La Sociedad de Técnicos de Automoción pone sobre la mesa las últimas innovaciones en el sector del automóvil
Los multimateriales y la fabricación aditiva centran el IV Congreso I+D+i de STA
En un sector competitivo como es el de la automoción, las actividades de I+D+i no son una opción sino una necesidad. Conscientes de ello, desde STA —Sociedad de Técnicos de Automoción— vienen realizando una serie de congresos técnicos donde compartir los últimos avances en temas relacionados con el sector. El último de ellos, celebrado en la Escola Tècnica Superior d'Enginyeria Industrial de Barcelona —ETSEIB— a principios de abril, expuso algunas de estas tendencias.

El IV Congreso I+D+i titulado ‘Construyendo el futuro: una visión sobre las tendencias en I+D+i e innovación’ enfocado al sector de la automoción, organizado por la Sociedad de Técnicos de Automoción —STA— puso sobre la mesa lo ‘más candente’ en temas como los nuevos materiales —composites, nanomateriales y grafeno— o las tendencias en innovación disruptiva —robótica, mecatrónica y fabricación aditiva 3D.
Abrió el congreso Francesc González, presidente de STA, acompañado de Neus Cònsol, directora de la ETSEIB, Antoni M. Grau, director general d’Indústria de la Generalitat de Catalunya, y Vicenç Aguilera, presidente de CIAC — Clúster de la Indústria d'Automoció de Catalunya—. González expuso que el objetivo de este congreso es compartir conocimiento para crear networking en un mundo, el de la innovación en automoción, “que sigue siendo minoritario pese a todo”. Por su parte, Antoni M. Grau puso de manifiesto el reciente acuerdo firmado entre Generalitat y empresas y agentes sociales para doblar la inversión en centros tecnológicos —red Tecnio— para fortalecer todavía más la cooperación y la transferencia tecnológica como muestra del interés del Govern para potenciar e incentivar la apuesta en I+D+i entre las compañías.
Posteriormente intervino Francesc Perarnau, vocal de tecnología de STA, para presentar la jornada y plantear hasta qué punto es importante que las empresas tengan en su estrategia empresarial la gestión de la innovación como objetivo. “Pero ello demanda de una cultura específica y es necesario trabajar en este sentido”. Para Perarnau, “es necesario fomentar la creatividad y la iniciativa entre los empleados. Y que las empresas sean más flexibles”. En su opinión, el sector de la automoción convergirá en los próximos años en investigaciones propias de otros sectores, como las TIC, las comunicaciones industriales y la informática, “por lo que la flexibilidad será vital para poder cooperar y compartir estos conocimientos”.

El futuro pasa por los materiales compuestos
Albert Riera, director de ST Plásticos de STA, se encargó de presentar los ponentes de la primera parte de la jornada, dedicada a ‘nuevos materiales’ y ‘tendencias en innovación disruptiva’.
Inició el turno Josep Costa, del grupo de investigación perteneciente a la Universitat de Girona, Amade —Análisis y materiales avanzados para el diseño estructural—, y miembro de Aemac —Asociación Española de Materiales Compuestos—, quien expuso la oportunidad que suponen los materiales compuestos en la automoción. Consciente que actualmente el material más usado en este sector es el acero (en un 37,5%), mientras que los composites son minoritarios, expuso aquellas partes de un vehículo donde existen piezas de mayor peso y, por lo tanto, allí donde podría actuar para aligerar el peso total mediante materiales más ligeros. Se trata principalmente de partes estructurales (que suponen un 30% del peso) como el chasis o la carrocería, piezas del sistema de tracción (22%) como el motor, la suspensión o la transmisión, la zona interior del automóvil (23%) como el salpicadero, el suelo, los paneles de las puertas, el volante o el asiento, las zonas exteriores (11) que incluyen el módulo de puerta, capó, puerta de maletero y parachoques, y los componentes eléctricos (14%) como los interruptores o el cableado y luces. En estos casos los materiales varían entre acero, composites, aluminio, titanio, plásticos, magnesio, etc. según las aplicaciones.
Así, expuso algunos de los cambios previstos a corto/medio plazo en cuanto a la introducción de materiales ligeros que permitan aligerar los pesos. “Un cambio que permitirá cumplir con las normas europeas medioambientales pero, a la vez, garantizar la máxima seguridad”. Costa alertó que el mercado demanda cada vez más “vehículos multifuncionales, lo que incide de manera importante en el coste de producción”. Por otra parte, también apuntó las “enormes ventajas que aportan los materiales compuestos” si bien reconoció que “son 10 veces más caros que los aceros convencionales. Ello se debe al precio de la fibra de carbono, base de los composites, que procede de países asiáticos que cuentan con el monopolio, hasta ahora, puesto que Europa se ha planteado producir este material y dejar de depender de los países productores”. Asimismo, expuso también la multifuncionalidad de estos materiales con propiedades estructurales como conductividad eléctrica, sensores embebidos, fibras piezoeléctricas, antenas, transmisión de información y almacenamiento de energía. “Sin embargo, existen otros factores que supone un retos a la hora de desarrollar dichos materiales: la poca consciencia del potencial de ahorro en peso, el coste o la complejidad del diseño, a la vez que requieren de desarrollos tecnológicos en cuanto a materiales, procesos, personal preparado y diseño”. Precisamente en lo que se refiere a los retos en diseño, Costa apunto varios: “las propiedades mecánicas de un material compuesto se ‘diseñan’, a la vez que dependen de la dirección (anisotropía). Asimismo, el material compuesto no se deforma plásticamente —es poco o nada tolerante a la sobrecarga—, las matrices son sensibles a efectos higrotérmicos, presentan comportamientos dependientes del tiempo y los mecanismos de daño son múltiples, complejos e interactuantes…”.
En conclusión, el investigador afirmó que el potencial de los materiales compuestos a la hora de contribuir a la reducción del impacto ambiental de los automóviles es incuestionable pero teniendo en cuenta las barreras a superar para su introducción, esto es, el coste; el tiempo de cadencia de producción; las herramientas predictivas y capacidades de diseño; y la formación del personal para el proceso y el diseño, a la vez que alertó de la necesidad, “indispensable”, de desarrollar estrategias colectivas.
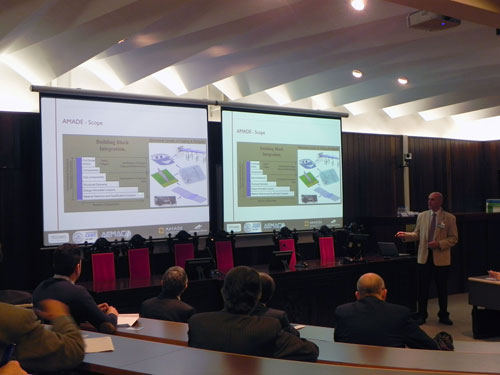
La metalización del plástico
Matías Ordinas, director de asistencia técnica de MacDermid, presentó el potencial que representa la metalización de plástico, una tecnología que desarrollan en la empresa. MacDermid proporciona a las compañías soluciones en recubrimientos anticorrosión para muchos segmentos, entre ellos el de automoción y componentes, un mercado que supone más del 50% del total. Ordinas señaló que “actualmente se croman más de 70 millones de metros cuadrados de plástico anualmente, sobre capas de cobre y níquel, lo que supone un gran consumo de este producto”. De hecho, en los interiores de los automóviles se pueden encontrar múltiples ejemplos de plástico cromado “y es una tendencia que va en aumento”. Asimismo, el hecho de que el sector de la automoción sea uno de los que requiere estándares más altos de calidad supone un fuerte impulso a la evolución tecnológica en este campo. Pero, ¿qué busca este sector en la metalización de plástico?: “reducir los costes, aumentar las prestaciones y eliminar materiales peligrosos”. En este sentido, apunto que algunas de las mejoras que han venido produciéndose buscan mejoras medioambientales, “y es que las exigencias en este sentido están dirigiendo las innovaciones químicas”, afirmó Ordinas. Ejemplo de ello es el desarrollo de un material alternativo al cromo hexavalente (altamente tóxico durante el proceso, cancerígeno), o la eliminación de otros productos peligrosos que aparecen en el proceso de cromado, que requiere de un tratamiento mediante mordentado.
En cuanto a los materiales metalizables, Ordinas expuso el ABS como el más indicado, por ventajas como “su elevada resistencia al impacto, la poca fragilidad, bajo coeficiente de dilatación térmica, buena resistencia química y al ‘stress cracking’, así como un excelente acabado superficial”. Sin embargo, conscientes de las exigencias medioambientales que las empresas automovilísticas deben cumplir cada vez más, en MacDermid están trabajando en un proceso de mordentado libre de cromo, “patentado en julio de 2013 tras 5 años de investigación”. Entre otras ventajas, este nuevo proceso no requiere de grandes inversiones en equipos, no supone un tiempo extra de procesado, mejora el rendimiento de la pieza, asegura menos rechazos y usa los mismos sustratos (ABS, ABS-PC). Asimismo, el ratio tiempo/temperatura de trabajo es idéntico que el proceso anterior, tan sólo requiere de un tratamiento simple de aguas residuales y no supone un incremento significativo en el coste del proceso.
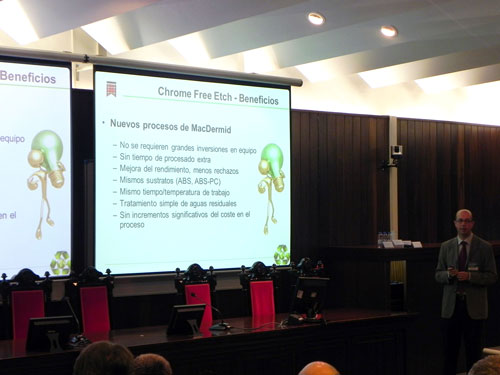
Aquél material (casi) mágico
En su turno de exposición, Alfonso del Rey, del Institut Català de Nanociència i Nanotecnologia (ICN2), introdujo las ventajas que puede aportar un material como el grafeno a la automoción. “Un material que ha creado muchas expectativas y que seguramente no cumplirá muchas de ellas pero que es la base a su vez de nuevos materiales en 2D”. Y si bien hay quien lo considera el material, del futuro, el investigador del ICN2 puso en evidencia algunos productos que ya contienen grafeno, “como raquetas de tenis de alta competición”. Por otra parte, puso sobre la mesa el error de considerarlo un único producto cuando, en realidad, puede ser varios teniendo en cuenta las diferentes técnicas de obtención. Se trata de un producto que levanta interés en el mundo científico e industrial, lo que explica que “Europa invierta hasta 1.000 millones de euros en 10 años en investigaciones relacionadas con este material. Una inversión muy necesaria para no perder posiciones en la carrera por desarrollar productos de grafeno puesto que no debemos olvidar que países asiáticos como Corea del Sur también están trabajando en ello”, alertó.
Entrando concretamente en el mercado de la automoción Alfonso del Rey explicó que hasta el momento “han existido algunos experimentos como el desarrollado por Daimler-BASF para reducir el peso del asiento incidiendo en el sistema de calefacción de éste. Es de prever que los primeros usos de este material sean, como en cualquier innovación, en F1 donde hay mucha capacidad de I+D+i, para luego aplicarse a vehículos de alta gama y finalmente a utilitarios”.
Asimismo, enumeró algunas de las aplicaciones que puede aportar el grafeno: recubrimientos, almacenamiento de energía, composites, electrónica/electrónica impresa y sensores. En el caso de los recubrimientos, la aplicación sería el uso de placas solares en techos o carrocería del automóvil o la disipación de calor, usos antiestáticos o de anticorrosión. En el caso de almacenamiento de energía, el grafeno sería útil en baterías y supercapacitadores y, en el caso de su aplicación en materiales compuestos, permitiría aligerar estructuras; incrementar la resistencia; disipar el calor; aportaría propiedades eléctricas; y podrían obtenerse composites por inyección. En el caso de la electrónica y electrónica impresa, su uso sería en favor de la disipación del calor o bien para desarrollar paneles informativos transparentes en el vehículo. Finalmente, en cuanto a sensores, el grafeno supondría un incremento de la sensibilidad de éstos y permitiría desarrollar sensores multifuncionales.
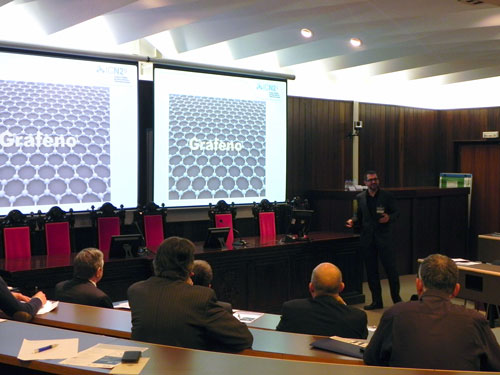
Herramientas de soporte a la producción
Tras la pausa para el café, y generar un tiempo de ‘networking’, retomaron la palabra Marc Segura, de ABB, y José Luis Sobrino, de Siemens Industry.
El primero centró su presentación en el reto que supone para las empresas la alta variedad de productos que, hoy por hoy, pueden proveer gracias a la personalización, poniendo especial énfasis en la necesidad de asegurar “la rapidez, flexibilidad y calidad de la producción”. Presentó así la solución desarrollada para tal fin, junto con la empresa Nub3D: el sistema robotizado de medición con luz blanca Sidio Airus para realizar el control dimensional en el mismo puesto de producción.
Por su parte, el representante de Siemens expuso las ventajas de un sistema como el Teamserver, un PLM que permite realizar el seguimiento y control de la producción en tiempo real, con total integración de los procesos y actualizado en todo momento. Estos sistemas aportan ventajas en cuanto a velocidad de planificación, permitiendo “resolver problemas y reaccionar ante problemáticas en todo momento, además de compartir información entre departamentos y vincular y sincronizar listas de ingenierías y de fabricación”.
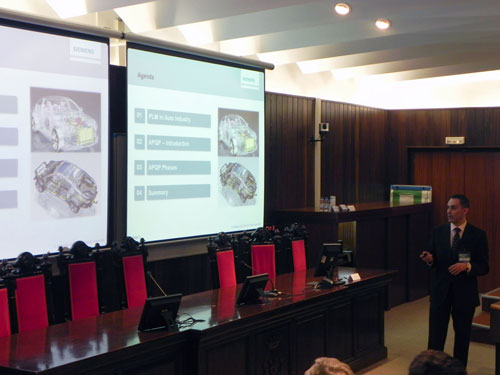
Más allá del prototipado: fabricación 3D
Cerró el bloque de la mañana Víctor Paluzíe, de RMS/EOS con una presentación de las posibilidades de la fabricación 3D con materiales metálicos, una realidad que, sin embargo, está todavía poco arraigada en nuestro imaginario, si bien “del total de sistemas de fabricación aditiva instalados en el mundo, un tercio de ellos son para el sector metal”. Para Paluzíe, “actualmente la mayoría se dedican al sector del prototipado pero cada día se está implantado más la manufactura directa, principalmente en aplicaciones médicas o para el sector de la automoción, aeronáutico, etc.”. En este sentido, admitió que “en automoción normalmente se utiliza la impresión 3D para prototipado por cuestiones de coste mientras que el Rapid Manufacturing está pensado para series cortas o unitarias”. Se trata de un sistema de fabricación con el que se logran piezas totalmente personalizadas de manera rápida y de alta calidad, exactamente tal y como están diseñadas. “Con Rapid Manufacturing se puede fabricar una pieza de una sola atacada en lugar de ensamblar diferentes partes de ésta, lo que supone una reducción de costes de producción y tiempos de trabajo”.
La experiencia de EOS en este campo le permite desarrollar bien piezas donde el factor crítico es la rapidez —grandes y voluminosas, en las que se permite rugosidad superficial y superficies funcionales acabadas convencionalmente— o bien focalizando la atención en la calidad —piezas más bien pequeñas, en las que se exige una alta resolución—. En el sector de la automoción, Paluzíe mostró algunos de los ejemplos a los que la fabricación 3D puede dar respuesta, obteniendo componentes ligeros y complejos a través de la libertad de diseño, con funcionalidades integradas sin herramientas de fabricación, reduciendo así el coste, para desarrollar piezas individualizadas que cumplan con las necesidades y requerimientos del cliente.
El resultado son piezas un 70% más ligeras, con una considerable reducción de las emisiones de CO2, sin restricciones a la hora de diseñar la pieza. “La fabricación aditiva viene a resolver la exigencia del sector de la automoción en cuanto a la eficiencia energética, a la vez que permite la integración funcional de herramientas adicionales. También permite obtener componentes de automoción individualizados a través de cambios en las necesidades del cliente”. En este sentido, Paluzíe expuso que cada vez más la automoción transmite emociones, de modo que “cuanto más personalizadas sean las necesidades del usuario del coche, más atractiva será esta individualización y la fabricación aditiva permite la personalización en masa rentable y en un único paso”.
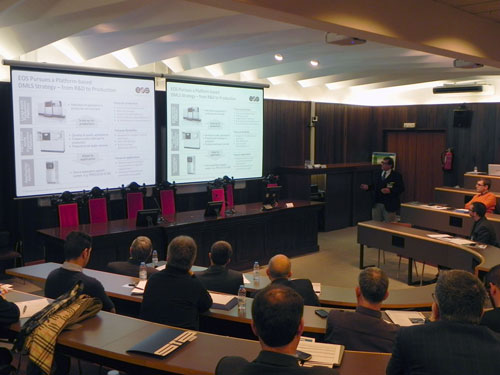