Control del proceso de inyección (Parte 2)
¿Sobre qué outputs focalizarnos?
Como hemos comentado, la gran cantidad de inputs, outputs, variables, variaciones que aparecen en el proceso de inyección durante las fabricaciones hace que los expertos que dominan y controla este proceso y sus variables sean escasos en el mercado. Aun siendo experto en el proceso, no podemos controlar todas y cada una de las variables.
Cada pieza e incluso cada aplicación o sector tiene sus criticidades desde el punto de vista de las piezas. Estas criticidades pueden hacer que tengamos que dar prioridad a una serie de inputs y por supuesto, controlar una serie de outputs que inciden en esas características críticas que queremos tener controladas. Por el contrario, puede haber outputs o inputs menos críticos para nuestras piezas, aplicación o sector.
Como línea general, estos serían los outputs que deberíamos tener controlados, registrados y bajo control.
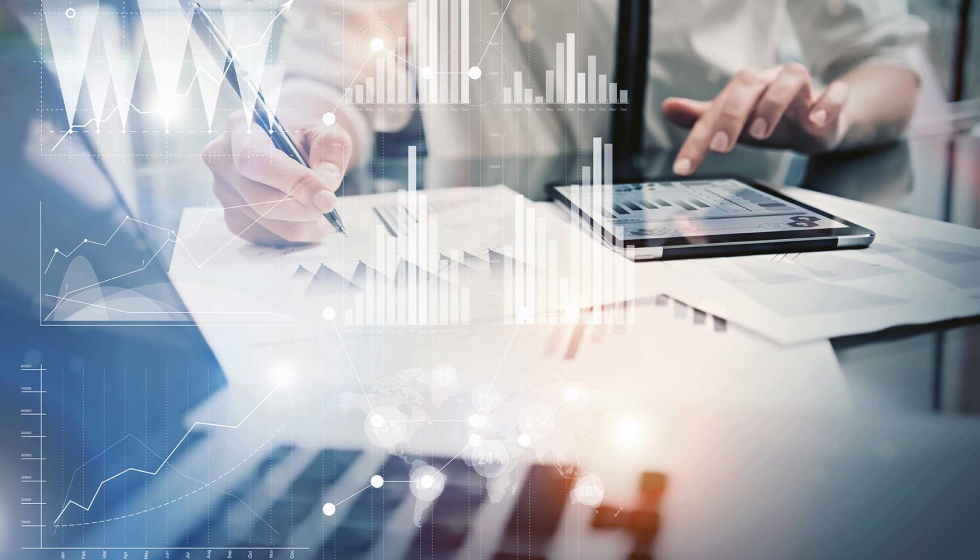
Tiempo de llenado
El tiempo de llenado es el tiempo más crítico de todo el proceso de inyección. Hay autores que indican que la dispersión máxima permitida entre ciclos es de + - 0,04 segundos.
Este tiempo debe ser repetitivo y no variar lote a lote e incluso en diferentes máquinas. No es admisible que este tiempo varíe.
Para que este tiempo no varíe, debemos tener claramente bien definidos y controlados conceptos de Scientific Injection Molding tales como Delta P, o la capacidad de compensación de la presión de la inyectora, conceptos que se explican y aplican con esta metodología.
Si el molde cambia de máquina o de planta productiva, el tiempo de llenado debe ser el mismo.
Presión de inyección en el punto de conmutación
Esta es la presión en el punto de cambio de llenado dinámico a postpresión. Aquí es la máxima presión solicitada a la unidad de inyección para alcanzar este punto de llenado. Esta presión no debe variar en su rango. Podemos tener diferentes presiones con diferentes lotes de materia prima, diferentes pigmentos o masterbaches, pero el rango o diferencia entre valor máximo y valor mínimo no debería variar.
Cuando comienza una producción, podemos tener las mayores variaciones de estos valores de presión. Esto es debido a que el proceso necesita estabilizarse. Valores tales como temperatura del acero de las cavidades, temperatura el aceite hidráulico o temperatura de la masa, necesitan un tiempo de estabilización térmica. A partir de esa estabilización el valor debe mantenerse dentro de un rango.
Si movemos el molde de máquina y estamos trabajando con presión de inyección específica debemos tener los mismos valores de presión en el punto de conmutación (siempre que utilicemos la misma boquilla de maquina en diseño interior).
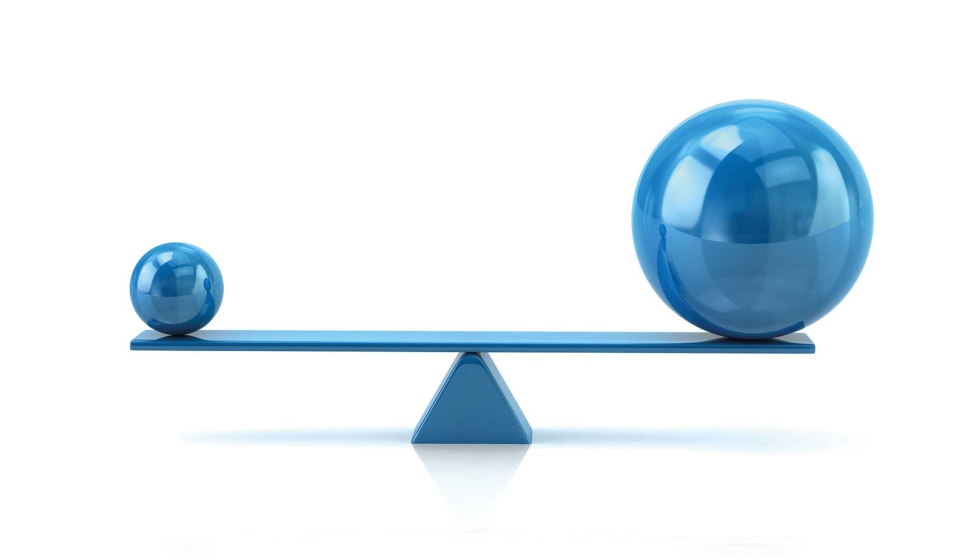
Cojín
Residual de material que permanece en la zona delantera del husillo al finalizar la fase de inyección y compactación. El cojín debe ser estable, aunque sus valores absolutos podrían variar al cambiar de lote de materia prima, debería mantenerse estable en el mismo rango.
El cojín debe ser, como norma de taller de fácil cálculo, un 10% de la dosis utilizada. Un cojín excesivamente pequeño puede dar lugar a que en algún ciclo el cojín llegue a 0 con lo que no tendríamos transmisión de presión a la cavidad y por el contrario, un cojín demasiado grande provoca dos efectos adversos. El efecto horno y el efecto muelle.
Efecto horno
El material fundido que hay en la zona delantera del husillo ha sido fundido a través de las resistencias externas de la unidad de inyección y a través del funcionamiento interno del husillo. La cizalla que se genera en los filetes del husillo junto con la zona de compresión hacen que se genere calor interno y que el material se entremezcle y se homogenice térmicamente, de modo que tenemos un material térmicamente homogéneo. Cuando este material queda parado en la zona delantera el husillo, como cojín por ejemplo, el calor que recibe durante todo el tiempo que esté en la zona delantera del husillo, será a través de las resistencias externas de la unidad de inyección, por tanto, el calor que generan estas resistencias externas difícilmente llegará al núcleo del material fundido en la zona delantera. Más si tenemos en cuenta que el plástico es mal conductor térmico. De modo que tendremos material más caliente en el anillo externo de este material fundido y más “frío” en el núcleo de la masa fundida. De modo que durante el tiempo que tenemos el cojín esperando en la zona delantera del husillo, estamos desequilibrando la homogeneidad térmica que hemos conseguido con el husillo. Es por esto por lo que no es recomendable un cojín muy grande porque tendremos más material con menor homogeneidad térmica.
Efecto muelle
El plástico fundido en la zona delantera del husillo trabaja como un muelle cuando aplicamos presión para compactar la cavidad. Si delante de la válvula de la punta el husillo hay mucho cojín, es como si tuviéramos un muelle grande que amortigua parte de la presión que estamos ejerciendo en la cavidad, mientras que un cojín pequeño, sería un muelle pequeño, amortigua mucho menos la presión que ejercemos desde el husillo en la cavidad. De modo que un cojín grande transmite peor la presión a la cavidad que uno más pequeño.
- Tiempo de dosificación: Es un indicador de estabilidad del proceso. No hay procesos estables con tiempos de dosificación irregulares. Tolerancias habituales en este output del orden del 2% son correctas. En caso de gran dispersión hay que comprobar la válvula de punta de husillo, la temperatura de la traversa y la temperatura de la unidad de inyección.
- Tiempo de ciclo: Debe ser repetitivo. Atención cuando el ciclo es semiautomático con operario. En estos casos, hay que asegurar que el ciclo se mantenga o estaremos generando variaciones en el proceso.
- Temperatura de la pieza: Este es un output que correlaciona la consistencia de la temperatura de molde y del material. Al empezar el proceso esta temperatura irá variando y creciendo hasta que se estabilice. Tolerancias aquí del orden de + - 5 grados son aceptadas.
Si estos outputs son estables y están controlados, tenemos muchas probabilidades de que nuestras piezas sean constantes y repetitivas. De otra forma si estos outputs varían en exceso podemos estar seguros de que nuestras piezas están siendo diferentes, con dispersiones en sus cualidades y el proceso no será robusto ni consistente.
Por eso vale la pena dedicar un tiempo a analizar sus desviaciones: en qué rango se mueven durante las fabricaciones, definir sus tolerancias reales en función de los resultados de las desviaciones de sus valores y del efecto en las piezas del estos, aumento del rango de dispersión, etc, para, con estos históricos, tener un verdadero control del proceso.
José Ramón Lerma es autor de los libros: 'Libro Manual Avanzado de Inyección de Termoplástico', que tiene como objetivo ser, por un lado, una herramienta para la formación y, por otro, un manual de ayuda para todo el personal de una empresa de inyección de plásticos y, del recientemente editado, 'Scientific Injection Molding Tools. Productividad a través del dominio del proceso'. Ambas publicaciones, comercializadas por Plásticos Universales / Interempresas (libros@interempresas.net), consta de detallados casos prácticos, amplia información de moldeo científico y un ‘pendrive’ con 20 hojas de cálculo y herramientas de SC Molding o Scientific Injection Molding, además de optimización y definición de proceso, lo que lo hacen único en el mercado. El libro Manual Avanzado de Transformación de Termoplásticos ha sido editado y comercializado en inglés a nivel mundial por la editorial Hanser Publications.
Página web sobre Scientific Injection Molding: www.asimm.es