La refabricación es posible y así lo demuestra Scania en un proyecto experimental
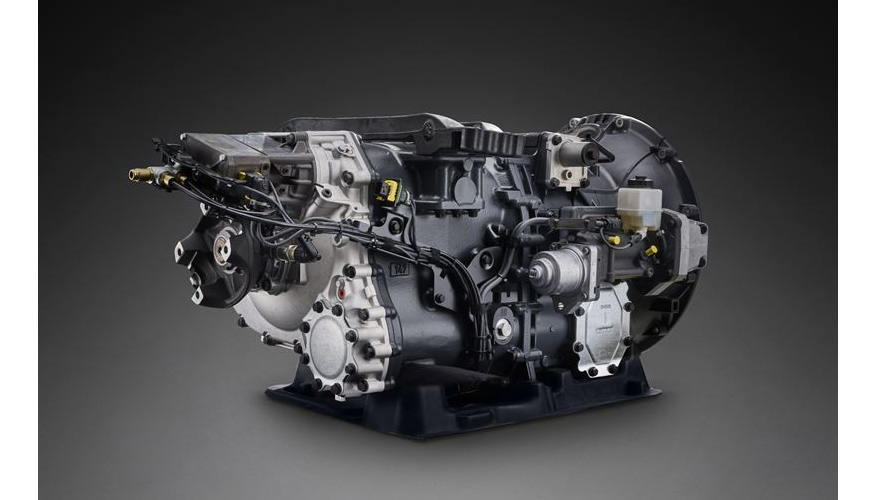
El fabricante sueco Scania reutiliza componentes en su línea de producción y reduce a la mitad el consumo de materiales y emisiones de carbono en un avance pionero en la industria del transporte pesado
Scania, reconocido fabricante de vehículos pesados, ha dado un paso crucial hacia la sostenibilidad al implementar componentes refabricados en su línea principal de producción en Suecia. Este innovador proyecto de “refabricación” de cajas de cambios, denominado Milestone, ha logrado reducir en un 50% el uso de materiales y disminuir en un 45% las emisiones de carbono en comparación con la producción de cajas de cambios completamente nuevas.
Este primer proyecto ha sido lanzado en colaboración con el Real Instituto de Tecnología KTH y Scandinavian Transmission Service AB, y gracias al financiamiento de Vinnova (agencia sueca de innovación).
Scania ha lanzado el primer proyecto de refabricación en la industria del transporte pesado que incorpora piezas reutilizadas en la cadena de montaje de vehículos nuevos. El proyecto iReGear no solo demuestra la viabilidad de esta práctica, sino que también establece una base para avanzar hacia una producción más sostenible y respetuosa con el medio ambiente en la industria.
Pruebas rigurosas de calidad para asegurar el rendimiento
La caja de cambios refabricada ha pasado por el mismo banco de pruebas que las cajas nuevas, evaluándose bajo los más estrictos parámetros de calidad y rendimiento. Scania ha verificado que esta pieza reutilizada cumple con más de 100 indicadores de funcionamiento, lo que permite afirmar que la caja de cambios es “tan buena como una nueva” y cumple con los exigentes estándares de la marca sueca.
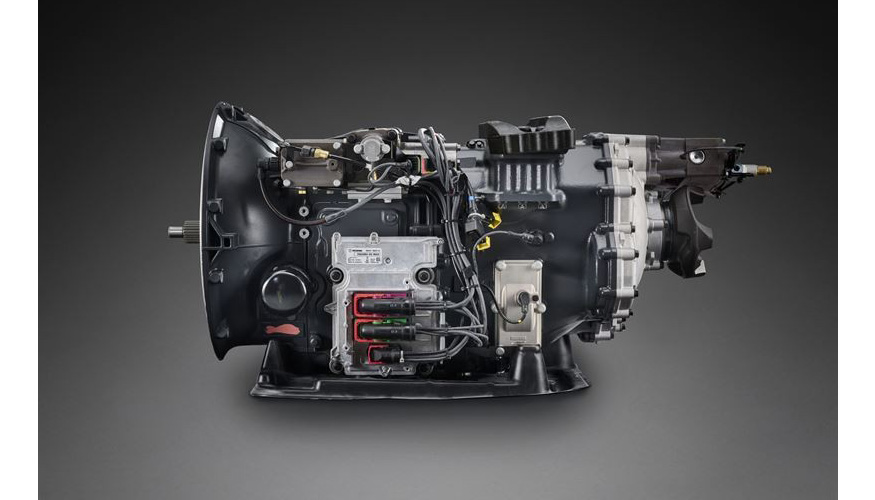
Sostenibilidad y eficiencia: menos consumo de materiales y menores emisiones
La refabricación, al reutilizar componentes en lugar de emplear materiales nuevos, reduce el consumo de recursos y minimiza la huella de carbono. El índice de sustitución de piezas durante el proceso de refabricación puede variar entre un 10% y un 100%, dependiendo del nivel de desgaste, pero incluso en los casos más complejos, se ha logrado una reducción significativa de materiales y emisiones en este proyecto.
Hacia un modelo de fabricación circular en la industria del transporte
La integración de componentes reutilizados directamente en la producción de vehículos nuevos representa un cambio de paradigma en la industria del automóvil. La mayoría de las piezas refabricadas en Europa se destinan a recambios posventa, limitando su impacto ambiental. El proyecto iReGear, sin embargo, busca transformar este enfoque, incorporando la refabricación en la línea de montaje y abriendo nuevas posibilidades para un modelo de economía circular en el sector de los camiones y vehículos pesados.
Fredrik Nilzén, director de Sostenibilidad de Scania, afirma: “Este proyecto marca un hito en la sostenibilidad y eficiencia de nuestra producción, manteniendo los más altos estándares de calidad y contribuyendo a la transición hacia un modelo de economía circular.”
El éxito de esta iniciativa experimental no solo subraya el compromiso de Scania con el medio ambiente, sino que también marca el inicio de una transformación en el sector de transporte pesado hacia una fabricación más sostenible, abordando simultáneamente los problemas de escasez de recursos y las necesidades de reducción de emisiones.