Las tecnologías de Inteligencia Artificial son un habilitador clave para sacar partido al esfuerzo de digitalización de la Industria 4.0
IA para la optimización y mejora de procesos de fabricación
Aitor Arnaiz, director de la Unidad de Sistemas de Información Inteligentes de Tekniker
24/07/2023El IoT y ‘Big Data’ suponen una oportunidad para aumentar la calidad y eficiencia en las líneas de producción. En este artículo, Tekniker presenta un caso de uso en procesos críticos de la producción de neumáticos en la empresa Continental.
La mejora tecnológica propiciada por la digitalización de la industria ha facilitado la irrupción de Internet de las cosas (IoT). Una penetración que permite escalar y mejorar el nivel y calidad de datos e información a la que puede acceder una empresa para analizar su desempeño y, con la ayuda de nuevas tecnologías como la Inteligencia Artificial, Big Data y Machine Learning, mejorar sus procesos.
Sin embargo, esta mejora es una tarea compleja. Es necesario tener cierto conocimiento de los procesos, operación y características de las máquinas, conocido como conocimiento del dominio o ‘domain knowledge’, que se debe plasmar mediante las diferentes técnicas de análisis y modelización, para escoger aquellas que resulten adecuadas en cada caso.
Para garantizar una mejora en los procesos, es necesario mantener una fuerte interacción positiva entre el personal de la planta, los expertos, que poseen los conocimientos sobre la misma y serán usuarios finales de la solución, y los modeladores/analistas que la desarrollarán.
Retos y oportunidades en fabricación de neumáticos
En el caso de la fabricación de neumáticos dentro de una planta, el proceso comienza habitualmente con la preparación de compuestos que, dependiendo de las recetas, pueden incluir diferentes ingredientes (caucho sintético, negro de carbón, butilo, óxido de zinc, aceleradores, antioxidantes…). Estos materiales se mezclan de forma mecánica a altas temperaturas, lo que evita que comience un proceso temprano de vulcanización de la mezcla.
La mezcla se conduce a una línea de extrusión que puede contener varias extrusoras, que producen una lámina de material a través de las bocas. Esta lámina se coloca en una línea de enfriamiento donde se corta y lleva primero a montaje junto con el resto de los componentes (cables de acero/tejido, aislamiento…), después a las prensas de curado donde se produce la vulcanización y adoptan su forma definitiva, y, finalmente, a los controles de calidad.
Una parte central del proceso es la extrusión. Consiste en la combinación de varios compuestos bajo condiciones fisicoquímicas concretas y da lugar a la creación de las láminas de material compuesto con propiedades concretas (la receta). Asimismo, es importante que las láminas se enfríen y corten manteniendo unas condiciones de velocidad y temperatura adecuadas. De esta manera se evitará generar defectos relacionados con calidades o dimensiones incorrectas, lo podría tener un impacto significativo en la productividad si no se detectan a tiempo. Tras la extrusión, quedan numerosos pasos en el proceso antes de validar las dimensiones y la calidad final del neumático.
Por otro lado, es importante anticipar anomalías en la línea de producción, puesto que cualquier parada puede a su vez interrumpir el resto del proceso e incluso requerir una detención total de la planta, en pocas horas.
En ciertas fábricas este proceso es aún más crítico ya que se realizan series muy cortas, con lo que en cada cambio de receta es necesario un tiempo de ajuste de todo el proceso. También puede haber necesidad de probar nuevas recetas con cierta frecuencia. En una línea de fabricación avanzada puede haber entre 10 y 20 cambios de receta al día y de 2 a 3 pruebas de nuevas recetas por semana, por lo que el tiempo total de proceso efectivo varía entre un 75 y un 50% del tiempo total.
En definitiva, existe un amplio margen de mejora a la hora de anticipar o evitar posibles anomalías para reducir la producción de defectivo, además de mejorar la eficiencia, como por ejemplo lograr un menor número de paradas por preventivos o una mayor rapidez en la puesta a punto de la producción de nuevas series.
Afortunadamente, la creciente digitalización de los procesos permite disponer ya en muchos casos de una información de partida, datos que ofrecen la oportunidad de emplear tecnologías de inteligencia artificial (IA) para mejorar en calidad y eficiencia.
Este artículo presenta un caso de optimización dentro de una planta de fabricación de neumáticos en el que se puede demostrar el amplio abanico de tecnologías que componen la IA y cómo, de la mano de Tekniker y su experiencia, se puede ajustar su uso a la complejidad y características de los problemas.
En concreto, Tekniker ha trabajado uno de los procesos críticos de la producción de neumáticos dentro de una línea de extrusión y fabricación de producto de la empresa Continental.
Optimización de la extrusión del material
El sistema de extrusión está compuesto de diferentes extrusoras/bocas de extrusión, en este caso cinco, que combinan el material necesario para producir la receta especificada. Cada extrusora está formada por un mecanismo de alimentación, y un tornillo sin fin que empuja el material hacia un troquel. Gracias a las condiciones de presión, temperatura y viscosidad del material de entrada, el troquel consigue que este adquiera las propiedades y forma deseadas. Una vez extruido, el material pasa a la línea de enfriado y, posteriormente, se corta.
Cada vez que comienza una nueva extrusión, por cambio de material y/o parada de producción, el operario debe determinar si considera que la situación de la extrusora (presiones, temperaturas, viscosidades…) es adecuada para comenzar a extruir e introducir unas consignas de funcionamiento dependientes de la receta que fabrica.
Una vez comienza a salir el material extruido, este se somete a una inspección por profilometría (visión) que indica si se adapta o no a los requisitos de calidad y se decide si se continúa con la extrusión o si es preciso eliminar el material extruido y esperar a condiciones mejores para volver a relanzar la extrusión.
Frecuentemente, el relanzamiento de la extrusión no da lugar a una extrusión satisfactoria, bien porque las consignas de extrusión no son las adecuadas o porque el estado de la extrusora no es el adecuado para relanzar el proceso. Además, cuando la extrusión se efectúa en buenas condiciones siempre existe cierto rechazo que suele estar relacionado con el tiempo de estabilización requerido por la extrusora para llegar a valores de profilometría adecuados.
Este proceso es un tanto manual, ya que el operario solo dispone de su conocimiento para determinar si la condición de las extrusoras es adecuada para comenzar a extruir y para identificar las mejores consignas para cada receta. En definitiva, la ejecución de cada nueva extrusión con cambio de receta puede suponer un importante coste de prueba y error, en donde la decisión pasa por hacer varias iteraciones en el proceso hasta identificar unos parámetros que permitan iniciar el proceso con las suficientes garantías de calidad. Refinar este procedimiento requiere una mayor experimentación, lo que implica parar la producción para hacer varios ensayos buscando ajustar la consigna, con su consiguiente coste.
¿La alternativa? Ejecutar esas extrusiones de forma virtual. Es decir, emplear modelos capaces de simular la operación de la extrusora. Estos modelos subrogados, que se generarán a partir de los datos de operación existentes, sirven para identificar las mejores consignas de operación a partir del uso de algoritmos de optimización.
La solución: modelos subrogados
En Tekniker hemos trabajado en una modelización subrogada que ayude al operario a reducir el tiempo de estabilización y la cantidad de rechazo. Para poder hacerlo, en primer lugar es necesario evaluar si existe un conjunto de datos suficientemente representativo de la variabilidad del problema y luego extraer los indicadores que realmente representan el sistema.
Gracias al trabajo previo de digitalización, disponíamos para este fin de hasta tres años de datos de extrusiones con la suficiente calidad que representan la variabilidad del proceso en infinidad de combinaciones de condición y consigna sobre cientos de recetas diferentes.
Sin embargo, estos datos o señales en crudo son datos no estructurados y, para que sean susceptibles de ser empleados por modelos de datos o inteligencia artificial, es preciso dotarlos de estructura. Para ello, se realiza una extracción de indicadores, que consiste en extraer la información relevante de esas señales que refleje el estado de la extrusión. Para este paso se requiere tener una estrecha colaboración entre expertos de dominio, que conocen los factores que afectan a su proceso, y analistas, que codifican esos factores a modo de indicadores estructurados.
Así, una vez efectuada la extracción de características y de acuerdo con los expertos de dominio, se distinguen 3 tipos de indicadores:
- Indicadores de condición: que reflejan la situación de cada extrusora antes de relanzar el sistema.
- Indicadores de consigna: que reflejan la consigna introducida por el operario.
- Indicadores de calidad: que reflejan el resultado de la extrusión.
Puesto que el reto del operario consiste en determinar la adecuación de las extrusoras y determinar las mejores consignas de comienzo de extrusión, se decide dividir el problema y crear dos modelos:
- Primero, un modelo determina si las condiciones actuales son propicias para su relanzamiento. Para ello toma las presiones y temperaturas en cada extrusora y evalúa si estas condiciones son o no adecuadas. Este modelo se ejecuta cada 5 segundos de forma que el estado de la adecuación estimada, adecuado, parcialmente adecuado, inadecuado, se actualiza y presenta al operario. Es el modelo de ‘readiness’.
- Un segundo modelo cuyo resultado se activa cuando la extrusión se puede lanzar y presenta unas recomendaciones sobre las consignas para minimizar el tiempo de estabilización y el residuo generado con respecto a las condiciones de extrusión. Es el modelo de optimización.
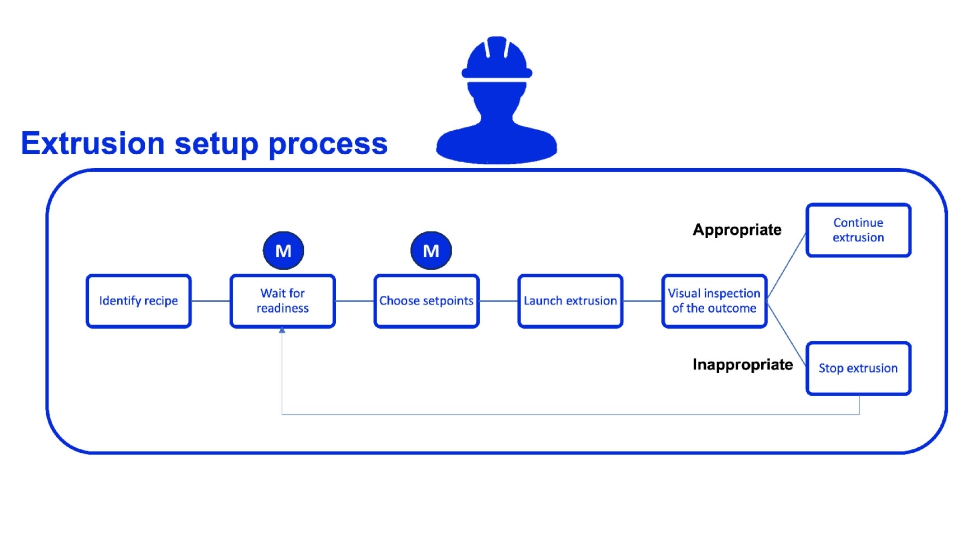
El procedimiento de creación y explotación de ambos modelos es parecido: u na vez se dispone de los indicadores de las extrusiones, se determina qué relaciones deberán mapear los modelos, es decir, cuáles serán las entradas de nuestro modelo y cuáles sus salidas. Si el modelo es capaz de representar esas relaciones con suficiente precisión, podrá subrogar de forma satisfactoria nuestra planta real, o, lo que es lo mismo, podrá saber qué salidas se esperan cuando se den ciertas entradas.
Así cada modelo cuenta con un set de entradas/salidas diferentes:
- Modelo de 'readiness':
o Entradas: indicadores de condición que representan el estado previo al lanzamiento de la extrusión.
o Salidas: indicadores de calidad global de la extrusión (buena o mala).
o Objetivo: determinar si conociendo la situación previa al lanzamiento se puede saber si la extrusión será o no buena.
- Modelo de optimización:
o Entradas: indicadores de condición y consignas del operario. Además de considerar la situación de las extrusoras en el lanzamiento, se incluye la acción del operario.
o Salidas: indicadores de calidad, cantidad de residuo y tiempo de estabilización.
o Objetivo: dadas ciertas condiciones de extrusora e inputs de operario, ser capaces de estimar el tiempo de estabilización y el residuo que generará una extrusión.
El modelo de 'readiness' nos permite saber de forma directa si las lecturas, como las presiones y temperaturas, son adecuadas o no para lanzar una extrusión en este instante. Por ello, se puede ejecutar con cierta periodicidad introduciéndole las lecturas de los sensores y determinar si las condiciones son adecuadas o no.
Por otro lado, el modelo de optimización nos permite estimar el residuo que se generaría y el tiempo de estabilización que requerirían ciertas condiciones de extrusión y ciertos parámetros introducidos por el operario. De esta forma, este segundo modelo nos permite lanzar una optimización en la que, de forma virtual, se evalúan el residuo y los tiempos de estabilización que se obtendrían con diferentes settings de la extrusión. De esta manera, se puede iterar hasta encontrar los parámetros óptimos de lanzamiento de la extrusión para cada receta sin necesidad de parar la planta real.
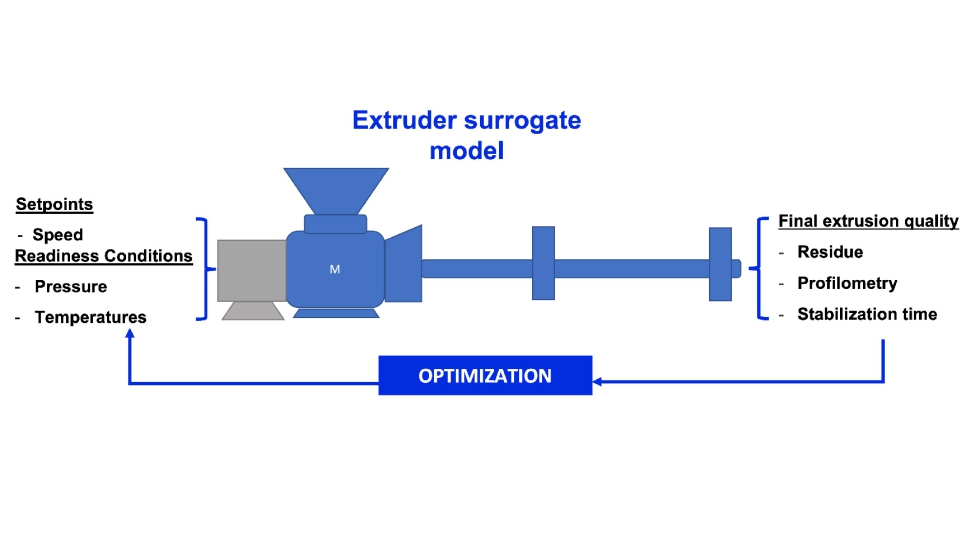
El despliegue
Para poder desarrollar y explotar estos modelos, es preciso crear una infraestructura que permita guardar los datos, así como ejecutar los modelos en tiempo real y facilitar su mantenimiento a lo largo del tiempo.
En primer lugar, se extraen los indicadores del histórico de datos creando una base de datos de indicadores que se emplea para crear los modelos de datos. Posteriormente, esa base de datos se alimenta de forma continua con los indicadores extraídos en tiempo real por si fuera necesario volver a entrenar estos modelos.
Una vez se han creado los modelos, se pueden ejecutar inferencias con los datos en tiempo real para dar soporte a las decisiones de los operarios.
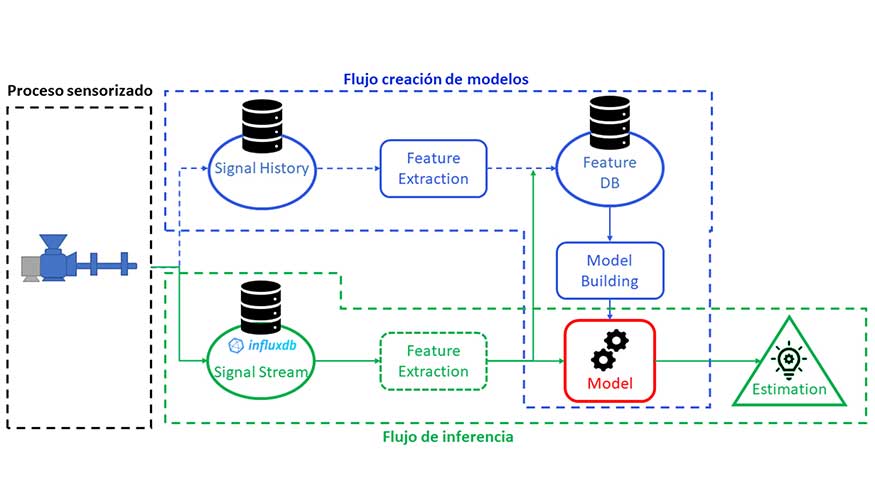
El resultado, mejora en la estabilización de la extrusión de cada compuesto
El resultado es una mejora significativa que supone, con el modelo de adecuación, un incremento de extrusiones con buena calidad de entre el 33 y el 90% con respecto a la operación que realiza el operador, y una reducción en los tiempos de estabilización de compuestos más empleados de entre el 60 y el 86%.
Todo esto supone una reducción muy importante en tiempos, en energía de proceso y en rechazos que no hay que reprocesar o tirar, con la consiguiente reducción de costes económicos y también medioambientales.
Conclusiones
El caso de uso aquí mostrado no es sino una evidencia más de cómo la inteligencia artificial y los modelos de datos (modelos híbridos/subrogados o gemelos digitales) pueden mejorar los procesos industriales. En Tekniker creemos que las tecnologías de inteligencia artificial son un habilitador clave para sacar partido al esfuerzo de digitalización que está realizando la Industria 4.0, ya que estas mismas tecnologías están facilitando mejoras en productos y procesos de competidores en todo el mundo.
Desde Tekniker abordamos la investigación y desarrollo de tecnologías de optimización desde perspectivas y capacidades complementarias. Apostamos por un alto grado de especialización tecnológica y a un conocimiento profundo de los procesos industriales en sectores tan diversos como los de automoción, aeronáutica, energía, o máquina herramienta, entre otros, para poder dar una solución robusta y ad-hoc a cada problema: desde la modelización de procesos en base al conocimiento existente, hasta la generación de herramientas y tecnologías que simplifiquen el análisis de datos y mejoren la fiabilidad de la inteligencia artificial. Desde el desarrollo de algoritmos de diagnóstico, predicción y optimización que combinan información proveniente de datos y experiencia, hasta su explotación en entornos adecuados a las necesidades de nuestros clientes (desde el edge hasta la nube ‘computing continuum’).