Materiales de alto rendimiento, una plataforma hacia el éxito
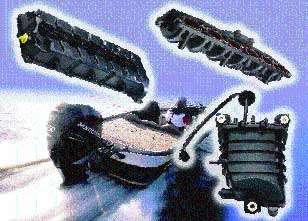
DuPont ha desarrollado un severo sistema para guiar su esfuerzo innovador. De forma sistemática realiza una segmentación basada en las necesidades del cliente para identificar objetivos comerciales relevantes. Estos objetivos se someten a una revisión y se establecen las prioridades, utilizando criterios diferenciados consistentes con las misiones comerciales individuales. A continuación se prosigue con cada proyecto principal empleando rigurosas prácticas de gestión de proyectos.
DuPont denomina a sus proyectos tecnológicos de máxima prioridad el Top 75. Para analizar estos Top 75 de forma cuantitativa se ha desarrollado el índice de tracción. Éste mide las oportunidades más altas de beneficio identificadas por sus empresas frente a lo que cree su organización en I+D que puede conseguirse de cada prioridad. El índice considera la relevancia en el mercado de cada proyecto, su singularidad técnica y su plan de comercialización. Cada uno de estos componentes se analiza en cinco factores cruciales. A estos factores se les atribuyen valores; la puntuación de confianza en cada componente que va de cero a 100 se establece haciendo una media de estos cinco factores cruciales. El índice de tracción es, por lo tanto, el producto de las medias de los tres componentes expresado en porcentajes. Este sistema permite a DuPont prever de forma más precisa cómo reparte el valor de su I+D. El negocio de Ingeniería de Polímeros ha cosechado recientemente algunos éxitos en sus actividades de innovación.
Estética funcional
En desarrollo, otro material, Shine-E Rynite, amplía las fronteras de la sustitución del metal por plásticos. Combina un brillo superficial muy alto con las posibilidades de alta temperatura y las propiedades estructurales del poliéster termoplástico reforzado con PET.
Aquellos paneles de automóviles pintados con esta nueva resina pesarán menos que la pieza equivalente en metal. La superficie similar a un espejo de las piezas sin pintar abre otras prometedoras aplicaciones: piezas de electrodomésticos que están expuestas al calor como manillas de puertas de hornos, tostadores, carcasas y carcasas de motores. En la actualidad, DuPont está desarrollando versiones conductivas eléctricamente que apuntan a mayores aplicaciones que requieran disipación electrostática.
Asimismo, están extendiendo esta competencia de decoración a otras resinas de su cartera de Ingeniería de Polímeros, como por ejemplo, la poliamida reforzada con mineral Minlon y la poliamida de alto rendimiento Zytel HTN. Por ejemplo, el nuevo grado de chapa en Zytel HTN es una sustitución robusta y efectiva en costes del metal enchapado para muchas aplicaciones que requieren altas temperaturas y estabilidad dimensional. Su potencial está en dispositivos eléctricos, industria automovilística y otras industrias: piezas como botones y pasamanos en dispositivos que se calientan como hornos y cocinas; en el campo automovilístico piezas bajo el capó o cubiertas de ruedas que soportan el calor de los frenos.
Para probar estas tecnologías y apoyar los desarrollos con sus clientes, la compañía dispone de un laboratorio de decoración muy moderno en el Centro Técnico Europeo, con sede en Ginebra. Edificio que será muy similar a los que se están construyendo en EEUU y Japón.
Mientras tanto, otras extensiones de la cartera de estética funcional de DuPont en la línea de investigación incluyen poliamidas transparentes y decoración mediante sublimación en 3D.
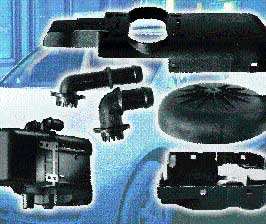
Polimerización continua para la poliamida HTN de alto rendimiento
Unión estructural de plásticos disimilares
Por ello, DuPont ha desarrollado la unión estructural, una nueva tecnología que permite una unión firme de casi cualquier plástico disimilar utilizando cualquier proceso que una las dos superficies en estado fundido. Ejemplos de tales procesos son el moldeado de doble componente, el sobremoldeado o cualquier tipo de soldadura. La tecnología de unión estructural consiste en una capa tirante microporosa especialmente desarrollada que tiene como consecuencia una fuerte unión física entre los dos materiales. DuPont dispone de dos aplicaciones de patentes que cubren este descubrimiento.
Los desarrollos tempranos de la aplicación incluyen componentes suaves al tacto realizado mediante sobremoldeado o moldeado de doble componente y la soldadura de componentes de poliacetal a la superficie de los tanques de combustible en polietileno.
Membrana activa
La membrana activa tiene muchas aplicaciones posibles; ya se comercializa como revestimiento de techos, los cuales se colocan bajo las tejas para evitar que la lluvia y la nieve penetren mientras que dejan que traspase el vapor de agua. Su excelente rendimiento permite que se utilicen estos revestimientos en techos con una oscilación de 5°, mientras que el límite práctico de modelos anteriores era de 10°.
Las aplicaciones de la membrana activa en vestimentas médicas todavía están en proceso de desarrollo. Las vestimentas médicas proporcionan una protección impermeable contra los fluidos corporales, bacterias y virus, aunque permiten que la transpiración se evapore. La membrana es impermeable a partículas extremadamente pequeñas, incluso al virus más pequeño conocido, el Phi-X174, que sólo tiene 0,027 µm de diámetro.
TiO2
Este tipo de composición reduce costes y mejora la calidad, ya que los aditivos seleccionados se añaden de forma precisa al TiO2 de encargo que se está componiendo. El centro de su mercado inicial ha sido la industria de polímeros, aunque se están evaluando otros segmentos del mercado como la industria de recubrimientos y la industria papelera. DuPont ha abierto recientemente una planta para la producción personalizada de TiO2 u otros productos incoloros o blancos con una medida de submicras en Antwerp, Bélgica.
Polímeros conductivos
Asimismo, se ha visto el potencial de sus resinas conductivas en muchas otras aplicaciones, donde había que disipar las cargas estáticas: maquinaria comercial, periféricos de ordenadores, muchos dispositivos electrónicos, equipos médicos y otros. Además, se están utilizando tecnologías relacionadas con resinas conductivas en aplicaciones de dispositivos EMI.
ETPV
CRT y ELV
Más que una simple tecnología consistente en emplear material ya utilizado y convertirlo en material nuevo. Asegurarnos que lo que hacemos hoy será sostenible mañana, en términos de beneficios a la economía y a la sociedad en general.
El reciclado de plásticos, principalmente de embalajes, es un negocio en curso en muchas partes del planeta. Pero no ha habido muchas iniciativas en este campo en el sector del automóvil. La normativa que lo regule pronto va a modificar este panorama.
Cada año, cerca de 12 millones de vehículos en la Unión Europea se convierten en vehículos dados de baja o ELVs. Dichos vehículos generan más de ocho millones de toneladas de residuos. La Comisión Europea ha promulgado una Directiva que exige, entre otras cosas, que todos los vehículos que se vendan en la UE a partir del 1 de Enero de 2006 deben ser reciclables en un 85 por ciento, y en 2015 en un 95 por ciento. Las cifras alcanzan ahora un 75 por ciento.
DuPont ha desarrollado una tecnología compuesta de reciclado para nylon para ayudar a la industria automovilística a alcanzar estos objetivos. Se trata de un proceso de bucle cerrado que se inicia con piezas de vehículo utilizadas de nylon reforzado con cristal o con mineral y que se torna en el equivalente de material virgen.
Conjuntamente con su socio japonés, Denso Corporation, DuPont ha investigado la posibilidad de un bucle cerrado potencial a gran escala, reciclando pieza por pieza. Se recogieron 500 tanques frontales de radiadores fabricados en nylon de 66 de coches estropeados de Japón. El material estaba degradado por los años en contacto con el refrigerante del motor. Se redujeron los tanques e introdujeron las partículas en el reactor prototipo. Al disolver el polímero, filtrando las fibras de vidrio y los contaminantes, y precipitando, secando y reconstruyendo el polímero, se produjo un nuevo nylon parecido al 66. Se mezcló con fibra de vidrio y moldearon nuevos tanques frontales.
Los materiales mezclados se sometieron a una serie de pruebas: fuerza, rigidez y fuerza de impacto del reciclado mezclado, las cuales consiguieron resultados similares a las del nylon virgen. Se sometió a los tanques frontales de radiadores moldeados con el material reprocesado a pruebas adicionales, incluyendo deslizamiento en altas temperaturas, ciclos de alta temperatura, e impacto de vibración y de baja temperatura. Los resultados obtenidos fueron similares a aquellos en tanques fabricados en materiales vírgenes. En ambos casos, superaban las exigencias de los clientes de la empresa automovilística de Denso.
Nueva clase de vulcanizados termoplásticos técnicos
El ETPV de DuPont amplía la variedad de aplicaciones de los elastómeros termoplásticos, especialmente cuando se necesita una mayor resistencia al calor y a los líquidos. Las piezas fabricadas en este nuevo material resisten el aceite, la grasa y los productos químicos con un rango de temperatura de entre -40 °C y 160 °C. Actualmente, se están realizando más pruebas con una temperatura de hasta 170 °C. Su combinación de propiedades lo convierte en un producto adecuado para aplicaciones de automoción colocadas bajo la carrocería, como conductos o tubos, juntas de ignición, juntas de dos componentes y tapones, mangueras hidráulicas y compartimentos con junta homocinética (CVJ) a bordo.
Suministrado en formato granulado, el ETPV de DuPont es adecuado para el moldeado por inyección, el moldeado por presión de líquido, el moldeado por extrusión o el moldeado de dos componentes en equipo de procesado termoplástico estándar. En un principio, se ofrecerán dos calidades, 90 Shore A, con niveles máximos dentro del rango de dureza y 60 Shore A, con niveles mínimos dentro de ese rango. Ambas calidades están disponibles en versiones estándar (1000 horas a 150 °C) y estables térmicamente (3000 horas a 150 °C). Actualmente, se están elaborando otras calidades.
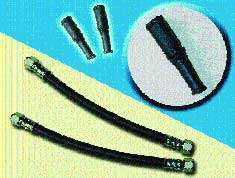