Sinterizado láser directo de polvo metálico para la fabricacióin de moldes
Jefe de Proyectos de Rapid Tooling & Materiales Fundación ASCAMM15/10/2003
Repaso de la técnica
La máquina está formada por el láser, el sistema de espejos focalizadores, dos cubetas (una de alimentación y una de crecimiento) con sus motores para desplazamiento vertical, una rasqueta niveladora con su motor para desplazamiento horizontal, el sistema generador y distribuidor de N2, el equipo de refrigeración, un sistema de extracción y purificación de gases, un ordenador de control y diversos sensores para control y seguridad del proceso.
El siguiente esquema resume las etapas necesarias para poder sinterizar una capa.
1 El haz láser es focalizado sobre la cubeta de crecimiento de pieza y va resiguiendo la geometría establecida por el programa de control, gracias al sistema de espejos que lo conducen. El polvo, al recibir la energía del láser, llega a la temperatura de sinterizado. El sinterizado en sí mismo tiene lugar entre las partículas de una misma capa pero además también con el material de la capa inmediatamente inferior, hecho que garantiza la máxima adherencia entre capas. Con la finalidad de compensar las tensiones introducidas en el rápido proceso de calentamiento-enfriamiento y la contracción del material, la exposición del láser se realiza según unas estrategias de alternancia continua.
2 La cubeta de crecimiento de capa desciende el valor del grueso de capa con el que se esté trabajando y la cubeta de alimentación de polvo desciende un valor superior.
3 La rasqueta niveladora se desplaza desde la cubeta de crecimiento hacia la cubeta de alimentación para nivelar la última capa sinterizada y recuperar el polvo que pudiera haber quedado sin sinterizar. Este polvo es depositado en la cubeta de alimentación.
4 La cubeta de alimentación asciende un valor determinado que garantiza suficiente material para la siguiente capa a sinterizar.
5 La rasqueta niveladora se desplaza desde la cubeta de alimentación hacia la cubeta de crecimiento para depositar la capa de polvo a sinterizar. El polvo sobrante cae en un recogedor para ser rehusado posteriormente.
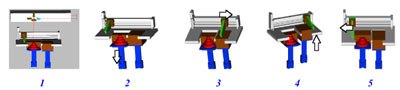
Para la realización del postizo sinterizado la máquina parte de un fichero consistente en las “rebanadas” de la pieza que se desea obtener. El fichero original de la pieza debe ser un fichero STL de alta calidad y resolución a gusto del usuario.
Objetivos del proyecto
Estudio de la desviación dimensional y rugosidad del proceso
El diseño de las probetas se realizó con el software I-Deas, el formato Iges fue traducido a formato STL mediante el software Magics y finalmente el programa de control de sinterizado se preparó con el software propio del fabricante de DMLS.
Las probetas se realizaron con polvo de acero de 20 _m de tamaño de partícula y el proceso llevó 17,3 horas de máquina, de las cuales 15,2 fueron de exposición de láser.
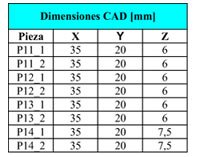
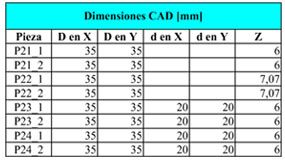
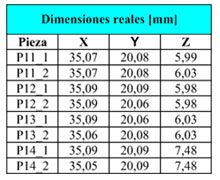
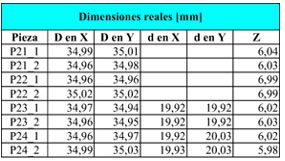
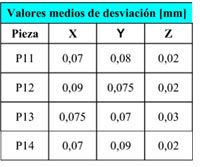
El análisis de los resultados permite afirmar que la desviación dimensional es excelente en comparación con otras tecnologías convencionales de fabricación. Esta afirmación es especialmente cierta para la desviación vertical —eje Z—, aunque para ella se aprecia una considerable desviación cuando se trata de superficies esféricas o quasiesféricas.
Además del control dimensional se ha realizado un control de rugosidad en planos:
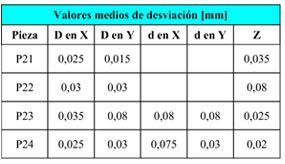
Si bien las conclusiones pueden parecer contraproducentes para fabricar moldes de inyección de plástico, debe mencionarse la excelente capacidad del material para ser pulido. Se recomienda el uso de un simple sistema de granallado para reducir la rugosidad y aumentar la facilidad de pulido.
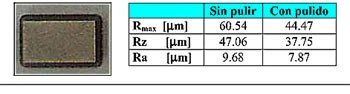
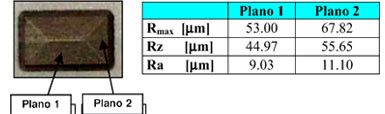
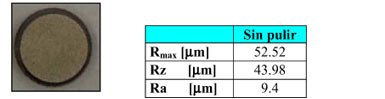
Estudio de la dureza del componente
Se trata de unos valores admisibles para las aplicaciones que suelen cubrir la mayoría de los casos de inyección de plástico. Debe advertirse que para moldes de gran producción y para casos de inyección de materiales muy abrasivos esta dureza es baja y se debe plantear entonces un recubrimiento o tratamiento en la superficie del inserto.
Haciendo la equivalencia numérica de dureza Brinell a dureza Rockwell puede resumirse y compararse la dureza en la superficie externa con aquellos valores para otros materiales comúnmente usados en inyección de plásticos:
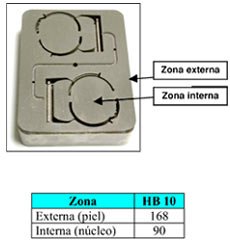
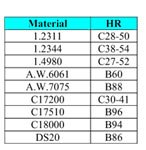
Aplicación de un caso concreto
Con la finalidad de cubrir las exigencias de acabado de superficie en la cara vista del logo y el plazo de fabricación se decidió fresar la mitad inyección y sinterizar la mitad expulsión.
El tiempo necesario para sinterizar el postizo de expulsión fue de 46 horas de máquina. Posteriormente el postizo fue separado del resto de plataforma mediante fresado de alta velocidad en seco. A continuación el postizo fue fresado en su cara superior para garantizar un buen ajuste de molde. No se aplicó ningún tipo de pulido ni tratamiento especial en la superficie.
Finalmente, se realizó el ensamblado de todos los elementos del molde, ajustes y retoques finales. El siguiente cuadro muestra los tiempos necesarios para este molde:
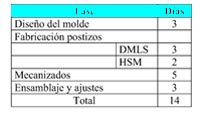
La siguiente fotografía muestra el molde abierto con los dos insertos:
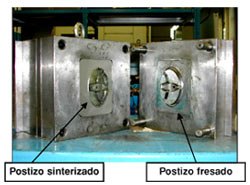
Las conclusiones que se han sacado de esta primera experiencia con un molde son las siguientes:
- Debe mejorarse el acabado superficial mediante, como mínimo, granallado de bola de acero.
- Debe reducirse el tiempo de programación de las estrategias de sinterizado mediante la exigencia de buena calidad en el fichero original Cad 3D de la pieza y los postizos a sinterizar.
- El DMLS se complementa perfectamente con el fresado de alta velocidad en cuanto a la fabricación del molde.
- El canal de refrigeración realizado no ha aportado mucha mejora en el tiempo de ciclo, desde el punto de vista de una serie corta de 500 piezas. El tiempo empleado en su diseño y vaciado de polvo sobrante no se justifica por la reducción del tiempo de ciclo.
- No haber sellado el circuito de refrigeración ha conllevado problemas de filtraje de agua en todo el postizo. Ello hubiera traído problemas en la calidad de las piezas inyectadas más adelante. Se debe infiltrar el canal de refrigeración con resina epoxi que evite el paso de agua o refrigerante al molde.
- El operario de taller ha considerado que el trabajo con el postizo mecanizado y con el postizo sinterizado es prácticamente el mismo.
Conclusiones y siguientes acciones a realizar
- Reducción del coste de los materiales
- Aumento de la velocidad de proceso
- Reducción de la rugosidad de la pieza sinterizada
- Aumento de la dureza de la superficie del postizo sinterizado
Los aspectos positivos que se han determinado son:
- Excelente comportamiento dimensional
- Grado de porosidad bajo
- Facilidad de mecanizado posterior
- Comodidad para repetitividad de postizos
- Buen comportamiento frente a recubrimientos y tratamientos que no requieran de altas temperaturas (Tmax < 600º C para base bronce y Tmax < 800º C para base acero)
Puesto que el proyecto no está todavía acabado, en las inmediatas pruebas se pretende evaluar la idoneidad de determinados recubrimientos y tratamiento térmicos.
Agradecimientos
- Ministerio de Ciencia y Tecnología.
- Electroless Hard Coat, S.A.
- Grupo TTC.
- Apolo Fijaciones y Herramientas, S.L.
- Centre Tecnològic de Manresa.
Referencias
[2] P.Engelmann, B.Dealey, “Maximizing performance using copper alloys”, Modern Plastics, May 1999.
[4] Jan W. Gunnink, “Rapid Tooling for Magnesium Die Casting”, TNO, Society of Manufacturing Engineers, 2002.
[3] EOS GmbH technical documentation.