La revolución de la multifunción
13 de diciembre de 2011
‘Done in one’ de Mazak
Mazak denomina a sus máquinas multitarea ‘Integrex’, denominación que se ha convertido en un estándar de mercado. Dentro del rango de máquinas Mazak, además de las Integrex también se pueden encontrar las Variaxis, las cuales, mediante la integración de operaciones de torneado, fresado y la posibilidad de atacar a una pieza desde 5 caras permiten terminar piezas complejas en una atada. Desde Intermaher, distribuidor en exclusiva de Mazak en España desde 1975, afirman que estos equipos “actúan como una minifábrica, donde entra la materia prima y sale la pieza terminada”. A esto hay que sumarle ventajas como “la mejora de plazos de entrega, reducción de stock, utillajes mucho más simples, menos tiempos improductivos, mejor utilización del personal, mejor aprovechamiento del espacio, mayor calidad en las piezas y capacidad para fabricar piezas más complejas y de más valor”.
La gama Integrex, y su consigna ‘done in one’ (‘hecho en uno’), últimamente ha aumentado la familia con dos novedades que se presentaron en la EMO con los modelos Integrex j200 e Integrex i200S. El Integrex i200S, con un diseño futurista completamente renovado obra del diseñador japonés Ken Okuyama, dispone de 2 platos y un eje Y de 250 milímetros, voltea 658 milímetros con una longitud de corte de 1.011 milímetros y aúna en una sola máquina a un torno con dos cabezales y a un centro de mecanizado de 5 ejes. La serie Integrex ‘i’ permite otras opciones como son máquina con doble cabezal para mecanizar piezas con 2 fases de mecanizado de forma automática, torre inferior para mejorar los tiempos de ciclo, movimiento continuo del giro del cabezal para mecanizados con 5 ejes continuos, etc. y dispone de más potencia en sus accionamientos.
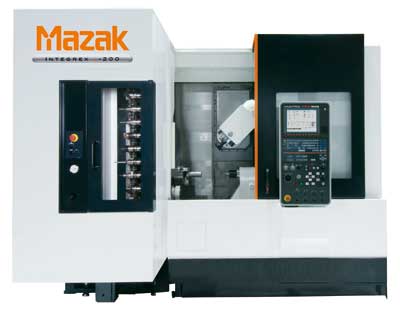
En cuanto al Integrex j200, Intermaher lo define como el ‘portal de entrada’ a los equipos multitarea, y lo presenta así por sus características muy útiles para el cliente y unas prestaciones limitadas con relación a la serie i200. Como consecuencia, su precio es más ajustado y es una solución muy válida para quien precisa algo más que un torno con herramientas motorizadas. Su control Matrix Nexus permite programar el mecanizado a realizar a pie de máquina, con su lenguaje tipo CAM Mazatrol, muy apreciado por todos sus usuarios. Su diámetro máximo de corte y su longitud máxima de mecanizado son de 500 milímetros, con un eje Y de 200 milímetros.
Cabezal de torneado y fresado y torreta DirectDrive de DMG
Con su potente cabezal de torneado y fresado, torreta inferior DirectDrive y tecnología de control de 2 canales, la nueva CTX beta TC 4A de DMG destaca por su combinación del potente cabezal de torneado y fresado y la torreta inferior como base productiva para el mecanizado de 6 caras con hasta 5 ejes simultáneos en una máquina. Según Harry Junger, director general de Gildemeister Drehmaschinen GmbH: “La CTX beta 1250 TC 4A marca el nuevo modelo superior en el sector de piezas medianas en el rango de diámetro de hasta 390 milímetros y para longitudes de torneado hasta 1.250”. El nuevo desarrollo se diferencia de la CTX beta 1250 TC con eje B en mayor parte debido a la adicional torreta inferior. Harry Junger declara: “ambas herramientas montadas en las torretas trabajan de forma autónoma y sin restricciones” Esto hace posible trabajar en un husillo de cuatro ejes con dos herramientas o trabajar en ambos lados en paralelo (en la versión con contrahusillo).
El director general de Gildemeister Drehmaschinen GmbH considera que el grado general de productividad se ha aumentado hasta en un 50% en el nuevo CTX beta 1250 TC 4A comparado a la versión con eje B. Y añade: “Si el programa de trabajo de una pieza necesita operaciones de torneado, taladrado profundo, fresado con engranaje, torneado fuera de centros, torneado/fresado, desbaste a 4 ejes, fresado de alto rendimiento, fresado y torneado fuera de centros o incluso fresado con 5 ejes simultáneos y los clientes desean completar estas tareas de corte de metal con la máxima flexibilidad en una máquina, la CTX beta 1250 TC 4A es la primera opción para el futuro”.
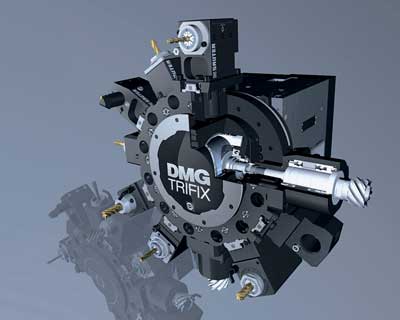
Dentro del proceso, la CTX beta 1250 TC 4A trabaja por un lado con un eje B que es basculable por +/-100° con motor husillo de 12,000 rpm, y por otro lado con la torreta inferior VDI 40-DirectDrive con 12 puestos motorizados para velocidades de hasta 10,000 rpm. La propia torreta tiene adicionalmente un eje Y (±40 mm) y todos los puestos de herramienta incluso en la versión estándar están equipados con el Inteface de precisión DMG Trifix para reducidos tiempos de preparación y aumento en la precisión de herramienta así como en estabilidad.
Para el husillo de torneado y fresado, la versión standard de la CTX beta 1250 TC 4A tiene un almacén de disco de 24 posiciones. Sin embargo, el sistema de disponibilidad de herramientas se puede incrementar con una adaptación de un almacén de cadena de 80 posiciones.
El nuevo control ShopTurn 3G garantiza el máximo rendimiento desde el diseño hasta el mecanizado completo. Una de las novedades es la programación multicanal que posibilita al usuario seleccionar libremente el programa DIN o WOP. Así es posible una programación gráfica en 3D en el taller directamente en la máquina, con simulación de procesos y ciclos de fácil uso gracias a un interface ShopTurn, como también una programación que optimiza los tiempos de los contornos complejos y la integración de ciclos personalizados, módulos de programas generados exteriormente o con tecnologías auxiliares a través de un código DIN, por el que los ciclos ShopTurn pueden incluso combinarse flexiblemente con funciones DIN para ShopTurn 3G. Además, el control ofrece al usuario imágenes para una rápida preparación, un interface Ethernet para rápidos intercambios de datos, una fácil solución de posibles errores con señalizaciones de diagnósticos y funciones para el mantenimiento.
Danobat: multifunción ‘a lo grande’
La cooperativa elgoibarresa Danobat, integrada en Danobat Group y en la Corporación Mondragón, fabricó el pasado año uno de los mayores tornos verticales construidos recientemente en España para un exigente cliente alemán del sector energético. Este tipo de máquinas responde a uno de los principales retos estratégicos de la empresa: desarrollar máquinas de grandes dimensiones y tecnológicamente avanzadas, dando respuesta así a la creciente demanda de mecanizado de grandes componentes, en las que se pueden realizar todas las operaciones que requiera cada pieza, incluyendo el torneado, fresado, roscado, taladrado, rectificado, tallado, medición y otras operaciones requeridas por clientes específicos.
En concreto, el torno vertical de grandes dimensiones VTC-6000 es una máquina multifunción que ofrece una elevada versatilidad y productividad. Los principales elementos estructurales son de hierro fundido y estabilizado, evitando las vibraciones y garantizando al máximo la rigidez y estabilidad de la máquina, que tiene un peso total de 180.000 kilos.
Este centro de torneado puede admitir piezas hasta 100 toneladas de peso, 6.000 milímetros de diámetro y 4.000 de altura. Gracias al desplazamiento vertical del travesaño se pueden mecanizar piezas tanto de baja como de gran altura, con la máxima calidad y precisión, en cualquier posición en que se encuentre el travesaño.
La máquina, equipada con cabezal hidrostático de una potencia de 140 kW y un par de 170.000 Nm, monta en el travesaño, dos RAM motorizados, con una potencia de 37 kW al 100% y con una sección cada uno de 300 milímetros. Los ejes X y Z (4), todos ellos de deslizamiento sobre guías hidrostáticas, consiguen precisiones de posicionamiento de 0,01 milímetros y unas precisiones de repetibilidad de 0,006 milímetros.
La máquina incorpora además doble eje C así como dos almacenes de herramientas, uno para cada RAM, con múltiples puestos para las herramientas de tornear, taladrar, roscar, fresar, muelas de rectificar, así como para los cabezales rectos y angulares que requieren dichas herramientas. Danobat ha prestado una gran atención en el diseño ecológico de la máquina, minimizando al máximo los consumos de aceite y haciendo especial hincapié en el ahorro de energía, por medio del sistema programable de ‘sleep mode’.
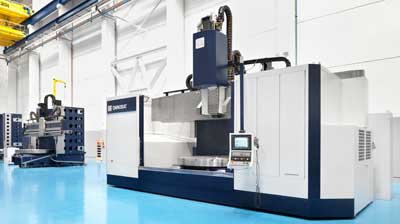
Los ‘Multus’ de Okuma
En Okuma, marca japonesa representada por Maqcenter, hablar de equipos multitarea es hablar de la gama Multus. Por ejemplo, el Okuma Multus B400 trabaja con hasta siete ejes, y consigue mecanizados de alta precisión gracias al concepto TFC, que permite un control de las posibles desviaciones debidas al efecto térmico. Equipado con el PC-CNC Okuma OSP-P200 con LCD de 15” y panel táctil, tiene como punto fuerte la protección anticolisión CAS. Con una capacidad de longitud de torneado de aproximadamente 1.500 milímetros, permite mecanizar piezas de tamaño medio, utiliza un husillo sobredimensionado de 80 milímetros de diámetro y 22 kW, con un giro de hasta 3.800 rpm en su configuración estándar. El husillo de fresado tiene 14 kW, mientras que la bancada y las telescópicas están moldeadas en frío, y poseen una estructura muy rígida que soporta una capacidad de arranque de viruta en torneado de 4 milímetros de profundidad por pasada y una capacidad de fresado final de 450 centímetros cuadrados por metro.
Por su parte, el torno multifunción Multus B750, de grandes dimensiones, está especialmente concebido por su capacidad de trabajo en el sector de la aeronáutica, en la fabricación de componentes de motores de turbina, estructuras de fuselaje y tren de aterrizaje. Sus potentes motores, tanto de husillo como de movimiento de ejes permiten una gran capacidad para remover elevadas cantidades de material logrando tiempos de fabricación muy reducidos. Además permite optimizar coste y tiempo de producción gracias al sistema anticolisión y ‘thermo friendly’ asegurando una alta precisión, incluso en las aplicaciones más complejas. Combina la capacidad de fresado de los centros horizontales MA600 y la de torneado de los tornos LB45II. Con capacidad de cinco ejes, facilita flexibilidad a la hora de trabajar y así hacer frente a las más duras condiciones y superficies complejas, manteniendo tolerancias muy pequeñas.
Okuma completa su gama de tornos multitarea con la más pequeña de la serie, el modelo Multus B200W trabaja con plato de 6” y, opcionalmente, con 8” con una distancia entre centros de 550 mm (versión con/sin contrapunto) y de 750 mm (versión de subhusillo). Utiliza un husillo sobredimensionado de 62 mm de diámetro y 11 kW, girando hasta 6.000 rpm en su configuración estándar. Las aplicaciones se adaptan a cualquier mecanizado. El husillo de fresado tiene motor de 11 kW y 12.000 rpm como estándar y, opcionalmente, 9 kW y 20.000 rpm. Consigue mecanizados de alta precisión gracias al concepto TFC que permite un control de las posibles desviaciones debido al efecto térmico. Como el resto de la serie equipa el control Okuma OSP-P200L con LCD de 15” y el sistema anticolisión CAS.
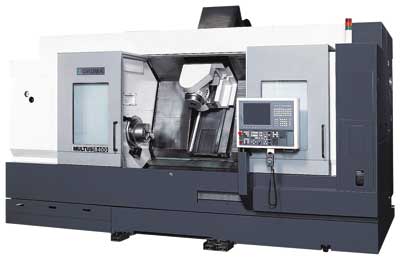
Matsuura y Muratec de Maquinser, otras dos sugerencias en multifunción
La marca japonesa Matsuura, distribuida por Maquinser, cubre la demanda de equipos multitarea con los centros de mecanizado de 5 ejes de la gama Cublex, formada por los modelos Cublex 25, 35, 42 y 63.
El resultado final es una máquina más compacta que las tradicionales máquinas multitarea, con mayor capacidad de fresado, adecuada en torneado y que ofrece la versatilidad de dotar el cambio de palé estándar de diferentes soluciones mulitpalé y hasta 520 herramientas. La opción multipalé es fundamental para poder tener diferentes preparaciones colocadas en máquina ofreciendo mayores posibilidades de producción flexible en series pequeñas exigidas en el competitivo mercado actual. Obtiene además un incremento notable de producción al no tener necesidad de parar la máquina para realizar nuevas preparaciones.
La Cublex 63 permite mecanizar una pieza de 630 milímetros de diámetro por 450 de altura y con un peso máximo de 450 kilos, sobre un palé de 500 milímetros de diámetro. La máquina alcanza precisiones muy elevadas en circularidad fresando (1,94 µm) y torneando (1,35 µm), siendo la precisión cilíndrica de 1,24 µm en 300 milímetros de longitud.
La máquina incorpora en su dotación estándar del nuevo sistema Thermal Meister de compensación térmica, Handy Mann II para mantenimiento y rápido set up y función de chequeo de un correcto equilibrado de la pieza.
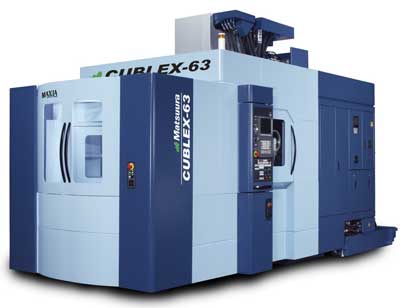
La nueva serie Muratec MT supone una paso adelante al respecto de las máquinas multifunción con posibilidad de mecanizar en la misma máquina piezas en barra y con cargador de piezas por robot gantry. O también ambas a la vez. La máquina equipa dos cabezales de la misma potencia y puede combinar la opción de 1 torre superior y 1 torre inferior o bien 2 torres superiores y 1 torre inferior. Todas ellas con equipadas con eje Y.
En su modo estándar la máquina puede incorporar un cargador de barras para cabezal izquierdo, y un cargador/descargador de piezas cortadas en la parte derecha de la máquina. Además de un recogedor de piezas por bandeja. Convirtiéndola en una máquina multifunción perfecta para la producción flexible.
La nueva serie MT 200 viene a aumentar la versatilidad de la serie MT. Todas ellas equipadas con los controles CNC Fanuc serie 30i de última generación.
Centros MPS y Mill de Chiron
Los centros de fabricación MPS de Chiron, marca comercializada por Maquinaria Eurotec, son idóneos para el mecanizado completo de perfiles por los cuatro lados, incluyendo operaciones de desbastado, acabado, fresado circular, taladrado, abocardado, escariado, roscado y aserrado. Este centro de mecanizado ofrece la posibilidad de la fabricación de variantes, reduce los desarrollos internos del proceso operacional, ahorra horas de operario y aumenta enormemente el volumen de producción. Requiere muy poco personal. Proporciona ventajas como lotes con hasta 800 piezas a trabajar por hora, volumen de producción 5 veces más elevado, eficiencia elevada debido a los procesos de producción mejorados son los resultados de usuarios altamente satisfechos con los centros de mecanizado MPS Chiron. Los perfiles se toman en la estación de carga. A través de la unidad de avance se alimenta automáticamente el material para mecanizar. Gracias al mecanizado total y longitudinal en un amarre está garantizada la máxima precisión. La elevada productividad de este proceso permite costes por pieza más reducidos. La producción automática de piezas puede trabajar desde piezas pequeñas hasta una pieza acabada de 11 metros de largo, con velocidades de giro del husillo hasta 30.000 rpm y aceleraciones de los ejes de hasta 2 G. Ofrece velocidades de marcha rápida hasta 75 metros por minuto y cambios de herramienta en tan sólo 0,5 segundos.
El centro de mecanizado multifuncional Chiron Mill 800 taladra, mandrina, fresa y tornea a partir de barra de cualquier longitud en 6 caras en como máximo dos sujeciones, incluso en piezas complejas, cosa que aumenta la precisión, ahorra tiempo y reduce los costes por pieza. La serie Mill ofrece grandes recorridos de desplazamiento y una elevada capacidad de fresado para el mecanizado completo de cantidades medianas y pequeñas. El centro Mill 800 está equipado con un cabezal giratorio CN, con un carro CN con volteador de piezas así como con un paquete de torneado potente. Además de los tres ejes X, Y y Z, el modelo Mill 800 ofrece un cabezal giratorio CN robusto como 4º eje CN. Éste se puede girar horizontalmente con progresión continua en +/- 100º a través del eje X. Un giro de 90º se realiza en 0,5 segundos. En el interior del cabezal giratorio se encuentra un husillo refrigerado por agua, térmicamente estable y de 34 kW con velocidades de giro de hasta 20.000 rpm. Del avance de la barra se encarga un carro CN (6º eje) con aparato inversor sobrepuesto (7º eje) y bloque de sujeción así como un contrapunto para apoyo. Con el fin de mecanizar la parte posterior (6º lado), la pieza a trabajar se extrae poco a poco del husillo, se sujeta en la mordaza, se corta con una fresa de disco de la barra y, con la ayuda del aparato inversor y del carro, se lleva a la posición de descarga. Los recorridos de los ejes X, Y y Z son de 800 x 480 x 630/715 milímetros, con unas marchas rápidas de 60 metros por minuto. La capacidad de fresado (en St 60) es de hasta 600 centímetros cúbicos. El tiempo de cambio de herramienta es de 1,5 segundos y el tiempo aproximado de viruta a viruta es de 2,9 segundos. Acepta barras de hasta 100 milímetros de diámetro. El almacén de herramientas permite hasta 180 herramientas para diferentes operaciones de mecanizado.
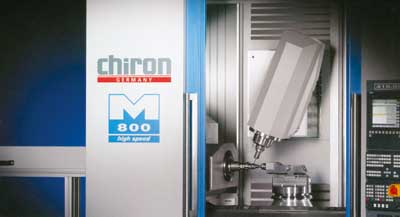
Serie MT de Hermle: torneado y fresado simultáneo en 5 ejes
Fresado y torneado en una sujeción. Los modelos C 42 U MT dynamic, C 50 U MT dynamic y C 60 U MT dynamic de la serie MT (Mill/Turn) de Hermle, marca comercializada por Delteco, incorporan una mesa giratoria completamente integrada con cuya ayuda se puede llevar a cabo los exigentes de fresado y/o torneado vertical u horizontal de 5 ejes simultáneos con una sujeción. En la mesa, incluso al estar inclinada, pueden llevarse a cabo todos los procesos de torneado. De ello se derivan muy novedosas posibilidades de mecanizado, así como mayor flexibilidad de utilización. La tecnología de torneado está completamente integrada: gracias a la combinación del eje giratorio combinado (eje A) con el eje de la mesa giratoria (eje C), pueden llevarse a cabo exigentes procesos de torneado, así como procesos de torneado y fresado combinados. Además, una de las particularidades más destacadas de la serie MT de Hermle es su capacidad de mecanizar las piezas de mayor tamaño del mercado, también en una misma sujeción, mediante el proceso combinado de torneado y fresado. A fin de evitar problemas y deterioros que puedan surgir debido a los momentos de inercia, se utiliza en la mesa giratoria un sistema manual de equilibrado integrado en la mesa giratoria.
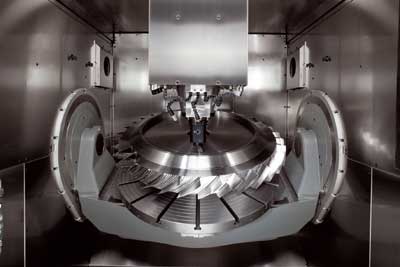
Para el mecanizado completo de piezas de precisión, estos equipos cuentan con un sistema de supervisión de rotura de herramienta y medición de herramienta para la medición de las herramientas de fresado por láser y la exploración de las herramientas de torno por palpador 3D. Adicionalmente pueden adaptarse como opción almacenes adicionales modulares, ergonómicos y accesibles para herramientas de fresado y de torno adicionales. Una de las principales ventajas del concepto MT de Hermle AG es que los mecanizados giratorios no sólo se pueden realizar en una posición de 0° y de 90° de la mesa circular orientable CN, sino también en cualquier posición intermedia e inclusive en continuo. Gracias a ello pueden utilizarse herramientas de torno muy cortas. El husillo principal se bloquea en las operaciones giratorias, permitiendo así que se transfieran sin problemas incluso los pares más grandes y se posicione exactamente la herramienta de torno de forma reproducible. El acreditado concepto de 5 ejes de la serie C presentan también en las versiones MT sus ventajas prácticas, ya que en comparación con las máquinas de la competencia, los centros de mecanizado C 42 U MT dynamic y C 50 U MT dynamic de Hermle muestran un contorno de fallo máximo claramente superior en la zona de desplazamiento del husillo, lo que significa que también se pueden mecanizar piezas correspondientemente más grandes mediante el fresado / giro combinados en una sujeción.
Takisawa TMT-4500 y TMM 250, para todos los retos del mecanizado
La marca japonesa presenta la multitarea TMT-4500 como la “máquina definitiva” de procesos múltiples. Cuenta con dos cabezales integrados A2-11 de 26 kW con paso de barra de 90 milímetros. El cabezal de fresar con eje ‘B’ soportado por el sistema de doble columna con 30 kW de potencia y con alojamiento Capto C-6 para las herramientas cuyo almacén puede disponer opcionalmente hasta 200 unidades. Este husillo puede utilizarse plenamente debido a la rigidez que le otorga la construcción de doble columna y la tracción en tándem.
Destaca el recorrido en Y de 430 milímetros similar a un centro de mecanizado vertical. Este amplio recorrido transversal permite la completa mecanización de piezas complejas de dimensiones hasta ahora imposibles de realizar. Dispone además del control Tiwa P-I, que ofrece un diálogo de programación muy fácil, con simulaciones y dibujos animados en 3D y conversión del programa de código G.
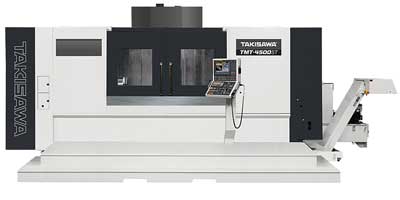
Las multitarea Takisawa evolucionan hacia un sistema más modular, incluyendo En la parte superior un cabezal fresador o eje B y en la parte inferior una torre de 15 posiciones para poder tornear y fresar en ambos husillos indistintamente.
Con los dos husillos enfrentados y las dos torres (motorizadas en sus 30 posiciones), las cuales pueden mecanizar en ambos husillos indistintamente, pueden lograrse tiempos de ciclo equilibrados. El mecanizado simultáneo en el lado izquierdo o derecho o en ambos husillos permite conseguir la compensación ideal de los tiempos de ciclo.