La producción de la primera serie con el método Dolphin ha comenzado
02/01/2012
2 de enero de 2011
Más confort, esa es la tendencia en el diseño de interiores de vehículos, incluyendo los camiones. Las piezas inyectadas con superficies de tacto suave que pueden producirse en una única fase del proceso aplicando el método Dolphin, han contribuido a promover esta tendencia. La aplicación de la primera serie comenzó en otoño, el proveedor Daimler SOLE produce piezas de interior para el nuevo Mercedes- Benz Actros utilizando Dolphin.
La línea de producción, que opera la firma italiana SOLE S.p.A en las instalaciones de Daimler en Wörth (Alemania) se compone de una máquina de inyección Engel duo, representada en España por Helmut Roegele, con un sistema de mesa horizontal rotatoria intermedia, un robot industrial de múltiples ejes y equipamiento para espumado físico. Primero, se inyecta el material y se espuma con elastómero termoplástico en un solo ciclo. Eso es lo que el método Dolphin representa como una economía alternativa para la producción de componentes hard/soft en comparación a otros métodos convencionales multicomponente o de espumación.
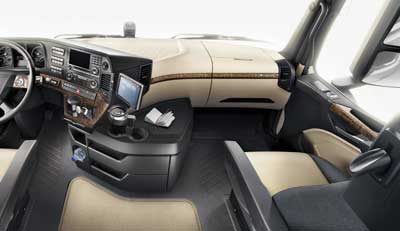
Más confort en la cabina del conductor: el nuevo Mercedes- Benz Actros contiene piezas con superficies suaves al tacto, hechas con el método Dolphin. (Fotografía: Daimler).
El método de fabricación integrado ha sido desarrollado por Engel Austria en cooperación con el fabricante de moldes suizo Georg Kaufmann así como con el fabricante de plástico BASF y el Grupo P, ambos alemanes. Aunque se presentó en la Feria K 2007 junto con el proveedor de automóviles alemán Johnson Controls, el método ha experimentado un mayor desarrollo en los últimos años gracias a SOLE y ha sido optimizado para la producción en masa. Además de Engel, Georg Kaufmann y P-Grup participan en el Proyecto de Actros.
“El comienzo de la producción ha comenzado como estaba planeado”, afirmó Michael Fischer, responsable de ventas para tecnologías en Engel: “El potencial del método Dolphin es enorme debido al ato nivel de integración de proceso así como a la alta calidad relacionada con la superficie de los componentes. Las negociaciones con clientes para comenzar aplicaciones en serie se encuentran actualmente en proceso”.
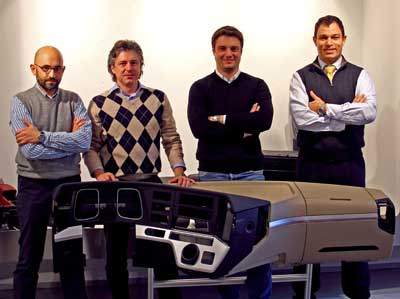
Andrea Bicego (derecha), responsable de investigación y desarrollo en Sole con su equipo: Andrea Bellantoni, Stefano Fingolo y Luca Piovesan (de izquierda a derecha). (Fotografía: SOLE)
Empresas o entidades relacionadas
Roegele, S.A.