Componentes involucrados en la formulación de caucho
Centro de Investigación en Química Aplicada Saltillo, Coahuila. México15/09/2003
- la selección del caucho,
- la selección y cantidades de los componentes,
- de la forma de realizar la mezcla,
- de los métodos de moldeo empleados y
- de la vulcanización
En una formulación se pueden utilizar entre 20 y 30 componentes, la variedad con la que se pueden cambiar sus propiedades al combinarlos es una de las características más notables de la tecnología del caucho. En general, una formulación está constituida por [1,2,3]: (1) base elastomérica, (2) agentes reforzantes, (3) ayudas de proceso, (4) antidegradantes y (5) sistema de vulcanización.
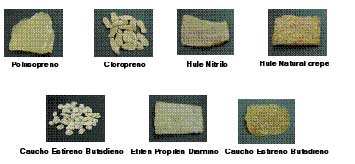
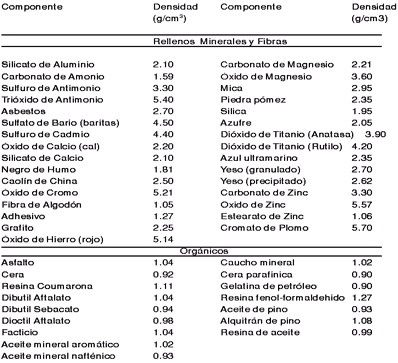
(1) Base Elastomérica
La selección del caucho está basada principalmente en su costo, facilidad de mezclado y propiedades. Por otro lado, hay diferentes grados de cauchos [4] y para su selección hay que tener en cuenta las condiciones a las cuales estará expuesto como pieza terminada, como por ejemplo si va a ser expuesto a solventes químicos, expuesto a temperaturas elevadas o intemperismo. En la figura 1 muestra algunos tipos de cauchos naturales y sintéticos que se usan en la industria hulera.
(2) Agentes Reforzantes
En la selección de un relleno [9,10] se toma en consideración: el tamaño de partícula, el área superficial, la estructura y la actividad superficial. En la figura 2 se presenta la clasificación de ciertos agentes reforzantes con respecto al tamaño de partícula y en la tabla 1 proporciona la densidad de los rellenos más.
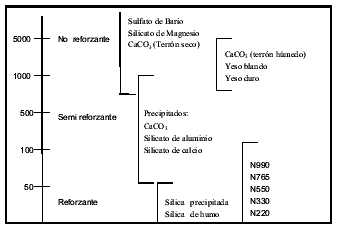
(3) Ayudas de Proceso
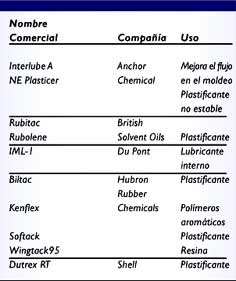
Peptizantes - son usados [12] principalmente en el caucho natural para ayudar a incrementar la eficiencia en la masticación del caucho e incrementar la velocidad del rompimiento molecular evitando la formación de radicales libres, se añaden al inicio del mezclado debido a que el azufre inhibe su acción, los cauchos sintéticos necesitan de altas concentraciones de peptizantes.
Los primeros peptizantes utilizados fueron los mercapturos aromáticos. Los complejos de quelatos como fierro, cobalto y manganeso son muy eficientes para reducir la viscosidad y se usan en concentraciones de 0,1 - 0,5 ppr. En la tabla 3 especifica algunos peptizantes comerciales.
Semipeptizantes - son llamados así debido a que ayudan en el rompimiento de las moléculas de los cauchos naturales y sintéticos, en algunos casos facilitan el mezclado y procesado. Estos se mezclan generalmente con componentes orgánicos sulfurados y aceites minerales con densidades de 0,82 - 1,23 g/cm3. Generalmente son líquidos aunque también se les encuentra en forma de polvo. Se usan en concentraciones de 1 - 3 ppr y en ocasiones hasta 5 ppr para piezas de esponja.
Ablandadores - se aplican en pequeñas cantidades para facilitar la incorporación de los rellenos, ablandar la pasta de caucho durante la vulcanización y así facilitar el procesamiento. Los principales ablandadores se obtienen del:
- Petróleo (aceite nafténico, aromático, cera, asfalto)
- Pino (alquitrán de pino, resina)
- Alquitrán de hulla (aceite de alquitrán de hulla, resina)
- Aceites y grasas naturales (aceites vegetales o fundidos, ácidos grasos)
- Compuestos orgánicos sintéticos (plastificantes del tipo éster, polímeros líquidos, entre componentes sintéticos)
La selección de un ablandador puede ser por: (a) la estructura química "polaridad y aromaticidad", la cual determina el grado de compatibilidad con el caucho; (b) el peso molecular, controla la viscosidad del material y (c) la reactividad química, la cual cubre el efecto catalítico en la oxidación.
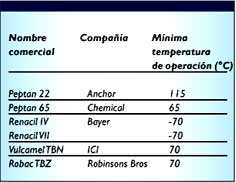
También se usan en el sistema de vulcanización con peróxido, proporcionan pegajosidad durante el procesado y polimeriza durante el curado, contribuye a una alta rigidez y aceleración durante la etapa de curado, participando en la reacción de entrecruzamiento.
Ácidos grasos y sales - se usan en pequeñas cantidades como parte del sistema de vulcanización con azufre, el ácido esteárico también actúa como un plastificante, ayuda a la dispersión del negro de humo y otros rellenos, además reduce la tendencia de adhesión a los rodillos. Bajo las mismas circunstancias el estearato de zinc se usa en lugar del ácido esteárico y óxido de zinc. Algunas veces son usados como ayudas de proceso el laureato de zinc y las sales de zinc de alto peso molecular.
Aceites y extendedores - en contraste con los peptizantes, los aceites de petróleo actúan mejor de forma física que de manera química, su efecto no depende de la temperatura de mezclado, se usan en intervalos de concentración de 5 - 10 ppr. Además actúan como un plastificante durante el procesado causando una reducción en la viscosidad y facilitando la incorporación del relleno.
Lubricantes - los aceites de petróleo además de aplicarse como lubricantes se usan como extendedores para disminuir el costo de la pieza. Estos pueden ser incorporados durante el mezclado en los cauchos como el caso del SBR y EPDM, en los cuales se añaden en pequeñas cantidades junto con el relleno, logrando un ablandamiento durante la vulcanización. Estos lubricantes se clasifican en:
- Aceites Aromáticos: son buenos para ayudar a la dispersión del negro de humo durante el mezclado, presentan un efecto de decoloración en la pieza, además presentan un efecto adverso en la resistencia al calor y radiación ultravioleta.
- Aceites Parafínicos: son menos eficientes como ayudas de proceso, pero tienen mejor efecto durante el envejecimiento, en la decoloración o la estabilidad al calor. Su desempeño a bajas temperaturas es mejor que los aromáticos.
- Aceites Nafténicos: su efecto se sitúa entre los aceites aromáticos y parafínicos.
Facticio - durante el mezclado controlan el nervio del caucho, logran una mejor dispersión e incorporación de los componentes en forma de polvo, se usan como ayudas de proceso en la extrusión de los cauchos naturales y sintéticos ya que proporcionan un filamento de buena calidad y previenen la deformación durante la vulcanización. Su rango de aplicación es de 5 - 30 ppr. A altas concentraciones se utilizan en piezas muy blandas como por ejemplo en: los rodillos de la impresora, para ayudar a la incorporación del plastificante líquido y además se utilizan para reducir la posibilidad de ser extraídos en la pasta de caucho. Existen muchos tipos de facticios como los del tipo oscuros y dorados, se clasifican en primer, segundo y tercer grado.
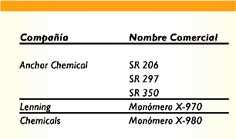
Resina Coumarona - es usada como plastificante en cauchos sintéticos para adherirse a los rodillos. Su apariencia varía desde líquidos viscosos hasta sólidos, en el caso de los líquidos varían en el color desde café oscuro a crema y en los sólidos se caracterizan por el punto de fusión de 65 a 110°C.
Resinas de Estireno - contienen un 85 por ciento de estireno, se usan como ayudas de proceso para termoplásticos debido a su acción reforzante, particularmente en piezas que necesitan tener una alta dureza. Para asegurar una buena dispersión de la resina, la temperatura de mezclado debe ser mayor a 95°C. En la tabla 5 se mencionan algunos ejemplos.
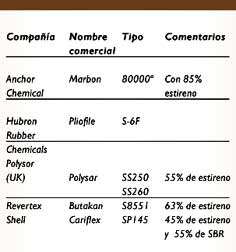
(4) Antidegradantes
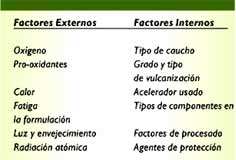
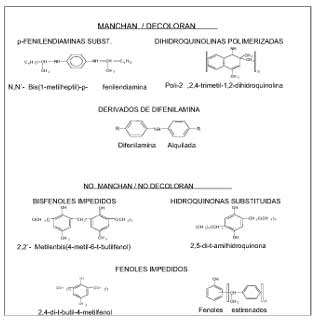
Los antioxidantes se dividen en primarios y secundarios. La función de los primarios es atrapar los radicales libres antes de que estos reaccionen con el caucho, se clasifican en aminas secundarias y fenoles substituídos con hidrógenos muy reactivos. En la figura 3 se presentan las diferentes estructuras químicas de los antioxidantes primarios.
Los antioxidantes fenólicos se emplean en piezas blancas en donde las aminas no son las adecuadas debido a la decoloración y manchado que estás ocasionan en el producto. Los fenólicos también se aplican en piezas de color, pero la mancha es significante comparada con la obtenida por las aminas. Los fenoles impedidos son más efectivos sin embargo también son más caros. La mezcla de mercaptoimidazoles y ditiopropionatos presenta un efecto sinergístico.
Antiozonantes - se utilizan [16] para evitar una degradación en la superficie del caucho al exponerse al ozono. Para evitar esto es necesario formar una barrera en la superficie de la pieza. El ozono se encuentra presente en la atmósfera formándose por la acción de la luz solar con las partículas de contaminación presentes en el medio ambiente.
El mecanismo de degradación inicia por la reacción del ozono con los dobles enlaces del caucho para formar ozonidas, las cuales se descomponen al romper los dobles enlaces y bajo esfuerzo aparece la fractura, siendo una reacción repetitiva. Si el caucho no se encuentra bajo esfuerzo, los dobles enlaces son capaces de recombinarse, presentan la factura en forma de escarcha. Los factores que afectan la degradación son:
1. La completa dispersión de los ingredientes, la pobre dispersión acelera este fenómeno
2. La presencia de material extraño, las impurezas metálicas o polvo aceleran la fractura de una pieza terminada
3.La historia térmica del material antes del moldeo, materia prima envejecida antes del moldeo reduce la fractura.
Ceras - las ceras [17,18] protegen al caucho del deterioro ambiental que ocasiona un envejecimiento prematuro, formando una película en la superficie del caucho que lo protege del ataque por el ozono, presentando un efecto barrera, que depende de la solubilidad y temperatura. Existen dos tipos de ceras [19]: la cera parafínica y la microcristalina; esta última tiene menos tendencia a ser visible en la superficie. Por lo general se recomienda mezclar las dos para una máxima protección en un amplio rango de temperaturas de exposición. Su ventaja es que son de bajo costo, no manchan y no afectan la vulcanización.
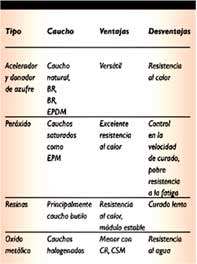
5. Sistema de vulcanización
Con la vulcanización se incrementa el esfuerzo tensil, el módulo, la dureza, la resistencia a la abrasión y por consiguiente disminuye la elongación, compresión permanente y la solubilidad. La resistencia a la tensión y al rasgado muestra un valor óptimo, debido a los cambios producidos por el grado de entrecruzamiento.
Con un entrecruzamiento excesivo se obtienen productos rígidos, con un entrecruzamiento normal se mejora la propiedad de resistencia a la tensión y al rasgado, además de la fatiga. Un entrecruzamiento pobre proporciona una degradación oxidativa y térmica con una baja compresión permanente. En la tabla 8 se describen las propiedades del caucho crudo y vulcanizado.
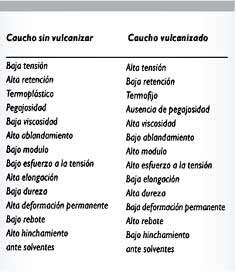
Es el agente de vulcanización [21] más ampliamente usado en los cauchos, cuya estructura está conformada por dobles ligaduras como en el caso de los cauchos: natural, estireno-butadieno (SBR), polibutadieno, nitrilo, policloropreno y polisopreno. Es insoluble en el caucho por lo que migra a la superficie antes de la vulcanización, es de bajo costo y baja toxicidad, compatible con otros aditivos.
Un sistema de vulcanización típico esta compuesto por el azufre, óxido metálico como el oxido de zinc, ácido graso (para solubilizar el óxido metálico) y uno o más aceleradores orgánicos. Se usa en una concentración de 1 a 3 ppr, los métodos para la vulcanización pueden ser:
- Azufre solo
- Azufre convencional y aceleradores
- Baja cantidad de azufre y aceleradores
- Sistema donador de azufre
Activadores - ayudan a incrementar la velocidad de vulcanización reaccionando primero con los aceleradores, después activan al azufre para iniciar la vulcanización, estos pueden ser orgánicos, inorgánicos y metálicos. Los activadores más comunes son la combinación de óxido de zinc en concentraciones de 2 - 4 ppr y el ácido esteárico que puede variar desde 1 - 3 ppr; éste último actúa como un lubricante para reducir la viscosidad durante el mezclado. Se han usado otros óxidos metálicos como el de plomo, cadmio y algunos ácidos grasos (por ejemplo el ácido láurico y el propiónico) para propósitos específicos. En la figura 5 se observa el efecto de los activadores sobre la velocidad de curado o entrecruzamiento, la cuál se refleja en el aumento del torque.
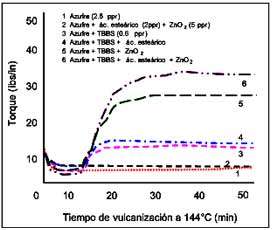
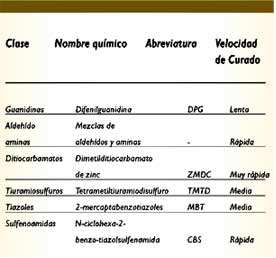
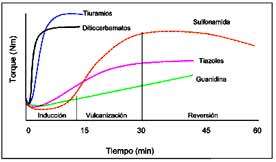
Además estas características varían con el tipo de acelerador o la combinación entre ellos, por ejemplo con el azufre, el tipo de caucho y los componentes involucrados en la formulación.
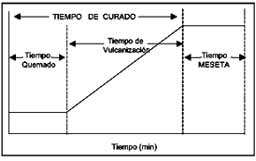
Existen tres clases de retardadores: la primera corresponde a los ácidos orgánicos como el ácido salicílico, maléico y el anhídrido ftálico; su uso no es muy frecuente y se aplican en dosis de 2 ppr. La segunda clase es la ciclohexiltioftalimida (Santogard PVI o CTP) la cuál no afecta las propiedades durante la vulcanización y no causan manchado o porosidad en el producto; una de sus ventajas es que se pueden usar en una gran variedad de cauchos. En la figura 8 se muestra el efecto de este tipo de retardador. La tercera clase es la sulfonamida.
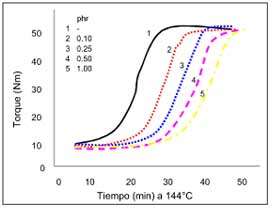
Los cauchos que no contienen dobles ligaduras en su estructura molecular no pueden ser vulcanizados con azufre, requieren de un agente entrecruzante alterno capaz de reaccionar con una ligadura, para este tipo de cauchos se puede usar los peróxidos. Los agentes del tipo óxidos metálicos o compuestos difuncionales son usados en casos especiales.
Peróxidos - son los agentes [26,27] más usados después del azufre por su habilidad para:
- El entrecruzamiento con una variedad de cauchos insaturados y saturados
- Proporcionar estabilidad térmica en el enlace carbono-carbono, formado durante el entrecruzamiento
Al usar peróxidos, los compuestos presentan mejores propiedades en el envejecimiento térmico, baja compresión permanente y buena flexibilidad a bajas temperaturas. Se deben tomar medidas de precaución durante su manejo y almacenamiento ya que son sustancias de riesgo. Comparadas con otras materias primas, producen un olor desagradable durante la vulcanización y reaccionan con otros componentes, por lo que se restringe el uso de antioxidantes en este sistema.
No es recomendable usarlos en presencia de oxígeno, como en el caso de la vulcanización continua en aire caliente, la razón es que el radical de transferencia de la cadena del caucho se oxida, formándose hidroperóxidos responsables del inicio de la degradación.
La velocidad de curado del peróxido se controla por la temperatura y por el tipo de peróxidos, en las tablas 10 y 11 se especifican los cauchos que pueden o no ser entrecruzados con este agente.
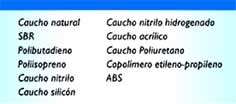
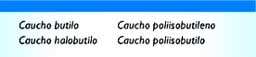
Las sales inorgánicas de cobre y magnesio pueden ocasionar fragilidad en los productos de caucho. El plomo puede reaccionar con el pigmento durante el curado y se obtienen productos blancos o de color; esto se elimina al usar solamente un 0,002% de plomo.
Entrecruzamiento con aminas - los cauchos fluoroeslastomeros (FKM) y los poliacrilatos (ACM) no son vulcanizados con azufre, debido a que contienen una pequeña cantidad de monómero reactivo que reacciona con las aminas. El azufre puede ser añadido solamente como un retardador de la vulcanización.
Compuestos difuncionales - ciertos componentes bifuncionales son usados para llevar a cabo el entrecruzamiento formando puentes entre las cadenas del caucho. Los componentes de este tipo son: p-quinona dioxima, la cual es oxidada a p-dinitrisobenzeno para formar el puente con los dobles enlaces del caucho, se usa en el caucho butilo; la resina epoxi para el caucho nitrilo y la resina fenólica también se aplica para el caucho butilo y EPDM.
Referencias
[2] Tecnología en Elastómeros, Grupo Hulero Mexicano A. C.
[3] Frederick R. Eirich, Science and Technology of Rubber, Academic Express New York San Francisco London, 1978
[4] J. R. Beatly and M. L. Studebaker, Rubber Age, 1975, 107, 8, 20 – 38
[5] Gerard Kraus, Reinforcement of Elastomers, Interscience Publishers, 1965, 491 – 511
[6] Bernhard Schwaiger and Anke Blume, Rubber World, 2000, 222, 1, 32 – 38
[7] Dieter Berkemeier, Walter Haeder and Maik Rinker, Rubber World, 2001, 224, 4, 34 - 39
[8] Larry R. Evans and J. M. Huber, Rubber World, 2001, 224, 1, 18 - 21
[9] C. M. Blow, Rubber Technology and Manufacture, Butterworths London, 1971
[10] Gary R. Hamed, Rubber Chemical and Technology, 2000, 73, 3, 524 - 533
[11] J. R. Beatty and M. L. Studebaker, Rubber Age, 1975, 107, 9, 39 – 44
[12] Lars C. Larsen, Rubber World, 1997, 217, 3, 22 – 24
[13] Peter A Ciullo and Norman Hewitt, The Rubber Formulary, Noyes Publications Norwich New York, 1999
[14] Robert W. Layer and Robert P. Lattimer, Rubber Chemical and Technology, 1990, 63, 3, 425 - 450
[15] S. A. Pushpa, P. Goonetilleke and N. C. Billingham, Rubber Chemistry and Technology, 1996, 69, 5, 885 - 896
[16] Robert F. Ohm and R. T. Vanderbilt Co, Rubber World, 1993, 208, 5, 18 – 22
[17] H. Michalak, Rubber Age, 1974, 106, 6, 40 – 41
[18] Sung Seen Cahi, J. Appl. Polym. Scie., 1999, 73, 13, 2587 - 2593
[19] P. I. Dimauro, H. L. París and M. A. Fath, Rubber Chemistry and Technology, 1979, 52, 2, 973 - 985
[20] Michael A. Fath, Rubber World, 1993, 209, 1, 22 – 25
[21] E. Koczorawska, B. Jurkowsko and B. Jurkowski, J. Appl. Polym. Sci., 1998, 69, 8, 1531 – 1536
[22] Barlow Fred W., Rubber Compounding: Principles, Materials and Techniques, Marcel Dekker Inc., 1988
[23] Herbert Morawetz and Herman F. Mark, Rubber Chemistry and Technology, 2000, 73, 3, 405 - 426
[24] J. R. Beattly and M. L. Studebaker, Rubber Age, 1976, 108, 12, 37 – 36
[25] Michael A. Fath, Rubber World, 1993, 209, 3, 17 – 20
[26] Arthur L. Barbour, Elastomerics, 1978, 110, 6, 23 - 27
[27] Peter R. Dluzneski, Rubber Chemistry and Technology, 2001, 74, 3, 451 - 492