Tendencias en el campo de la fundición inyectada
1. Introducción
La fundición inyectada ha demostrado su versatilidad y eficiencia económica, aplicándose a una gran variedad de productos en sectores tan diferentes como el de automoción, aeronáutico, eléctrico, componentes electrónicos, etc.
Todas estas aplicaciones de la fundición a alta presión se fundamentan en la posibilidad de producir grandes lotes de productos en tiempos reducidos y a un bajo coste. Ello se consigue a costa de disminuir la calidad de los productos en relación a los obtenidos con otras técnicas, como la fundición por gravedad o la fundición a baja presión. Esta disminución de la calidad es debida básicamente a la generación de defectos, en forma fundamentalmente de porosidad, y que fragilizan los componentes, imposibilitando la realización de tratamientos térmicos de mejora de propiedades e incluso su soldabilidad.
De acuerdo con los últimos análisis realizados por la North American Die Casting Association (NADCA), se prevé un notable incremento de la producción de componentes obtenidos mediante fundición inyectada. Este incremento se produciría principalmente en componentes obtenidos con aleaciones de aluminio.
La continuidad de las empresas que se dedican a estas tecnologías pasa por intervenir en la mejora del producto/proceso en base a:
- Disminuir los costes de fabricación
- Mejorar la calidad de los productos
- Incrementar las aplicaciones
La disminución de costes se puede conseguir interviniendo en aspectos diferentes como son:
- Disminución de los costes de personal: la disminución de los costes de personal se ha venido consiguiendo introduciendo mejoras en la automatización y control de los mismos. Las necesidades inmediatas pasan también por incrementar la productividad, lo que implica, entre otros factores, la necesidad de personal altamente cualificado, que no sean sólo ‘apretadores de botones’.
- Incremento de la vida útil de los moldes: el incremento de la vida útil de los moldes pasa por el correcto diseño de los mismos, pero también por incidir en aquellos parámetros que afectan a las condiciones de servicio: el tratamiento térmico preventivo de alivio de tensiones, la utilización de menores temperaturas de inyectada, el uso de aleaciones mejoradas, etc.
- Optimización del diseño de los componentes y de los moldes. La simplificación del diseño y el rediseño con estructuras híbridas, así como la correcta utilización de las herramientas de simulación, y la adaptación de las mismas a las innovaciones tecnológicas, son reglas básicas a tener en cuenta.
- Ahorro de la energía utilizada: la disminución de energía consumida es una necesidad de las empresas por el elevado coste de la misma, y se viene consiguiendo en base a disminuir el valor de parámetros tales como la disminución de los tiempos de ciclo, la utilización de máquinas de menor fuerza de cierre, en base a un diseño mejorado de los moldes, o la disminución de la temperatura del caldo, lo que entra en contradicción con la colabilidad.
La mejora de las propiedades, básicamente mecánicas, pasa por reducir aún más la cantidad y tamaño de los defectos, rechupes y gas atrapado principalmente, y que son inherentes al proceso de fabricación. La eliminación de los mismos permitiría la realización de tratamientos térmicos de mejora de propiedades, como serían los tratamientos T4, T5 o, fundamentalmente, T6. Estos tratamientos serían aplicables a aquellas aleaciones susceptibles de esta mejora de propiedades, como es la aleación EN AC-46000 (AlSi9Cu3), una de las más utilizadas en la fundición inyectada. Estos tratamientos mejoran la resistencia mecánica y la resistencia a fatiga. Estas mejoras de propiedades actualmente las proporcionan técnicas como la fundición inyectada de alta presión al vacío, la técnica Vacural, la Nissan Innovative Casting Process, o el proceso Pore-free, entre otros. Pero si además se pretende alargar la vida del molde, son los procesos de conformación en estado semisólido (SSM) los recomendados. La NADCA incluye a estos procesos SSM en el bloque de técnicas de Alta Integridad. Estas tendencias se pueden visualizar en la Figura 1.
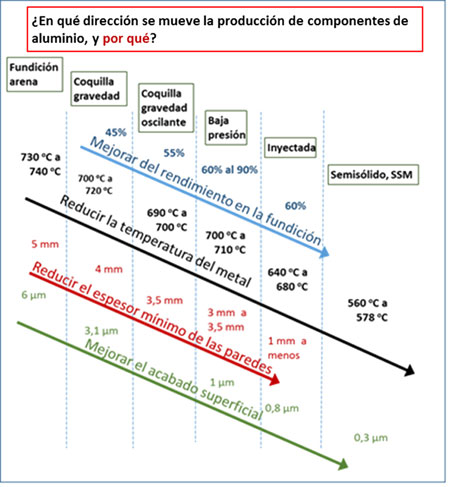
Estas tecnologías SSM se están desarrollando rápidamente, por lo que será fundamental para el sector poseer experiencia en las mismas. Los procesos SSM pueden causar un notable impacto en los nuevos diseños de componentes y su repercusión en las industrias productoras puede afectar a la capacidad competitiva de las mismas.
Se prevé un notable incremento del campo de aplicación de los componentes conformados en estado semisólido, especialmente en las industrias aeronáutica y del automóvil. Ello es debido a su mayor resistencia específica, que permite reducir el peso de los componentes y, en consecuencia, el consumo de combustible y la contaminación. Se considera que implantar estas tecnologías en la empresa mejorará su competitividad, ya que las técnicas SSM permiten obtener componentes de aluminio con mejores propiedades y a costes próximos a los de la fundición inyectada. Esta tecnología podrá competir en precio con los procesos de colada y forja y podrá abaratar la producción de piezas críticas. Además, los productos obtenidos tienen un buen acabado superficial con lo que se eliminan operaciones posteriores de mecanizado. En las figuras 2, 3, 4 y 5 se pueden observar algunos componentes de aluminio fabricados mediantes diferentes técnicas SSM, concretamente mediante Thixocasting (TC), Sub-Liquidus Casting (SLC), Semi-Solid Rheocasting (SSR) y New-Rheocasting (NRC).
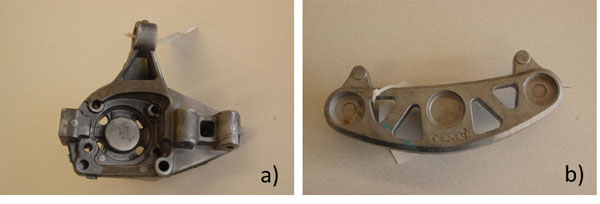
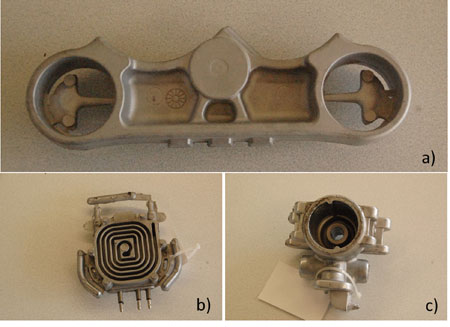
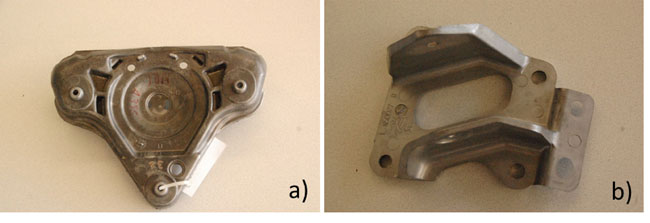
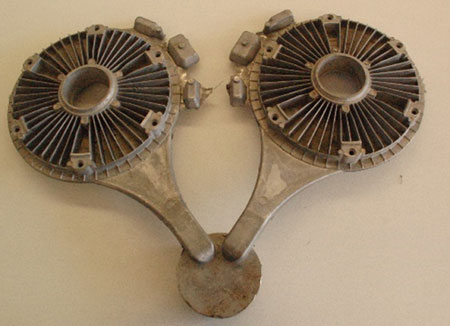
2. Ventajas de la conformación en estado semisólido
- Se reduce la porosidad hasta el 1%. Ello posibilita que las piezas obtenidas tengan una resistencia mecánica y un alargamiento mejor que las piezas coladas por gravedad. Al no tener gas atrapado también pueden tratarse térmicamente, duplicando el valor de la resistencia y límite elástico. Los valores dependen de la aleación y de la técnica SSM utilizada. En la Tabla 1 se comparan para la EN AC-46400 (AlSi9Cu3) las propiedades mecánicas conseguidas para componentes obtenidos mediante diferentes técnicas como son la fundición inyectada, el moldeo en coquilla por gravedad y una técnica SSM como es el proceso Semisolid Rheocasting (SSR).
Aleación y condición |
Límite elástico Rp0,2 /MPa |
Resistencia a tracción Rm /MPa |
Alargamiento A /% |
AlSi9Cu3 SSR |
118 |
226 |
2,5 |
AlSi9Cu3 SSR T6 |
319 |
358 |
1,2 |
AlSi9Cu3 inyectada |
110 |
180 |
< 1 |
AlSi9Cu3 inyectada T6 |
La norma no contempla este tratamiento |
||
AlSi9Cu3 coquilla |
100 |
170 |
1 |
AlSi9Cu3 coquilla T6 |
235 |
275 |
1,5 |
Tabla 1. Propiedades mecánicas de la aleación AlSi9Cu3 conformada mediante diferentes técnicas. Aleación y condición Límite elástico Rp0,2 /MPa Resistencia a tracción Rm /MPa Alargamiento A /% AlSi9Cu3 SSR 118 226 2,5 AlSi9Cu3 SSR T6 319 358 1,2 AlSi9Cu3 inyectada 110 180 < 1 AlSi9Cu3 inyectada T6 La norma no contempla este tratamiento AlSi9Cu3 coquilla 100 170 1 AlSi9Cu3 coquilla T6 235 275 1,5
- Los procesos SSM son también una alternativa al Squeeze Casting debido a que pueden producir piezas de paredes muy delgadas, hasta 2,5 mm, con un sustancial incremento de la productividad (se puede estimar un incremento del 100%). Debe destacarse que, en principio, muchas aleaciones de aluminio que se utilizan en fundición podrían utilizarse en procesos de conformación SSM.
- Los productos obtenidos tienen un buen acabado superficial con lo que se eliminan operaciones posteriores de mecanizado.
- Se eliminan operaciones como el impregnado.
- Menor temperatura de inyección: en la aleación EN AC-46000 esta temperatura se reduce en más de 100 °C, pasando de 720 a 590 °C.
- Más vida útil de los moldes, debido al menor choque térmico. Este incremento puede llegar a un 50%, basado en cálculos de fatiga térmica.
- Iguales o menores tiempos de ciclo, con una reducción que puede llegar al 25%, dependiendo del grosor de las paredes, lo que permite la producción de un mayor número de componentes/hora. Si bien se inyecta a menor velocidad, la menor temperatura del material inyectado requiere tiempos inferiores entre la inyección y la extracción de la pieza.
- Buenas tolerancias dimensionales.
- El menor tiempo de lubricación reduce la cantidad de lubricantes utilizados
- Menor ángulo de desmoldeo.
- Buen acabado final, con una rugosidad que puede llegar a valores de 0,3 µm.
- Buena resistencia a la corrosión: Los ensayos de corrosión en cámara de niebla salino-acética concluyen que las piezas tratadas con T6 presentan una resistencia a la corrosión más alta que con el tratamiento T5 y mucho mayor que las piezas brutas de colada.
- Posibilidad de anodizar los componentes. El anodizado de las piezas tratadas térmicamente proporciona al componente una capa superficial resistente al desgaste. Hasta ahora no se obtenían anodizados de calidad en piezas de aleación aluminio-silicio inyectadas, pero la microestructura obtenida mediante el proceso SSR y el tratamiento térmico, han permitido el anodizado duro con una capa de 3 µm a 5 µm. Con ello se obtiene una reducción significativa del coeficiente de fricción y se ha incrementa hasta en cinco veces la resistencia a corrosión en niebla salina.
- Posibilidad de utilizar aleaciones de segunda fusión.
3. Inconvenientes de la conformación en estado semisólido
Estas tecnologías también ofrecen, como contrapartida, algunos inconvenientes con respecto a la fundición inyectada clásica. Entre ellos cabe destacar:
- Una mayor inversión inicial, debido al coste de las estacionales adicionales. No se considera un sobrecoste la utilización de manipuladores o robots auxiliares, dados que estos sistemas son de aplicación también en la fundición a alta presión.
- Limitación a aleaciones con un cierto intervalo de solidificación. Las aleaciones eutécticas, o de composición próxima al eutéctico, no son adecuadas para estos procesos.
- Control más preciso de las condiciones de fabricación (control estricto de las temperaturas y de los tiempos de las diferentes etapas).
- Necesidad de optimizar las condiciones de llenado con el fin de evitar uniones frías y segregaciones de fase líquida. Ello pasa por la aplicación de programas de simulación para el diseño del molde y de las condiciones de llenado.
4. Situación de la tecnología SSM.
En estos momentos la implantación de estas técnicas es muy variada en las diferentes áreas geográficas, con dificultades en mercados como el europeo o el estadounidense. Las limitaciones para su implantación pasan desde el ya general Rechazo al Cambio, común a muchas innovaciones tecnológicas o metodológicas, hasta la existencia de algún fracaso histórico en Estados Unidos, fruto de una mala gestión del proyecto.
En Europa existen pocas empresas que hayan implantado sistemas SSM, siendo referente en este sentido la empresa italiana Stampal, perteneciente a la multinacional Euralcom Group. En Norteamérica esta implantación es algo desigual, con mayor presencia de estas técnicas en Canadá.
El sudeste asiático, en cambio, se caracteriza por una fuerte y creciente implantación de las más variadas técnicas. En China, el año 2013 se reportaron más de 400 empresas que utilizaban estas técnicas. En Japón las técnicas más utilizadas son la NRC, de la empresa UBE, y, fundamentalmente, el Honda Process, desarrollado por esta firma japonesa.
Para facilitar la introducción de estas tecnologías a escala industrial, nuestro país dispone de centros, reconocidos internacionalmente, con una amplia experiencia en procesos y productos industriales conformados en estado semi-sólido. Es decir, la industria puede contar con el soporte necesario para la selección de procesos, la puesta a punto de la producción en planta, el diseño de moldes, el control y optimización de procesos, el control de la integridad estructural de los productos, la optimización de los tratamientos térmicos y la aplicación de anodizados y otros tratamientos de superficie.
El Centro de Diseño de Aleaciones Ligeras (CDAL) de la Universitat Politècnica de Catalunya, ubicado en el Campus de Vilanova i la Geltrú (Barcelona), es pionero en la introducción de algunos de estos procesos en Europa, habiendo colaborado con varias empresas en la implantación de los mismos.