante los cambios. Cualquier cambio realizado en el proceso productivo ha de ser homologado y certificado antes de ser aplicado a una pieza o componente que vaya a volar. Este proceso es dilatado en el tiempo y costoso económicamente.
Así pues, es posible que se encuentren procesos en los que se empleen herramientas descatalogadas por los fabricantes de herramientas, no por que presenten un rendimiento mayor que las nuevas herramientas propuestas sino por la complejidad y coste asociado a la incorporación o sustitución de la herramienta. Por este motivo, en el sector aeronáutico es necesario disponer de un procedimiento de homologación de herramientas más complejo que para otros sectores industriales, que permita evaluar la factibilidad de nuevas incorporaciones como ejercicio previo a la homologación sobre pieza y proceso real.
A la hora de precisar un procedimiento de homologación debe definirse como una herramienta útil para ayudar a acometer dos objetivos principalmente: a) estudio continúo de mercado, identificando las nuevas herramientas de cada fabricante que sean susceptibles de ser empleadas en los procesos productivos, b) definir el proceso de validación de nuevas herramientas a implementar en el proceso antes de realizar la homologación sobre pieza final. En la figura, se muestra un flujo de operaciones e identificación de puntos básicos para un proceso de validación de herramientas.
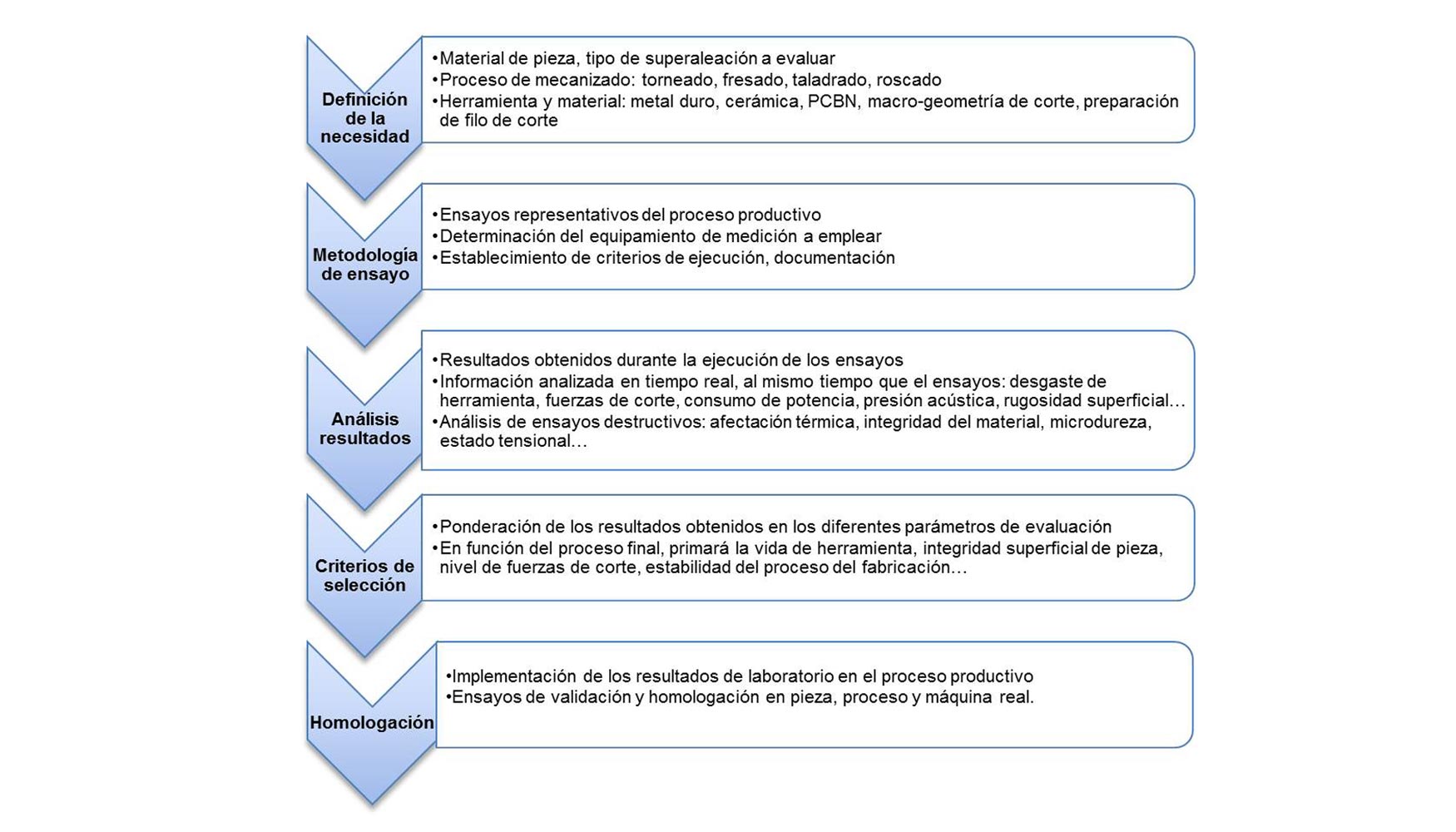
El procedimiento debe identificar de la manera más concreta posible la necesidad que es necesario cubrir. En este punto se definen las características más básicas del proceso a analizar, tanto si se trata de un proceso de selección de nuevas herramientas como si se trata de un proceso de sustitución. Será necesario definir el material de pieza, considerando todas las particularidades que puedan afectar al rendimiento de la herramienta y que sean trasladables al material de ensayo. Así pues, se consideraran las características mecánicas del material, requisitos microestructurales, aplicación de tratamientos térmicos en caso necesario, forma de fabricación (fundido, laminado, forjado). El proceso de fabricación introduce restricciones a la hora de definir las características geométricas de las probetas. Se pueden hacer dos grandes divisiones, procesos en los que la velocidad de corte se introduce a través de la pieza, como son todos los procesos relacionados con operaciones de torneado. En este caso las probetas han de tener geometría de revolución. Por otro lado se encuentran los procesos en los que la velocidad de corte viene impuesta por la rotación de la herramienta de corte, dentro de este concepto se encuentran las operaciones de fresado, taladrado, roscado… En estos casos la geometría de las probetas es más próxima a la forma prismática, siendo un parámetro importante el espesor de la misma cuando se realizan operaciones relacionadas con el proceso de taladrado. Por último es necesario definir las características básicas de la herramienta a evaluar, considerando el material constituyente de la herramienta, metal duro, cerámica, CBN, recubrimiento de la herramienta. Además en este punto juega un papel primordial el trabajo previo de análisis de mercado ya que es el momento de seleccionar las herramientas que encajan con el material de pieza y proceso.
Los resultados obtenidos en la fase experimental han de proporcionar la suficiente información como para determinar el comportamiento de la herramienta en el proceso de fabricación real, por lo que la definición de la metodología de ensayo es crucial a la hora de obtener buenos resultados prácticos. En este punto se profundiza en el proceso que se va a ensayar, con objeto de identificar las características más relevantes del mismo. Se determinará las condiciones de corte, pudiendo ser unas específicas o estar basado en un diseño de experimentos para identificar la ventana óptima de trabajo. Por otro lado, es importante realizar una comparación cuantitativa del rendimiento de las herramientas. Con el fin de establecer unos criterios objetivos, durante el proceso se emplean sistemas para la monitorización de parámetros tales como consumo de potencia, ruido, vibración, temperatura, fuerzas de corte… Después del proceso se evalúan los posibles mecanismos de desgaste experimentados por las herramientas y las características de pieza como rugosidad, daño a nivel microestructural, tensiones residuales… Debe documentarse de manera exhaustiva, todos los aspectos relativos a la metodología experimental tales como el equipamiento a emplear, su montaje en el sistema experimental, metodología de calibración de los instrumentos, descripción detallada de los pasos que constituyen el proceso de ensayo y formatos de recogida de resultados. La generación de una buena documentación garantiza la consistencia de todos los ensayos a realizar. Además, esta documentación supondrá un procedimiento de ensayo cerrado cuya consulta será imprescindible en futuros procesos de homologación de nuevas herramientas.
Entre los factores del proceso que son objeto de análisis se pueden distinguir en dos grandes grupos, aquellos que dan información interpretable al mismo tiempo que se realizan los ensayos y aquellos que han de analizarse una vez acabada la fase experimental. Independientemente del grupo al que pertenezca el factor a analizar debe proporcionar una información objetiva, que permita una ponderación frente al resto de ensayos realizados. La evaluación del rendimiento de las herramientas se debe realizar atendiendo al conjunto de factores analizados, ya que una herramienta puede proporcionar resultados muy satisfactorios en un aspecto productivo y no cumplir con otros requerimientos.
De manera muy simplificada, se puede decir que el factor más importante a la hora de analizar el rendimiento de una herramienta es el análisis del desgaste que experimenta en el proceso de fabricación. Las características del material de la herramienta o la geometría de corte simplemente hacen que los diferentes procesos que se desencadenan en el proceso de corte afecten en mayor o menor medida a la duración del intervalo de tiempo en el que la herramienta mantiene unas características funcionales aceptables. La medida del desgaste se puede realizar de manera directa o a través de métodos indirectos.
Los métodos directos están basados en la medición directa del desgaste de la herramienta por medio de la aplicación de técnicas ópticas o de resistencia eléctrica entre pieza y herramienta. La precisión es la gran ventaja de estos métodos aunque no son aplicables en el sistema productivo ya que son sensibles a las condiciones de producción. Para realizar la medición es necesario interrumpir el proceso de mecanizado, las mediciones no se pueden realizar si existe viruta o refrigerante. La técnica más extendida es la medición óptica, de la que existen varios métodos, pero el más aplicado es el que se basa en la reflectividad del material. La zona desgastada de la herramienta tiene mayor reflectividad en comparación con la zona no desgastada. Esta propiedad es empleada por algunos métodos para determinar la forma y medida del área desgastada. La técnica de resistencia eléctrica se basa en el aumento del área de contacto entre herramienta y pieza como consecuencia del desgaste, disminuyendo de esta forma la resistencia eléctrica de la unión.
Los métodos indirectos tienen una mayor aplicación fuera de un entorno de laboratorio. Son métodos que apoyados en la una técnica de medición directa como es el método óptico para realizar su calibración, pueden ser empleados en el entorno productivo de forma individual para estimar el nivel de desgate de la herramienta. Entre estos métodos los más destacables son la medición de fuerzas de corte, vibración. Técnicas indirectas como medición temperatura y rugosidad superficial son más complicadas de integrar de manera sistemática dentro del proceso de mecanizado. Nada más que comienza la operación de mecanizado, como consecuencia del movimiento relativo entre pieza y herramienta, comienzan a desencadenarse los procesos de desgaste y a afectar a la capacidad de corte. Una herramienta desgastada ejerce mayor esfuerzo de corte para eliminar la misma cantidad de material que una en perfecto estado. Así pues, la fuerza de corte se incrementa a medida que aumenta el desgaste y por lo tanto, es un factor que se puede medir fácilmente con el fin de monitorizar el desgaste de la herramienta. La medición de las fuerzas de corte, en el proceso productivo, también es empleada para detectar cambios en las condiciones de corte, velocidad de avance o profundidad de pasada. Basándose en el mismo principio, la medición de la potencia consumida por la máquina herramienta en el proceso de corte, es otro método de identificar el nivel de desgaste aunque este valor puede verse alterado por desgate o alteración de elementos propios de la máquina. En operaciones de torneado, los fenómenos de vibración son provocados por la fricción entre pieza y herramienta. La fricción generada en el corte es característica de cada herramienta y varía a medida que el desgaste aumenta. A mayor desgaste mayor superficie de fricción en la herramienta. El rendimiento del mecanizado depende en gran medida de la ausencia de procesos de corte libres de vibraciones. La aparición de vibraciones perjudica adicionalmente la integridad de la herramienta, pudiendo provocar su rotura. Este fenómeno también influye negativamente en la vida de algunos elementos de la máquina herramienta. Generalmente su medición y registro se realiza por medio del empleo de acelerómetros, aunque el empleo de micrófonos o de sensores de presión acústica también son empleados para tal fin. La temperatura alcanzada en el proceso de corte también proporciona información sobre la eficiencia del proceso de corte, fricción entre pieza y herramienta y es posible su relación con el nivel de desgaste del filo de corte. Es una técnica empleada a nivel de laboratorio, su integración en el sistema productivo supone sobre costes en la preparación de la herramienta. Por lo general, en esta técnica se realiza mediante la introducción de termopares cerca de la zona de corte, por lo que es necesario perforar la herramienta para alojar el sensor de temperatura. Además es necesario realizar procesos de calibración y complejos modelos de ajuste en base a la conductividad térmica del material de la herramienta. Es posible realizar mediciones de temperatura menos precisas empleando sistemas de medición de emisión infrarroja.
Finalmente, terminado el proceso de mecanizado es necesario analizar la integridad superficial de la pieza. En este punto se valora principalmente el estado de rugosidad superficial, deformación y dureza del material de la superficie de la pieza a nivel microestructural y tensiones residuales introducidas como consecuencia del proceso de corte. Por lo general, estos factores están estrechamente relacionados. La rugosidad superficial empeora cuando el nivel de desgaste de la herramienta supera un umbral máximo. Cuando la rugosidad está por encima del nivel umbral el corte ha dejado de ser efectivo, incrementando los esfuerzos de corte y consecuentemente la deformación en la capa más externa del material de pieza. Al mismo tiempo se incrementa la temperatura del proceso, por lo que además de una deformación plástica a nivel microestructural se produce una afectación térmica. La conjunción de todos estos factores también tiene consecuencias a nivel tensional de la superficie, generando tensiones residuales perjudiciales para el componente fabricado, aspecto de alta criticidad cuando se trata de elementos que forman parte de un motor aeronáutico.
En consecuencia, establecer un procedimiento de ensayo y homologación de herramientas que contemple estos aspectos es crucial para identificar las herramientas más adecuadas para cada aplicación, las condiciones de corte óptimas de aplicación así como establecer un umbral máximo de desgaste de la herramienta que no produzca perjuicios en la pieza mecanizada. Por último, es necesario realizar el proceso de homologación en pieza, proceso y máquina real, comprobando nuevamente, que los resultados obtenidos a nivel de laboratorio se ajustan y son consecuentes con los obtenidos en la fase experimental y acordes al cumplimiento de los estándares de seguridad de elementos de motores aeronáuticos.
La Universidad como laboratorio de procesos
No hay duda de que es necesario generar un conocimiento más profundo que permita afrontar de manera más eficiente el mecanizado de superaleaciones. De esta forma se podrá abordar la posibilidad de emplear nuevos materiales que reduzcan el peso del motor aeronáutico o que faciliten alcanzar mayores temperaturas de operación. También es necesario avanzar en el desarrollo de nuevas herramientas de corte que desempeñen su laborar de manera más eficaz primando la integridad del componente mecanizado. Claramente, hay que apostar por la investigación de nuevas tecnologías, desde el nivel conceptual y maduración en entorno de laboratorio hasta su implementación en plataformas representativas del proceso productivo. Asumir el trabajo que implica todos estos puntos, es prácticamente imposible para una empresa dedicada al mecanizado de piezas para el sector aeronáutico. Es necesaria la colaboración con agentes investigadores, como la Universidad o centros tecnológicos, que sirvan de generadores y trasmisores del conocimiento y nuevos desarrollos.
La investigación en este ámbito de la tecnología lleva asociados unos costes muy elevados. En el caso de la Universidad del País Vasco es posible mantener el nivel de las investigaciones gracias a la financiación obtenida a través de diferentes proyectos de investigación. El programa Estatal de I+D+i orientado a los Retos de la Sociedad es un buen ejemplo. Programa promovido por el Ministerio de Economía y Competitividad del Gobierno de España a través del Fondo Europeo de Desarrollo Regional (FEDER). El objetivo de esta convocatoria es apoyar iniciativas de cooperación entre empresas y organismos de investigación, con el fin de promover el desarrollo de nuevas tecnologías, la aplicación empresarial de nuevas ideas y tecnologías así como contribuir a la creación de nuevos productos y servicios. Gracias a este tipo de iniciativas es posible generar masa crítica de I+D+i de carácter interdisciplinar, promover la creación de empresas de carácter innovador, incrementar el nivel tecnológico del país, mejorar la competitividad del tejido empresarial y reforzar la capacidad de liderazgo internacional del Sistema Español de Ciencia Tecnología e Innovación.
La Universidad del País Vasco participa en el programa Retos a través del proyecto Desafio II: ‘Desarrollo de sistemas de fabricación de alta fiabilidad para piezas rotativas con altos requisitos de integridad superficial – II’. Gracias a este proyecto es posible colaborar con empresas como ITP, Danobat, GMTK y EKIN y otros agentes investigadores como MGEP e Ideko. El proyecto está enfocado a la innovación en productos y procesos relacionados con la fabricación de discos de turbina con alta fiabilidad en aspectos de integridad superficial. Entre los objetivos del proyecto se encuentra desarrollar nuevos procesos de mecanizado mediante el empleo de nuevas herramientas de corte, mejora de condiciones de corte y alternativas a las estrategias de mecanizado, en procesos como torneado, fresado, brochado, rectificado... Aplicabilidad de nuevos desarrollos para la asistencia al mecanizado, principalmente desde el punto de vista de sistemas de refrigeración. Profundización y desarrollo de sistemas de monitorización del proceso a nivel de laboratorio e industrial. La participación de empresas de sector de máquina herramienta posibilita investigar en la arquitectura de máquina, con objeto de adaptarla a las necesidades del mecanizado de las piezas rotativas de la turbina.
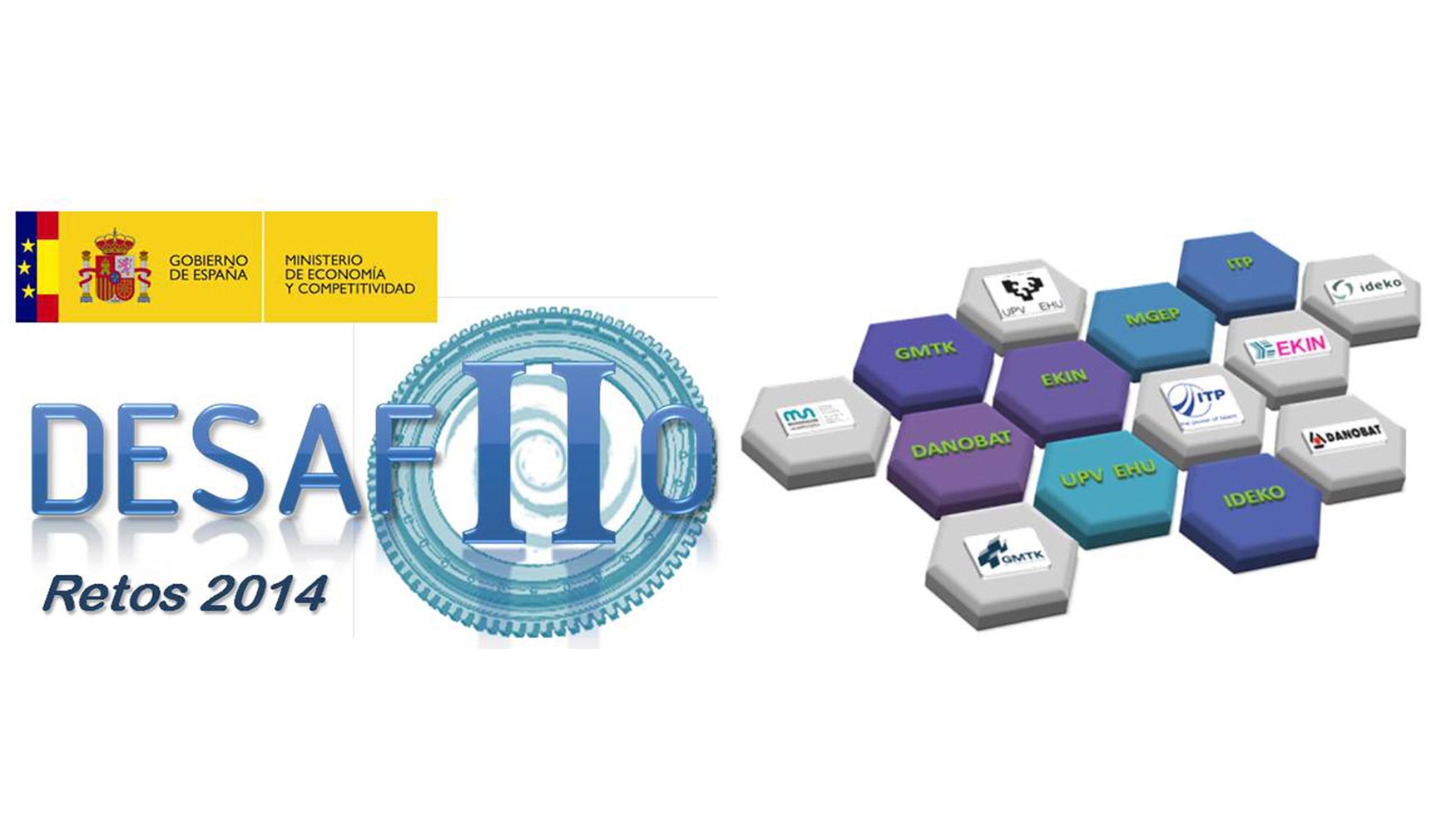
Máquina herramienta dedicada al sector aeronáutico
Con una gama de productos de elevada configurabilidad, Ibarmia Innovatek S.L.U.se presenta como una empresa referente en el mecanizado de las diferentes tipologías de piezas presentes en el sector aeronáutico, como bien justifica el aumento del número de clientes integrantes en este sector.
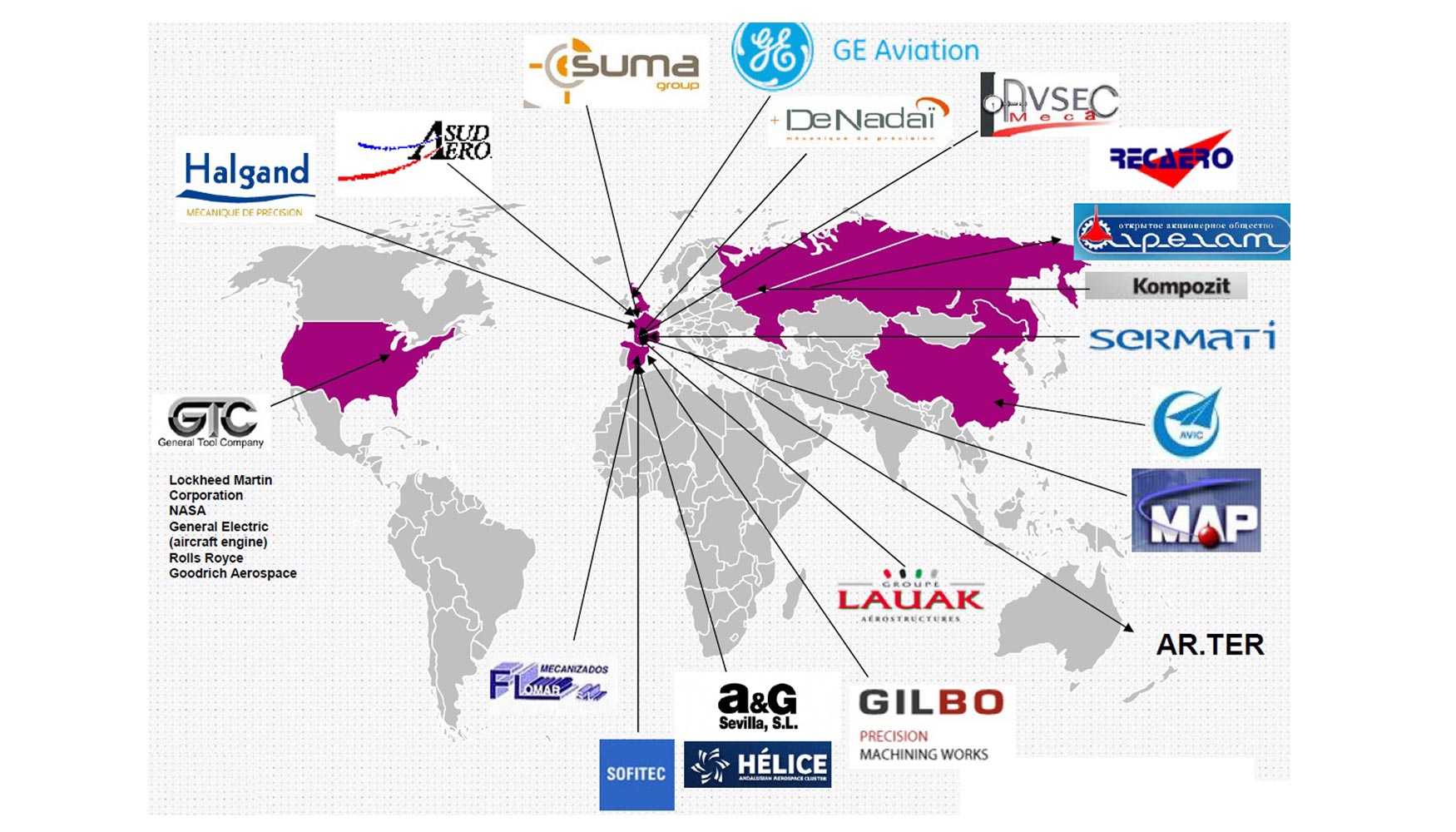
El trato individual y cercano que la empresa ofrece a cada uno de sus clientes deriva en un producto flexible que satisface las necesidades del cliente. Esta flexibilidad se traduce en centros de mecanizado que van desde los 3 a los 5 ejes, capaces de combinar diferentes procesos (serie multiprocess), y con recorridos en X de hasta 12 metros. Hay que destacar la nueva serie T, idónea para el mecanizado de componentes circulares de elevada dimensión, también su nuevo cabezal horquilla (HR) y la incorporación de “funciones inteligentes” dentro de los diferentes controles numéricos (CN).
El doble bobinado de los nuevos electrohusillos proporciona un elevado par a bajas revoluciones, que permite tanto el mecanizado de materiales de baja maquinabilidad (Inconel, Titanio, Waspaloy), como el mecanizado a elevadas revoluciones de materiales de alta maquinabilidad, como es el caso del aluminio, con elevada presencia en aplicaciones estructurales. Esto permite el mecanizado del amplio rango de materiales vinculados al sector aeronáutico en una misma máquina. Además, el doble bobinado evita la formación de corrientes inducidas, lo que le permitirá trabajar a elevadas revoluciones sin sufrir un calentamiento excesivo del mismo.
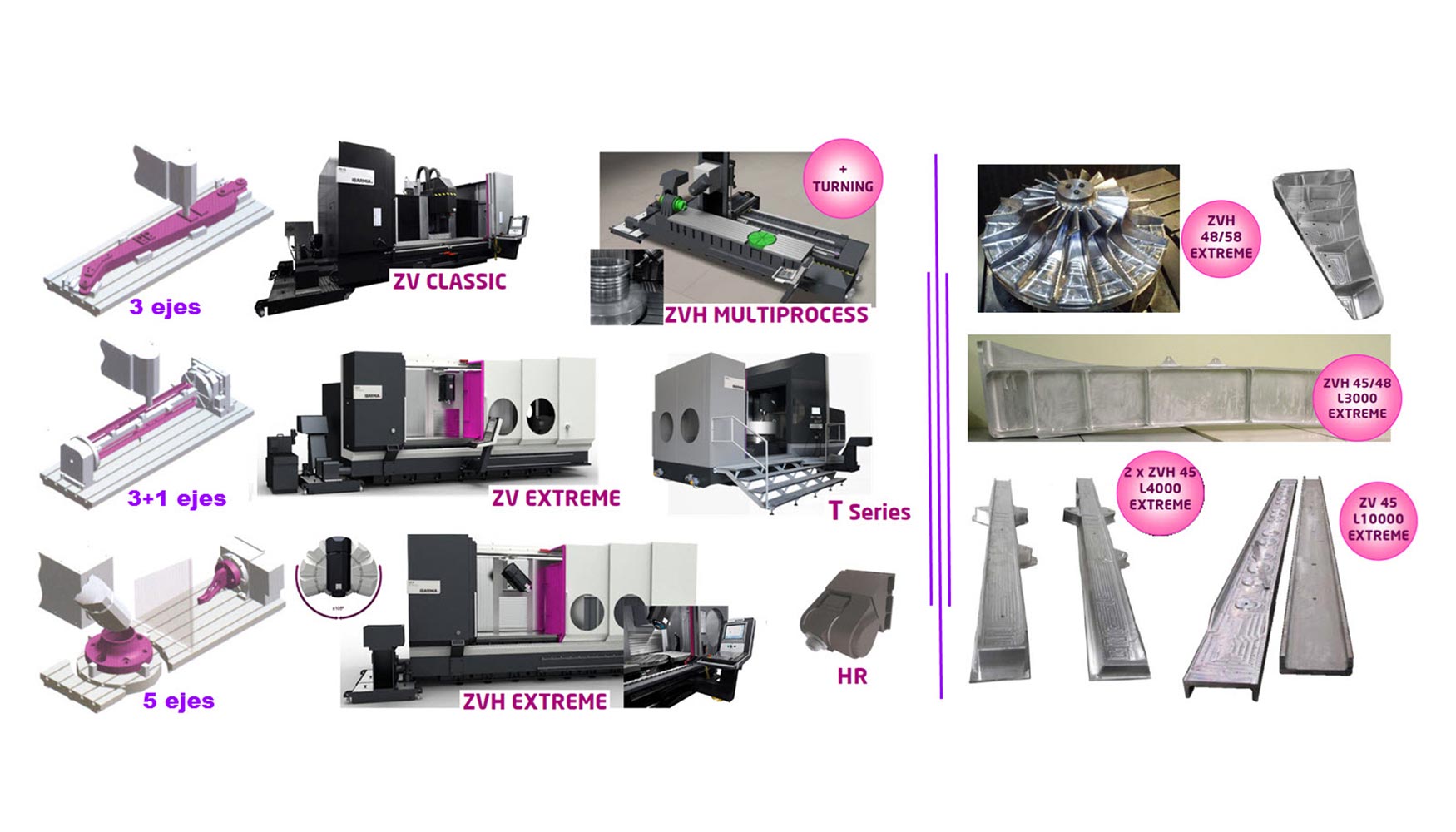
La apuesta por la I+D de Ibarmia en el sector aeronáutico se ha visto fortalecida por la integración de la misma en el Centro de Fabricación Avanzada Aeroespacial (CFAA), situado en el parque tecnológico de Bilbao, que será operativo en Junio de 2015. Con su participación como socio, Ibarmia afianzará su conocimiento sobre componentes y procesos complejos del sector, logrando así una mayor adaptabilidad en su gama de soluciones, lo que le permitirá ofertar soluciones integrales a sus clientes, más allá de su avanzada maquinaria.