La calidad como prioridad para Audi y Fronius
La tecnología Acerios de plasma activo caliente de Fronius elimina las partículas y películas de suciedad, tanto en superficies metálicas como no metálicas. El fabricante de automóviles Audi lleva dos años aplicando este proceso a las piezas finas de carrocería de aluminio.
Acerios de Fronius ha conseguido reducir significativamente los costes de limpieza de Audi en los casos en que las chapas deben prepararse para la soldadura de pernos, aumentando al mismo tiempo la eficiencia de los recursos.
“En el peor de los casos, el fallo de una conexión con el perno de masa puede provocar que el vehículo se detenga”, afirma el ingeniero Daniel Rudolph, responsable de Desarrollo Tecnológico de Unión y Construcción ligera en Audi AG. “En la producción del Audi A8, colocamos numerosos pernos de masa y tenemos que asegurarnos de que cada uno esté perfectamente conectado. Hacemos todo lo posible por cumplir las exigencias de calidad”.
La calidad de cualquier soldadura de pernos viene determinada en gran medida por las propiedades de la superficie. La contaminación por aceites y lubricantes secos, como los utilizados en el moldeado de metales, puede provocar defectos de unión.
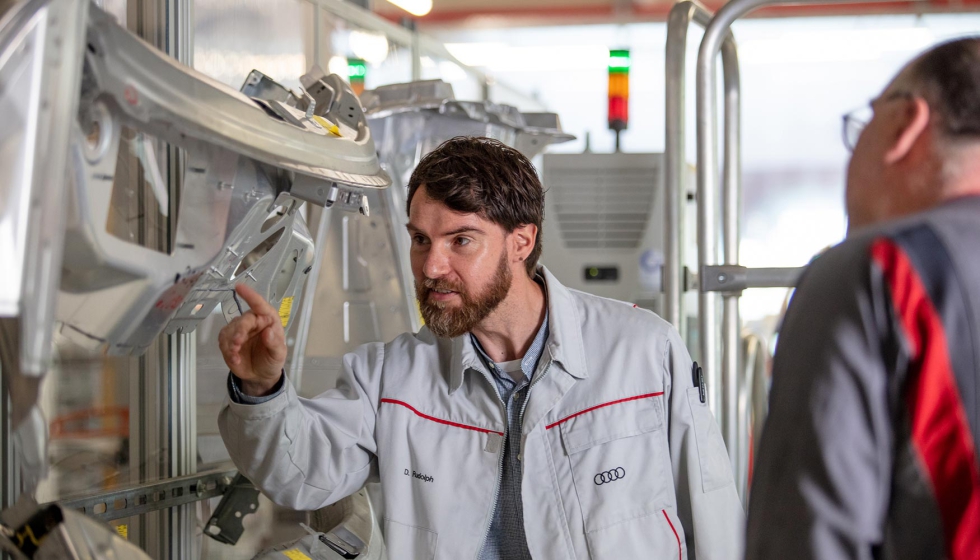
Examen de las zonas del alojamiento del motor que se han sometido a una limpieza por puntos con HAP. Foto: Fronius.
Clean Flash fracasa debido al grosor de chapa
En muchos casos, el problema de la suciedad puede resolverse con la propia soldadura de pernos. Para ello, el proceso de soldadura propiamente dicho va precedido de un aumento de corriente (Clean Flash), que limpia la superficie de trabajo. Sin embargo, este método no sirve para las chapas de aluminio de menos de 2 mm de grosor, ya que estas se quemarían durante la soldadura debido a la excesiva aportación de calor. Asimismo, este proceso puede dar lugar a poros, entre otras cosas, que perjudican la calidad del cordón.
Un componente de este tipo presente en la producción de Audi es, por ejemplo, el alojamiento del motor del Audi A8, que consiste en una chapa de aleación de aluminio (serie 6XXX) de solo 1,5 mm de grosor en los puntos donde se sueldan los pernos de masa: “Durante los primeros años, tras el inicio de la producción en serie, había que limpiar químicamente y decapar todo el componente, lo que requería mucho tiempo y dinero”, explica Rudolph. “Solo así podíamos garantizar siempre el 100 % que se nos exige en lo que respecta a la calidad de la soldadura de los pernos”.
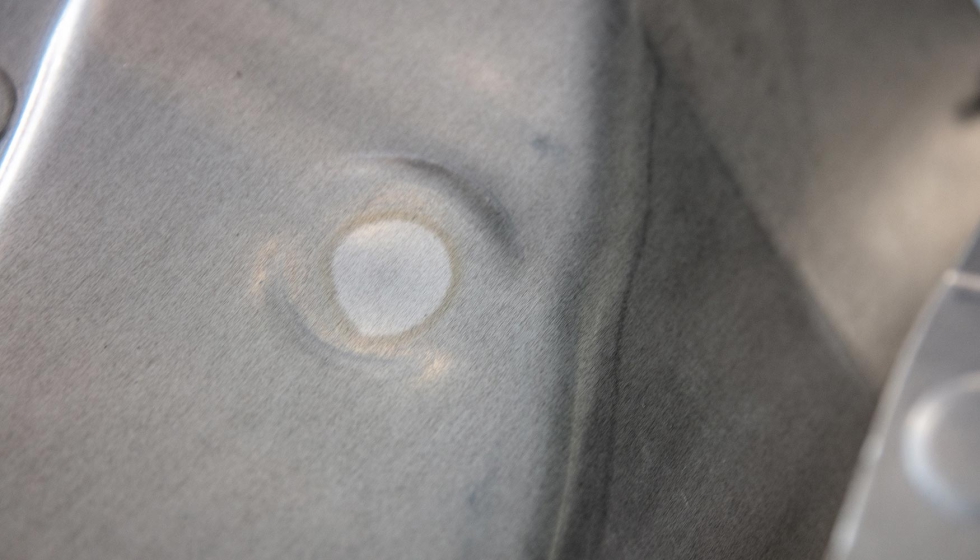
Después del tratamiento con Acerios, el punto de soldadura del perno está libre de aceites y lubricantes. Foto: Fronius.
En 2017, Audi tuvo que construir una nueva instalación de producción para la quinta generación del A8. A su vez, quería encontrar un remedio para la laboriosa limpieza química. Una posible solución era la tecnología de plasma activo caliente (HAP), en la que Fronius, proveedor de tecnología de soldadura y socio de desarrollo desde hacía muchos años, ya había estado trabajando intensamente. Audi también había aplicado ya el enfoque HAP a través de sus universidades asociadas.
Dado que el área de responsabilidad de Rudolph también incluye la evaluación de nuevas tecnologías de fabricación y su posterior desarrollo hasta que estén listas para la producción en serie, los especialistas en tecnología de uniones de Audi y Fronius colaboraron estrechamente. Más adelante, este enfoque técnico se desarrolló conjuntamente y se certificó para la producción en serie. Rudolph explica: “Fronius se encargó principalmente de desarrollar la tecnología de procesos e instalaciones. A continuación, se realizaron en nuestra producción pruebas de funcionamiento relacionadas con la aplicación, pruebas de parámetros, pruebas de vida útil y pruebas funcionales. También analizamos cómo afecta el uso de la tecnología a otras cadenas del proceso, como la unión, la resistencia, la adherencia de la pintura y mucho más”.
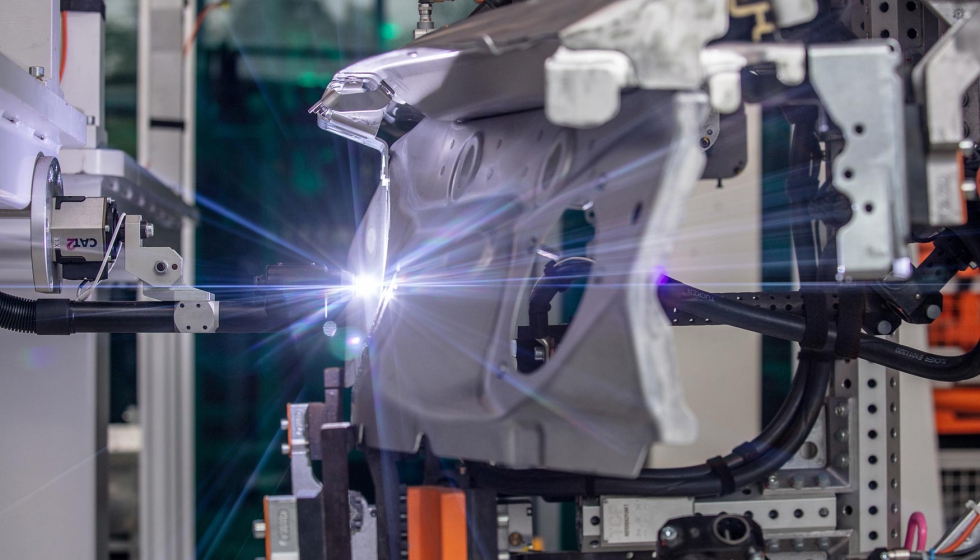
En Audi, el robot guía la pieza de la carrocería hasta la antorcha de plasma de instalación fija (izquierda). Foto: Fronius.
Solución: limpieza parcial con plasma
Las ventajas del tratamiento de superficies con la tecnología Acerios de plasma activo caliente (HAP) de Fronius son muchas. Mediante un flujo de gas protector, el plasma del arco voltaico se transforma en una llama que alcanza temperaturas de hasta 1000° C en el núcleo. Los procesos térmicos y químicos que se desencadenan garantizan que las superficies del material queden libres de forma parcial y precisa de los residuos orgánicos y las películas de suciedad. Al mismo tiempo, se activa la superficie. Dado que el arco voltaico en Acerios se genera entre el inyector de plasma y el electrodo de tungsteno de la antorcha, no es necesario establecer una pinza de masa en la pieza de trabajo. Por consiguiente, los materiales no metálicos también pueden limpiarse con plasma activo caliente.
“Hemos probado Acerios, al igual que todas las nuevas tecnologías que hemos observado más detenidamente, para comprobar su idoneidad, así como para determinar la magnitud de influencia técnica de soldadura y las posibles ventanas de parámetros. Junto con Fronius, optimizamos de forma rápida y eficaz el prototipo para la producción en serie”, explica Rudolph. “A continuación, nuestros planificadores de instalaciones y compañeros de producción se pusieron manos a la obra para identificar una situación de fabricación que fuera favorable”.
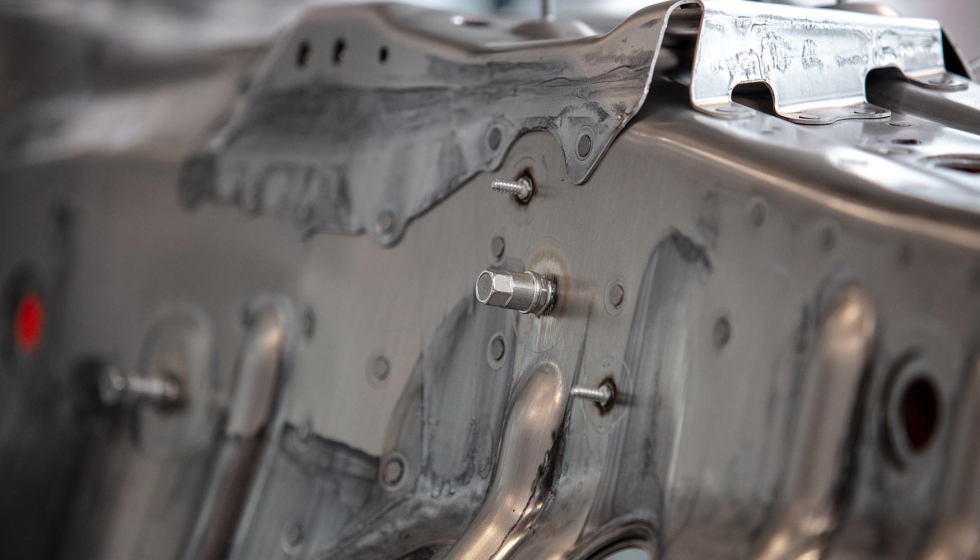
Perno de masa soldado del componente del túnel del Audi A8. Foto: Fronius.
Finalmente, los responsables de la línea del A8 decidieron utilizar Acerios en una celda robotizada que disponía de suficiente tiempo libre no productivo para limpiar dos zonas, cada una con una superficie de 12 cm². “Por lo tanto, el tiempo disponible fue incluso suficiente para aumentar el tiempo de calentamiento del arco voltaico de Acerios a seis segundos por punto de soldadura. La distancia entre la antorcha y la pieza de trabajo es de 30 mm y podemos reducir la corriente a 120 A sin sacrificar el efecto de limpieza”, añade Jürgen Kolbenschlag, experto en soldadura del taller de carrocerías del A8.
“De este modo, nos ahorramos consumibles”, las cuales sustituía antes Audi tras 10 000 puntos de limpieza. Pero incluso después de superar esta cifra, los límites de desgaste aún estaban lejos de alcanzarse. Como resultado, la sustitución periódica se amplió de forma continua. A mediados de 2021, todavía no se había alcanzado el límite de desgaste, a pesar de haberse fijado 25 000 puntos de limpieza.
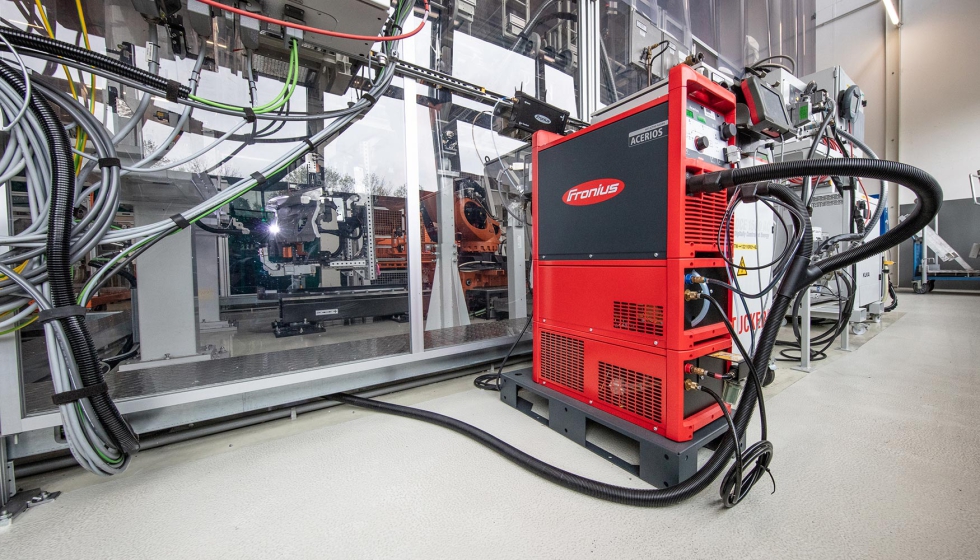
La fuente de potencia de plasma Acerios requiere poco espacio. Foto: Fronius.
Integración sencilla
La integración de la tecnología de plasma activo caliente se vio facilitada por el hecho de que los planificadores pudieron instalar la antorcha de plasma Acerios PCT 2000 de forma fija. Para ello, bastaba con una zona de trabajo mínima dentro del radio de acción del robot. “La fuente de potencia también ocupa menos de un metro cuadrado de superficie, por lo que pudimos colocarla sin problema fuera de la celda, entre las fuentes de potencia existentes”, explica Rudolph.
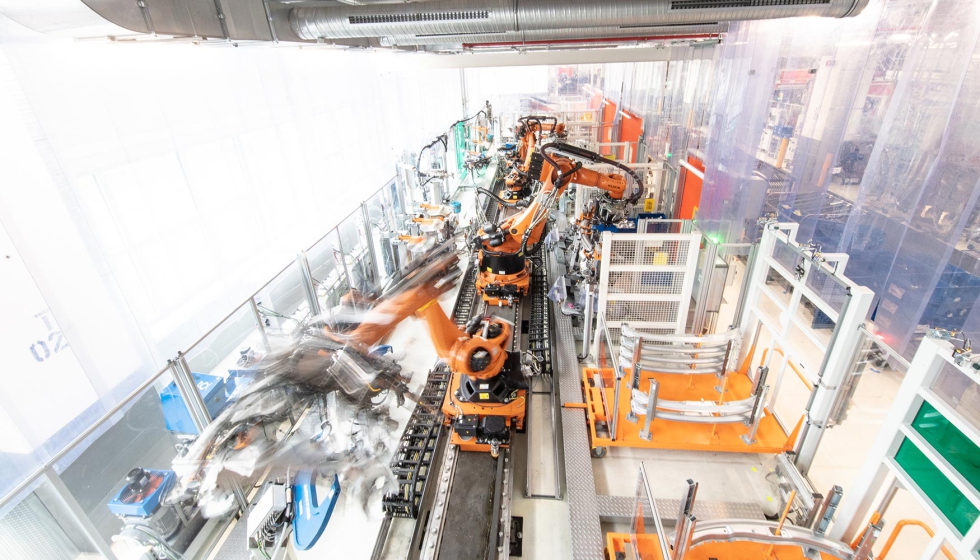
Línea de producción de piezas de carrocería del A8 en Audi, Neckarsulm, Alemania. Foto: Fronius.
El tiempo no productivo que no aprovechaba previamente el robot, se utiliza ahora para transportar el componente a la antorcha. La accesibilidad a la pieza de trabajo también es excelente gracias a la forma estrecha de la antorcha, que permite que la llama de plasma se aplique exactamente en vertical y, por tanto, que pueda estar alineada a la perfección con la superficie. También se elimina la necesidad de utilizar conductos durante el proceso, ya que el efecto de limpieza, que se produce desde el interior hacia el exterior, cubre completamente la superficie deseada en el tiempo de calentamiento del arco.
El hecho de que Acerios funcione con gas protector argón, de bajo coste, también era conveniente para Audi, pues esto permitió recurrir a la red existente de tuberías de argón para alimentar los sistemas de soldadura MIG. Por tanto, no se incurrió en costes adicionales.
La fuente de potencia de plasma, que se conecta a la antorcha mediante un juego de cables de 6 m de longitud, también se integró por Audi con facilidad, como informa Rudolph: “La interfaz del sistema Acerios es la misma que la de nuestros sistemas de soldadura MIG/MAG de Fronius. Como forma parte de la especificación de interfaz de VW, pudimos conectar el sistema Acerios al control de la instalación sin problemas en un solo día”.
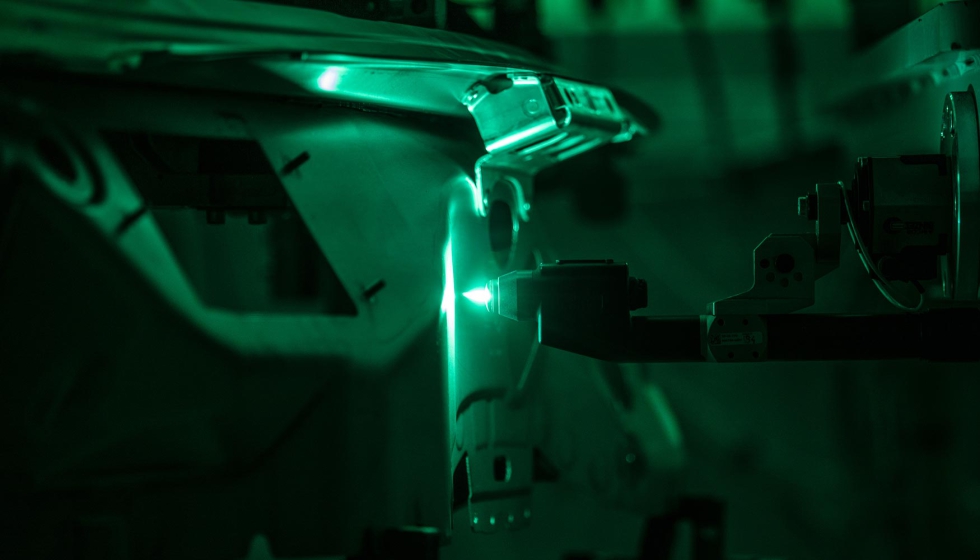
Llama de plasma Acerios en acción con gran precisión. Foto: Fronius.
El ajuste y el manejo de la instalación también se basan en gran medida en los de las fuentes de potencia de soldadura TIG, como confirma Rudolph: “Cualquiera que pueda configurar una fuente de potencia TIG también puede trabajar con el sistema Acerios. El manejo es sencillo de por sí, ya que solo hay que ajustar algunos parámetros, como la intensidad de corriente o el tiempo de combustión”.
Costes de adquisición y explotación asumibles
Las inversiones para el uso de Acerios en Audi han sido comparativamente bajas. Sin embargo, esto no solo se debe a la posibilidad de dar un doble uso a los medios de servicio existentes y diversas piezas de hardware. La amplia experiencia de Audi con otras fuentes de potencia de soldadura de Fronius y sus bajos costes de mantenimiento también fueron factores decisivos. En comparación con otras soluciones de limpieza parcial, el sistema HAP de Fronius se caracteriza por unos costes de adquisición especialmente bajos.
Los sistemas basados en láser, por ejemplo, conllevan una inversión inicial de alrededor de un millón de euros. Sin embargo, la configuración Acerios supone solo una pequeña parte de este precio. Incluyendo la instalación de automatización correspondiente, la solución Fronius se sitúa en torno a las cinco cifras. Además, no es necesaria una celda robotizada blindada independiente, como requiere el sistema de láser. El consumo de energía también es significativamente inferior al de un láser de limpieza. Asimismo, Acerios necesita unos 15 litros de gas por minuto.
El ahorro conseguido también es considerable en comparación con la limpieza en húmedo, que antes se realizaba habitualmente y requería mucho tiempo, como confirma Rudolph: “Pudimos reducir los costes de limpieza por cada alojamiento del motor a una cantidad de euros de una sola cifra y, al mismo tiempo, aumentar la eficiencia de recursos sin comprometer la calidad de la limpieza. Conseguir un ahorro comparable en la construcción de vehículos suele suponer un esfuerzo mucho mayor”.
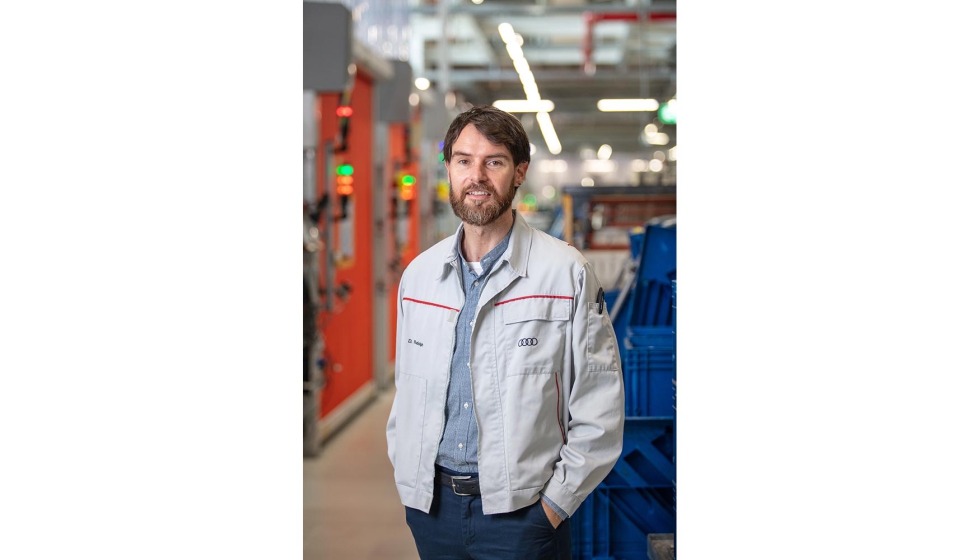
Daniel Rudolph, Desarrollo Tecnológico de Procesos Lineales de Unión, Neckarsulm, Alemania. Foto: Fronius.
Basándose en su experiencia práctica con el sistema, Audi AG concluye que, dados los bajos costes operativos y de adquisición, el uso de Acerios es rentable incluso para pequeños lotes, pero también en la producción a gran escala. Además, la tecnología HAP de Fronius resulta especialmente útil en espacios reducidos y cuando se trata de tareas de limpieza puntuales de segundos de duración.
Acerios amplía la cartera tecnológica de Audi
Debido a estos constantes resultados positivos, Audi ya ha integrado la tecnología de limpieza de Fronius en un componente de túnel, donde las superficies de cuatro soldaduras de pernos también se limpian con tecnología HAP. “Acerios amplía de forma óptima la cartera tecnológica de la que disponemos”, concluye Rudolph. “Siempre que se trata de soldar pernos de masa en componentes con paredes finas, la tecnología HAP está ahora en la lista de favoritos como proceso de limpieza”.
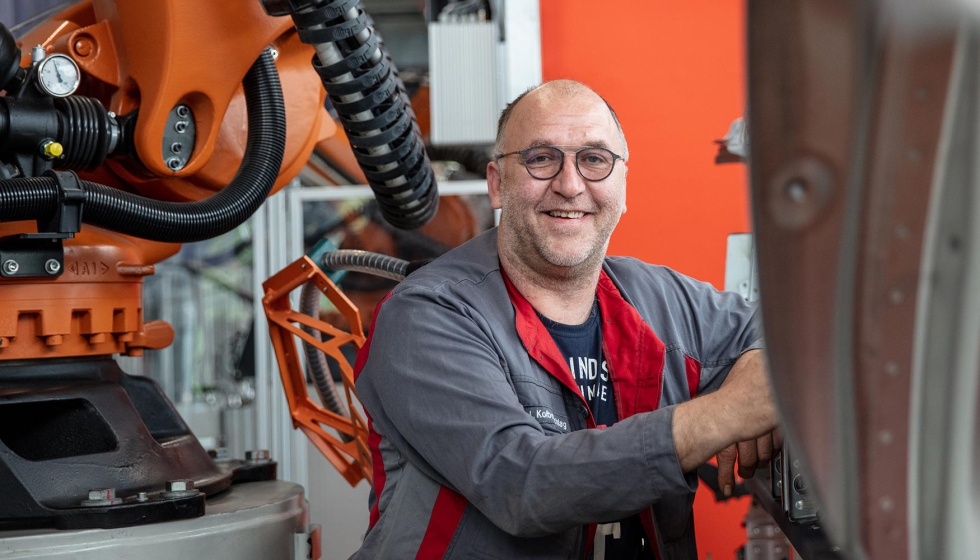
Jürgen Kolbenschlag, instructor certificado de Soldadura DVS en Taller de Tecnología de Construcción de Carrocerías en Neckarsulm, Alemania. Foto: Fronius.