Grind Hardening, el proceso que permite rectificar y templar simultáneamente
Los inicios del grind hardening han sido difíciles debido a la cantidad de problemas que inicialmente se presentaban , y que hacían dudar de la viabilidad práctica de el proceso. Entre estos problemas están: la suciedad producida en la máquina, el control de las chispas, la repetitividad el proceso, la duración de la muela , la calidad de la estructura del material , el conocimiento de las condiciones de mecanizado, la influencia de la geometría de la pieza….
En la figura 1 se puede ver una fotografía de un proceso de grind hardening. Como se ve el proceso da lugar a un volumen importante de chispas con los problemas asociados que ello implica: necesidad de evacuación de las mismas, formación de costras en el interior de la máquina…
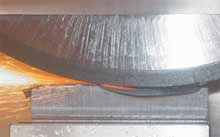
En un principio la única manera de generar suficiente calor es teniendo la muela seca en el punto de contacto con la pieza. Para conseguir este efecto y simultáneamente enfriar la muela se han desarrollado dispositivos como el de la figura dos. Estos dispositivos sirven para enfriar la muela con un chorro de líquido refrigerante en un punto y a continuación secar la muela durante su recorrido entre el punto en que se refrigera y el punto en que trabaja. Si la muela está totalmente seca se obtiene un mayor calor (y por tanta se alcanzan mayores profundidades de capa templada ), sin embargo el esfuerzo térmico crece notablemente. Cuando se realiza grind hardening con la muela totalmente seca las chispas que salen son de un material fundido que se pega a la superficie de la máquina. Una vez pegado es muy difícil de eliminar. Actualmente existen muelas capaces de generar el suficiente calor aún refrigerando en la propia pieza. Con este nueva forma de trabajo el problema de la adherencia a la máquina de las chispas queda resuelto.
Otra forma de trabajo es con la muela no totalmente seca, de manera que existe algo de lubricación en el proceso de arranque de material . De esta forma tampoco se da el problema de las virutas, aunque las capas obtenidas son de menor profundidad.
En la figura 2 se expone un sistema de refrigeración y secado de muelas para grind-hardening.
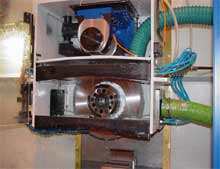
El grind hardening siempre se hace de una sola pasada. En rectificado cilíndrico e,n la entrada de la muela sobre la pieza transcurre un tiempo hasta que se genera el suficiente calor para que endurecer el material. La muela va avanzando produciendo una capa de profundidad constante. Cuando llega al final de la vuelta no hay suficiente material para arrancar y entonces no se produce el suficiente calor y no hay endurecimiento. La pieza queda con una zona donde el material está en las mismas condiciones. Este problema hace que en rectificado cilíndrico la solución sea muy difícil. En este momento se están llevando algunas líneas de investigación en el centro tecnológico Ideko para intentar solucionar este problema.
En la figura 3 se representa esquemáticamente el overlaping en rectificado cilíndrico.
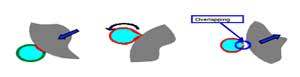
En rectificado plano hay tres tipos de solapamiento.
- El efecto de borde producido antes de que la muela empiece a comer con una pasada suficiente. Caso 1.
- El efecto producido por mecanizar una pieza de mayor anchura de la muela en varias pasadas. Caso 2.
- El efecto producido por retirar la muela y continuar el mecanizado. Caso 3.
Una forma de evitar el overlapping en rectificado plano es :
- El caso 1 , utilizando una pieza algo mas larga y cortando la zona inicial.
- El caso 2, utilizando una muela mas ancha que la pieza
- El caso 3 solo se da si la pieza es lo suficientemente larga.
La solución de estos problemas en rectificado plano permitiría incrementar el campo de aplicación de la técnica, se abriría un abanico de posibilidades en piezas y anchas.
Actualmente se están desarrollando nuevas muelas de CBN con el objeto de rectificar piezas muy largas.
¿Que se pretende obtener cuando se realiza grind hardening ? En primer lugar repetitividad en el proceso, en segundo lugar profundidad de capa suficiente y en tercer lugar que la estructura del material obtenido sea correcta.
En la figura 5 se expone el diagrama de microdurezas de una probeta de acero F1252 en la que se ha realizado un ensayo de grind hardening. Puede verse que hay dos zonas , una zona templada ,en la que la dureza es mas o menos constante , y una segunda zona en la que la dureza decae.
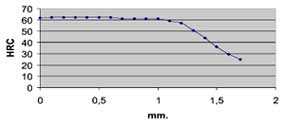
Las diferencias entre el grind hardening y el rectificado convencional son muy importantes, y aún necesitándose una rectificadora de mayor rigidez que las convencionales y con algunos dispositivos especiales las ventajas obtenidas son tan grandes que es verdaderamente difícil encontrar un caso en el que siendo aplicable , no suponga una mejora en todos los sentidos frente a los procesos tradicionales. No solamente se elimina el templado de las piezas sino que las severas condiciones de mecanizado necesarias eliminan la necesidad del fresado. En la figura 6 se presenta un diagrama comparativo de las operaciones y máquinas necesarias en un proceso tradicional y en uno de grind hardening.
En la figura 6 se expone como para una operación en la que es necesario dos transportes y tres máquinas , cuando se utiliza grind hardening pasa a necesitarse una sola máquina. Las mejoras de coste, fiabilidad del proceso y tiempos de fabricación son inmediatas.
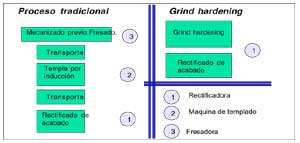