Acelerando el mecanizado de ranuras
Las ranuras suelen dejarse de lado en los debates sobre el mecanizado de engranajes. No obstante, gran parte de la geometría giratoria dedicada al mecanizado de engranajes complejos también es aplicable a la producción de ranuras. Y, debido a lo frecuentes que son en los vehículos pesados, de minería, de construcción, agrícolas y otros tipos de maquinaria de movimiento de tierras, es increíble que no se les preste la atención que merecen. Prácticamente siempre que se transmite un movimiento de rotación de un árbol a otro entra en juego una ranura. Debido a los requisitos de carga, por ejemplo, de una ranura de un árbol de transmisión de maquinaria pesada es necesario contar con ranuras cada vez más complejas (árboles dentados con más dientes en diferentes geometrías) para maximizar la superficie de contacto y distribuir homogéneamente las elevadas cargas del árbol macho al hembra.
Los OEMs (fabricantes de equipos originales) y sus proveedores directos solicitan a los talleres y productores componentes de gran calidad. Esto no es una novedad. Los proveedores de componentes llevan tiempo contando con la tecnología necesaria para producir ranuras para los vehículos pesados. En lo referente a satisfacer las necesidades de productividad con lotes de tamaño muy grande, las herramientas de acero rápido tradicionales (HSS), como las fresas para cremalleras, fresas madre, fresas de brochado y fresas de desbarbado de ranuras han hecho un trabajo excelente. No obstante, empieza a exigirse una mayor flexibilidad. El ritmo de cambio ha incrementado y el lanzamiento de nuevos modelos, a menudo basados en plataformas completamente nuevas, son más frecuentes que nunca. Pero, históricamente, ha sido difícil para los fabricantes de ranuras reaccionar rápidamente y hacer cambios de diseño frecuentes.
Desventajas intrínsecas de un sistema probado
Para cada conjunto de profundidades de corte, configuraciones y geometrías de ranura hay una única fresa de brochado, fresa para cremalleras o fresa madre de HSS diseñada casi exclusivamente para esa tarea. En ciclos largos de un mismo lote, estos procesos son excelentes y producen resultados muy repetibles con especificaciones estrechas.
La desventaja en esas operaciones es la necesidad de disponer de varias herramientas, dado que las operaciones de mantenimiento, como el rectificado y la corrección de recubrimiento, exigen sacarlas de la máquina y del taller. Con el fin de mantener las máquinas en marcha para el mecanizado de la ranura, los talleres necesitaban tener en el inventario por lo menos dos de cada una de estas herramientas de HSS para asegurarse de que tenían un repuesto para las operaciones de mantenimiento (rectificado/arreglo del recubrimiento) programadas y los posibles fallos.
A medida que el ritmo de cambio en la construcción pesada aumentaba, la única manera de seguir siendo lo suficientemente flexible para manejar cambios de especificaciones y diseño o, por ejemplo, hacer prototipos era poseer un juego completo de fresas madre de todos los tamaños y formas para cubrir cualquier contingencia. Y para la producción, eso implicaba poseer dos de cada. Durante años, esto ha hecho que muchos de los trabajos de mecanizado de ranuras y engranajes se realizaran en talleres especializados.
Flexibilidad en lotes más pequeños
Ahora se está produciendo un salto en el ámbito de la flexibilidad, ya que las máquinas multieje y multitarea permiten que las fresas de disco hagan el trabajo que hasta la fecha hacían exclusivamente las fresas madre, las fresas de brochado, las fresas para cremalleras etc. en el mecanizado de ranuras. El mecanizado diente a diente o el tallado con fresa de disco de los dientes de una ranura exterior o interior puede ser una forma muy rentable de enfrentarse a las ranuras. Con las máquinas multitarea y las soluciones de plaquita, puede utilizarse una única herramienta de corte para realizar múltiples operaciones. Esto es especialmente importante para las operaciones de lotes pequeños a medianos, que a menudo son las operaciones que requieren más cambios a lo largo del proceso de mecanizado y más manipulación. En lugar de producir 10.000 componentes idénticos, estos talleres a menudo producen 100 ranuras de un mismo tipo y luego otras 200.
La fresa de disco CoroMill 172 de Sandvik Coromant proporciona la flexibilidad del tipo de máquina utilizado, es decir, refleja la adaptabilidad de una máquina multitarea. No obstante, las plaquitas son específicas para un tamaño de ranura y un número de dientes concretos. Entonces, el cliente está sustituyendo la flexibilidad de la fresa madre por la flexibilidad del diseño de la máquina: máquinas multitarea, tornos con herramientas accionadas y eje Y y centros de mecanizado con mesas rotativas.
Por ejemplo, en lugar de tener una máquina para el proceso de torneado y una máquina de tallado con fresa madre para generar la ranura, la máquina multitarea puede hacer la pieza completa. O, la célula podría ser una máquina de torneado con un centro de mecanizado de 3 ejes que utiliza una mesa rotativa. Los beneficios de mecanizar la pieza completa en una máquina son tiempos de reglaje reducidos y características de tolerancia optimizada. Al utilizar un centro de mecanizado y una mesa rotativa, el fabricante no se ve atado a una máquina especializada. El centro de mecanizado podría utilizarse para mecanizar otros componentes con ranuras entre un reglaje y otro. Además, también se pueden realizar otras operaciones como el cajeado, el mecanizado de agujeros cruzados, el mecanizado de planos, etc.
Para muchos talleres o proveedores directos, esta flexibilidad se ha traducido en el mantenimiento de más trabajos a nivel interno. Las operaciones de mecanizado de ranuras subcontratadas a especialistas para engranajes ahora pueden realizarse en el taller; lo único necesario es un centro de mecanizado de tres ejes básico y una mesa rotativa con una serie relativamente pequeña de fresas de disco intercambiables. Una de las ventajas principales es la posibilidad de cambiar entre diferentes perfiles de plaquita intercambiable en una misma fresa para conseguir las diferentes profundidades de agujero, configuraciones de raíz o chaflanes de punta. Compare eso a la necesidad de contar con un tamaño y perfil de fresa madre, fresa de cremalleras o de brochado únicos para un único trabajo. Por no mencionar que las fresas de disco, en especial las plaquitas aplicables a un cuerpo específico de herramienta, son relativamente baratas en comparación con las fresas madre, las fresas para cremalleras o las fresas de brochado. Si tiene en cuenta la necesidad de disponer de menos herramientas y su capacidad de mecanizar diferentes tipos de ranuras, verá que son una solución auténticamente excelente.
Otro factor que debe tenerse en cuenta es la reducción del tiempo de reglaje. Para los fabricantes de ejes, todos los árboles tienen una pequeña ranura. Si un árbol tiene que cambiarse de máquina para múltiples operaciones, aumentan los tiempos de reglaje y la posibilidad de que se produzcan errores en la sujeción, el transporte y la re-sujeción. En las máquinas multitarea con fresas de disco, estos árboles dentados pueden mecanizarse en un único reglaje.
Hoy en día, los fabricantes buscan una manipulación más sencilla de los componentes con soluciones más inteligentes, sencillas y flexibles. El camino más fácil es a menudo el mejor camino, y reducir el inventario de herramientas y el reacondicionamiento puede ayudar a simplificar el trabajo a la vez que se limita el inventario de herramientas y los costes de mantenimiento.
Principio de adelgazamiento de la viruta en el mecanizado de ranuras
Los cálculos de adelgazamiento de la viruta son esenciales para un mecanizado de ranuras efectivo con fresas de disco, dado que el adelgazamiento de la viruta es el principio más básico de la operación. Las dos principales recomendaciones de avance de los fabricantes de fresas de disco son normalmente el avance por diente (fz) y el grosor de viruta máximo (hex) programados. Ambos valores deben ser iguales cuando la fresa está reglada con un empañe de corte radial igual o mayor a su propio radio. No obstante, el efecto de adelgazamiento de la viruta deseado solo puede empezar a producirse cuando el empañe radial es inferior al radio.
Con fresas de disco que actúan básicamente como herramientas de mecanizado diente a diente o de cajeado en la fabricación de ranuras, el reducido empañe radial en las ranuras frente al diámetro de la fresa implica que siempre debería producirse adelgazamiento de la viruta. Para conseguir el mejor hex posible y optimizar la operación de “cajeado” de ranuras, los operarios deben calcular el valor de fz, derivado del empañe de la fresa de disco en función del diámetro de la misma. Utilice esta fórmula para el adelgazamiento de la viruta (Figura 1).
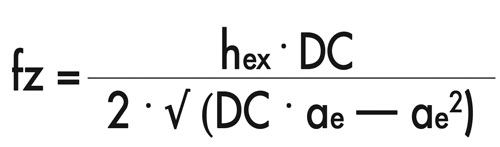
Figura 1: Determinar el avance por diente para el adelgazamiento de la viruta. Donde DC = diámetro de corte / ae = empañe radial.
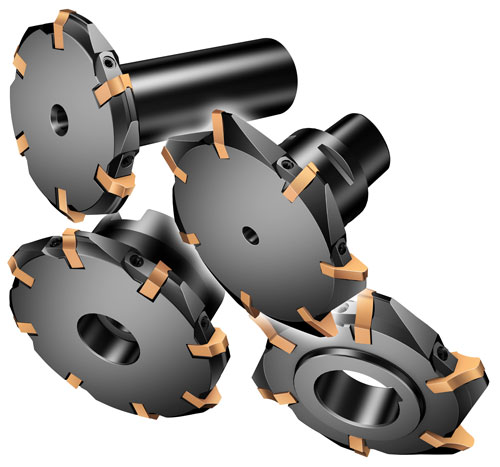
Si un operario no opta por el avance por diente correcto, cabe la posibilidad de que la velocidad de avance sea demasiado baja para la preparación del filo o la geometría de la plaquita. Como el cuerpo de la herramienta ofrecerá cierta tolerancia en la desviación, como norma general, se recomienda a los operarios evitar ir por debajo de 0.003" (0.076 mm) en hex. Si hex es demasiado bajo, se produce un efecto de frotamiento, en lugar de un corte efectivo. Esto produce un calor adicional que puede reducir la vida útil de la herramienta y disminuir la precisión del proceso. Los fabricantes de fresas de disco deberían poder proporcionar parámetros hex máximos.
Si el objetivo es una producción maximizada, el adelgazamiento de la viruta es un factor clave en las operaciones que simulan el mecanizado diente a diente o el cajeado, como en el mecanizado de ranuras con fresas de disco. Este factor es especialmente importante en el desbaste con dos pasadas, ya que se corre un mayor riesgo de disminuir la productividad en esa fase.
Ajustes para la flexión
Un efecto derivado del cambio de una máquina de tallado con fresa madre especializada a una máquina multitarea o un centro de mecanizado es que la herramienta solo se sostendrá en el lado del adaptador del husillo. En una máquina de tallado con fresa madre tradicional, la fresa madre se sostiene en ambos extremos del eje. Al tener el soporte de la herramienta únicamente en un extremo, cabe la posibilidad de que se produzca una flexión de la herramienta. Unos pocos pasos ayudan a protegerse de la flexión. Primero, al seleccionar una fresa de disco para una operación de mecanizado de ranuras, debe limitarse la flexión de la herramienta, seleccionando la herramienta más estable disponible. No utilice una herramienta más larga de lo necesario en base a la accesibilidad. Evite una relación L/D > 5 si es posible, dado que la flexión y la estabilidad de la herramienta requerirán más de dos pasadas, impactando gravemente en la productividad.
Además, asegúrese de que el adaptador del husillo no sea demasiado débil para el diámetro de herramienta disponible. Los fabricantes de las fresas de disco deben proporcionar a los operarios las dimensiones correctas para el acoplamiento de la herramienta en función de la longitud de la herramienta. Por último, si es necesario, utilice una estrategia de dos pasadas, utilizando una pasada de acabado con una profundidad de corte inferior. Una menor fuerza de corte durante el corte de acabado resulta en una superficie optimizada con una flexión mínima. El componente y la fijación también juegan un papel importante en las vibraciones.
Si las medidas preventivas no evitan adecuadamente la flexión, los operarios pueden encontrarse con desviaciones del perfil entre un lado del diente y el otro. Cuando el perfil del diente de la ranura muestra una desviación de la pendiente igual, con la misma dirección de inclinación tanto en el lado derecho como en el izquierdo del diente, esto quiere decir que la longitud de reglaje debe ampliarse o reducirse. Para calcular la longitud de ajuste (más abajo como x, en mm), utilice la siguiente ecuación:

Figura 2. Diám. de la cresta del engranaje – diám. del valle del engranaje. Donde: fHa(iz.) = error de pendiente del perfil (a izquierda del diente). fHa(de.) = error de pendiente del perfil (a derecha del diente).
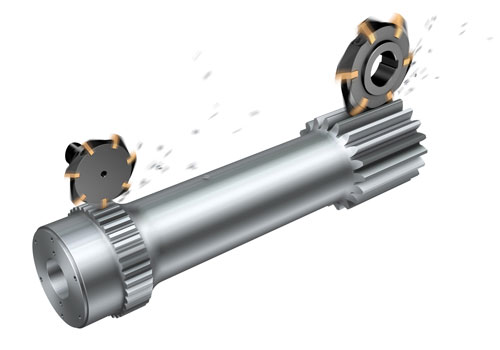
Para las ruedas dentadas externas, un perfil de diente con una pendiente igual a derecha e izquierda, pero en direcciones opuestas, implica un diámetro de engranaje incorrecto con cortes demasiado profundos o superficiales. Si las pendientes de las líneas muestran un punto de estrechamiento en la parte superior del protocolo, quiere decir que el diámetro del engranaje es demasiado pequeño. La solución es consultar las medidas de MdK (dimensión sobre rodamientos) y ajustar el reglaje a cortes menos profundos. Por el contrario, si las pendientes de las líneas muestran un punto de estrechamiento en la parte inferior del protocolo, quiere decir que el diámetro del engranaje es demasiado grande. La solución es consultar las medidas de MdK y ajustar el reglaje a cortes más profundos.
Una pendiente angular diferente en el lado derecho e izquierdo del diente del engranaje indica un error debido a una profundidad de corte (medidas MdK o MdR, donde MdR = dimensión sobre pasadores) y flexión de la herramienta incorrectas.
Para ajustar la profundidad de corte para el diámetro y el grosor de diente correctos, el operario primero debe determinar la medida MdK o MdR. Mecanice un componente de prueba o realice por lo menos dos cortes para medir las dimensiones MdK o MdR del engranaje. El diámetro de la rueda dentada/profundidad de corte puede ajustarse después de cortar solo dos espacios entre dientes y medirse con una unidad de medición o un micrómetro.
Una vez que se consigan las medidas MdK o MdR correctas, compense la flexión de la herramienta conforme a la fórmula de ajuste de la flexión de la herramienta (Figura 2).
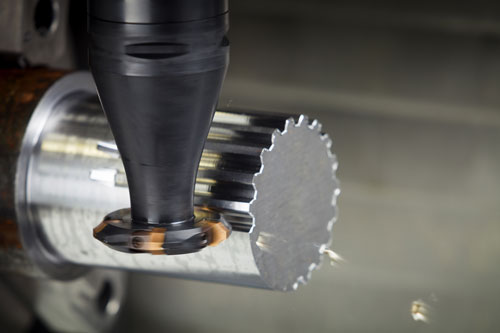
Fresas de disco en acción en operaciones de mecanizado de ranuras: Un buen ejemplo
Comparemos una fresa de disco, en este caso la fresa Sandvik Coromant CoroMill 172, con una herramienta de acero rápido (HSS) en el desbaste y acabado de una ranura externa en un árbol de acero de baja aleación (16MnCr5). Los datos de la ranura para esta operación eran: DIN 5480 con el módulo 5 (tamaño similar al ANSI 5/10) de 26 dientes (z).
Para conseguir el resultado deseado, la herramienta de HSS necesitó dos pasadas de desbaste y una pasada adicional de acabado a una velocidad de corte de 165 pies/min con un avance por diente programado de 0,003”. La pasada de desbaste adicional fue necesaria porque la fresa madre solo estaba sostenida por un extremo. La fresa de disco CoroMill 172, no obstante, consiguió lo mismo con una única pasada, más rápida, de desbaste a 540 pies/min con un avance por diente de 0,008” y una pasada de acabado a 640 pies/min con un avance de 0.007" por diente.
La duración resultante del ciclo de la herramienta de HSS fue de 250 minutos, frente a los 20 minutos de CoroMill 172. Este tipo de ahorro de tiempo es solo un ejemplo del potencial de optimización de la velocidad que se puede conseguir en la producción de ranuras con fresas de disco de tallado en máquinas multitarea. CoroMill 172 crea perfiles de engranaje conforme al estándar DIN 5480 para ranuras (DIN 867 para engranajes) y tiene la capacidad de realizar operaciones de mecanizado interior y exterior de ranuras, engranajes y cremalleras. Las posibilidades de aplicación van más allá de las máquinas multitarea inicialmente comentadas, pueden utilizarse en centros de mecanizado, centros de torneado e incluso aplicaciones en máquinas de tallado con fresa madre tradicionales.
A CoroMill 172, que cubre la gama de módulos de 3 a 10 (DP 8/16 – 2.5/5), ahora se le une la nueva CoroMill 171, que cubre los módulos de 0.8 a 3 (DP 32/64 – 8/16). Esto proporciona a Sandvik una gama completa de tamaños de herramienta de fresas de disco intercambiables frecuentemente utilizados en la industria de los vehículos pesados dependiente de las ranuras. La fresa CoroMill 171 dispone de las plaquitas más pequeñas posibles y se ajusta a la gama de ranuras utilizadas en el lado ligero de los vehículos pesados, principalmente en los camiones pesados y los autobuses. No obstante, las ranuras existen en todas las industrias que requieren cajas de cambio o transmisiones.
El panorama de la fabricación de los vehículos pesados está cada vez más sujeto a las mismas presiones que vemos en la industria de la automoción, es decir, la necesidad de disponer de flexibilidad y ciclos más cortos para tamaños de lote de pequeños a medianos. Esta tendencia está convenciendo a los propietarios de talleres a volver a internalizar el proceso de fabricación de ranuras. Los fabricantes ahora pueden utilizar las nuevas tecnologías de mecanizado con fresas de disco en las máquinas de CNC tradicionales (tornos, centros de mecanizado, máquinas multitarea) para fabricar ranuras en un programa adaptable que permita ahorrar tiempo y dinero, a la vez que se reduce el inventario de las herramientas de corte.