Una campana extractora que además adorna
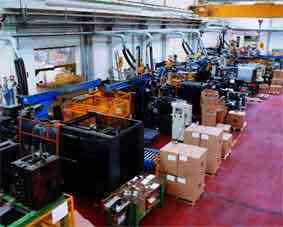
Todos los componentes se fabrican en dos fábricas, localizadas en Mergo y en Serra San Quirico. En la primera de ellas se encuentra el taller de inyección de plásticos, donde se producen las diferentes piezas de esos materiales.
Fue sólo a partir de 1997, después de años externalizando el moldeo por inyección a otras empresas, cuando Elica decidió construir su propio taller de inyección y equiparlo con tres inyectoras Sandretto de la serie Otto, con 85, 200 y 400 t de fuerza de cierre. Claro que eso fue sólo el principio, porque luego se adquirieron trece máquinas más: siete de la serie Otto con fuerzas de cierre de 85 a 400 t y seis de la nueva serie Nove T, la mitad de ellas con 165 t de fuerza de cierre, dos con 300 t y la otra con 400 t.
La mayoría de las piezas inyectadas (ventiladores de aspiración, transportadores, soportes para motor, bridas, cubiertas, etc.) están hechas de polipropileno. Más en concreto, dos de las inyectoras de la serie Nove T se utilizan para fabricar en policarbonato las piezas de la parte superior de la zona de iluminación de la campana.
La empresa, que trabaja en tres turnos diarios, produce 110.000 piezas diarias con un total de unos 300 modelos diferentes. Estos modelos se montan en las 12.000 campanas que se realizan a diario.
El ciclo operativo es totalmente automático: desde la alimentación del material mediante un sistema neumático, hasta la incorporación de insertos en el molde y la descarga de las piezas mediante manipuladores.
El funcionamiento consolidado de las primeras máquinas de la serie Otto facilitó en buena medida la instalación de las nuevas máquinas de la serie Nove T que, ya en la fase de proyecto, se probaron con Elica.
En este sentido, Vincenzo Tortolini, Director de Planta de la fábrica de Mergo, señala que "el desarrollo de esta línea nos permitió apreciar las características de la máquina frente a las de la serie anterior. Su elevada precisión nos asegura un moldeo de alta tecnología, sobre todo en las piezas -como las ruedas del ventilador- que no pueden alejarse en ningún caso de las especificaciones. Si estas exigencias no se cumplieran, las piezas producidas no obtendrían la conformidad. Su excentricidad y planitud deben ser constantes. Si no fuera así, no se podría responder a los requerimientos necesarios en lo relativo al nivel de ruido y capacidad de aspiración".
La fiabilidad de todas las inyectoras Sandretto instaladas, que operan sin parar 24 horas al día, combinada con un servicio técnico puntual y de calidad, ha contribuido al prestigio de esta marca dentro de este transformador de plásticos italiano que cuenta con la certificación ISO 9001 y UNI EN ISO 14001.
Y la cosa puede ir a más, ya que el pasado mes de octubre Elica abrió una planta en Brasil, lo que se puede considerar como una nueva oportunidad para Sandretto. La capacidad de la planta brasileña, por el momento, es de 200.000 piezas diarias y está preparada para responder al 30% de la demanda del mercado de ese país.