Tecnología Titech en la planta de clasificación de envases de Málaga de Limasa
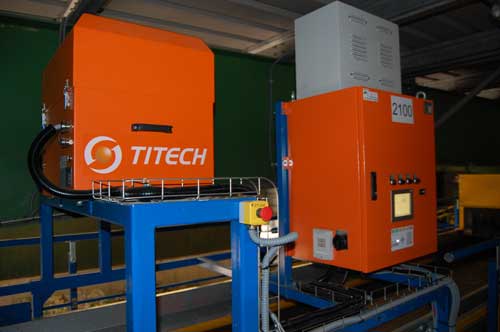
Limasa, empresa mixta encargada del servicio de limpieza pública, recogida, transporte, tratamiento y eliminación de los residuos sólidos urbanos (RSU) de la ciudad de Málaga, atiende a una población aproximada de 600.000 habitantes. Para el desarrollo de los procesos de tratamiento, valorización y eliminación dispone de un Centro Ambiental ubicado en la Finca 'Los Ruices', con una superficie de 320 Has repartidas en distintas instalaciones. Una de estas instalaciones, la Planta de Clasificación de Envases, ha sido objeto de una reciente remodelación, que ha supuesto su completa automatización y la adquisición del equipamiento necesario para tratar un flujo de residuos con un mayor porcentaje de envases recuperables, con el objetivo de alcanzar efectividades de recuperación de los materiales de al menos el 95%.
Carlos Manchado Atienza, director para la Península Ibérica y Latinoamérica de Titech, que ha seguido muy de cerca este proyecto, ha explicado: “Esta es la primera planta española en funcionamiento dotada con los nuevos sistemas Titech autosort 4, trabajando para el Sistema Integrado de Gestión (SIG) de Ecoembes, con unos resultados y rendimiento, que aunque esperados, han sido muy elevados”.
Además, Manchado declara sentirse muy satisfecho con el resultado de esta instalación, la primera de una nueva generación de plantas, ya que según él mismo ha avanzado: “la tecnología del nuevo autosort 4 será implementada en breve en otras plantas de la geografía española (Tudela, Barcelona, Madrid y Mallorca, entre otras) que ya han emprendido su modernización y adaptación a las nuevas exigencias tecnológicas y de mercado. Con ello obtendrán importantes ahorros en energía y mantenimiento y una mayor fiabilidad y rendimiento de sus equipos”.
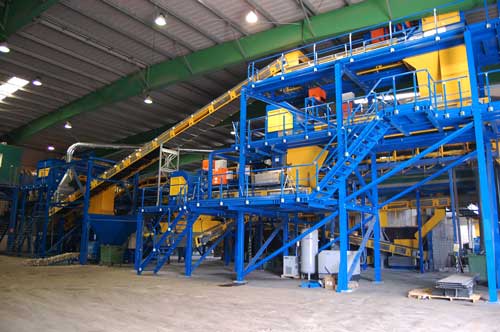
Más eficiencia y mayor capacidad productiva
La mejora de la planta, según consta en el proyecto, se ha realizado con criterios de eficiencia técnica, viabilidad ambiental y económica. Para ello, entre el nuevo equipamiento incorporado, Limasa ha adquirido tres separadores ópticos Titech autosort 4, los primeros equipos con sensores infrarrojos de cuarta generación que se instalan en una Planta de Clasificación de Envases en España.
En los últimos 5 años las cantidades de envases procedente de la recogida selectiva de envases en la ciudad de Málaga se ha prácticamente duplicado pasando de las 2.880 t (año 2007) a las 4.896 toneladas (año 2012) y la previsión para 2013 es alcanzar las 5.000 toneladas. El diseño de la planta se ha realizado pensando en dotarla de la mayor flexibilidad para atender tanto la demanda actual como la posible evolución de las entradas de material. Según ha explicado Javier Pazos Parent, director del Centro Ambiental de Limasa “La nueva línea está dimensionada para el tratamiento de 3 t/h de residuos de envases, con la máxima eficiencia de recuperación, al implantar las últimas tecnologías de selección de envases que hay en el mercado”.
Así, con el sistema de selección óptico, en la planta se separan de forma automática los envases según el tipo de plástico: PET (botellas de agua, bases de pizza, bandeja alimentaria…), PEAD (botellas de detergentes, suavizantes…) y Plástico mezcla (resto de plásticos como PP, PVC, PS, utilizado para bandejas de fruta, carne, yogures...). También el brik se clasifica mediante la tecnología Titech autosort 4. Asimismo, al final de la cadena un equipo óptico realiza la recirculación a cabecera de proceso de los posibles plásticos y briks que pudieran llegar a este punto con el fin de alcanzar el máximo aprovechamiento y nivel de recuperación de los envases. Para Javier Pazos, las ventajas que aporta la tecnología Titech son claras: “la inclusión de esta tecnología ha representado una mayor eficiencia, reducción de costes y un aumento de la capacidad de producción”.
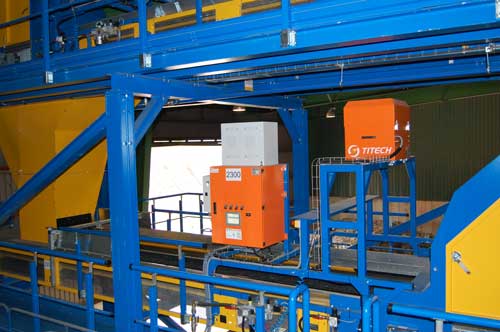
Gracias a sus innovadores sensores, los sistemas Titech autosort analizan y clasifican los diferentes materiales con mayor velocidad y precisión que las técnicas convencionales, incluyendo la clasificación manual. Titech autosort 4 es el primer sistema de escaneado por infrarrojo cercano (NIR) que no requiere una fuente de luz externa para su funcionamiento, ya que incorpora la tecnología Flying Beam, que integra las lámparas en el interior de la caja del escáner e ilumina sólo el área exacta de la cinta transportadora que escanea. Esta tecnología aporta como principales beneficios una mayor estabilidad en la fase de detección, una reducción del consumo de energía eléctrica, hasta un 70%, y una menor necesidad de mantenimiento.
En cuanto al proceso de instalación, adecuación al proyecto existente y atención técnica de Titech, Javier Pazos también está satisfecho: “El servicio postventa ha realizado una excelente gestión minimizando cualquier inconveniente. Hemos compartido bastante tiempo con los técnicos y ello nos ha permitido familiarizarnos rápidamente con el funcionamiento. Además, hemos firmado un contrato de mantenimiento con Titech para mantener una buena asistencia técnica y garantizar el mejor rendimiento de los equipos”. Esta es la mejor manera de tener el conjunto de separadores ópticos optimizados y con un mínimo riesgo de averías, ya que implica revisiones periódicas del funcionamiento mecánico, eléctrico y neumático de los equipos y también la actualización del software y recalibrado de los sensores, operaciones que consiguen aumentar el nivel productivo de los ópticos.
El proceso de clasificación de los autosort 4 en la línea
Hay un total de 3 equipos instalados, trabajando sobre el flujo de rodantes del separador balístico: una unidad de una anchura de 1.000 mm (Titech autosort 4 [NIR][S1000]) y dos unidades de 1.400 mm de ancho (Titech autosort 4, [NIR][S1400]), estos últimos de doble track. El primer equipo separa los plásticos del resto del material (no plásticos). Estos dos flujos caen separadamente sobre una cinta dividida longitudinalmente que alimenta la cinta de aceleración del segundo separador óptico.
En este siguiente separador óptico, de doble track, se separa el PET del flujo de plásticos y el Brik del flujo de no plásticos. Ambos materiales van a cabina de triaje para control de calidad. El resto del material alimenta al tercer separador óptico, también de doble track, que separa PEAD del flujo de plásticos, quedando por defecto el plástico mezcla; mientras del flujo de no plásticos separa todos los posibles plásticos que pudieran haber llegado a este punto para su recirculado al inicio de la cadena de ópticos.
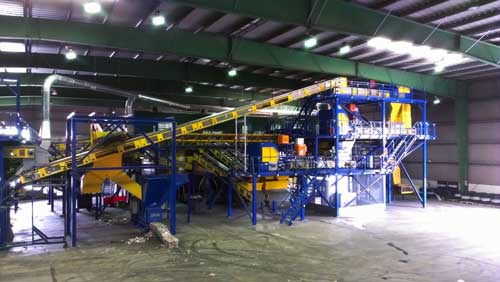
Este diseño con sistemas de Doble track ha permitido a Limasa optimizar la inversión, ya que un único óptico es capaz de separar dos fracciones cada vez, pero manteniendo los ratios de recuperación y pureza de los materiales separados por los Titech al máximo. Ello, junto a la nueva generación de Titech autosort, ayuda a alcanzar y superar el 95%, tal y como las primeras pruebas han mostrado.
Además del innovador sistema de iluminación del escáner, ya comentado, esta nueva generación de equipos incluye otras características avanzadas, como una tarjeta para el control de las válvulas de soplado de alta capacidad, una unidad de control más potente (CU) y un nuevo concepto de bloque de válvulas. La CU está dotada de un ordenador industrial, que ofrece un rango de temperaturas ampliado y dispone de refrigeración pasiva a base de disipadores de calor. Por su parte, los nuevos bloques de válvulas de Titech, con controladores de alta velocidad, permiten una precisión y una pureza de separación aún mayor con válvulas hasta 3 veces más rápidas, con menor separación entre sí (25 mm), de menor diámetro (2,2 mm) y con menores consumos (aprox. 200 l/min), en lugar de 30 mm de separación, 3,5 mm de diámetro y 300 l/min de consumo de las válvulas estándar de la anterior generación de Titech autosort.