Sistema de visión multicámara para un taladrado y fresado más preciso de piezas aeronáuticas
Pablo Puerto, investigador del equipo de Visión y perteneciente al grupo de Diseño e ingeniería de precisión en Ideko
21/07/2023Aplicar soluciones de robótica ofrece grandes ventajas a la industria ya que aportan gran flexibilidad y versatilidad en operaciones de baja fuerza de mecanizado, procesos de lijado, taladrado o de recanteo para eliminar el material de las piezas. En este escenario, los brazos robóticos se están convirtiendo en herramientas de gran interés para sectores como la automoción y la logística de montaje. Sin embargo, otros sectores que requieren de una mayor precisión también buscan aprovechar las ventajas de esta tecnología para la optimización de procesos de fabricación más complejos.
En los últimos años Ideko está apostando por desarrollar tecnologías, en concreto, la visión artificial, que permitan a los robots ser capaces de localizar y manipular con precisión una gran variedad de piezas y herramientas. Una de las últimas soluciones desarrolladas por el centro son los sistemas de visión multicámara, gracias a los cuales se ha conseguido incrementar la precisión de los robots para determinados procesos de fabricación a un coste mucho más asequible que los sistemas actuales.
En el presente artículo de investigación se muestra un innovador sistema multicámara diseñado por el centro tras años de investigación que cumple con los requisitos de precisión en tareas de fresado y taladrado de piezas aeronáuticas. El estudio, llevado a cabo por el equipo de investigadores de ingeniería de precisión de Ideko, ofrece una solución eficiente y precisa para mejorar los procesos de fabricación en la industria aeroespacial.
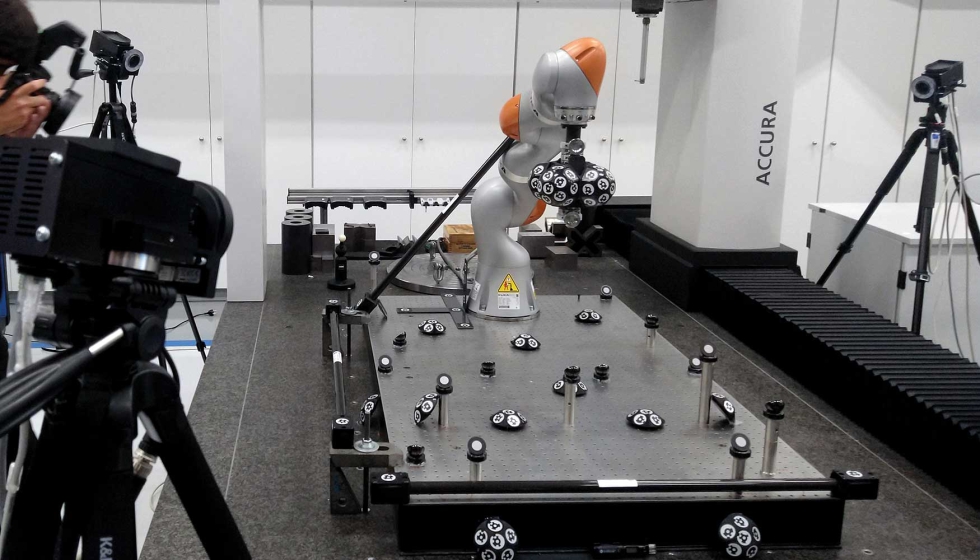
Este sistema ha utilizado un enfoque de lazo cerrado para corregir la posición del extremo ‘end-effector’, el dispositivo situado al final del brazo del robot, en relación con una referencia estática. Esto se logra mediante el seguimiento de la posición de ambos elementos mediante un sistema de múltiples cámaras y marcadores colocados en sus superficies. El desafío principal ha consistido en encontrar un sistema auxiliar capaz de medir con precisión estos marcadores en volúmenes de trabajo grandes, superando los 3 metros cúbicos, garantizando así los niveles deseados de precisión.
En la etapa inicial de investigación, se han comparado tres tecnologías: una máquina de medición por coordenadas (CMM), un láser tracker (LT) y un sistema de fotogrametría portátil (PP), siguiendo las pautas de la norma VDI/VDE 2634-parte 1 para la medición de la referencia estática. Estas pruebas han permitido seleccionar la mejor alternativa para el escenario industrial y realizar pruebas adicionales con cargas útiles mayores que las utilizadas en el entorno de laboratorio.
Sin medición no hay precisión
La precisión se ha convertido en un factor crucial en procesos a gran escala, y algunos proyectos europeos destacados, como LaVA o DynaMITE del Programa Europeo de Metrología para la Innovación e Investigación de Empir, están abordando estos desafíos desde diversas perspectivas para sectores críticos como la industria aeroespacial, naval y energética.
En estos sectores, el seguimiento del end-effector y la posición de vehículos guiados automatizados (AGV) se está volviendo fundamental para avanzar en tareas como el montaje de grandes estructuras, inspecciones y fabricación. Además de la precisión, la latencia de estos sistemas también influye en los tiempos de producción.
El láser tracker (LT) es la herramienta más utilizada para estimar la posición del punto central de la herramienta (TCP) debido a su confiabilidad y facilidad de uso. Por esta razón, se emplea en numerosas calibraciones de robots. Sin embargo, esta tecnología requiere un accesorio adicional, como T-MAC de Leica, para medir los seis grados de libertad (DoF), lo que representa un coste adicional significativo. Además, estos accesorios, que generalmente se colocan en la herramienta del robot, añaden peso y generan niveles más altos de incertidumbre.
En este contexto, la tecnología de fotogrametría se presenta como una alternativa real al LT, ya que puede medir los seis grados de libertad de los objetos agregando marcadores retrorreflectantes en los elementos a rastrear. Además, su coste es menor que el del LT con el accesorio requerido.
La presente investigación se centra en cómo industrializar un sistema de rastreo multicámara utilizando la estrategia eye-to-hand, rastreando el extremo del brazo, lo que permite cerrar el bucle del control y reducir las posibilidades de error durante el taladrado.
Comprender la relevancia de la incertidumbre de los parámetros extrínsecos en los sistemas de medición utilizados en aplicaciones industriales es otro aspecto fundamental. Para abordarlo, en el marco de la investigación, se han realizado estudios comparativos utilizando tres sistemas de medición diferentes: la Máquina de Medición de Coordinación (CMM), el Laser Tracker (LT) y un sistema de Fotogrametría Portable (PP).
La CMM se ha considerado como la referencia principal, ya que proporciona un bajo nivel de incertidumbre en las mediciones y toma el rol de “ground truth”. Sin embargo, debido a las limitaciones de la CMM para medir objetos fuera de su alcance, los sistemas LT y PP se evaluaron como candidatos para medir los marcadores de referencia en piezas de gran volumen.
La comparación entre el LT y el PP se ha llevado a cabo, y posteriormente se ha realizado una validación en un escenario industrial siguiendo las pautas establecidas en la guía VDI2634 parte 1. En esta validación, el LT se ha utilizado como “ground truth” para rastrear el end-effector de un brazo robótico, mientras que simultáneamente se ha rastreado por un sistema de multicámara (MC). Esta validación ha permitido evaluar la precisión y confiabilidad de los sistemas de medición en un entorno industrial real.
Además de la validación, de cara a demostrar la utilidad de los sistemas de medición se ha llevado a cabo una aplicación industrial específica, en la que se ha registrado la temperatura de las articulaciones al mismo tiempo que se rastreaba el end-effector durante un ciclo de calentamiento. El objetivo principal era determinar la desviación inducida por la temperatura y evaluar la capacidad de los sistemas de medición para capturar y compensar este efecto.
La búsqueda de mayor precisión en los procesos a gran escala ha impulsado el estudio y desarrollo de sistemas de medición avanzados. La comparación entre diferentes tecnologías y la validación en entornos industriales reales son pasos clave para garantizar la selección adecuada de los sistemas de medición y su aplicabilidad en diversos contextos industriales. Además, la investigación se ha enfocado en abordar desafíos específicos, como la compensación de desviaciones inducidas por factores externos, como la temperatura, a fin de optimizar la precisión y la eficiencia en las tareas industriales.
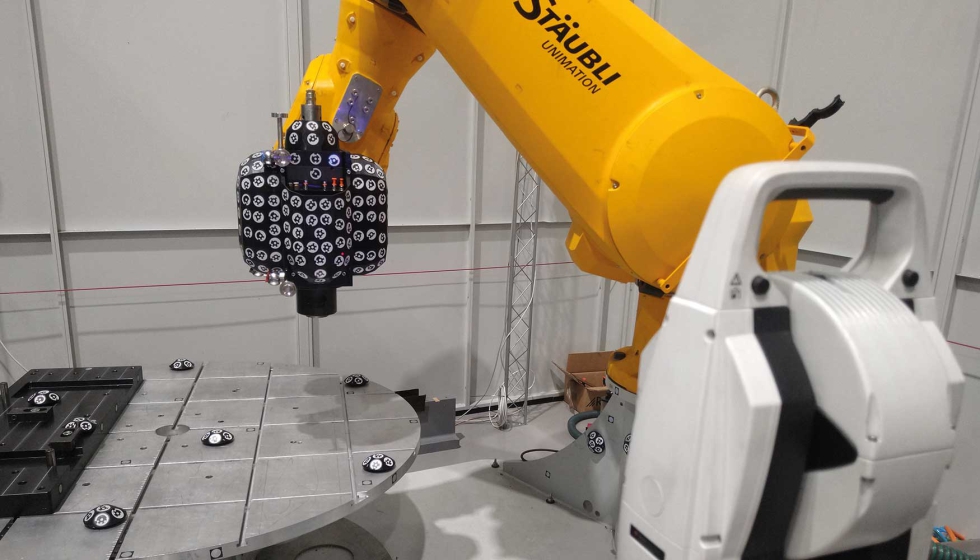
Fotogrametría, una alternativa eficiente
La fotogrametría está emergiendo como una alternativa prometedora para satisfacer los requisitos de los robots industriales, al tiempo que permite minimizar la inversión requerida. Antes, la fotogrametría requería la fijación de marcadores ópticos físicos al objeto y una referencia para resolver las posiciones relativas entre ellos. Sin embargo, actualmente se está trabajando en los propios marcadores naturales de la pieza, como agujeros o formas, para resolver este problema.
Esta técnica ha permitido guiar robots cuadrúpedos dinámicos en escenarios industriales sin la necesidad de marcadores artificiales. Aunque esta aproximación es prometedora, para cumplir con los requisitos de incertidumbre de medición, todavía es necesario detectar marcadores ópticos retrorreflectantes para rastrear la pieza.
No obstante, los marcadores no son el único componente crucial en una aplicación exitosa de la fotogrametría. Se deben tener en cuenta varios puntos críticos, que incluyen los parámetros intrínsecos y extrínsecos de la cámara, la referencia estática y dinámica, así como la distribución de los marcadores en los objetos. Además, la detección 2D es un factor clave que ha sido ampliamente estudiado.
Los parámetros intrínsecos de la cámara se utilizan para corregir la distorsión de la lente y del sensor. Varios modelos se han propuesto para corregir esta distorsión y llevar a cabo la calibración. Por otro lado, los parámetros extrínsecos son la posición y orientación relativa de la cámara con respecto a una referencia. En sistemas de fotogrametría, los marcadores codificados suelen ayudar a calcular esta posición. En el caso de un sistema de múltiples cámaras (MC), se requiere una medición previa para determinar las dimensiones del objeto de referencia y del objeto rastreado.
Estos parámetros pueden resolverse tanto en una tarea previa al proceso -referencia estática- como en tiempo real, es decir, durante las mediciones -referencia dinámica-. La referencia estática se recomienda cuando las cámaras están en posiciones estáticas con respecto a las referencias y existe la posibilidad de que un número significativo de puntos de referencia esté oculto por el objeto. Por otro lado, la referencia dinámica adquiere relevancia cuando la referencia se mueve con respecto a la cámara, o si las cámaras pueden moverse debido a una sujeción flexible o desviación térmica.
La distribución de los marcadores en el objeto es otro factor a considerar. Una distribución incorrecta puede resultar en una solución con alta incertidumbre. Es bien conocido que un objeto 3D ayuda a reducir la incertidumbre de la medición.
La distribución adecuada de los marcadores y una referencia 3D precisa son elementos esenciales en la fotogrametría industrial. El posicionamiento correcto de la cámara con respecto al volumen de trabajo a veces puede resultar un desafío. Para resolver este problema, Hänel et al. [1] han desarrollado un método robusto para lograr una ubicación fiable de la cámara. Este enfoque permite obtener un sistema de referencia mejorado, donde se mide la referencia para calcular los parámetros extrínsecos de la cámara en escenarios a gran escala.
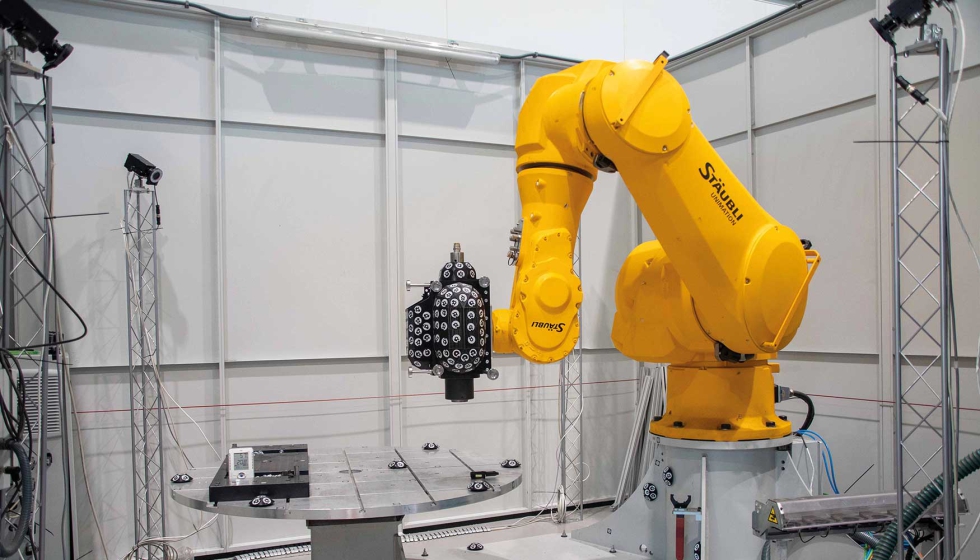
Al igual que en el caso del Láser Tracker (LT), la distribución de puntos de referencia es relevante para obtener resultados fiables en los sistemas multicámara (MC). La alta incertidumbre de medición puede ocasionar un emparejamiento incorrecto de las cámaras. Sin embargo, con la fotogrametría, es posible utilizar fuentes adicionales para medir los puntos de referencia. Por ejemplo, tanto la Máquina de Medición de Coordinación (CMM) como el LT pueden medir estos puntos, además de la fotogrametría en sí. Kang et al. [2]. exploraron un enfoque diferente mediante el uso de una plataforma giratoria para mover el artefacto y obtener mediciones más precisas.
Dentro de la investigación, también se ha estudiado la relevancia de la incertidumbre de la nube de referencias. La novedad de este estudio radica en determinar qué tecnología, LT o PP, es más adecuada para medir el punto de referencia en un sistema MC. Si bien la fotogrametría portátil (PP) se utiliza regularmente para medir puntos de referencia, este documento determinará si el Láser Tracker (LT) puede mejorar la precisión de los sistemas MC.
Una vez que esta tecnología esté madura, un sistema de multicámara permitirá la colaboración entre humanos y robots, favoreciendo que ambos trabajen en el mismo espacio. Este sistema multicámara puede prevenir colisiones y proporcionar un canal de comunicación a través de gestos. Sin embargo, la comunicación efectiva entre robots y humanos sigue siendo un desafío importante en este ámbito.
Los avances en fotogrametría están demostrando ser una opción viable para satisfacer los requisitos de los robots industriales, al tiempo que consiguen minimizar la inversión. La distribución adecuada de marcadores y una referencia precisa, junto con el desarrollo de métodos robustos para la ubicación de cámaras, contribuyen a mejorar el cálculo de los parámetros extrínsecos. El estudio comparativo entre LT y PP para medir puntos de referencia en sistemas MC añade un nuevo enfoque a la investigación en fotogrametría. La futura implementación de sistemas multicámara facilitará la colaboración humano-robot.
La metodología utilizada en este estudio se centra en medir la referencia para el cálculo de los parámetros extrínsecos que permiten calcular la colocación de las cámaras en un sistema multicámara. Este aspecto resulta crucial para poder industrializar dicho sistema debido a las limitaciones de precisión que involucra. Para llevar a cabo este análisis, dentro de la investigación se ha seleccionado una Máquina de Medición de Coordinación (CMM) como referencia de trazabilidad base y se ha comparado con dos tecnologías a gran escala: Laser Tracker (LT) y fotogrametría portátil (PP).
En el marco del estudio, se ha realizado una comparación del rendimiento de las tres tecnologías, considerando que el CMM presenta un rendimiento dos veces mejor en orden de magnitud (1 μm) que los dos sistemas estudiados (100 μm). Se han medido los marcadores de referencia tres veces por tipo de marcador, y se ha llevado a cabo un ajuste óptimo (best-fit) para que coincidieran todas las mediciones. También se ha analizado la repetibilidad de los marcadores, comparando la precisión con las mediciones del CMM.
Una vez obtenida la referencia, se ha realizado un ensayo para verificar el rendimiento del sistema multicámara. Este ensayo ha consistido en colocar el objeto rastreado en varias posiciones y resolverlas. Durante el ensayo, el único punto modificado han sido los valores de referencia de los tres tipos de marcadores utilizados a fin de estudiar su influencia. Para garantizar que el cambio único fuera la fuente de medición de la referencia, se han tomado las mismas fotografías y sólo se ha modificado dicha referencia en el proceso de cálculo. La suposición principal era que el robot no se movía entre las diferentes mediciones, independientemente de la posición.
Además, se ha repetido la misma medición 5 veces en una misma posición en las ubicaciones probadas, y se ha obtenido una repetibilidad de 0,003 mm (desviación estándar k = 1). Este valor es más alto que el de un elemento fijo debido al contacto del CMM con el robot.
La metodología utilizada para comparar las tecnologías se ha basado en la norma alemana VDI/VDE 2634 parte 1, la cual se emplea para calcular el error de medición de longitud (LME) en un sistema de medición punto a punto. La metodología utilizada en este estudio ha consistido en medir la referencia extrínseca para calcular la colocación de las cámaras en un sistema multicámara.
Los autores han adaptado esta guía, optando por barras virtuales en vez de físicas, implementando a su vez la recomendación de la distancia relativa del volumen de prueba. Para llevarlo a cabo, se ha utilizado un robot que ha ayudado en la colocación y la posición espacial del objeto, verificando la distancia con el CMM en cada posición. Esta distribución de barras virtuales ha permitido estimar el error en el volumen con un esfuerzo mínimo.
En cada barra virtual probada, el robot ha movido el objeto rastreado al origen y luego se ha dirigido a otras posiciones. La desviación se ha determinado como la diferencia entre las mediciones del CMM y las del sistema multicámara utilizando un lado de la barra como origen. Cabe destacar que el robot no ha participado en la cadena de incertidumbre, ya que la posición ha sido medida por el CMM.
Resultados
Este artículo de investigación ha abordado la medición de marcadores de referencia con un sistema multicámara para grandes piezas. Se han realizado pruebas comparativas en un escenario de laboratorio para evaluar el rendimiento de las tecnologías CMM, LT y PP en la medición de marcadores de referencia. El CMM se ha utilizado como referencia de trazabilidad, mientras que LT y PP se han considerado posibles opciones para mediciones en volúmenes a gran escala. Según los resultados, ambas tecnologías han ofrecido resultados similares, cumpliendo con los requisitos de incertidumbre posicional de la industria robótica, lo que los hace aplicables al sector aeroespacial.
Posteriormente, se replicaron las pruebas en condiciones industriales. Siguiendo las conclusiones de las pruebas de laboratorio, el LT se utilizó como referencia y el PP se encargó de medir los marcadores de referencia. El sistema multicámara se instaló en una celda robótica, adaptando las posiciones de las cámaras al espacio limitado debido a las paredes del recinto donde se encontraba el sistema robótico. A pesar de que las condiciones fueran más desafiantes, el sistema ha demostrado un incremento en el valor de LME debido al menor espacio y al mayor volumen. También se ha llevado a cabo un nuevo enfoque para determinar el comportamiento del robot durante un ciclo de calentamiento, ajustando parámetros y modelando el robot para obtener datos confiables.
Además, se ha realizado una prueba de acuerdo con la norma ISO 92831 para evaluar la mejora en la incertidumbre de posición del robot mediante el uso del sistema multicámara. También se ha estudiado el ciclo de calentamiento para comprender el comportamiento del robot al comenzar a trabajar desde un estado enfriado.
Para la industrialización de esta solución es crucial que los marcadores en el extremo del robot mantengan su posición relativa con respecto al end-effector del robot, al igual que las piezas con respecto a los puntos de referencia. Si esta suposición se rompe, se compromete la precisión del sistema. Asimismo, en el diseño de un sistema multicámara hay que tener en cuenta la limitación en cuanto al número de cámaras necesarias para lograr un equilibrio adecuado entre coste y beneficio. También es necesario considerar la posible obstrucción de la visión del end-effector por elementos externos, lo que puede afectar a la información proporcionada por el sistema multicámara. Por lo tanto, se recomienda realizar un estudio virtual (digital-twin) previo exhaustivo a fin de predecir la influencia y garantizar la precisión desde diferentes puntos de vista.
Gracias al incremento de la precisión debido al sistema multicámara, se abre una nueva perspectiva en la automatización de procesos de fabricación, permitiendo a otros sectores manufactureros beneficiarse de la versatilidad de los brazos robóticos. Este avance tecnológico tiene el potencial de optimizar los procesos de fabricación en el sector aeroespacial, mejorando la calidad y la eficiencia de las operaciones.
Esta investigación representa un valioso avance en la integración de la robótica en la industria y abre las puertas a futuras mejoras en la fabricación de componentes aeronáuticos y otros productos manufacturados de alta precisión.
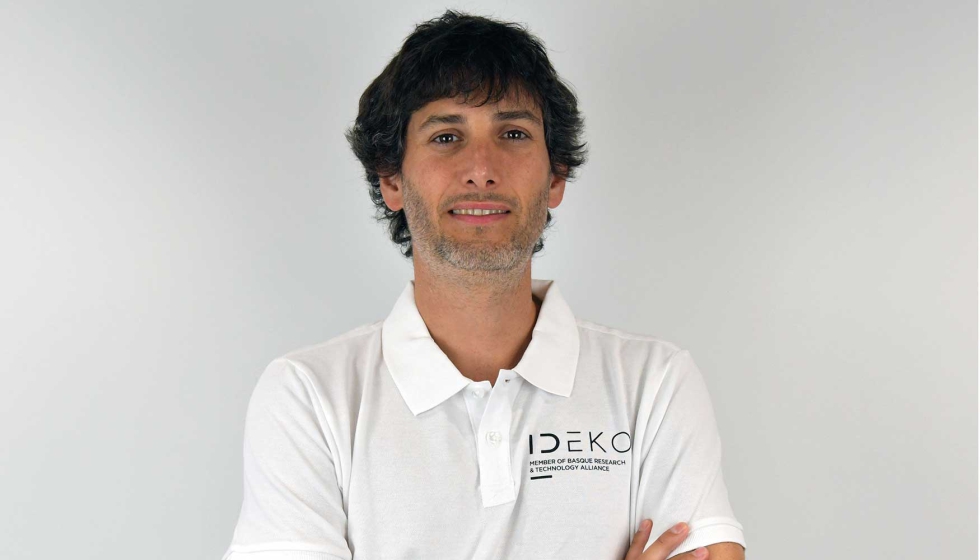
Referencias
[1] Hänel, M.L.; Schönlieb, C.-B. Efficient Global Optimization of Non-Differentiable, Symmetric Objectives for Multi Camera Placement. IEEE Sens. J. 2021, 22, 5278–5287. [Google Scholar] [CrossRef].
[2] Kang, H.; Seo, Y.; Park, Y. Geometric Calibration of a Camera and a Turntable System Using Two Views. Appl. Opt. 2019, 58, 7443. [Google Scholar] [CrossRef].