Los gemelos digitales como herramienta clave para mejorar la productividad del tejido industrial
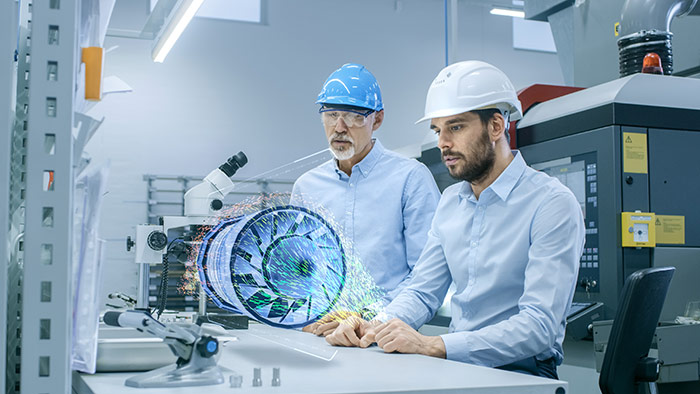
Comprobar si un producto o proceso cumple con las especificaciones ideadas en su diseño antes de hacer un prototipo real; monitorizar posibles fallos en piezas gracias a muchas más simulaciones de las que podríamos obtener en un entorno tradicional; detectar ineficiencias o áreas de mejora en los procesos de fabricación; probar distintos modelos de producción sin tener que implantarlos en la operativa diaria; o revolucionar los sistemas de mantenimiento, en los que se pasará de un modelo preventivo a uno predictivo son solo algunas de las ventajas que generará la aplicación de los gemelos digitales al ámbito industrial.
Una tecnología disruptiva, cuya progresiva implantación en todos los sectores productivos supondrá un estímulo para el desarrollo de la industria 4.0. En palabras de Álvaro Rodríguez, director de Desarrollo de Negocio de CTC, serán “una herramienta clave para mejorar la productividad del tejido industrial a medio plazo”.
La jornada “Gemelos Digitales: Aplicaciones industriales y oportunidades de negocio” ha constatado el interés general de las empresas en torno a esta tecnología. Con más de 70 participantes, este evento telemático, organizado conjuntamente por el Centro Tecnológico CTC y CEOE-Cepyme Cantabria, ha presentado algunas de las claves que marcarán el desarrollo de los gemelos digitales a medio plazo, así como varios casos de éxito relacionados con proyectos de I+D+i en los que ya se ha implementado esta tecnología.La irrupción de esta tecnología permitirá a las empresas de cualquier ámbito anticiparse al futuro. Implementar soluciones innovadoras fundamentadas en gemelos digitales supone minimizar los riesgos, reducir los tiempos de inactividad y optimizar los costes. “Paras las pymes, que son mayoría en nuestro entorno, estas tecnologías asumibles suponen ganar competitividad” explicó Enrique Conde. “Una de nuestras apuestas estratégicas pasa por incrementar el PIB industrial de Cantabria y disponemos de sectores claramente receptores de esta tecnología como la automoción, energías renovables y nucleares” concluyó el presidente de CEOE-Cepyme Cantabria.
Astander tiene en marcha dos proyectos basados en esta tecnología: Smartdoor, a través del que monitorizan la salud estructural de la compuerta de uno de sus diques, y el Escaneo en tiempo real
Como referente nacional en el desarrollo y transferencia de conocimiento a la industria sobre gemelos digitales de estructuras y componentes mecánicos, los ponentes del Centro Tecnológico CTC concentraron sus intervenciones en explicar de manera didáctica qué son los gemelos digitales y cómo se trabajan desde el Centro para generar ventajas competitivas a las empresas. “Esta tecnología se puede aplicar en cualquier parte de los procesos” explicó Álvaro Rodríguez. “Su implantación nos permitirá responder de forma anticipada y rápida a cuestiones críticas para optimizar la producción y garantizar la sostenibilidad”.
En ese sentido, Aratz García, project manager en el Centro Tecnológico CTC, explicó cómo están aplicando la Inteligencia Artificial y el análisis de datos para reducir el volumen de datos requeridos y así poder operar en tiempo real. “Aplicamos un modelo de orden reducido en el que controlamos los puntos críticos de cada proceso. Así, pasamos de billones de datos a manejar miles de datos” indicó García. “Esta circunstancia reduce notablemente el coste computacional y nos habilita para trabajar en tiempo real” continuó. Este investigador, que desarrolla modelos numéricos para aplicar en el ámbito de los gemelos digitales, incidió también en la importancia que tiene el histórico de datos para generar modelos capaces de “aprender” de sus propios errores.
Múltiples aplicaciones industriales
Además de conocer proyectos como MooringSense, una investigación de carácter europeo liderada por CTC en la que se aplican gemelos digitales para reducir hasta un 15 % el coste de mantenimiento de los aerogeneradores offshore e incrementar entre un 2 y un 3 % su rendimiento, o Predicarg, en el que CTC está trabajando con un sistema de predicción de cargas para los sistemas de fondeo, los asistentes a la jornada tomaron contacto con algunos casos de éxito relacionados con la aplicación de esta tecnología a diferentes sectores.
Para Astander, los “gemelos digitales son fundamentales para ahorrar costes, reducir los tiempos de trabajo y facilitar la toma de decisiones”. Laura Herrera, responsable de Desarrollo de Investigación y Proyectos de la compañía, explicó que disponer de un entorno virtual seguro les permite “prever los posibles riesgos laborales que se producen en nuestro sector”. Actualmente, Astander tiene en marcha dos proyectos basados en esta tecnología: Smartdoor, a través del que monitorizan la salud estructural de la compuerta de uno de sus diques, y el Escaneo en tiempo real, que les permitirá en el futuro disponer de una oficina técnica virtual para reducir los plazos evitar desplazamientos y ahorrar costes.
La intervención de Luis Fernández, Managing director de VBE6D, puso de manifiesto la idoneidad de los gemelos digitales tanto en los entornos fabriles como otros sectores ajenos al ámbito industrial. No en vano, su compañía brinda servicios de digitalización eficiente en la gestión de proyectos tanto a promotores inmobiliarios como a compañías de arquitectura, ingeniería y construcción (AEC), así como a fabricantes de bienes de equipo. “Nosotros trabajamos con un concepto que puede considerarse construcción industrializada” explicó. “Gracias a la tecnología BIM (Business Intelligence Model) podemos modelar desde un planta completa hasta las piezas que salen de cualquier planta”. Un concepto de “construcción 4.0” que “ya cuenta con algún caso de éxito en Cantabria”.
Por último, Viesgo aportó una funcionalidad complementaria y diferente a las expuestas por parte del resto de ponentes. José Ángel Padilla, responsable de Subestaciones Eléctricas de Cantabria y Castilla y León, desgranó en qué consiste su programa “Virtual Training”: una herramienta formativa que se sirve de los gemelos digitales para reproducir las mismas condiciones a las que deberán enfrentarse los operarios cuando trabajen en las subestaciones. “El programa nos permite trabajar con entorno idénticos a los reales de una forma segura, sin ningún tipo de exposición al riesgo y de forma completamente deslocalizada”.