Aumentar la vida útil de las herramientas con un servicio de pre y postratamiento especialmente adaptado
Hoy en día, la presión en costes que sufren los fabricantes de automóviles al fabricar engranajes y componentes de transmisión es decididamente alta. Esta presión sobre los costes muchas veces se compensa estirando al máximo la vida útil de las herramientas, lo que puede generar paradas de máquina indeseadas y caras pérdidas de producción. Con ‘primeGear’, Oerlikon Balzers lanza un completo servicio basado en consultoría integral y un detallado análisis de procesos que ayuda a los fabricantes a conseguir ahorros de hasta el 40% en los costes de producción. Procesos de pre y postratamiento especialmente adaptados a la aplicación y procesos de corte del cliente logran aumentar la vida útil de las herramientas y permiten planificar de forma anticipada y precisa los procesos de producción.
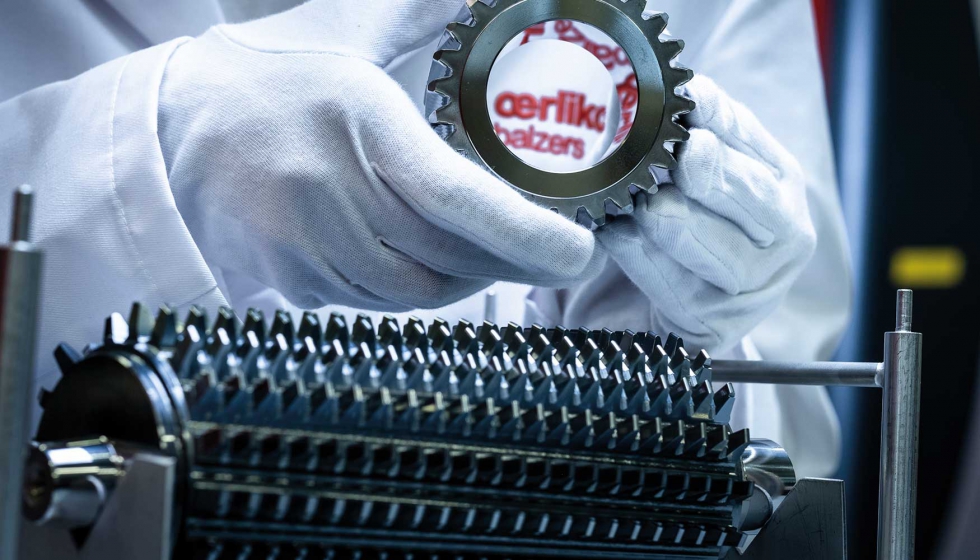
Es sabido que la vida útil de una herramienta se puede extender de manera considerable gracias a los procesos de pre y post tratamiento sobre los recubrimientos originales o decapando y volviendo a aplicar un recubrimiento. ¿Pero son esas las únicas maneras en las que una empresa puede aumentar su productividad y ahorrar en costes? Un área de incertidumbre que es difícil de despejar es la excesiva variación de la vida útil de una herramienta durante su tiempo de servicio, especialmente en la fabricación de engranajes. Más que nunca antes, la industria del automóvil sufre una gran presión sobre sus costes, lo que a menudo significa que los fabricantes estiran el uso de sus herramientas de corte al límite de su rendimiento. La fatiga a bajos ciclos y las micro roturas tienen como consecuencia la baja calidad del componente fabricado, lo que es un problema serio en la industria de automoción. Se demanda máxima productividad en un mercado cada vez más competitivo y las paradas de máquina no programadas pueden resultar muy caras para los fabricantes. ¿Hay alguna manera de resolver este dilema?
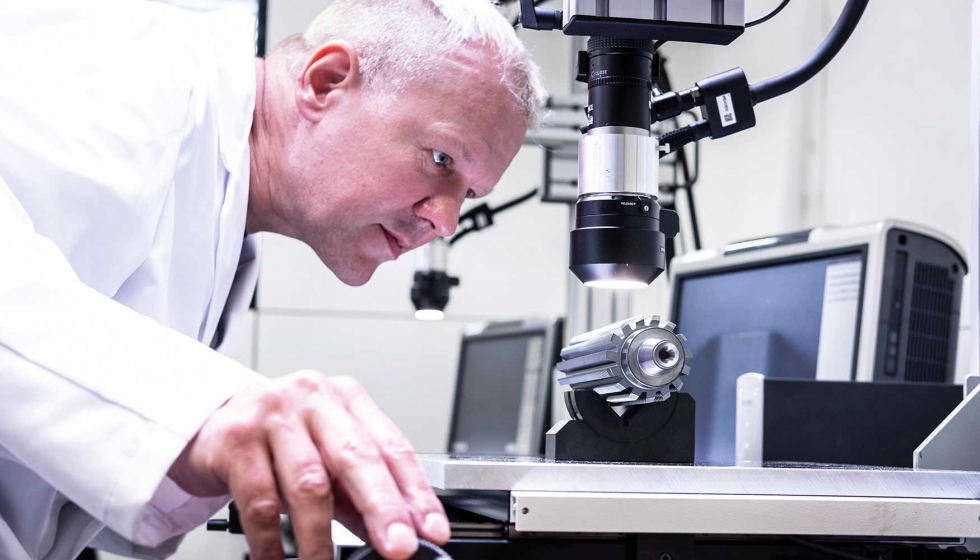
Inmenso potencial para maximizar el ahorro en los costes de producción
Oerlikon Balzers, proveedor especializado en tecnologías de superficie, cuenta con un profundo conocimiento y una gran experiencia que ha acumulado gracias a su cercana colaboración con sus clientes desde su creación hace ya más de 70 años. La compañía sabe cómo optimizar los procesos para que sus clientes sean más competitivos y logren mayores éxitos. La nueva solución que ha desarrollado para estabilizar el proceso de producción mientras reduce el desgaste de las herramientas se llama ‘primeGear’, un paquete de servicios totalmente integrado que optimiza el proceso de producción por medio de una intensa consultoría, un detallado análisis de la situación y la consecuente provisión de pre y postratamiento personalizado. Como parte integral del paquete de servicios, Oerlikon Balzers inspecciona cada una de las herramientas para verificar la calidad de las superficies afiladas y detectar daños que puedan haberse causado por una incorrecta manipulación o un afilado defectuoso. Los resultados de esta optimización de procesos son asombrosos: una vida útil más larga convierte el proceso de producción general en mucho más predecible, logrando ahorros de hasta el 40% en los costes de fabricación, además de asegurar una mejor calidad de la pieza fabricada.
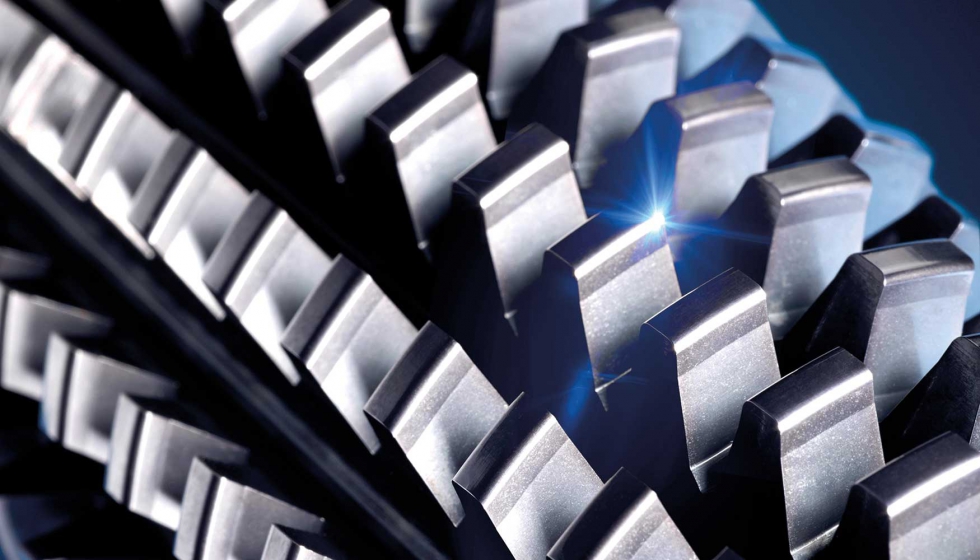
Servicio de consultoría profesional y profundo análisis del estado actual
El examen en profundidad del proceso de producción al completo suele revelar asuntos potencialmente críticos que pueden eliminarse en una primera etapa. Siguiendo un enfoque de “paso a paso”, expertos con experiencia de Oerlikon Balzers llevan a cabo un análisis de hasta el más mínimo detalle con sus clientes. ¿Cómo se manipulan las herramientas y cómo se mantienen las máquinas?, ¿cuál es la temperatura ambiente y está el entorno de trabajo lo suficientemente limpio?, ¿qué tal es la calidad del material a procesar?, ¿qué refrigerante se utiliza?, ¿son las velocidades de corte y avance los correctos?, ¿se preparan las geometrías de la herramienta y las superficies de corte de forma adecuada?
Con un enfoque iterativo, Oerlikon Balzers analiza a sus clientes y desarrolla con ellos la mejor solución posible personalizada a sus necesidades que consigue los mayores ahorros por pieza fabricada. El análisis del desgaste, en concreto, muestra hasta qué punto se ha estresado a una herramienta en el proceso de fabricación y cómo se puede maximizar su rendimiento. El objetivo es lograr un desgaste abrasivo y/o adhesivo consistente que nos permita predecir y planificar la duración del proceso de fabricación. Un desgaste consistente maximiza la vida útil de la herramienta y minimiza los tiempos de ciclo, ayudando a reducir los costes totales a niveles sostenibles.
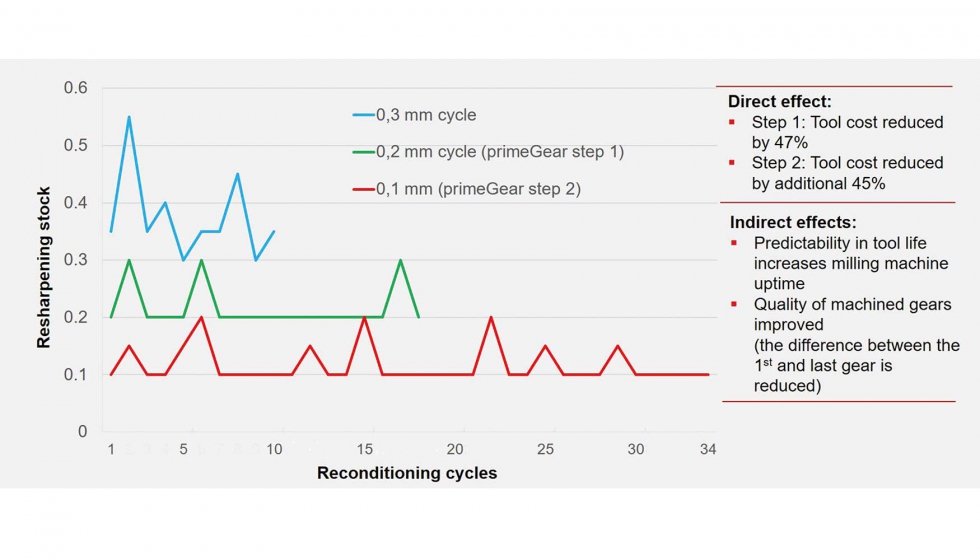
La preparación personalizada de la herramienta es clave para lograr mayores ahorros
Este enfoque basado en asesoría lo desarrolló inicialmente Primateria, una empresa sueca que Oerlikon Balzers adquirió en octubre del 2017. Desde entonces, Oerlikon Balzers ha expandido y mejorado su rango de servicios y tratamientos de superficie con tecnologías para el pre y post tratamiento. En el proceso de análisis, los expertos en tribología de Uppsala, Suecia, se concentran en la herramienta en sí, ya que funciona para ellos como un sensor que identifica los puntos débiles a lo largo de todo el sistema. “Gracias a su enfoque integral, un fabricante de camiones escandinavo ya ha logrado impresionantes ahorros utilizando ‘primeGear’ en su producción de engranajes en los últimos años”, dice Mats Larsson, jefe del Centro de Competencia en Tribología.
Una vez completado el análisis, se personaliza la preparación de la herramienta para sentar las bases de un proceso de fabricación eficiente. Los ensayos han demostrado que el periodo de rodaje (run-in) tiene un efecto crucial en la vida de la herramienta y el posterior proceso de producción, y un exhaustivo pre-tratamiento de la herramienta antes de su recubrimiento elimina las microrroturas y los problemas durante este periodo de rodaje. Las herramientas de metal duro y HSS necesitan aristas de corte optimizadas para brindar el mejor rendimiento, y éstas pueden modificarse para satisfacer las necesidades exactas del proceso de fabricación, el material de trabajo y los parámetros de corte del cliente.
Además de elegir los parámetros de corte adecuados, aplicar el recubrimiento perfecto es otro factor indispensable para conseguir un proceso de producción exitoso. Oerlikon Balzers siempre ha mantenido una estrecha colaboración con sus clientes y les asesora en la selección del recubrimiento idóneo, dependiendo de la aplicación, las herramientas que se utilicen y el proceso de mecanizado. Los innovadores recubrimientos como el Balinit Alcrona PRO y el Balinit Altensa representan la máxima productividad y son una parte esencial del paquete de servicios ‘primeGear’. El paso final es el postratamiento, en el que se eliminan las gotitas (droplets) para lograr la superficie de recubrimiento menos rugosa posible, asegurando una baja fricción y un funcionamiento suave, además de prevenir fallos por fatiga y aumentar la resistencia al desgaste.
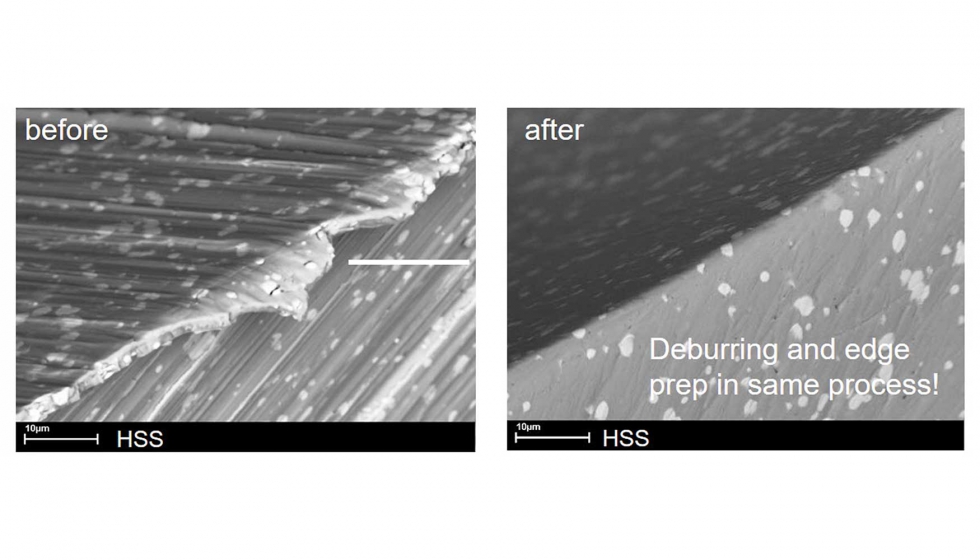
Resumen y conclusión
Varios proyectos con clientes y estudios han probado que el análisis en detalle y el tratamiento personalizado de las herramientas ayudan a minimizar las variaciones de las herramientas reacondicionadas. Las bajas variaciones permiten ciclos de reacondicionado más largos y los datos de corte consistentes permiten aumentar la vida útil de la herramienta y el tiempo de funcionamiento de la máquina. La mejoría del proceso de producción también tiene un efecto positivo en la calidad: el control de calidad demostró que la calidad era consistentemente alta desde el primer hasta el último engranaje fabricado con solo ligeras diferencias. Los ahorros en el coste total por pieza dependen del grado de optimización: un caso de optimización probó que en un primer paso se ahorró un 8% por medio de la estabilización del desgaste de la herramienta y se consiguió un ahorro del 16% aumentando la vida útil de la herramienta en un segundo paso. Reduciendo el tiempo de ciclo en el último paso de la optimización, se consiguió un ahorro del 22% en comparación con el estado inicial.
El paquete de servicios ‘primeGear’ demuestra que la alta calidad, ciclos cortos y bajos costes de herramienta no están reñidos. También demuestra que la deseable estabilización del proceso de producción basada en la abrasión controlada, sólo se puede conseguir por medio de un análisis sistemático y una ingeniería de superficie personalizada. El proceso de producción predecible es lo que hace más competitivos a los fabricantes y con ‘primeGear’ pueden predecir la vida de la herramienta y mecanizar engranajes con una consistentemente alta calidad mientras retienen el control total del coste. El posibilitar un uso cuidadoso y sostenible de los recursos es otro muy importante beneficio al elegir ‘primeGear’.