UTE Línea 3 de Metro, Bilbao. Impermeabilización de las galerías con la membrana proyectable MasterSeal 345
Con el objetivo de solventar los notables desafíos que presenta el revestimiento de las galerías de acceso OS-01 y OS-10 de la nueva Línea 3 del Ferrocarril Metropolitano de Bilbao se han analizado diversas alternativas, concluyendo que una solución con un revestimiento impermeabilizado de hormigón proyectado permite conseguir una durabilidad y calidad de acabados satisfactoria. La solución propuesta se denomina ‘Single Shell’ y en este artículo BASF Construction Chemicals Spain describe en qué consiste.
1. El proyecto
La Línea 3 del Ferrocarril Metropolitano de Bilbao es una nueva línea de metro que está actualmente en construcción, con una longitud final de 5.885 metros y 7 estaciones. Esta nueva línea está proyectada y construida por Euskal Trenbide Sarea (ETS-RFV)
La futura línea dará servicio a los barrios de la zona norte de Bilbao y tendrá conexión con las Líneas 1 y 2 en la estación de Casco Viejo.
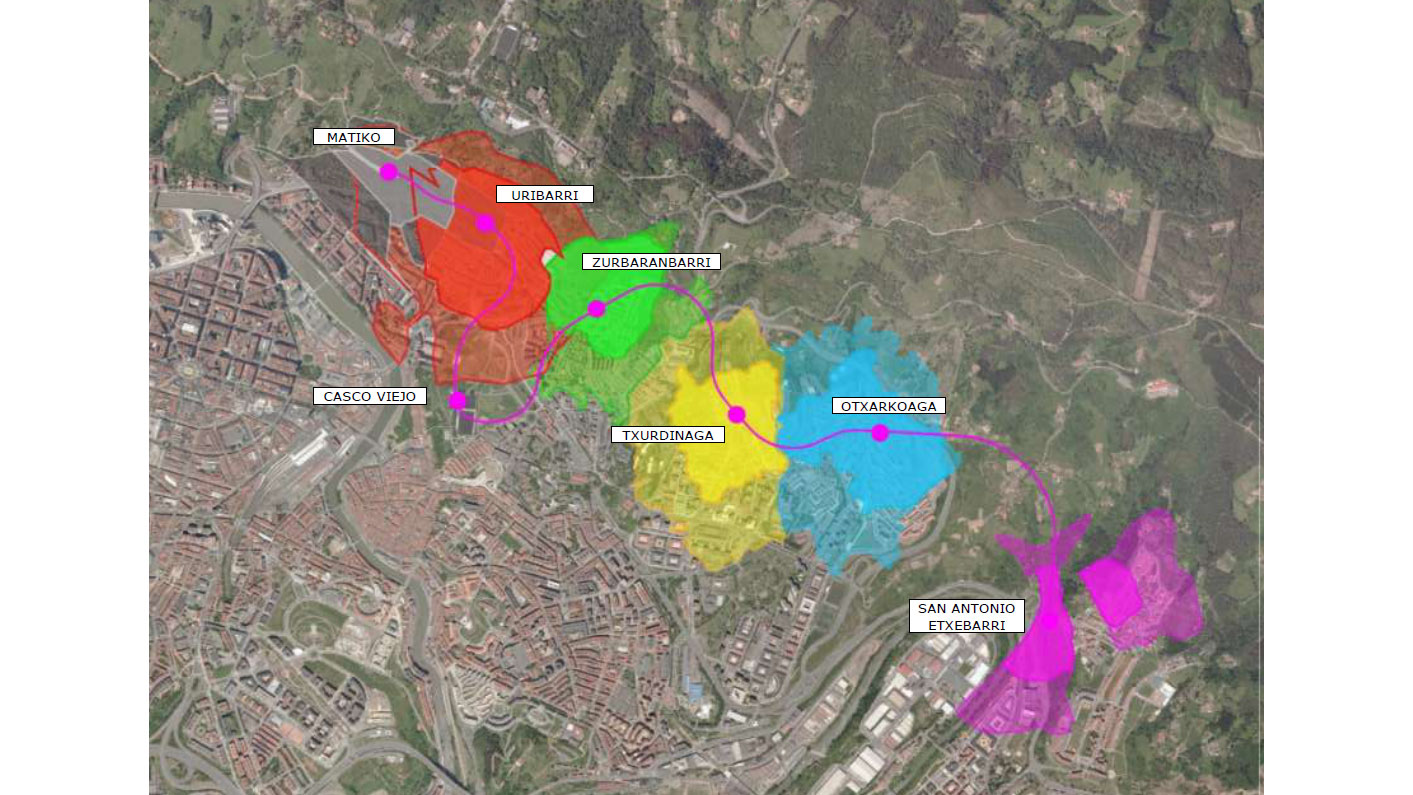
UTE Línea 3, una Unión Temporal de Empresas formada por Comsa, Nortúnel y Cycasa, fue la adjudicataria del tramo comprendido entre las estaciones de San Antonio de Etxebarri y Txurdinaga. Este tramo tiene una longitud de 2,6 km y discurre en su totalidad en túnel.
Las características principales del tramo son las siguientes:
- Túnel de línea: Con una longitud de 2.260 metros y una sección de 58 m2. La cobertera varía entre 5 y 118 metros.
- Galerías de acceso: Existen dos galerías, OS-1 y OS-10, que suman 505 metros de longitud, con una pendiente longitudinal del 15% y una sección de 58 m2.
- Estaciones: Dos estaciones, la de Otxarkoaga de 98 metros de longitud y cobertera entre 12 y 23 metros, y la de Txurdinaga de 90 metros de longitud y cobertera de 24 metros. Ambas estaciones tienen una sección de 118 m2.
- Cañones: 3 en la estación de Otxarkoaga y 2 en la estación de Txurdinaga.
- Pozos Ø 3,60 m: 12 unidades y una longitud total de 235 metros, excavados mediante Raise Boring.
2. Hormigonado e Impermeabilización de las galerías
Las galerías tienen una pendiente constante del 15% y presentan un radio reducido, con unas longitudes de 225 metros (OS-1) y de 280 metros (OS-10). La sección de revestimiento prevista en proyecto era de 30 cm con hormigón en masa tipo HM-20.
Estas características generan los siguientes problemas de ejecución:
a) Radio de las Galerías
La sección de las galerías es la misma que la del túnel de línea, por lo que estaba previsto emplear el mismo carro de encofrado. Sin embargo, las galerías presentan un radio de 50 metros durante una parte importante del su desarrollo lo que dificulta mucho el empleo único de esta solución, obligando a utilizar encofrados in situ, y condicionando el espesor de hormigón con el uso del carro en gran parte de la sección a revestir.
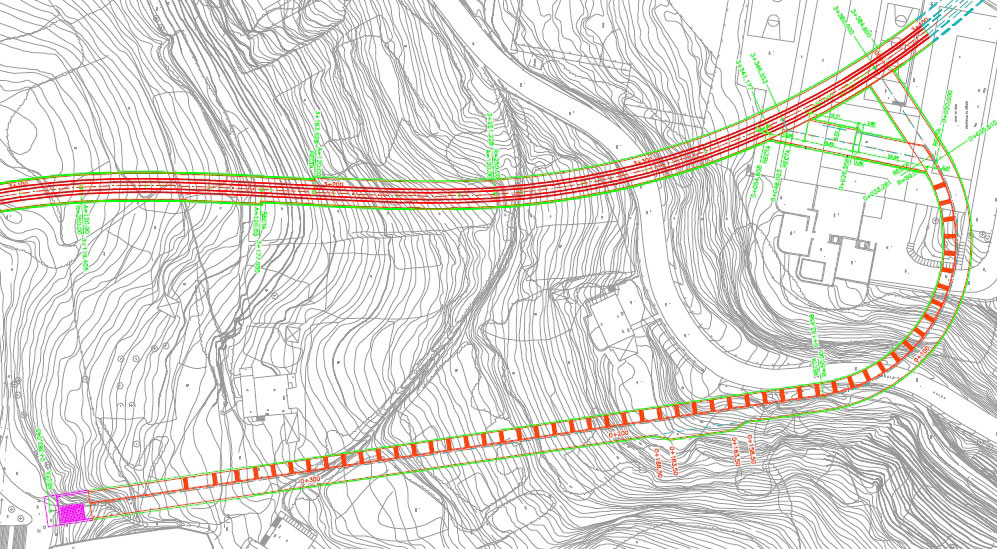
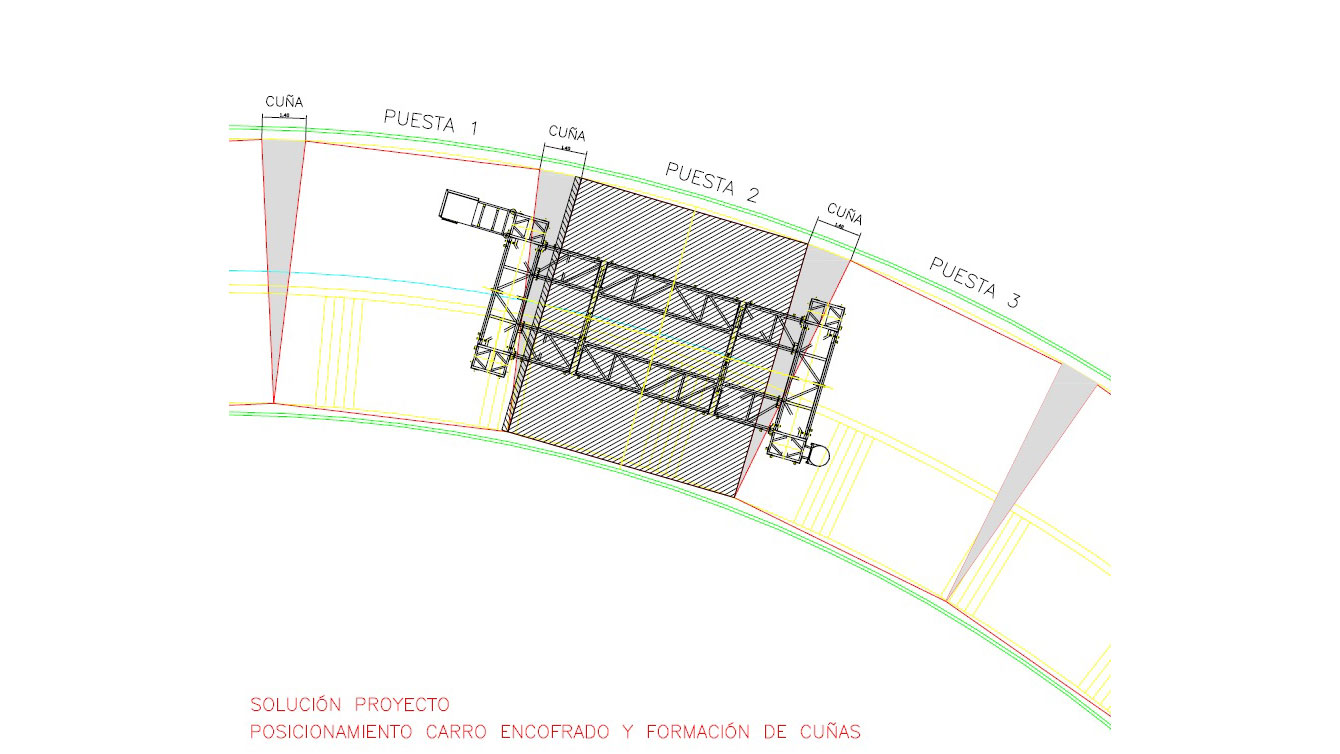
b) Pendiente de la galerías
La pendiente del 15% que tienen las galerías no permite que el carro de revestimiento se desplace por sí solo, tal y como se hace en el túnel de línea, haciendo necesario disponer un elemento de tracción. Esto supondría la colocación de un cabrestante en el interior del túnel para realizar el tiro del carro en las maniobras de desplazamiento.
Debido a la existencia de zonas curvas y al radio de éstas, habría que mover el cabrestante en varias ocasiones a lo largo de los trabajos para poder realizar un correcto tiro del carro de encofrado.
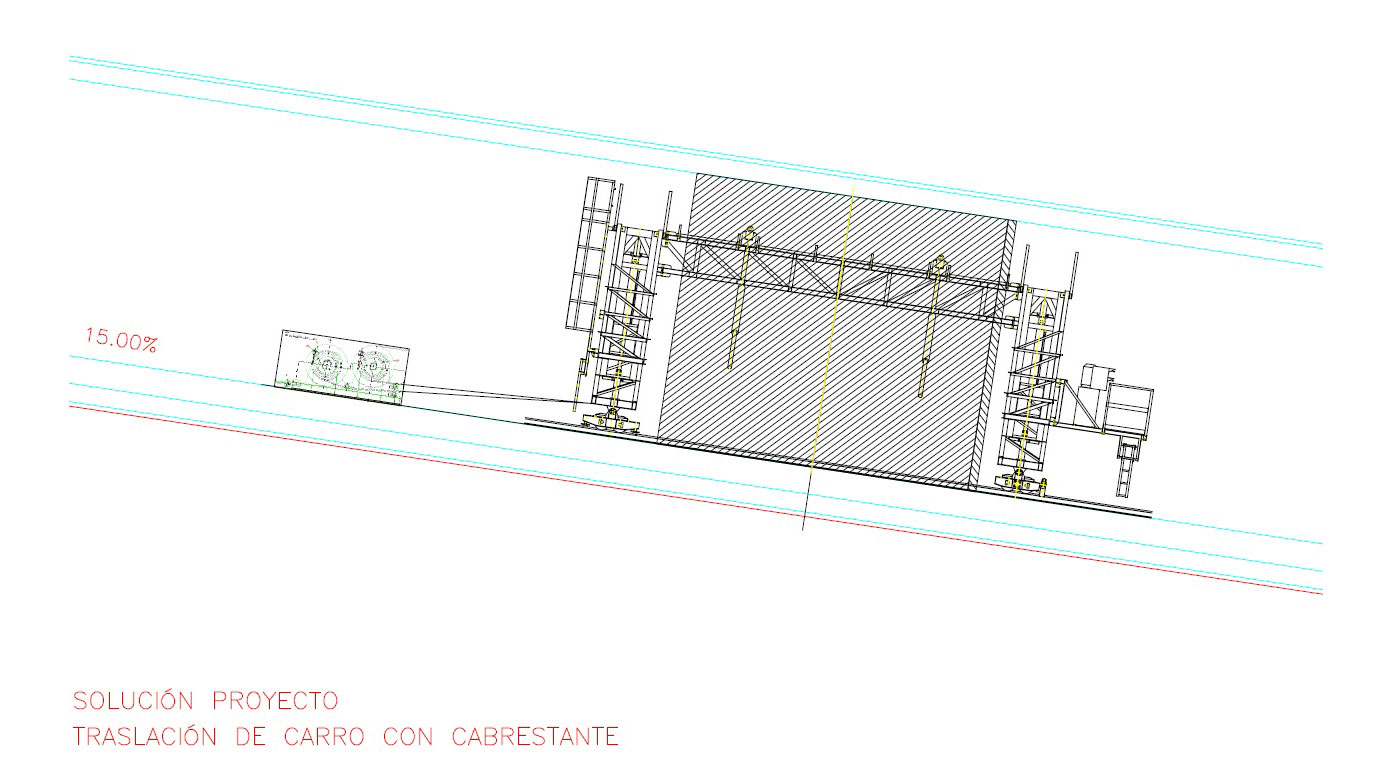
c) Hormigón de Revestimiento
El revestimiento de las galerías está previsto con un hormigón HM-20. Éste es un tipo de hormigón con relaciones A/C elevadas y que necesita tiempos de fraguado elevados, lo que influye negativamente en los plazos de ejecución.
d) Plazo de ejecución
Toda la problemática anteriormente descrita tiene consecuencias en el plazo de ejecución de los trabajos de revestimiento de las galerías, que son tareas críticas dentro la construcción de la obra. Además, los plazos de ejecución de los revestimientos condicionan los trabajos del resto de contratos que se han de ejecutar en la Línea 3, ya que estas galerías constituyen los accesos al tramo.
El radio de las galerías en las zonas curvas obligaría a utilización de encofrados in situ que conllevan más tiempo de ejecución y no permitirían el paso.
La pendiente de las galerías implicaría la utilización de un cabrestante para el traslado del carro de revestimiento, lo que implicaría mucho tiempo para la traslación del carro, a lo que se añadiría el tener que posicionar el cabestrante varias veces debido a los radios de la galería.
Por otro lado, la utilización de HM-20, no permitiría desmoldar al día siguiente de la puesta en obra del hormigón.
Dados los problemas de corte de paso por las galerías que implicaría el revestimiento previsto en proyecto, no se podría ejecutar el mismo en las dos galerías a la vez.
Con todo esto la ejecución del revestimiento de las galerías tendría un plazo estimado de 6 meses, 3 meses aproximadamente para cada una de las galerías.
3. El reto
Con el fin de mejorar el revestimiento de las galerías OS-01 y OS-10 se han analizado diversas alternativas, concluyendo que una solución con un revestimiento impermeabilizado de hormigón proyectado permite conseguir una durabilidad y calidad de acabados satisfactoria y evita la mayor parte de los inconvenientes de la solución de proyecto.
La solución propuesta se denomina ‘Single Shell’ y permite disponer de un revestimiento definitivo aprovechando el hormigón proyectado existente y aplicando sobre el mismo nuevas capas de hormigón proyectado de características mejoradas y de impermeabilización. De esta manera se consigue una solución en la que trabajan conjuntamente todas las capas, sin que la impermeabilización suponga una discontinuidad entre sostenimiento y revestimiento.
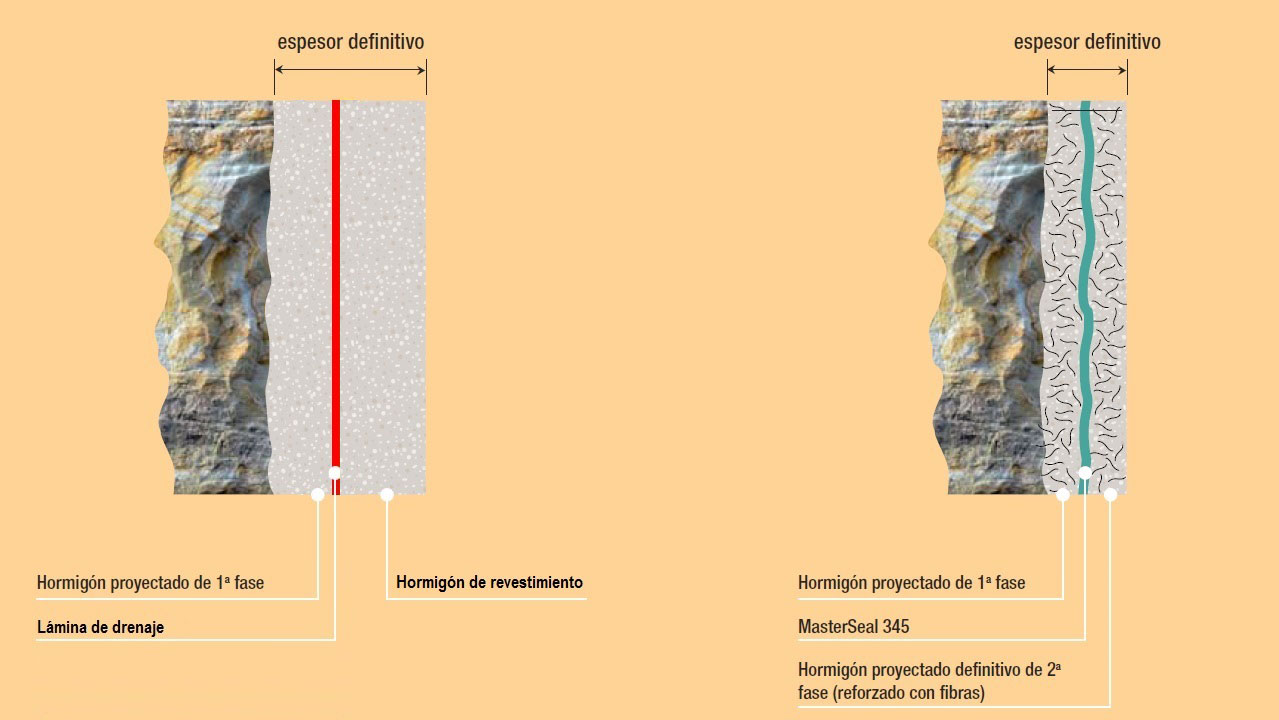
La propuesta consiste en la aplicación de una capa de 10 cm de un hormigón proyectado de altas resistencia y baja permeabilidad, que se aplicaría sobre el sostenimiento existente, previa limpieza con agua a presión del mismo. Posteriormente se colocaría la membrana impermeable proyectable MasterSeal 345 de 3 mm de espesor. Finalmente se protege la impermeabilización con una nueva capa de hormigón proyectado de 5 cm de acabado.
4. Materiales
4.1. Hormigón Proyectado
El hormigón proyectado es de 45 N/mm2, y un espesor de 15 cm. Este espesor se consigue en dos capas, una primera de 10 cm, y una segunda de 5 cm, una vez proyectada la membrana impermeable MasterSeal 345. Además, este hormigón proyectado tendrá una baja permeabilidad.
Los aditivos empleados para este hormigón han sido:
- MasterGlenium UG 1370 SK; superfluidificante para confeccionar un hormigón con R A/C 0,4 máxima.
- MasterX-Seed 130; activador de la hidratación del cemento que potencia las resistencias iniciales y finales del hormigón, así como reductor de la permeabilidad.
- MasterFiber 248; fibra estructural de polipropileno.
- MasterRoc SA 182; acelerante libre de álcalis que mejoran las resistencias finales y aumentan la durabilidad del hormigón.
4.2. MasterSeal 345
Membrana proyectable que queda colocada entre las dos capas de hormigón proyectado, con gran adherencia, que hace que el sistema trabaje como estructura monolítica.
Características principales de MasterSeal 345:
- Alta resistencia a la presión hidráulica hasta 20 bar.
- Alta adherencia al hormigón: 1,2 ± 0,2 MPa.
- Adherencia al acero: 0,65 ± 0,05 MPa.
- Resistencia contra rotura por tracción máxima de 4 MPa.
- Alargamiento a la rotura entre el 80% y el 140% con una temperatura entre -20 °C y +20 °C.
- Ausencia de componentes tóxicos
- Autoextinción en caso de incendio.
- Larga vida útil
5. Aplicación MasterSeal 345
La membrana impermeabilizante proyectable MasterSeal 345 se aplica sobre la capa de hormigón proyectado, que se diseñó con árido seleccionado para que tenga una superficie lo más liso posible consiguiendo una membrana continua y un consumo menor de material.
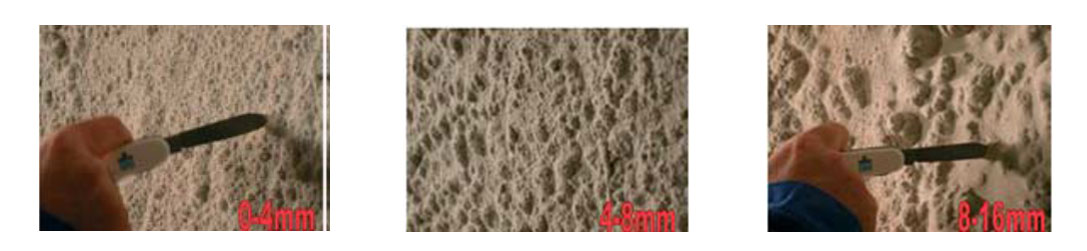
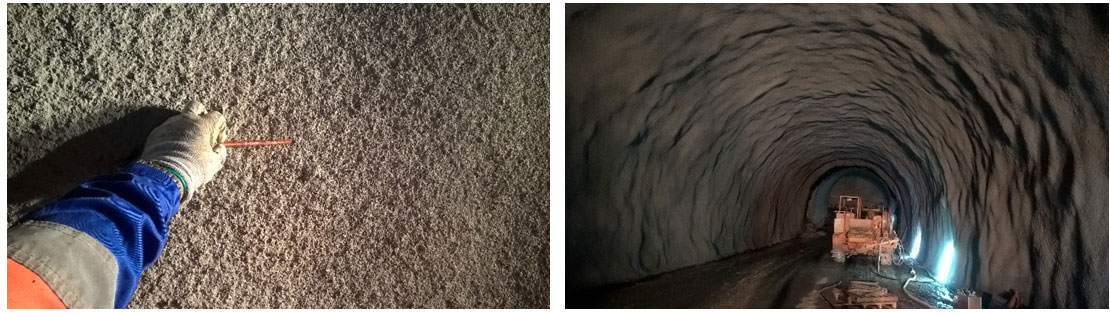
La empresa encargada de la ejecución del ‘Single Shell’ (hormigón proyectado – MasterSeal 345 – hormigón proyectado) ha sido Aragonesa de Hormigones Proyectados, que cuenta con gran experiencia, en la proyección de la membrana, por ejemplo los túneles de Bracons, Catí, Barasona entre otros.
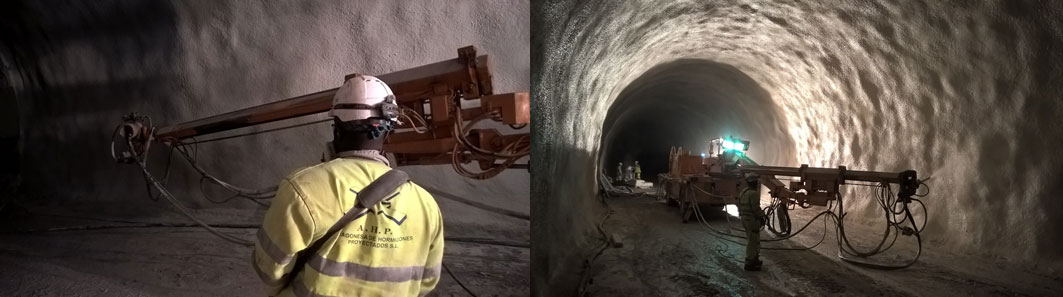
La proyección se ha llevado a cabo con una bomba electroneumática Atlas Copco Meyco Piccola, un robot de hormigón proyectado, del cual solo se ha utilizado el brazo para hacer la aplicación mecánica, y tres trabajadores, el primero manipula el brazo, el segundo controla el flujo de los diferentes elementos que alimentan la Piccola (aire, agua, electricidad) y también se encarga de comprobar los espesores y posibles errores de aplicación, y el tercero se encarga de alimentar la bomba.
El consumo ha estado en torno a los 4 kg/m2, consiguiendo un espesor de 3 – 4 mm. Durante la aplicación ha habido un control constante de la calidad, comprobando en todo momento el espesor, consumo calculado en zona predeterminadas, también se ha comprobado el perfecto curado.
Una vez curada la membrana 3 – 5 días, se ha aplicado la segunda capa de hormigón proyectado, quedando el túnel completamente seco.
6. Conclusiones
La utilización de un revestimiento definitivo de hormigón proyectado, junto la aplicación de membrana impermeable proyectable MasterSeal 345 ‘Single Shell’ aporta unas ventajas a la aplicación frente a los revestimientos e impermeabilización convencionales.
- Aplicación sencilla
- Reducción de los plazos de construcción y de los costes
- Reducción del mantenimiento
- Posibilidad de aplicación totalmente automatizada
- El revestimiento con impermeabilización adherida al hormigón de revestimiento en la primera y segunda capa, da nuevas oportunidades a un diseño óptimo en términos de costes-beneficios
- El comportamiento monolítico del revestimiento reduce significativamente el espesor final del revestimiento
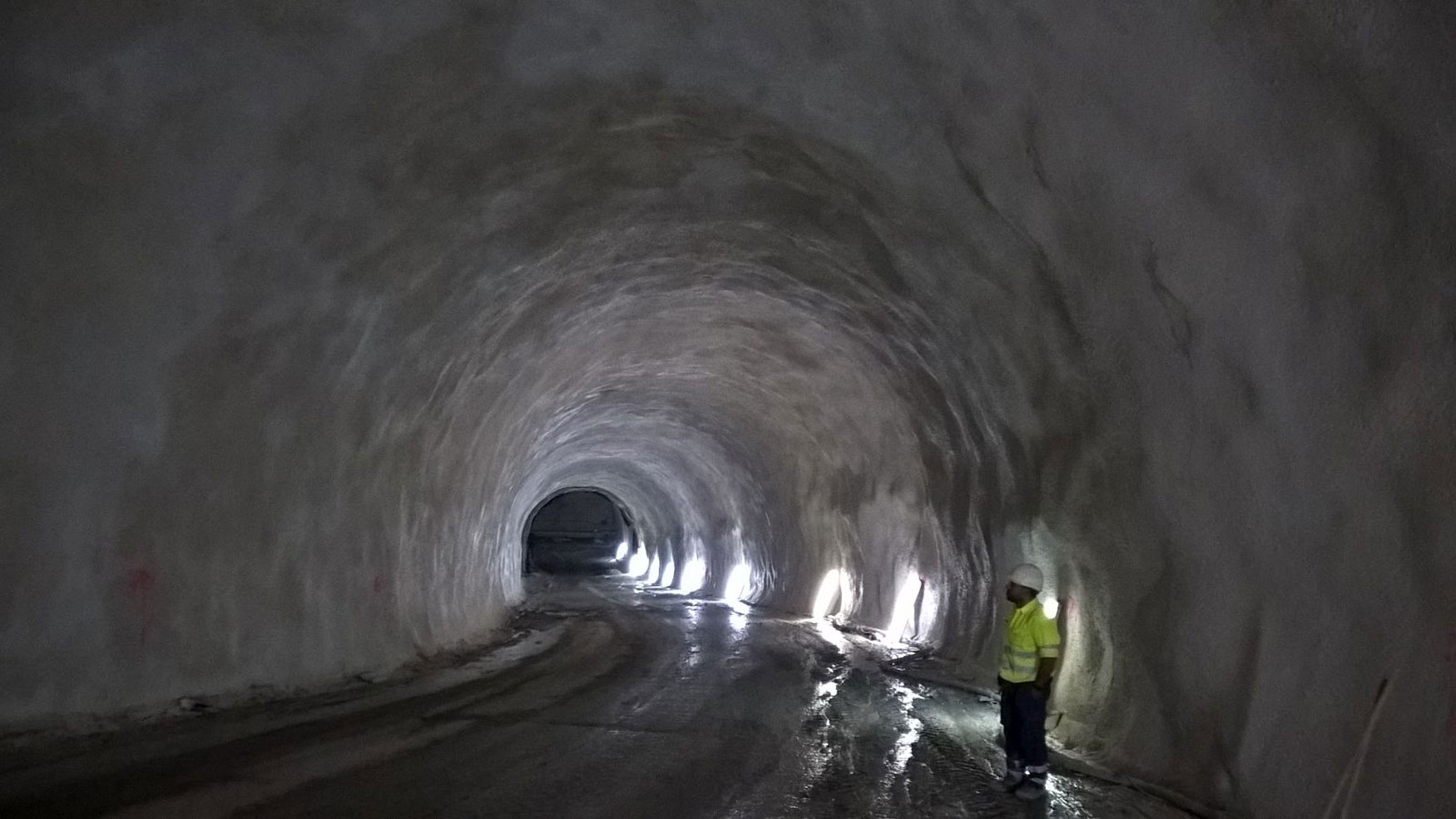
La membrana impermeable proyectada MasterSeal 345 confiere excelentes características impermeables a las estructuras subterráneas, previniendo el desarrollo de pasos de agua en las dos caras de contacto entre el hormigón y la membrana, convirtiéndose en la opción más efectiva, más rápida, más segura y más cómoda que los actuales sistemas de impermeabilización.