El proyecto EOCENE desarrolla nuevos componentes basados en materiales compuestos termoestables
El proyecto de investigación EOCENE, pionero en economía circular para minimizar el impacto medioambiental en el sector industrial de los materiales compuestos, ha concluido con éxito. Este proyecto ha logrado avances significativos en la valorización y reutilización de residuos y en la reducción de emisiones de CO2, marcando un hito en la colaboración empresarial y la innovación sostenible.
Así lo destacan fuentes Fundación Empresa Clima que coordina la comunicación del proyecto —cuyo objetivo ha sido “revolucionar la industria de los materiales compuestos termoestables mediante la implementación de principios de economía circular, reduciendo la huella ambiental en diversas aplicaciones finales”— que refleja “el compromiso con un futuro más sostenible y la promoción de prácticas respetuosas con el medio ambiente”.
El Proyecto EOCENE es una iniciativa conjunta de Cosentino, Acciona, Agbar (Grupo Veolia), Kimitec, Omar Coatings, Aerotecnic, y 19 entidades de investigación. Cada miembro ha aportado su experiencia y conocimientos, posicionando al proyecto en la vanguardia de la innovación sostenible, apuntan las mismas fuentes.
El respaldo del Ministerio de Ciencia e Innovación y la inclusión del proyecto en el ‘Programa Misiones’ del Centro para el Desarrollo Tecnológico y la Innovación (CDTi) “subrayan” su relevancia. “Los resultados incluyen prototipos demostradores de nuevas soluciones de materiales y tecnologías de procesado de residuos, estableciendo las bases para su implementación en varios segmentos industriales”.
El evento final del proyecto tuvo lugar el pasado 18 de junio en Cosentino City Madrid, un acto que contó con la apertura y ponencia de Valentín Tijeras, vicepresidente global de Producto, I+D+i y Calidad de Cosentino. A continuación, tuvo lugar una mesa redonda en la que intervinieron representantes de cada uno de los miembros del consorcio, quienes discutieron los avances y logros del proyecto. La conferencia magistral final corrió a cargo de la directora de la Fundación Empresa y Clima, Elvira Carles, quien compartió con los asistentes la situación actual de emergencia climática.
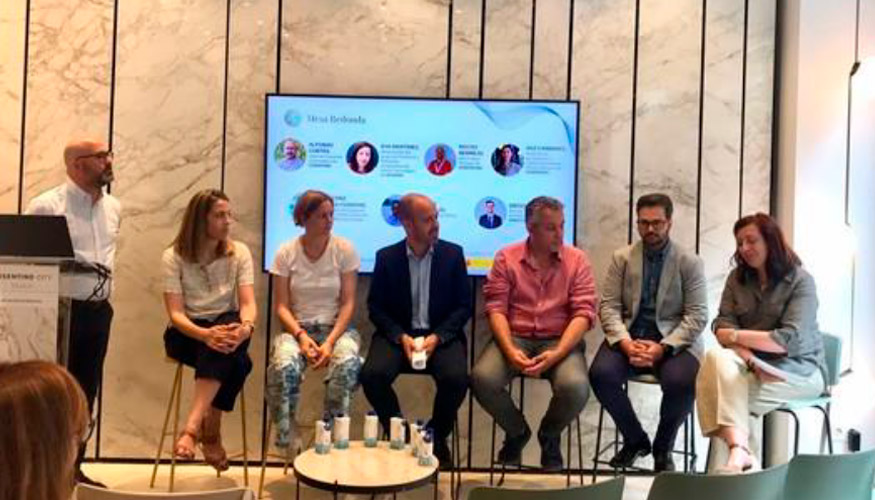
Innovaciones clave del Proyecto EOCENE
El Proyecto EOCENE “ha logrado avances significativos en la búsqueda de soluciones sostenibles e innovadoras para la industria de materiales y construcción. Estos hitos no establecen un precedente en la fabricación de materiales de alto rendimiento con un menor impacto ambiental”. Las mismas fuentes enumeran las principales innovaciones desarrolladas en el marco del proyecto:
1.- Desarrollo de resina de poliéster innovadora
Omar Coatings y Cosentino han desarrollado una resina de poliéster innovadora con un 70% de contenido bio a partir de fuentes renovables, destinada a la producción de Silestone. Aunque actualmente se ha logrado sintetizar a nivel de laboratorio, se continuará trabajando en su escalado industrial.
2.- Nuevas superficies para la arquitectura y el diseño con menor impacto ambiental
Cosentino ha creado prototipos de Silestone en planta piloto que implican una reducción significativa en huella de carbono del material, utilizando para ello componentes (resinas y cargas minerales) de alto carácter sostenible, pues provienen de residuos y subproductos industriales. Los resultados obtenidos son escalables con la tecnología de producción disponible y los materiales obtenidos tienen prestaciones técnicas equivalentes a los del Silestone actual.
3.- Monómeros bio
Kimitec ha obtenido tres monómeros aptos para la producción de poliéster mediante fermentación, reemplazando derivados del petróleo. Estos monómeros se han producido en lotes de cien litros, permitiendo un análisis preciso de la huella de carbono.
4.- Biodegradación de residuos de lodo
Kimitec ha investigado la biodegradación de lodos generados durante el pulido de Silestone, demostrando una degradación significativa y abriendo la posibilidad de utilizar técnicas de biorremediación.
5.- Biorresinas epoxi y vinilester para construcción
Acciona ha sintetizado un precursor de resinas epoxi a partir de vainillina, logrando una bioresina con más del 50% de contenido biobasado. La nueva bioresina es procesable por pultrusión, RTM e infusión. Este desarrollo es crucial para la fabricación de materiales compuestos estructurales en ingeniería civil, ya que cumple con todos los requerimientos.
Acciona ha sintetizado una resina vinilester biobasada a partir de vanillina con Tg>100°C, que debe ser estabilizada antes de proceder a su futuro escalado industrial.
6.- Hormigón-polímero sostenible
Acciona ha desarrollado un hormigón-polímero con más del 80% de cargas provenientes de residuos valorizados de Cosentino y Acciona, cumpliendo con los requisitos técnicos para usos industriales y marítimos.
7.- Materiales compuestos para la industria aeronáutica
Aerotecnic ha sintetizado un precursor de resina epoxi a partir de aceite de soja y ha desarrollado fibras de carbono recicladas, alcanzando una reducción del 54% en la huella de carbono en los materiales y proceso de fabricación de una aeroestructura.
8.- Materiales compuestos para la industria de la construcción
Acciona ha puesto a punto un proceso de reciclaje térmico a escala de laboratorio que ha permitido obtener fibras recicladas tanto de vidrio como de carbono, así como recoger los productos de descomposición térmica de las matrices poliméricas (líquidos pirólisis) para su posterior valorización. La calidad de las fibras obtenidas es adecuada y se han podido obtener diferentes productos intermedios: fibra corta, 'mats', velos, hilo continuo a partir de discontinuo.
9.- Transformación de residuos en recursos
Agbar ha logado transformar el 100% de los residuos de Cosentino en recursos sostenibles, incorporando hasta un 80% de materiales reciclados en productos como pavimentos de hormigón circular y pavimentos captadores de CO2.
Acciona ha logrado pultruir un laminado plano a partir de fibra reciclada de carbono discontinua a partir de continua, así como de fibra de vidrio reciclada (spun roving). Así mismo ha logrado hacer laminados por infusión usando dichas fibras recicladas. Además, la compañía ha conseguido fabricar un compounding de fibra de vidrio reciclada y matriz termoplástica (PP) compatibilizada con el sizing adecuado; formulaciones formulaciones de BMC a partir de fibra de vidrio reciclada y fibra de carbono con propiedades mecánicas comparables a las que existen comerciales, y ha incorporado como carga de refuerzo en un perfil pultruído y laminados fabricados por infusión, polvo de composite reciclado sobre resinas bioepoxi y biovinilester (reciclado mecánico).