Innovación en el diseño de equipos con gemelos digitales e IA en Advanced Factories 2025 de la mano de MathWorks
En el ámbito de la ingeniería moderna, Matlab y Simulink son herramientas fundamentales para el diseño de equipos de automatización y la optimización de operaciones de producción. Estas plataformas, desarrolladas por MathWorks, permiten a los ingenieros innovar y mejorar la eficiencia y fiabilidad de los sistemas industriales. La empresa explica en Advanced Factories 2025 cómo estas herramientas han facilitado avances significativos en la industria.
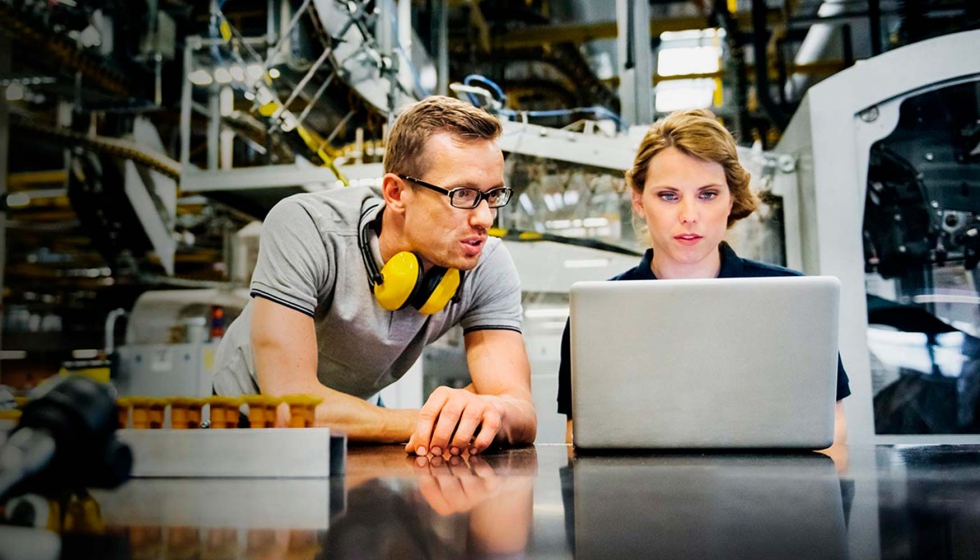
Una de las innovaciones clave es la creación de gemelos digitales. Los ingenieros utilizan Matlab y Simulink para desarrollar modelos virtuales que replican sistemas físicos reales. Estos gemelos digitales son esenciales para la simulación, el diseño de control, la optimización, el mantenimiento predictivo y la detección de anomalías. Simular el funcionamiento de una máquina en un entorno virtual permite identificar fallos potenciales y optimizar el rendimiento antes de implementar cambios, mejorando así la confiabilidad y eficiencia del sistema.
Los fabricantes originales de equipos industriales (OEM) también se benefician enormemente. Matlab y Simulink les permiten diseñar y optimizar sistemas mecatrónicos, combinando ingeniería mecánica, electrónica y software. Los OEM pueden desarrollar software de alta calidad que se integra con el hardware, asegurando un funcionamiento eficiente y fiable. La capacidad de simular diferentes configuraciones en un entorno virtual reduce el riesgo de errores costosos.
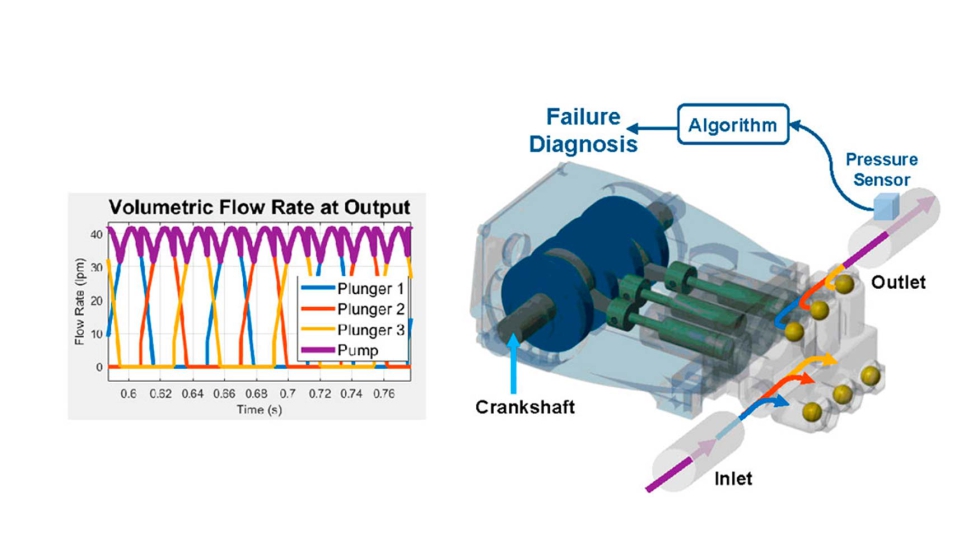
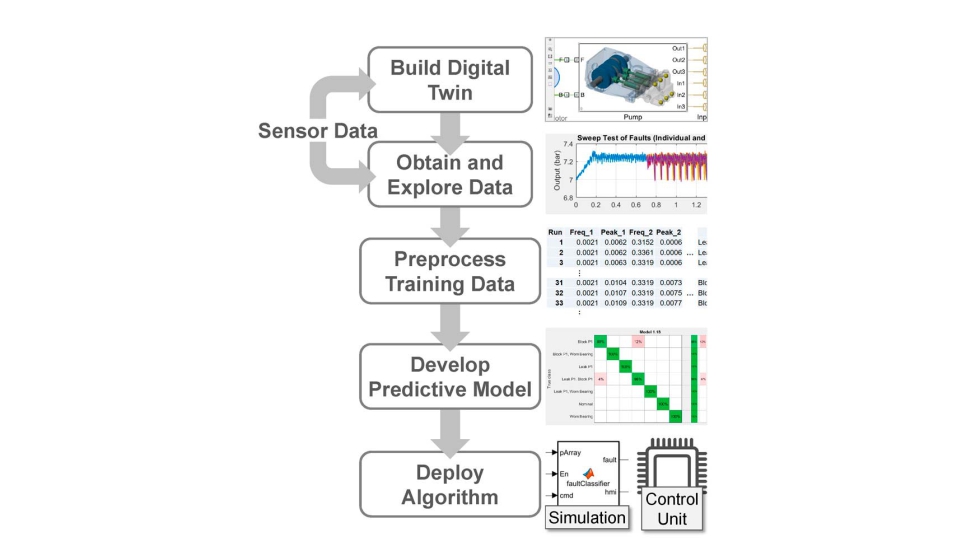
En las fábricas, los operadores utilizan Matlab y Simulink para aumentar la productividad. Analizando los datos de las operaciones diarias, los operadores pueden tomar decisiones informadas y basadas en datos. Esto es crucial en la fabricación, donde pequeñas mejoras en la eficiencia pueden traducirse en ahorros significativos. Las herramientas analíticas de Matlab permiten identificar cuellos de botella y optimizar flujos de trabajo.
Además, expertos en la industria están desplegando algoritmos avanzados y soluciones de inteligencia artificial ‘low-code’ usando Matlab y Simulink, tanto en la producción como en el dispositivo de borde o en la nube. Esto permite a quienes tienen poca experiencia en programación implementar soluciones de IA que mejoran las operaciones de producción. Con algoritmos avanzados, las fábricas pueden predecir fallos, optimizar recursos y mejorar la calidad del producto. La implementación en el dispositivo de borde permite un procesamiento rápido y respuesta en tiempo real, vital en entornos donde cada segunda cuenta.
En resumen, Matlab y Simulink están transformando el diseño y la optimización de sistemas industriales, impulsando la innovación y mejorando la eficiencia. Estas herramientas son esenciales para cualquier organización que busque mantenerse a la vanguardia de la tecnología en la industria manufacturera.
Caso de uso práctico de integración en el ámbito industrial
Desarrollo de soluciones de mantenimiento predictivo con algoritmos de IA para plataformas PLC
En el ámbito de la automatización industrial, integrar soluciones de mantenimiento predictivo con algoritmos de inteligencia artificial (IA) en Controladores Lógicos Programables (PLC) ofrece un enfoque transformador para la fiabilidad y eficiencia del equipo. Este proceso implica varios pasos críticos, comenzando con el desarrollo de modelos de IA capaces de detectar anomalías operativas.
Generación de datos y desarrollo de modelos
La fase inicial se centra en la generación de datos sintéticos. Utilizando modelos de diseño mecánico y eléctrico, los ingenieros pueden simular diversos escenarios operativos y modos de fallo potenciales. Estos datos sintéticos sirven como un conjunto de datos fundamental para entrenar los algoritmos de IA, permitiendo la identificación temprana de patrones indicativos de fallos en el equipo.
Integración de algoritmos
Una vez entrenados, estos modelos de IA se integran con plataformas PLC, que son ubicuas en entornos industriales debido a su robustez y capacidades de procesamiento en tiempo real. El proceso de integración implica incrustar los algoritmos de IA en la arquitectura de los PLC, permitiéndoles procesar flujos de datos en tiempo real desde sensores y otros dispositivos de entrada.
Detección de anomalías
La funcionalidad central de estos sistemas PLC mejorados con IA es su capacidad para detectar anomalías. Al monitorear continuamente el rendimiento del equipo, los modelos de IA pueden identificar desviaciones de las condiciones normales de operación, prediciendo así posibles fallos antes de que ocurran. Este enfoque proactivo minimiza el tiempo de inactividad y extiende la vida útil de la maquinaria industrial.
Implementación y pruebas
Tras la integración, se realizan pruebas rigurosas para asegurar la fiabilidad y precisión del sistema de mantenimiento predictivo. Esto implica pruebas en el mundo real donde se evalúa el rendimiento del sistema bajo diversas condiciones operativas para asegurar que cumpla con los estándares industriales.
El desarrollo de soluciones de mantenimiento predictivo utilizando IA en plataformas PLC implica la generación de datos sintéticos, el entrenamiento e integración de algoritmos, y pruebas exhaustivas, lo que lleva a una mayor eficiencia operativa y reducción de costos de mantenimiento en entornos industriales.