Entrevista a Elena Arias, vicepresidenta de Service de Vestas para Sur de Europa, África y Oriente Medio
En los próximos años, el mercado de la operación y mantenimiento de parques eólicos en España pasará de los 30 GW instalados actualmente a unos 50 o 60 GW instalados en 2030. Este aumento explosivo de nuestra flota viene acompañado de una nueva generación de aerogeneradores más grandes, más potentes y más complejos. La vicepresidenta de Service de Vestas para Sur de Europa, África y Oriente Medio, Elena Arias, comparte su visión sobre sobre la evolución del mercado español de O&M y la propuesta de Vestas para liderar esta expansión.

¿Cómo definiría el mercado de O&M actual?
Estamos viendo una flota cada vez más heterogénea, que abarca desde pequeños aerogeneradores con 800 KW de potencia y palas de 25 metros de longitud a nuevos modelos con 6 MW de potencia y palas que pueden superan los 80 metros.
Los aerogeneradores más antiguos y analógicos empiezan a convivir con modelos más grandes que incorporan desarrollos tecnológicos y procesos en continua evolución: softwares, sensores, drones, herramientas SCADA, sistemas de ciberseguridad e incluso robots que proporcionan constantes avances en eficiencia, seguridad y rentabilidad.
¿Cómo influye el tamaño en el mantenimiento de un aerogenerador?
Influye la complejidad tecnológica y efectivamente, el tamaño. Los aerogeneradores modernos permiten utilizar menos posiciones por parque eólico. Hace diez años, un parque de 30 MW estaba formado por 20 o 30 aerogeneradores. Hoy, podemos alcanzar esta potencia con solo cinco aerogeneradores de 6 MW cada uno.
¿Por qué es esto importante? Principalmente, porque el mantenimiento inadecuado de un aerogenerador de 6 MW puede salir caro. No solo por el coste creciente de las reparaciones, que pueden implican izar una nueva multiplicadora o una pala de varias toneladas a 110 metros de altura. La diferencia es que detener un aerogenerador averiado de 800 KW de potencia durante días, cuando este representaba el 2 por ciento de la producción de una planta, no suponía un coste significativo en términos anuales. Pero si el aerogenerador alcanza los 6 MW de potencia y representa el 20 por ciento de la producción total de energía del parque eólico, entonces una parada no programada provocaría una pérdida más cuantiosa, tanto en términos energéticos como económicos.
Hoy, un mantenimiento inadecuado genera un riesgo grande contra la rentabilidad del parque. A veces, puede no notarse a corto plazo, pero conforme va cumpliendo años, los riesgos de averías o paradas no programadas aumenta.
¿Cómo enfoca Vestas este reto?
Nuestra propuesta busca optimizar el caso de negocio de nuestros clientes desde el primer hasta el último año de vida del parque eólico. El año pasado anunciamos los primeros contratos de servicio por 35 años de duración. Implica tener un alto grado de confianza en nuestra tecnología y en la calidad del mantenimiento que ofrecemos.
Como líderes mundiales en mantenimiento, buscamos garantizar no solo una óptima condición de las máquinas, sino también una buena disponibilidad de las máquinas a lo largo de la vida útil del proyecto. Nuestra tarifa anual puede parecer más elevada que la de un ISP, pero a cambio reducimos el riesgo a corto y largo plazo y podemos garantizar un mayor retorno final del activo durante toda la vida útil de los aerogeneradores, contribuyendo también a alargarla. Para ello ofrecemos contratos por disponibilidad y rendimiento: La alta confiabilidad de nuestros datos nos permite ofrecer garantías no sólo sobre el tiempo de funcionamiento de la máquina, sino sobre la cantidad de energía que ésta puede generar durante el año.
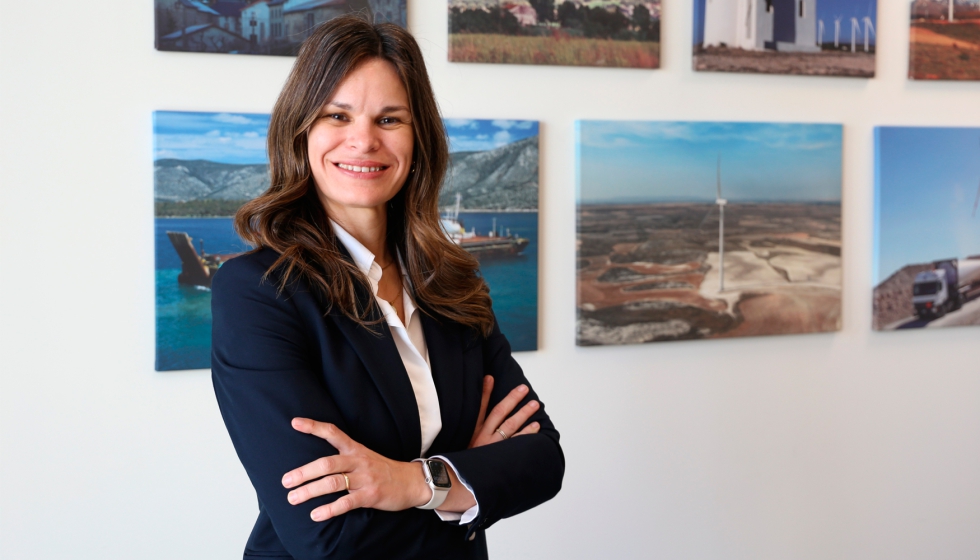
¿Qué factores pueden garantizar estos altos niveles de disponibilidad? Se habla mucho de la revolución de la inteligencia artificial. ¿Es tan determinante?
Hay muchos factores, pero empecemos por el tecnológico. En Vestas nos beneficiamos enormemente de la inteligencia artificial. Damos servicio a unos 157.000 aerogeneradores en todo el mundo, que equivalen a 152 GW de los que 8,5 GW son Multimarca. La información recabada al minuto por cientos de sensores de vibración, temperatura, etc. en cada aerogenerador nos permite identificar problemas reiterados y profundizar en sus causas y soluciones. Es la base de lo que ya se conoce como mantenimiento predictivo: La monitorización de nuestra flota global nos permite identificar posibles desviaciones y adelantarnos a posibles fallos en cada unidad.
Nuestra flota en España, de unos 6,5 GW, se beneficia constantemente de este aprendizaje global, lo que nos proporciona una importante ventaja competitiva.
A la inteligencia artificial hay que sumar el impacto de otros avances tecnológicos, como el uso de drones para la inspección de palas.
¿Están trabajando en alguna innovación importante en este campo?
Vestas realiza un constante trabajo de I+D para optimizar procesos y hacerlos más eficientes y sostenibles. Por ejemplo, a través de Skyrex, exploramos nuevas tecnologías para construir torres más altas y reponer componentes eólicos con mayor rapidez. Estas grúas nos permitirán elevar la altura de buje y capturar más viento, al tiempo que reducirá el tiempo y el riesgo necesario para reparar componentes del rotor y de la nacelle.
Otro ejemplo es BladeRobots, una solución robótica automatizada para el mantenimiento del borde de ataque de las palas eólicas.
Hasta ahora, este mantenimiento lo realizan equipos humanos de trabajos verticales que lijan, limpian y aplican material nuevo a los bordes en un proceso manual que se hace en altura, suspendidos sobre cuerdas o a través de plataformas externas. Los robots pueden realizar estas tareas en unas horas, manteniendo las palas de dos o más aerogeneradores en un solo día, y lo hacen de manera más segura.
Por último, continuamos buscando mejoras en el uso de Smart Data para poder realizar predicciones meteorológicas hiperprecisas y poder calcular la generación de energía que ofrecerá la planta en las próximas horas.
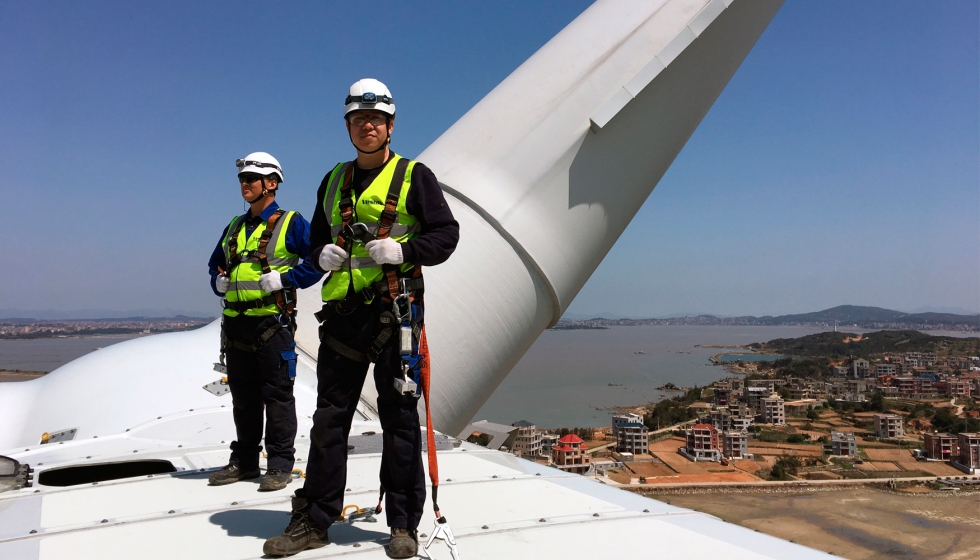
Ha mencionado la reducción del tiempo de mantenimiento humano. ¿Cómo evolucionará este campo? ¿Suponen estas innovaciones la reducción progresiva del número de técnicos?
En realidad, nos dirigimos a un escenario opuesto. En los próximos años se va a doblar el número de técnicos de Service. En España, el sector eólico empleará entre 60.000 y 70.000 personas en 2030, el doble que en la actualidad. Esto nos lleva a comentar la importancia del factor humano para garantizar la calidad del mantenimiento de parques eólicos.
En primer lugar, es fundamental actuar siguiendo los más altos estándares de seguridad. La calidad del mantenimiento empieza en la seguridad de todo nuestro personal. No es solo un tema ético. Repercute directamente en la calidad de todos los procesos. Siempre ha sido un reto del sector, pero lo va a ser aún más, pues requiere generar y transmitir una cultura en la que la seguridad sea la primera y la última preocupación del día. Al doblar el número de técnicos en tan solo 5 años, las empresas tendremos que hacer un esfuerzo mayúsculo para difundir esta cultura de una manera rápida y eficaz.
A pesar del crecimiento de nuestra flota, en Vestas hemos conseguido bajar nuestra tasa de lesiones de 3.3 por millón de horas trabajadas en 2022 a 3.0 en 2023. Es un avance, pero aún estamos lejos de las 0.6 lesiones que nos hemos fijado como objetivo en 2030.
Otro factor determinante en este contexto de expansión es el conocimiento y la formación de los equipos, que deben dar servicio a tecnologías cada vez más diversas y complejas, al tiempo que incorporan nueva mano de obra. Aquí también marcamos la diferencia, porque nuestros técnicos se benefician de la experiencia acumulada manteniendo el portafolio eólico más diverso del mundo desde hace más de 40 años.
P. Por último, quería preguntarle sobre los últimos avances en sostenibilidad para eliminar las emisiones de CO2 de la industria eólica y mejorar la gestión de los residuos.
Primero, es necesario aclarar que en términos de Kg de CO2 emitidos por MWh de energía generada, la eólica es unas 170 veces más limpia que el petróleo y 5 veces más limpia que la energía solar, por ejemplo[1]. Dicho esto, en 2020 nos marcamos el reto de alcanzar la neutralidad en carbono en nuestras propias operaciones y reducir un 45% la intensidad de las emisiones de nuestra cadena de suministros antes de 2030. Es un enorme reto que creo muestra nuestra determinación para liderar la transición energética mundial.
Estoy convencida de que la electrificación de nuestra flota de vehículos y el compromiso conjunto con nuestra cadena de suministro nos acercará a estos objetivos en los próximos años.
En cuanto a la gestión de residuos, también me gustaría aclarar que el 85% de los aerogeneradores son reciclables. El principal problema para avanzar hacia una economía totalmente circular es la reciclabilidad las palas eólicas, que hasta ahora se consideraban como un material compuesto no reciclable.
En 2023, Vestas presentó una solución química para reciclar palas fabricadas con resina epoxi, sin necesidad de cambiar el diseño o la composición de los materiales de la pala. La solución permite descomponer la resina en materiales vírgenes. Se puede aplicar a palas actualmente en operación, eliminando la necesidad de rediseñar las palas o desecharlas en vertederos cuando se desmantelen. Al mismo tiempo, permite reutilizar las palas para la fabricación de nuevas palas.
En O&M, también hacemos un gran esfuerzo para aumentar la circularidad de la industria. El 80% de los componentes principales que utilizamos para mantenimiento son renovados. Cumplen los mismos estándares de calidad y testeo que los nuevos, y reducimos un 45% las emisiones de CO2. En nuestra estrategia de circularidad, buscamos conseguir que el 30% de los todos componentes utilizados para mantenimiento sean renovados.
Creemos que es son pasos importantes para alcanzar la circularidad de la industria, pero todavía queda camino por recorrer. La reciclabilidad es solo una parte del objetivo, también hay que generar una industria rentable alrededor del reciclaje. Para ello, debemos seguir investigando y probando mejoras en todo el ciclo de vida de los aerogeneradores.
[1] Fuente: LCA Assessment de Esphera (2023) e informe World average (2023) de la IEA.