Adaptación de sistemas de óptica móvil tipo escáner al proceso de temple por láser remoto
En el mercado actual de la máquina-herramienta cada vez se están introduciendo con más fuerza máquinas multitarea que incorporan más de un proceso de fabricación sin tener que mover la pieza. Debido a su capacidad y flexibilidad en cuanto a tipo de proceso, actualmente la incorporación de sistemas de láser de alta potencia más escáner está muy valorado. Los escáneres son sistemas basados en ópticas móviles que dotan de movimiento al haz láser con velocidades lineales que pueden superar los 7.000 mm/s. Normalmente estos sistemas se usan para el marcado, texturizado o pulido de piezas metálicas, procesos donde predominan la fusión y sublimación de material. Su viabilidad para procesos de tratamiento superficial por láser está todavía por determinar.
En este trabajo se presenta la puesta a punto de un sistema compuesto por un láser de fibra con una fibra de 50 μm y un escáner 2D para realizar operaciones de temple por láser. En este proceso, la sublimación y/o fusión de material es inaceptable y es necesario realizar un control preciso de la temperatura. Para ello, por un lado se ha evaluado la deformación del haz láser en el plano de trabajo generado por la óptica móvil del escáner y, por otro lado, se ha caracterizado la dinámica del sistema de espejos móviles para ver un posible sobrecalentamiento de la zona tratada. Por último, se han evaluado los resultados mediante una serie de ensayos y mediciones tanto de durezas como de temperaturas.
1. Introducción
El temple por láser convencional es uno de los procesos de tratamiento que más está creciendo en la industria en la actualidad. Si se compara el temple por láser con otros procesos más tradicionales para tratamientos superficiales, como un endurecimiento por inducción o por llama, es posible obtener una zona tratada muy localizada sobre superficies complejas en 3D con mínimas distorsiones dimensionales, siendo posible eliminar en algunos casos el proceso final de rectificado [1]. Además, el interés de este proceso radica en la posibilidad de integrar una fuente láser muy versátil directamente dentro de la cadena de producción sin la necesidad de un medio de temple adicional y en la posibilidad de producir sobre un mismo material dos microestructuras muy diferentes, un núcleo dúctil junto a una capa superficial endurecida con tensiones residuales de compresión [2]. Se trata de un proceso que está siendo utilizado sobre todo en el temple de matrices y troqueles. En concreto, en aristas de cortantes [3], dado que se puede obtener una superficie de alta dureza después de realizar la operación de ajuste del troquel, sin introducir prácticamente distorsión geométrica. También se está empleando en series largas de componentes de automoción como bisagras de puertas.
Por otro lado, en los últimos años se están desa rrollando e industrializando sistemas basados en ópticas móviles para el guiado de láseres de alta potencia. Estos sistemas también se denominan escáneres y se suelen acoplar a la muñeca de un robot serie [4] o en el cabezal de máquinas-herramienta cartesianas[5], como se aprecia en la figura 1a). La característica principal de los escáneres es que son capaces de mover el haz láser con velocidades superiores a 7.000 mm/s. Esto es debido a que el movimiento se hace a través del giro de unos espejos con muy poca masa e inercia que convierten pequeños giros en movimientos lineales del haz láser en el espacio de trabajo, figura 1b).
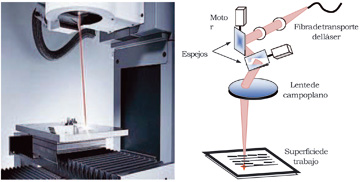
La principal ventaja de los escáneres es que trabajan lejos de la zona a procesar, pudiendo así llegar a zonas poco accesibles, con buena calidad de haz láser. Por esto, a los procesos de fabricación por láser que utilizan escáneres se les añade la palabra remoto [6]. Existen diversos trabajos de investigación en la actualidad dedicados al empleo de los escáneres en varios procesos de fabricación sobre todo en la industria automovilística como son el corte, el marcado o la soldadura por láser remota. Poco a poco los procesos por láser remotos se están introduciendo en otros sectores como el del molde y van apareciendo nuevos procesos como el texturizado o el pulido. En cambio, tratamientos superficiales por láser, como el temple en su variante remota, son muy poco conocidos pero se están empezando a estudiar [7,8]. Por último, decir que todo esto da una idea de la flexibilidad en cuanto a proceso que tienen los sistemas de ópticas móviles o escáneres.
Así, en el presente trabajo se pretende estudiar el proceso de temple por láser con ópticas móviles o escáneres haciendo especial hincapié en la adaptación de estos sistemas para el proceso y los parámetros de máquina y escáner que se deben de tener en cuenta. Además se estudiará el área de material templado mediante medición de microdurezas, ya que el principal problema de la superposición de trayectorias en el proceso de temple por láser es el reblandecimiento parcial de las zonas solapadas [9].
2. El temple por láser remoto
En el temple por láser convencional las dimensiones del haz láser definen de forma rígida la anchura del área a templar. En cambio, en el temple por láser remoto esta anchura se forma mediante barridos muy rápidos de un haz de menores dimensiones, el cual es controlado por servomotores. De esta forma la anchura de la zona templada es controlable y variable.
A diferencia del temple por láser convencional, en el temple por láser remoto coexisten dos velocidades, la de escaneo y la de avance. El parámetro característico de este proceso es la velocidad de escaneo [mm/s] que es la velocidad de movimiento del haz láser. Está, es controlada por el sistema óptico de espejos del escáner y puede llegar a superar los 7.000 mm/s. Por otro lado está la velocidad de avance [mm2/s] que es el movimiento real de avance de la línea templada sobre la pieza. Sus dimensiones se dan en velocidades de área barrida, no en velocidades lineales, ya que es dependiente de la velocidad de escaneo [mm/s] y la anchura del área barrida [mm]. Esta velocidad depende de la velocidad relativa entre la máquina (o robot) y el escáner. En cuanto al tipo de estrategias a la hora de barrer el área a templar se pueden usar dos tipos de estrategias, la de barrido continuo y la de barridos múltiples o de barrido por áreas, que se explican a continuación más detalladamente.
La estrategia de barrido continuo (Figura 2a) consiste en ir moviendo el láser en una línea ascendente y descendente a la velocidad de escaneo mientras la pieza se mueve en la mesa de trabajo con la velocidad de avance. En este caso el centro del haz láser solo pasa una vez por cada punto. Es el esquema más sencillo posible y se puede hacer con escáneres de una sola dimensión pero no es posible variar la densidad de energía del haz en el sentido de avance.
Por otro lado, la estrategia de barridos múltiples (Figura 2b) consiste en ir proyectando distintas áreas que se barren con el láser a la velocidad de escaneo mientras la pieza se mueve a la velocidad de avance. En este caso el haz láser pasa varias veces por el mismo punto y por lo tanto se podría configurar la potencia para dar densidades de energía variables en las distintas zonas del barrido. En el temple por láser convencional, se diseñan ópticas específicas para distribuir la densidad de energía más apropiada dentro del haz. Se trata de ópticas ‘a medida’ y normalmente basadas en ópticas difractivas [10]. En el caso de los escáneres, y con este procedimiento de barrido, es posible distribuir la densidad de energía en el haz simplemente con un cambio de trayectoria.
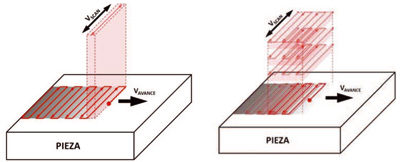
Además, en el proceso de temple por láser, es necesario controlar la temperatura de la superficie de la pieza en tiempo real, lo que normalmente se hace mediante pirometría biocrmática. Esta tecnología consigue medir la temperatura real en la superficie de la pieza sin contacto, de forma puntual, sin prácticamente retrasos térmicos y adquiriendo hasta 1.000 datos por segundo. En el caso del temple por láser remoto, sobre el registro térmico adquirido durante el proceso se pueden distinguir una temperatura de fonde o base y unas temperaturas de pico sobre la temperatura de fondo.
3. Sistema experimental y adaptación al proceso de temple
Para la realización de los ensayos de temple con escáner en el presente trabajo se ha utilizado un centro de procesado láser de materiales especialmente diseñado para la experimentación por el Grupo de Fabricación de Alto Rendimiento del Departamiento de Ingeniería Mecánica de la UPV/EHU denominado Kondia Aktinos 500. Se trata de un centro de mecanizado Kondia B500 reconvertido con una carrera en X, Y, Z de 700 x 400 x 600 mm. Se han eliminado elementos como el cabezal, el cambiador de herramientas, el filtro del fluido de corte, etc. añadiendo dos láseres industriales: un láser de diodos de alta potencia de 1,5 kW con un cabezal de aporte por láser y un láser de fibra de 1 kW con dos fibras de salida. Uno de ellos, de 600 μm, a la que se ha acoplado otro cabezal de láser cladding y una fibra de 50 μm acoplada a un escáner 2D. El escáner es un ScanlabTM Hurryscan 25 de dos ejes, con el que se puede barrer un área de 120 x 120 mm. En la Figura 3 se muestra el centro de procesado láser Aktinos 500.
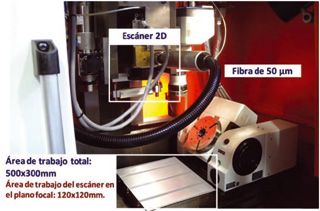
3.1 Consideraciones sobre los ejes de máquina y escáner
Para la óptima realización del proceso hay que sincronizar los ejes de la máquina y el escáner ya que en muchos casos los ejes del escáner son demasiado cortos (120x120 mm) ó porque se quiere templar un eje cilíndrico mientras se le induce un giro de máquina. En este caso en el centro de mecanizado láser se dispone de 7 ejes, los 5 ejes lentos y largos (3 lineales + 2 rotativos) de la máquina cartesiana Aktinos 500 y los dos ejes lineales rápidos y cortos del escáner láser. Por ello, la alineación entre los ejes es muy importante ya que los dos ejes lineales rápidos del escáner se corresponden con dos ejes lineales lentos de la máquina, el eje X y el eje Y.
Así, se ha medido el paralelismo de los ejes X e Y del escáner y de la Aktinos 500 ya que el escáner ha sido montado posteriormente a la fabricación de la máquina mediante un cabezal de diseño propio. Se han realizado dos tipos de ensayos marcando a baja potencia sobre pintura negra en una chapa sujeta con una mesa magnética. Durante los ensayos por un lado se han movido únicamente los ejes cartesianos de la máquina y a continuación únicamente los del escáner. Los resultados de los ensayos se han medido mediante un proyector de perfiles que es capaz de coger puntos con resolución de micras. El proyector tiene acoplado un sistema de adquisición de datos que mediante puntos puede sacar distintas variables geométricas. Se han realizado líneas para medir el ángulo entre ejes iguales y circunferencias concéntricas de distintos diámetros. Los resultados se muestran en la Tabla 1 y en la Tabla 2.
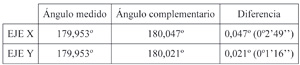
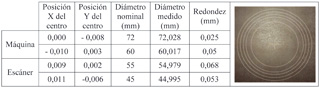
3.2 Caracterización del movimiento del escáner
A la hora de trabajar con un sistema de láser más escáner hay una serie de retrasos que es importante cuantificar ya que se deben de variar dependiendo del tipo de proceso que se esté realizando. Por un lado están los retrasos en el encendido y apagado del láser con respecto al movimiento de los ejes del escáner. Y por otro lado están los retrasos de polígono que tiene relación con el cambio de velocidad de los ejes en un cambio de dirección, si se baja la velocidad para seguir la geometría programada se producirá un quemado mientras que si se mantiene la velocidad constante se suavizarán los ángulos en los cambios de dirección.
En el caso del temple con láser se debe evitar zonas calientes por lo que conviene, como se puede observar en la Tabla 3, programar el retraso de encendido largo, el retraso de apagado corto y el retraso de polígono corto.
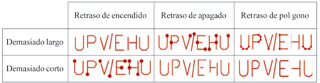
Los retrasos se han medido experimentalmente mediante el marcado de un rectángulo seccionado, como se observa en la Figura 4. Se ha cuantificado el retraso de encendido demasiado largo de 0,041 ms, el retraso de apagado demasiado corto de 0,141 ms y el retraso de polígono demasiado corto de 0,186 ms. Además, se han marcado distintos ángulos trabajando en pulsado y se ha visto claramente que aunque haya un recorte del ángulo marcado a altas velocidades, no hay en ningún caso un cambio en la velocidad del proceso.
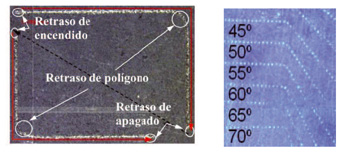
Además de los comentados existen otros dos tipos de retrasos, retraso de salto y retraso de marcada que darían problemas si son cortos pero si son largos, como es el caso, aumentan un poco el tiempo total del templado.
3.3 Errores dimensionales en el campo de trabajo
Por otro lado, para la puesta a punto del proceso se ha caracterizado el escáner en el plano de trabajo. Los sistemas ópticos que componen el escáner necesitan complicadas correcciones que normalmente vienen hechas de fábrica en el plano focal, Z=0 mm, y que dependen de la configuración del escáner [11]. Además hay que tener en cuenta que para el temple por láser y otros procesos de tratamiento superficial se trabaja con el haz desenfocado [7]. Esto hace que las dimensiones de la zona a tratar respecto de las programadas (120 x 120 mm) varíen considerablemente dependiendo del plano de trabajo (Figura 5). En este caso se ha trabajado en el plano Z=+50 mm. Para su caracterización se ha hecho una cuadrícula sobre una pintura negra a lo largo de todo el plano de trabajo y se han medido las dimensiones X e Y de las distintas cuadrículas en un proyector de perfiles. Como se observa en la Figura 5b, en este plano de trabajo la zona central tiene el mayor error en la distorsión total (obtenido mediante una media cuadrática de la distorsión correspondiente a las dimensiones X e Y de cada cuadrícula), pero presenta una variación menor y por tanto es más fácil corregirla. Así, la zona central se considera la zona óptima y es en la se ha trabajado.
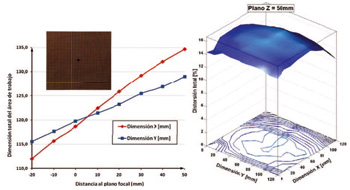
3.4 Consideraciones sobre el campo térmico
Como se ha comentado anteriormente es muy importante controlar el registro térmico que se da en la pieza durante el proceso, lo que se suele hacer mediante pirometría bicromática. En el temple con escáner al barrer áreas no es intuitivo saber la zona más caliente donde ha de colocarse el pirómetro.
Por ello se ha realizado un ensayo para poder caracterizar el proceso combinando simulación numérica y experimentación. Se ha escaneado una línea durante 2 segundos a una velocidad de escaneo de 60 mm/s solapando trayectorias hasta templar el material. A su vez se ha medido la temperatura y simulado numéricamente en distintas zonas de la línea. El campo térmico generado durante el templado en las distintas zonas de la línea escaneada durante el proceso se puede observar en la Figura 6. Tras el ensayo se siguientes conclusiones:
- En la zona central el número de ciclos térmicos es el doble que en los extremos.
- En los extremos estará la temperatura más alta, por lo que es la zona donde s colocará el pirómetro. A pesar de esto la diferencia de temperatura entre extremos centro no es significativa ya que en los extremos el tiempo de enfriamiento entre pasada y pasada es mayor mientras que en el centro la temperatura de fondo es más alta.
- La máxima anchura templada se encuentra donde el tiempo de cada ciclo que está por encima de la temperatura de austenización es mayor. Esto es cerca del punto de cambio de dirección o de temperatura máxima pero no en él.
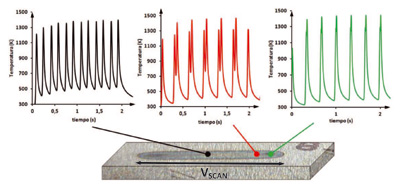
4. Ensayos experimentales
4.1 Comparación entre el proceso de temple por láser convencional y remoto
Para comparar el proceso de temple por láser convencional con el temple por láser con escáner se ha optado por realizar una serie de ensayos sistemáticos empleando la estrategia de barrido continuo, barriendo una línea de 10 mm de espesor. El motivo de la elección de esta estrategia es que a priori es más sencilla de controlar. Para ello, se han mantenido la velocidad de avance y la potencia en todos los ensayos, variables del temple convencional, y se han considerando distintos valores de velocidad de escaneo y separación entre pasadas y, así, poder ver el efecto de las variables del escáner. Los distintos parámetros ensayados se observan en la tabla 3. Estos ensayos equivaldrían a un único ensayo en el temple por láser convencional ya que la potencia y velocidad de avance se mantienen constantes.
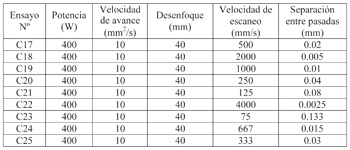
De los resultados obtenidos se puede concluir que los parámetros de barrido programados en el escáner influyen en el proceso de forma que se varía el campo térmico generado y, por tanto, el ciclo de calentamiento-enfriamiento que se da en el temple por láser de la superficie tratada. Además, como se observa en la Figura 7, en ningún caso se ha alcanzado una profundidad de capa templada por encima de los 0,5 mm de espesor. A velocidades de escaneo bajas con mayores separaciones entre pasadas la profundidad de capa templada es también mayor. Esto es debido al tiempo que se encuentra en cada ciclo sobre la temperatura de austenización, siendo este un factor con mucho peso sobre el espesor final templado.
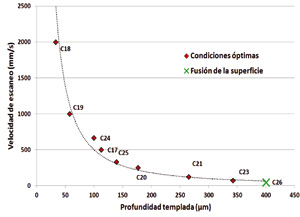
4.2 Aplicación del proceso sobre ejes de válvulas de asiento
Como ejemplo de aplicación del proceso sobre pieza real se han realizado una serie de ensayos templando con láser de forma remota mediante la estrategia de barrido continuo unos ejes de válvulas de asiento de 13.3 mm de diámetro cuyo material es acero inoxidable X45CrSi9_3. La configuración en máquina es la que se ve en la (Figura 8a), donde se usa el eje C de giro de la mesa para el movimiento de avance y el eje X del escáner como movimiento de escaneo. La anchura templada programada es de 10 mm.
Los distintos ensayos se han realizado con velocidades de avance variables entre 10 y 30 mm2/s, velocidades de escaneo entre 60 y 200 mm/s, potencias variables entre 300 y 450 W y, por último, se ha girado la pieza entre una y dos veces por ensayo. Se ha optado por velocidades de escaneo bajas ya que como se ha visto en el apartado anterior estas induces espesores templados mayores.
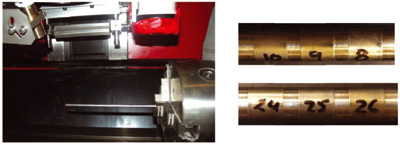
Durante la realización de los ensayos se han tenido en cuenta las distintas conclusiones sacadas en el apartado 3. Entre ellas se encuentran:
- Debido al paralelismo entre eje X de máquina de escáner se puede decir que el eje de la pieza y el barrido de escaneo son paralelos.
- Hay sincronismo entre las vueltas que da la pieza y el encendido y apagado del láser mediante el control numérico.
- Los retrasos de encendido y apagado del láser no sobreexponen de manera indeseada una zona de la pieza durante cada ensayo. Además solo se apaga y enciende el láser una vez durante cada ensayo
- Con el retraso de polígono corto no hay sobreexposición del láser en el cambio de sentido debido a una disminución de velocidad.
- Al trabajar en planos desenfocados para trabajar con anchuras de spot de 1mm, hay una distorsión de las medidas en el plano de trabajo y a los 10 mm programados habrá que sumarle un 15% en la anchura total templada.
- A la hora de hacer un control de temperatura el pirómetro se posiciona en una esquina del barrido que es donde se encuentra el pico de mayor temperatura.
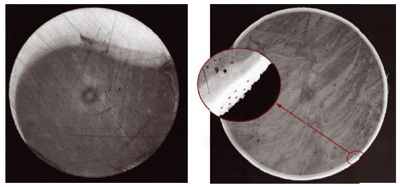
Analizando cortes transversales de los distintos ensayos se observa que con una sola vuelta y parámetros de temple agresivos (Figura 9a) el templado es muy discontinuo. Así, se observan zonas sin templar con zonas donde el temple ha profundizado hasta 4mm. Con más de una vuelta la capa templada se homogeniza pero no se han conseguido espesores templados homogéneos mayores de 500 μm (Figura 9b).
Por otro lado, la dureza inicial de 36 HRC ha llegado en todos los casos a valores medios de 62-63HRC en la capa superficial templada. Además se observa una capa intermedia un poco menor que la intermedia donde la austenización del material no ha llegado al 100% y la dureza ronda los 55 HRC. Igualmente, se han hecho distintas indentaciones de microdurezas en las zonas finales del ensayo donde existe una superposición de trayectorias y no se ha observado una bajada de dureza en el solape como ocurre en el temple por láser convencional.
5. Conclusiones
En el presente trabajo se ha puesto a punto un sistema de láser más escáner para el proceso de temple por láser remoto, un proceso todavía por estudiar. Para ello se han caracterizado distintos parámetros del sistema láser, escáner, máquina y control de temperatura.
Tras esto, con los resultados de la caracterización, se ha discutido la viabilidad del proceso poniendo como ejemplo de aplicación el templado por láser remoto de ejes de válvulas de asiento de acero inoxidable. Se han conseguido durezas de hasta 63 HRC con capas uniformes de hasta 500 μm alrededor de todo el perímetro del eje. Además, no se ha observado un reblandecimiento parcial del material en zonas de solapamiento de trayectorias.
Agradecimientos
Este trabajo se ha desarrollado dentro del proyecto ‘Tratamiento y modificación de superficies funcionales de alto valor añadido mediante radiación láser (Surfacer)’ DPI2010-20317-C02-01, financiado por el Ministerio de Economía y Competitividad.
Referencias
[1] R. Poprawe, Tailored Light 2 - Laser Application Technology, Springer, (2011).
[2] H. K. D. H. Bhadeshia. Steels for bearings, Progress in Materials Science, 57 (2012), 268-437.
[3] M. Miralles, Laser Hardening of Cutting Tools, Tesis Doctoral, Lulea University of Technology, Lulea, (2003).
[4] BLACKBIRD Robotics. “Solutions for robotic laser processing”. Disponible en la web: http://www.blackbird-robotics.de/. Consultado el 30 de enero de 2013.
[5] DMG/MORISEIKI. “Gama de máquinas LASERTEC”. Disponible en la web: http://www.moriseiki.com/. Consultado el 30 de enero de 2013.
[6] K. Kim, K. Yoon, J. Suh, J. Lee. Laser Scanner Stage On-The-Fly Method for ultrafast and wide Area Fabrication, Physics Procedia, 12 (2011), 452-458.
[7] F. Klocke, C. Brecher, D. Heinen, C. J. Rosen, T. Breitbach. Flexible scanner-based laser surface treatment, Physics Procedia, 5 (2010), 467-475.
[8] G. H. Farrahi, M. Sistaninia. Thermal Analysis of Laser Hardening for Different Moving Patterns, IJE Transactions A: Basics, Vol. 22, No 2 (2009), 169-180.
[9] R. S. Lakhkar, Y. C. Shin, M. J. M. Krane. Predictive modeling of multi-track laser hardening of AISI 4140 steel, Materials Science and Engineering A, 480 (2008), 209-217.
[10] M. K. H. Leung, H.C. Man, J. K. Yu. Theoretical and experimental studies on laser transformation hardening of steel by customized beam, International Journal of heat and Mass Transfer, 50 (2007), 4600-4606.
[11] M. F. Chen, Y. P. Chen, W. T. Hsiao. Correction of field distortion of laser marking systems using surface compensation function, Optics and Lasers in Engineering, 47 (2009), 84-89.