El soplado de cuerpos busca su hueco en la rentabilidad
11 de junio de 2010
El soplado de cuerpos huecos está muy ligado a la fabricación de envases, de botellas. Y las botellas, indiscutiblemente, muy ligadas al PET, el material más utilizado en el envasado de bebidas y alimentos líquidos. Se estima que en 2009 se utilizaron en el mundo 400.000 millones de botellas de PET, que representaron en torno a un tercio de todos los envases utilizados para envasar bebidas. Se sigue investigando en torno a otros materiales, de la misma forma que hace años surgieron algunos que parecían presentarse como competidores de este material. Sin embargo, nadie ha logrado destronarlo.
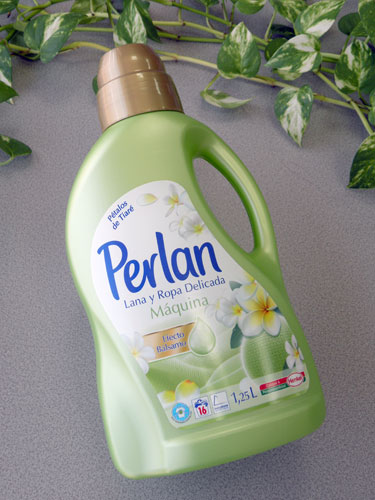
Pero en este artículo no pretendemos tratar la fabricación de botellas, sino, en general, el soplado de cuerpos huecos, una expresión en cierto modo redundante, porque siempre que se sopla, se obtiene un cuerpo hueco. El moldeo por soplado es responsable de una parte sustancial de la producción total de plásticos. Aparte de la técnica del moldeo rotacional, muy específica para determinadas aplicaciones y minoritaria en términos de volumen de mercado, para el moldeo de envases y otros productos similares, se recurre al proceso de extrusión-soplado o al de inyección-soplado.
En el primero de ellos, el de extrusión-soplado, se extruye un elemento tubular, (parison) que inmediatamente, en un mismo equipo, se introduce en el molde de soplado donde, mediante el soplado, adquiere la forma deseada. Esta técnica permite un buen aprovechamiento de las posibilidades multicapa. Las extrusoras suelen contar con acumuladores de extrusión para producir el parison de un modo mucho más rápido que el que permitiría el propio flujo del cabezal de extrusión, evitando que se descuelgue antes de quedar fijada por el pinzamiento del molde. Mediante extrusión-soplado se obtienen envases muy diversos y son habituales aplicaciones del sector de detergentes, productos de limpieza, productos cosméticos, champús, etc., pero también depósitos de combustible, artículos de juguetería y otros productos.
También se puede utilizar la extrusión-soplado en procesos más complejos en los que un robot posiciona el parison dentro de formas complejas y con cambio de dirección del molde abierto. Es un sistema al que se recurre, por ejemplo, para realizar tubos y conductos diversos destinados al automóvil, más en concreto para sus sistemas de climatización o conductos de admisión. Algunas empresas, como Uniloy utiliza una tecnología de succión para colocar el parison en la forma del molde.
Primero la preforma, luego la botella
La inyección-estirado-soplado nació para dar una respuesta objetiva a la obtención de envases para bebidas carbónicas en materiales transparentes. Por sus características mecánicas, el poliéster termoplástico es el material más adecuado, pero al tratarse de un polímero cristalino era preciso un proceso con una gran rapidez de transformación y enfriamiento que permitiera evitar la formación de cristalitas durante el paso a la fase sólida.
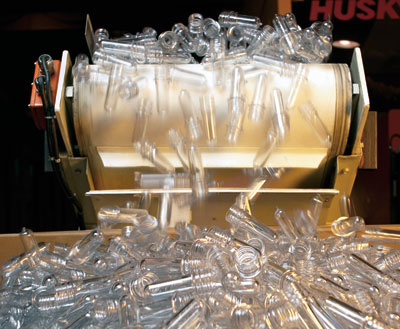
En este proceso, el primer paso es la inyección de una preforma que, en una segunda fase, es estirada de forma controlada, introducida en un molde de soplado y “soplada” para que el contacto con las paredes frías del molde endurezca el envase de modo casi instantáneo. El uso de PET exige un secado previo de la granza, puesto que cualquier traza de humedad invalida el proceso.
Existen máquinas en el mercado que realizan el proceso de la inyección de la preforma, su estirado y posterior soplado en el molde en un único proceso. Es el caso, por poner un ejemplo, de las máquinas de la japonesa Nissei ASB.
Pero también se pueden separar esas fases, es decir, inyectar las preformas en una inyectora para posteriormente realizar el proceso de soplado en una sopladora. Los fabricantes de máquinas para el moldeo por inyección que cuentan con una especialidad en la inyección de preformas ofrecen sistemas con moldes multicavidad que permiten la fabricación masiva de preformas.
Una de estas empresas es Husky Injection Molding Systems, por ejemplo, que presentó en la pasada edición de la feria Drinktec (septiembre 2009) el sistema HyPET que aumenta la cantidad de contenido reciclado en los envases para bebidas. Fue una novedad muy relevante, precisamente por ser el primer sistema del mundo optimizado para la fabricación de preformas con altos porcentajes de PET reciclado para uso alimentario. El sistema que mostró en la citada feria fue el HyPET RF (reciclado en escamas) 300, de 72 cavidades, con paquete de altas prestaciones (HPP), que utiliza una mezcla al 50% de resina virgen y 50% de PET reciclado, en escamas, de post-consumo.
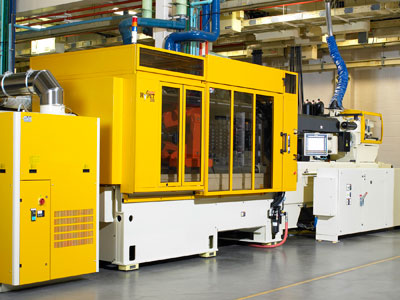
El sistema fabrica una preforma EcoBase de 34,7 gramos con el mismo ciclo de 10,5 segundos que se produciría al utilizar PET virgen 100%. Este diseño de preforma EcoBase se presentó por primera vez en la NPE 2009. Entre las mejoras del sistema se encuentran la filtración de material fundido en línea para eliminar las manchas negras que puedan afectar a la calidad de la botella, así como un nuevo diseño de extrusora para conseguir un procesamiento mejorado de las mezclas de granza y escamas. Estas características permitirán que los fabricantes que actualmente no utilizan PET reciclado en escamas introduzcan este material en sus productos. Para aquellos que ya utilizan PET reciclado en escamas, esta nueva opción puede eliminar algunos de los retos actuales de fabricación y calidad con los que se pueden encontrar, a la vez que permite aumentar el contenido de escamas. Para mostrar la calidad de la botella, las preformas se soplaron en una máquina de Sidel.
Otro especialista en la fabricación de sistemas para la inyección de preformas de PET es Netstal que ofrece para este mercado su sistema PET-Line, con fuerzas de cierre de 200, 350, y 600 toneladas y moldes de 24 a 192 cavidades. En 2007 presentó su línea de 200 toneladas de fuerza de cierre para la gama de pocas cavidades, con moldes de 24 a 48 cavidades. Junto con la suiza Otto Hofstetter AG Netstal ofrece también el sistema en moldes de 60 cavidades, sobre la misma plataforma, lo cual se considera un éxito porque hasta ahora estos moldes necesitaban máquinas de 350 toneladas. En la pasada edición de la feria Drinktec presentó una máquina para preformas de 0,5 litros y 18,15 gramos, en ciclos de 8,8 segundos. El resultado era una producción de más de 24.500 piezas por hora. De esta forma Netstal quiso mostrar que unos ciclos más cortos no necesariamente significan un mayor consumo de energía, ni una mayor necesidad de espacio para la máquina.
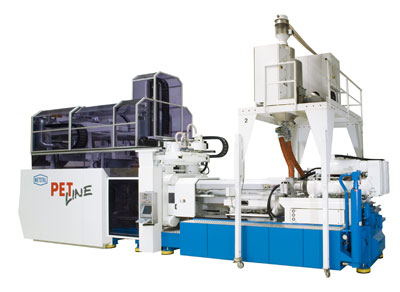
Para acelerar el ciclo Netstal incorpora a sus máquinas la tecnología Calitec, con la cual se somete a una pequeña presión de aire al interior de la preforma durante la fase de enfriamiento. De esta forma, por un lado se presiona la preforma todavía caliente contra las paredes del molde y se evita la retracción y, por otro, se reduce el tiempo de post-enfriamiento. Actualmente, la tecnología Calitec se está utilizando también con éxito en líneas PET-Line con 192 cavidades.